Main Frame and Structural Elements
The central foundation and supporting framework serve as the backbone, ensuring stability and efficient operation. These key components are engineered to withstand significant forces, while also providing a stable base for the overall structure.
The core elements are typically constructed from durable materials designed to endure heavy use and outdoor conditions. A solid frame not only supports the weight of the entire assembly but also absorbs vibrations, minimizing wear and tear on the machine over time.
- Base Structure: Provides a stable platform, keeping the entire unit grounded during use.
- Reinforced Supports: Strengthened components that maintain the alignment and balance of the equipment.
- Attachment Points: Specific areas designed for mounting additional components or tools.
- Protective Coatings: Surface treatments that prevent corrosion and extend the lifespan of the metal parts.
Each of these elements plays a critical role in maintaining the integrity and safety of the device, ensuring it can pe
Engine and Power Source Overview
The engine and power source play a critical role in driving the functionality of outdoor equipment. The selection of an appropriate power system determines both the performance and efficiency of the machine. Typically, these devices rely on a combination of mechanical and hydraulic components, powered by either gas engines or electric motors. This section provides an in-depth look at how these systems operate and contribute to the overall operation.
Gas-Powered Systems are known for their high power output and are often preferred for heavy-duty applications. These engines provide a consistent flow of energy, enabling the machine to handle more demanding tasks efficiently. However, regular maintenance and fuel management are necessary to ensure optimal performance.
Electric motors offer a quieter and more environmentally friendly alternative. While they may not deliver the same level of power as gas engines, the
Operation of the Wedge Mechanism
The wedge mechanism plays a crucial role in dividing solid materials, utilizing a powerful force to drive through dense objects. It operates by applying pressure, causing the material to separate into smaller sections. The precision and effectiveness of this tool depend on its design, strength, and the method of force application. Understanding its function is key to ensuring smooth operation and efficiency.
Component |
Function |
Wedge |
Concentrates force to initiate separation of material. |
Piston |
Moves the wedge forward, applying the necessary pressure. |
Guide Rails |
Ensure the wedge moves in a straight and stable direction. |
Control Valve |
Regulates the flow of hydraulic fluid to control movement. |
Log Cradle and Support Systems
The design and functionality of support structures are crucial for ensuring stability and safety during the processing of large timber. These components play a significant role in enhancing efficiency by securely holding the material in place, allowing for a more controlled and precise operation. Without effective support systems, the risk of accidents increases, and the overall productivity may diminish.
Support systems are designed to accommodate various sizes and types of timber, providing flexibility and adaptability to different working environments. They typically include features that enhance grip and prevent shifting, which is essential for achieving optimal results.
In addition, an efficient cradle offers the advantage of reducing strain on the operator, allowing for a more comfortable and ergonomic experience. This aspect is particularly important during prolonged use, as it minimizes fatigue and promotes better handling of materials.
Investing in high-quality support mechanisms is vital for anyone engaged in wood processing, as it directly impacts both safety and performance. Choosing the right system can significantly enhance the overall effectiveness of the operation, making it a key consideration for users.
Control Valves and Safety Features
The effectiveness of any hydraulic system is significantly influenced by its control mechanisms and safety protocols. These components play a crucial role in managing fluid flow, ensuring efficient operation, and protecting users from potential hazards. Understanding the functionality of these elements is essential for maintaining operational integrity and safety during use.
Importance of Control Mechanisms
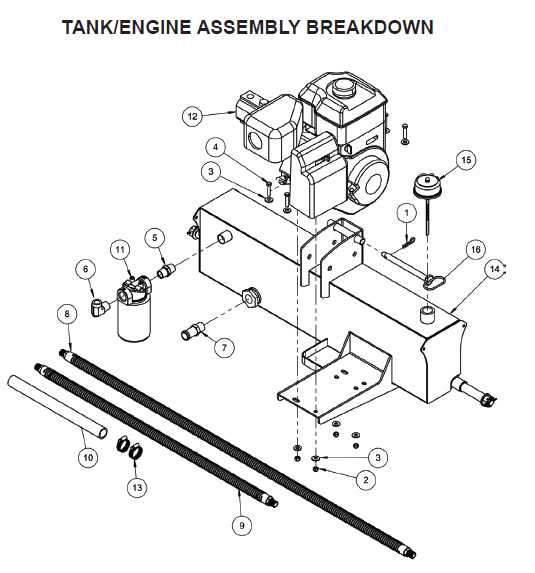
Control mechanisms serve as the brain of hydraulic systems, directing the flow of fluid to various components. They regulate pressure and ensure that each part receives the appropriate amount of power to function optimally. Properly calibrated valves contribute to the overall efficiency and responsiveness of the system.
Safety Protocols to Prevent Hazards
Incorporating safety features is vital for protecting operators from accidents and injuries. These features often include pressure relief valves, emergency stop buttons, and overload protection systems. Each element is designed to mitigate risks associated with hydraulic pressure and operational malfunctions.
Feature |
Description |
Functionality |
Pressure Relief Valve |
Prevents excessive pressure buildup |
Automatically releases fluid when pressure exceeds a set limit |
Emergency Stop Button |
Immediate shutdown of the system |
Quickly halts operation to prevent accidents |
Overload Protection |
Detects excessive load conditions |
Disengages the system to prevent damage |
How the Oil Filter Functions
The oil filter plays a crucial role in ensuring the longevity and efficiency of various engines. By removing impurities and contaminants from the lubricating fluid, it helps maintain optimal performance and prevents damage to internal components. This section delves into the mechanics of how this vital element operates within the system.
Mechanism of Filtration
The filtration process begins when oil circulates through the engine. As it moves, it carries microscopic particles and debris. The oil filter contains a media that traps these contaminants, allowing clean fluid to return to the engine. This action not only protects engine surfaces but also enhances overall functionality.
Importance of Regular Maintenance
Regularly replacing the oil filter is essential for maintaining engine health. Over time, the filter can become clogged, which can restrict oil flow and lead to increased wear and tear. Changing the filter during routine oil changes ensures that the engine remains lubricated with clean fluid, thereby prolonging its lifespan.
Function |
Description |
Contaminant Removal |
Eliminates dirt and debris from oil. |
Fluid Flow |
Ensures uninterrupted circulation of clean oil. |
Engine Protection |
Reduces wear on engine components. |
Performance Enhancement |
Improves overall efficiency of the engine. |
Towing and Mobility Attachments
When it comes to enhancing the functionality of your equipment, incorporating towing and mobility accessories is essential. These attachments enable greater versatility, allowing users to transport and maneuver their tools with ease. By facilitating movement across various terrains, they improve overall efficiency and usability.
Types of Towing Accessories
There are several types of towing accessories available, each designed to cater to specific needs. Hitches are among the most common options, providing a secure connection for towing trailers or other implements. Additionally, wheel kits offer enhanced mobility, allowing users to navigate uneven surfaces without difficulty.
Benefits of Mobility Enhancements
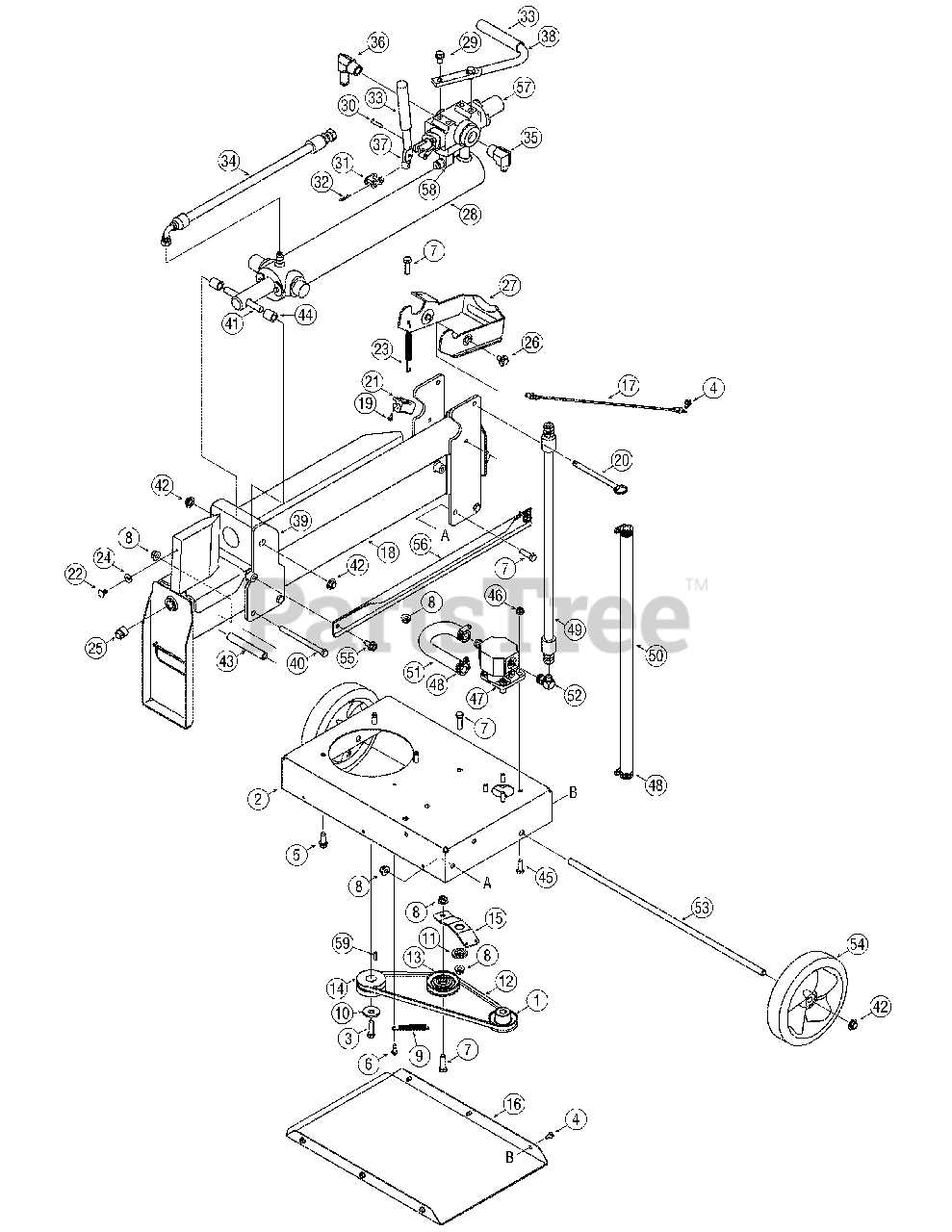
Integrating mobility enhancements not only boosts the versatility of your equipment but also contributes to safety. Improved stability during transport reduces the risk of accidents, while allowing for better control in challenging conditions. Ultimately, these accessories transform how you utilize your tools, making your tasks more manageable and effective.
Routine Maintenance for Longevity
Regular upkeep is essential for extending the lifespan of your equipment. By following a consistent maintenance schedule, you can ensure that your device operates efficiently and safely, reducing the likelihood of costly repairs and replacements. This section outlines key practices that promote durability and reliability over time.
Maintenance Task |
Frequency |
Description |
Inspect Fluid Levels |
Every Use |
Check oil, hydraulic fluid, and other essential liquids to prevent damage from low levels. |
Clean Air Filters |
Monthly |
Ensure filters are free from debris to maintain optimal airflow and performance. |
Sharpen Cutting Tools |
As Needed |
Keep blades and other cutting components sharp for efficient operation. |
Check for Wear |
Every Season |
Inspect belts, hoses, and other components for signs of wear and replace as necessary. |
Lubricate Moving Parts |
Every 10 Hours |
Apply appropriate lubricant to moving elements to reduce friction and wear. |
By adhering to these maintenance tasks, users can significantly enhance the reliability and efficiency of their equipment. A proactive approach not only saves time and money but also ensures safe and effective operation.
Common Issues and Troubleshooting Tips
When operating equipment designed for cutting wood, users may encounter various challenges that can affect performance. Identifying these issues early and knowing how to resolve them can enhance efficiency and prolong the lifespan of the apparatus. Below are some frequent problems and effective solutions to consider.
Difficulty Starting the Equipment
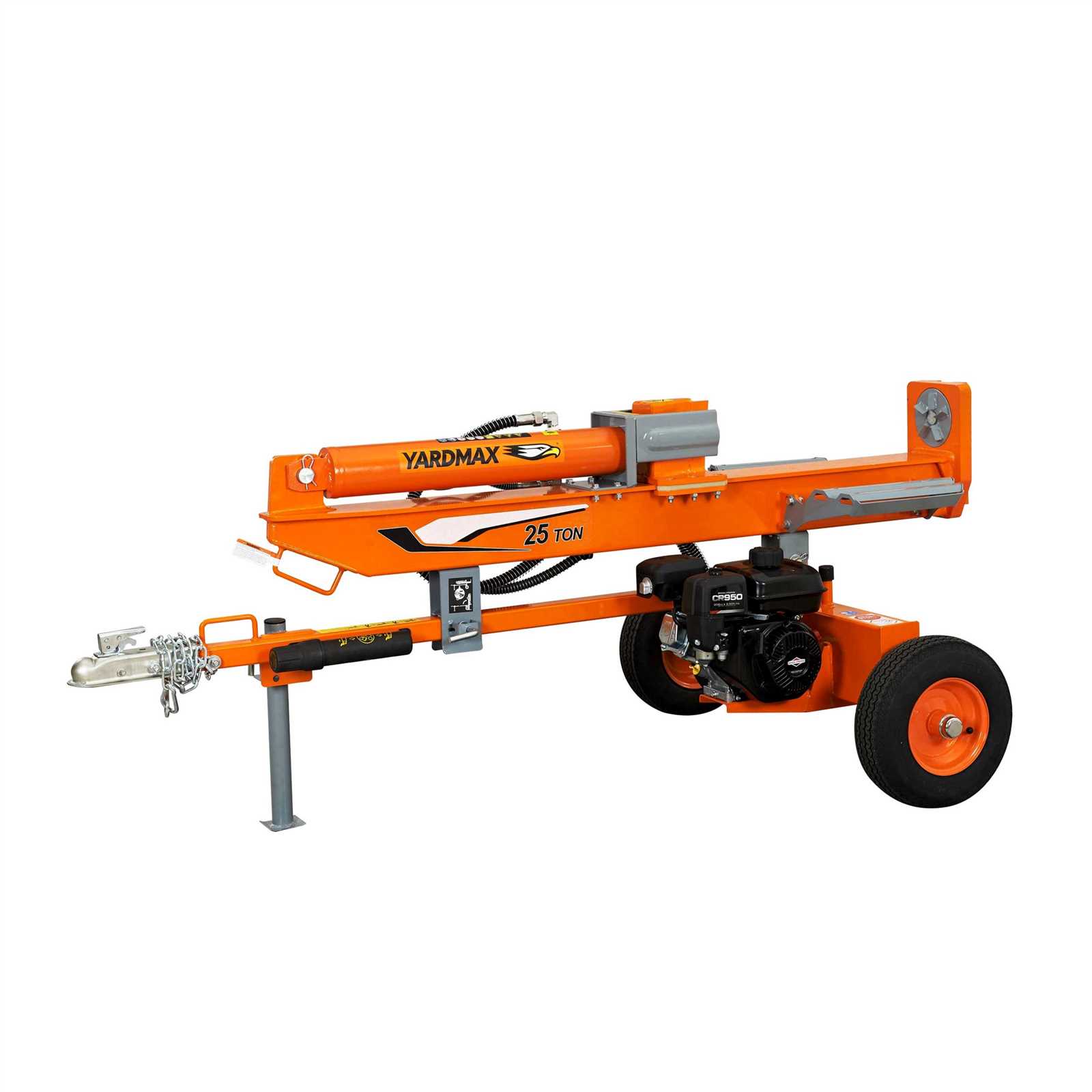
If the apparatus fails to start, check the fuel level and ensure that it is fresh and free from contaminants. Additionally, inspect the ignition system for any signs of wear or damage. A clogged air filter can also hinder performance, so be sure to clean or replace it if necessary.
Uneven Cuts or Stalling
Uneven cutting can result from a dull blade or improper alignment. Regular maintenance, including sharpening the blade and checking its positioning, can help achieve smoother operation. If the machine stalls during use, it may indicate that it is overloaded. Reduce the size of the logs being processed to prevent this issue.
Regular checks and proper maintenance are essential for keeping the equipment in optimal condition. Always consult the manufacturer’s guidelines for specific troubleshooting steps tailored to your model.
Replacing Worn or Damaged Parts
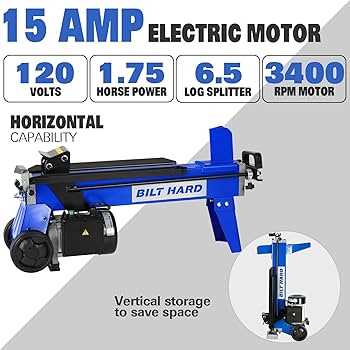
Over time, components within your equipment can suffer from wear and tear, impacting overall performance. Addressing these issues promptly ensures that your tool operates efficiently and safely. Regular inspections will help identify any elements that require attention, preventing further damage and costly repairs.
Recognizing Signs of Wear is crucial for maintaining optimal functionality. Look for any unusual noises, vibrations, or performance declines during operation. These can indicate that certain components are no longer functioning as they should.
Replacement Process involves a few key steps. First, ensure the equipment is powered off and disconnected from any power source. Next, consult the user manual or a reliable guide for specific instructions related to the components in question. Carefully remove the worn elements and replace them with new ones, ensuring that all connections are secure.
Regular maintenance not only extends the lifespan of your tool but also enhances its efficiency, making it essential to prioritize replacements as needed. Keeping spare parts on hand can also reduce downtime, allowing you to quickly restore your equipment to optimal working condition.
|