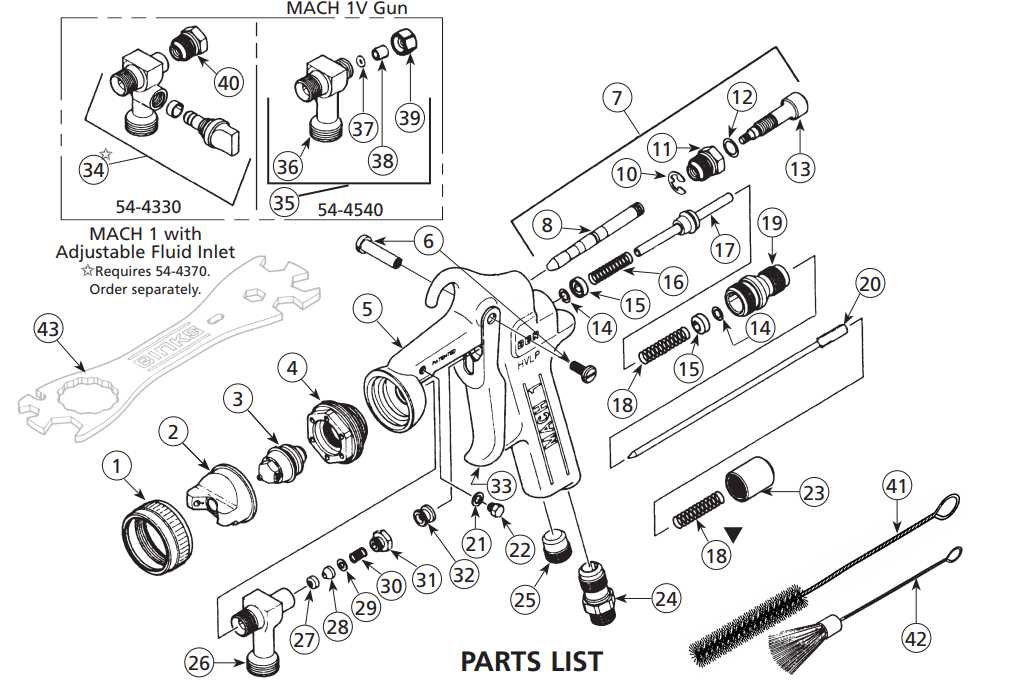
The structure and organization of various machine elements are essential for understanding how the tool operates efficiently. Each element works in harmony with others to deliver precise and smooth results during usage. By familiarizing yourself with these, you’ll gain deeper insight into the tool’s overall functionality.
Key sections of the device are strategically positioned to enhance performance and durability. Recognizing these individual elements ensures proper maintenance and troubleshooting, enabling long-term use of the equipment with minimal issues.
Understanding the overall layout is crucial, as it helps in identifying any potential areas that might require attention or adjustments. A thorough knowledge of the components will ultimately lead to improved efficiency and productivity in your work.
Understanding Paint Sprayer Components
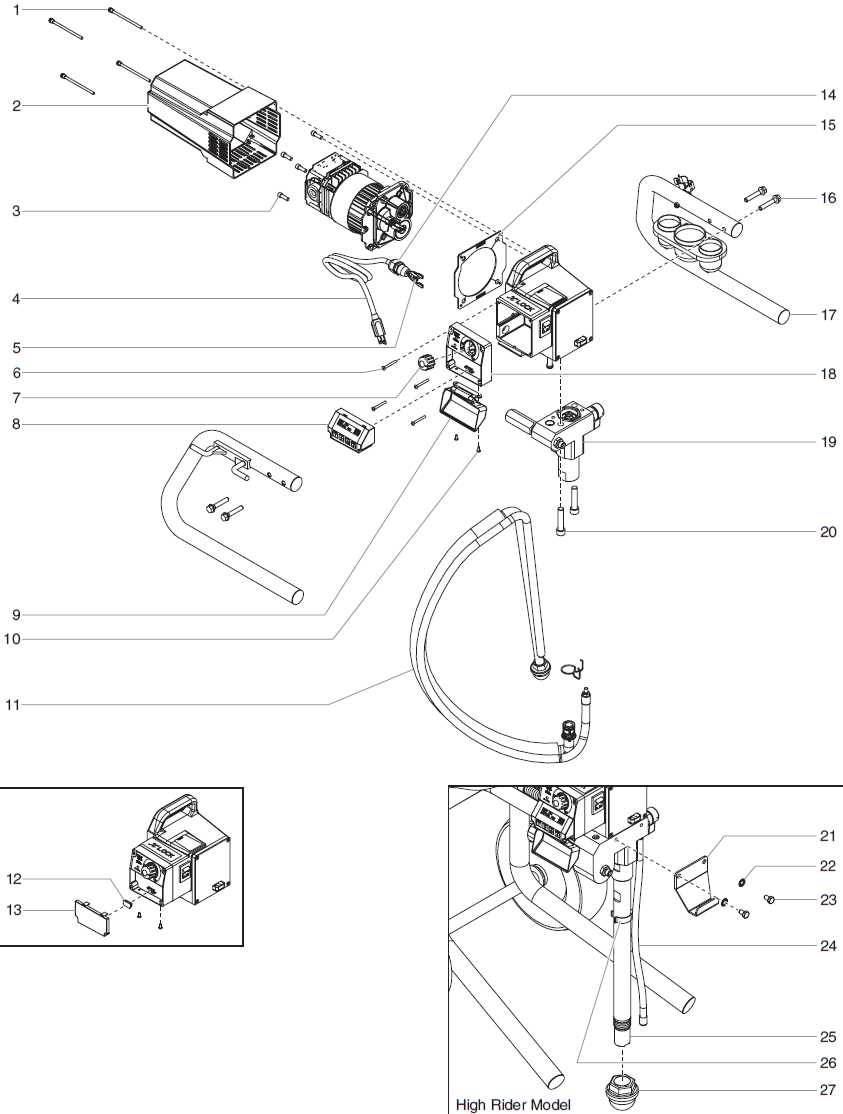
When working with a device designed for coating surfaces efficiently, it’s essential to familiarize yourself with its key elements. Each part plays a crucial role in ensuring the smooth operation and achieving a consistent finish. Knowing how these components interact can help maintain performance and extend the lifespan of the equipment.
Main Structural Elements
The core of the system includes several interconnected pieces that manage the fluid’s flow and pressure. These sections are designed to regulate how material is distributed, ensuring precision during application. Understanding these elements is critical for troubleshooting and maintaining efficiency.
Flow Control Mechanisms
Regulating the amount of coating applied is managed by specific components that allow for adjustments based on the required output. Ensuring these mechanisms are in good working order helps maintain accuracy and avoids material wastage.
Common Parts of a Paint Sprayer
The functionality of any device designed for applying coatings relies on various essential components. Each part plays a key role in ensuring smooth and efficient operation, providing users with control and precision during the application process. These components work together to handle fluid, regulate airflow, and deliver the material evenly on the target surface.
Key Components
Component |
Function |
Nozzle |
Directs the flow of material onto the surface. |
Trigger |
Controls the release of fluid when pressed. |
Hose |
Transfers the coating material from the container to the application point. |
Pressure Regulator |
Adjusts the amount of force used for application, ensuring even distribution
How a Spray Gun Functions
A spray device operates by utilizing a system that combines air pressure and liquid flow to create a fine mist for even application. The tool’s mechanism controls the release of the liquid, ensuring smooth and consistent distribution over a surface. Key elements work together to regulate the amount of material being dispersed and the velocity at which it exits.
Air and liquid control are crucial components that determine how the system functions. By adjusting these settings, one can control the thickness of the coat and the precision of the application. The mechanism also ensures consistent output, minimizing any unevenness or imperfections during use.
Exploring Nozzle Variations
Nozzles come in a wide range of types, each designed for specific purposes. Understanding the differences between these variations can help in choosing the right one for different tasks. Factors such as flow rate, pressure, and material compatibility play an important role in determining which nozzle is most suitable.
Common Nozzle Types
Nozzles can differ in shape and size, affecting how the substance is distributed. Some are designed for broader coverage, while others provide precision control. The angle of distribution and the velocity of the flow are also key considerations.
Nozzle Type |
Flow Rate |
Best Use |
Wide-Angle |
High |
Large surfaces |
Narrow-Angle |
Hose Types and Their Uses
Different hoses serve various functions, each designed for specific tasks and conditions. Understanding their characteristics and benefits helps in choosing the right one for the job.
Flexible Hoses are known for their adaptability. These are ideal for situations requiring easy maneuverability, as they can bend and twist without losing efficiency.
Rigid Hoses offer durability and strength. They are often used in settings where stability and resistance to pressure are essential, making them a reliable option for demanding environments.
Specialized Hoses are designed for unique conditions, such as high temperatures or specific materials. These hoses are tailored to meet specialized requirements, ensuring optimal performance under challenging circumstances.
Filters and Their Importance
Filters play a crucial role in ensuring the smooth operation of various systems by keeping impurities at bay. They are designed to trap particles and prevent them from clogging or damaging the equipment. Without these components, efficiency would drop significantly, leading to frequent malfunctions.
Types of Filters
- Mesh filters: Known for trapping larger debris.
- Cartridge filters: Effective at capturing smaller particles.
- Inline filters: Convenient for systems where space is limited.
Why Regular Maintenance is Essential
- Prevents blockages that can disrupt performance.
- Extends the lifespan of the equipment.
- Ensures consistent and reliable operation over time.
Pump Mechanisms in Paint Sprayers
The internal mechanisms responsible for fluid movement in coating devices are crucial for efficient and consistent material application. These systems vary in complexity but serve the essential purpose of maintaining a controlled flow, allowing for uniform distribution of substances over surfaces. Each design is tailored to optimize performance, depending on the specific type of coating equipment.
Types of Pump Systems
Pumps in these devices typically fall into two categories: those relying on pressure-driven systems and those utilizing mechanical force. Each system has unique advantages, providing solutions for different materials and project requirements.
Type |
Operation |
Advantages |
Pressure-Driven |
Uses air or hydraulic pressure to force liquid through a nozzle. |
Ideal for high-volume, large-scale projects. |
Trigger Systems Explained
Trigger systems play a crucial role in controlling fluid flow in various devices. Their design ensures efficient release and precise control, making them an essential component in many types of equipment. Understanding how these systems operate can provide better performance and longevity for the tool.
How Trigger Systems Function
The mechanism typically works by activating a valve that opens and closes with pressure. This allows for the regulation of liquid or gas flow depending on the need. The trigger can vary in sensitivity, providing either gradual control or a quick release.
- Activation of the valve controls flow
- Sensitivity settings allow for precise adjustments
- Durable materials increase longevity and reliability
Common Variations
There are multiple variations in trigger systems, each designed for specific purposes. Some are manual, requiring more force, while others may feature electronic components for automatic control. The choice of the system depends largely on the type of task and the environment in which it is used.
- Manual systems offer greater control but require more effort
- Electronic systems are more ad
Maintenance Tips for Sprayer Parts
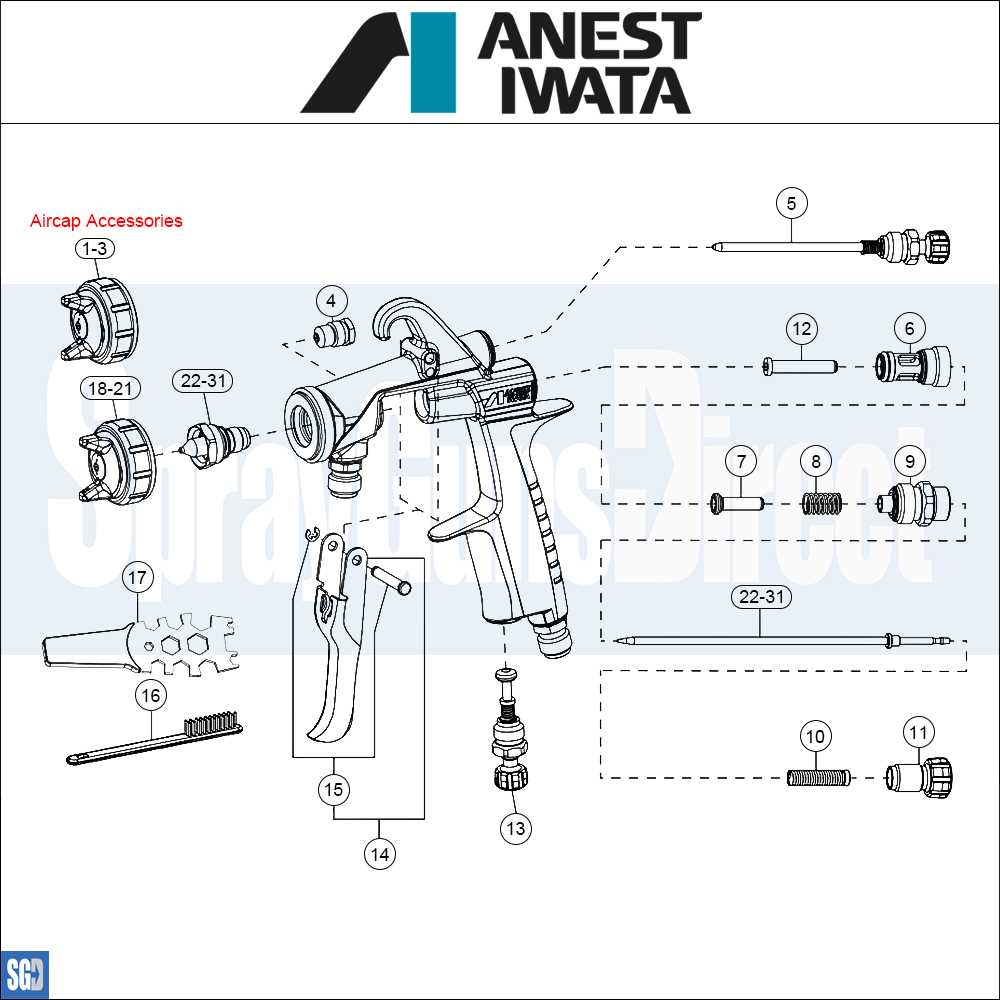
Proper upkeep of equipment components is essential for optimal performance and longevity. Regular care not only enhances functionality but also helps prevent unexpected issues that may arise during usage. Here are some effective strategies to maintain these crucial elements.
Regular Inspection
Consistent examination of individual elements is vital. Look for any signs of wear, damage, or buildup that could hinder performance. Addressing small issues promptly can prevent larger problems later on.
Cleaning Procedures
Routine cleaning is necessary to ensure all components function smoothly. Utilize appropriate cleaning agents and tools for each type of element to avoid damage. Follow the manufacturer’s guidelines for recommended cleaning methods.
Maintenance Task |
Frequency |
Recommended Tools |
Inspection |
Every use |
Visual check |
Cleaning |
After each use |
Soft brushes, cloths |
Lubrication |
Monthly |
Lubricant, applicator |
Choosing the Right Accessories
When it comes to enhancing the functionality of your equipment, selecting suitable attachments is crucial. The right additions can significantly impact the efficiency and quality of your projects, allowing for a more seamless experience and better outcomes.
Compatibility is one of the first factors to consider. Ensure that the accessories you choose align with your device’s specifications. This will prevent any issues during operation and maximize performance.
Another important aspect is material quality. Opt for durable and reliable options that can withstand the demands of frequent use. High-quality attachments not only last longer but also contribute to achieving superior results.
Finally, assess the variety of functionalities offered by different accessories. Depending on the tasks you intend to perform, you may require specific tools that cater to those needs. Exploring various options allows for a customized approach to your projects, enhancing versatility and effectiveness.
Signs of Worn or Damaged Parts
Identifying the indicators of deterioration or impairment in components is essential for maintaining optimal functionality and performance. Recognizing these signs early can prevent further damage and ensure a smooth operation.
Common signs of degradation include unusual noises during operation, which may indicate that certain elements are not functioning correctly. Additionally, visible wear, such as cracks or fraying, can be a clear signal that some pieces need attention. Leakage of materials is another critical sign that should not be overlooked, as it often points to compromised seals or connections.
Frequent clogging or interruptions in flow may suggest that specific components are not performing as intended, requiring inspection or replacement. Regularly monitoring these signs can lead to timely interventions and prolong the lifespan of your equipment.
|
|