Understanding the essential mechanisms of this equipment is crucial for its effective operation. The various subsystems work together to ensure optimal functionality, each playing a specific role in maintaining performance and efficiency. Whether it’s handling debris removal or liquid transportation, the integration of these components is critical.
The powerful suction system is designed to handle a range of materials. With its ability to create a strong vacuum, this component efficiently draws in various substances, making the equipment highly versatile in different scenarios. Maintenance of this system is key to ensuring long-lasting performance.
The high-pressure water system is another crucial part of the unit’s functionality. This element allows for effective cleaning and debris removal, utilizing water jets to dislodge materials. Regular upkeep ensures this system remains efficient and prevents clogging or damage.
The hydraulic system is a key component in complex machinery, offering the power and control needed for efficient operation. This section delves into the structural arrangement of the hydraulic components, explaining how they work together to ensure smooth and precise movement of mechanical parts. Understanding this layout can help operators maintain optimal performance and identify potential areas for regular inspection and maintenance.
Several critical elements form the backbone of the hydraulic system, each playing a vital role in the overall functionality. These components include pumps, valves, cylinders, and reservoirs, all connected by fluid lines.
Component |
Function |
Pumps |
Generate fluid pressure for system operation |
Pneumatic Parts and Their Functions
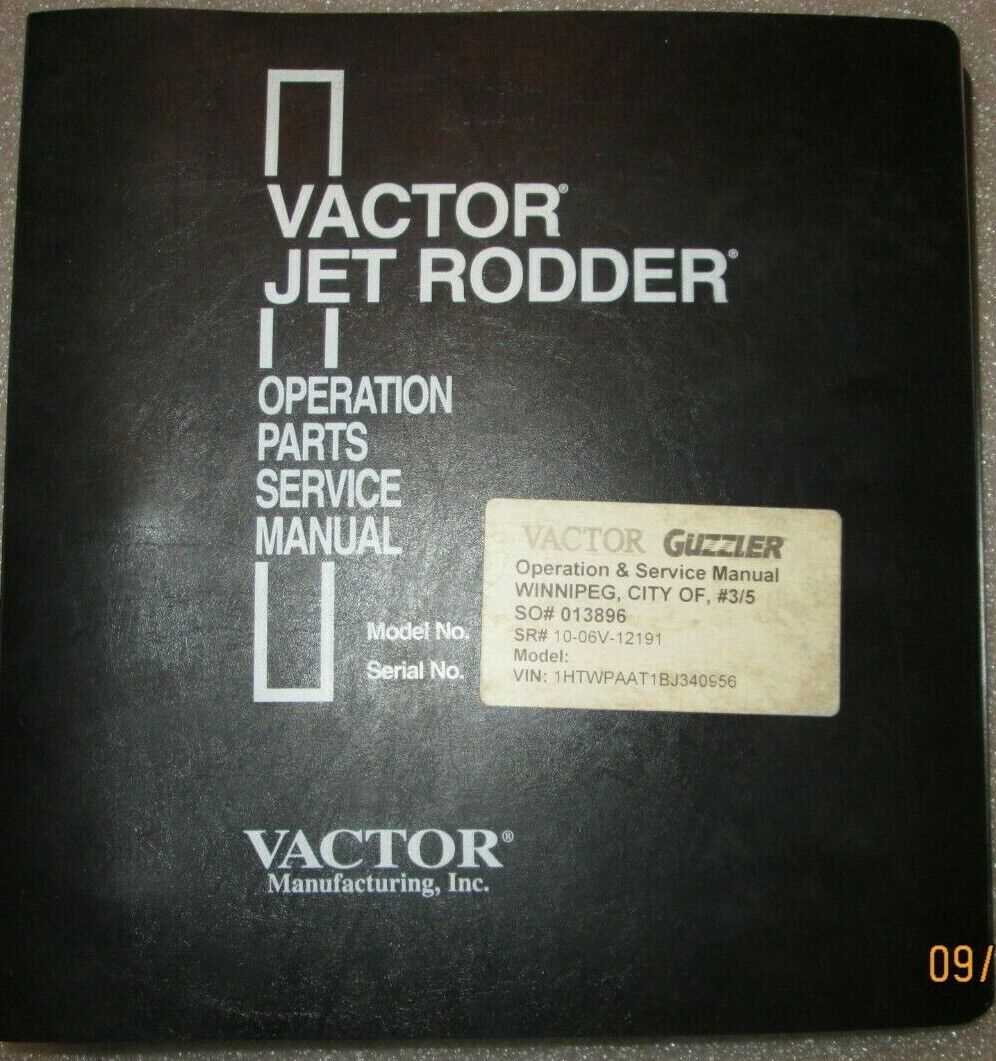
Pneumatic systems play a crucial role in various machinery by utilizing compressed air to perform mechanical work. These systems are known for their efficiency, reliability, and ease of maintenance, making them an essential component in many industrial applications.
Air Compressor: This device is responsible for generating the pressurized air needed to power the system. It draws in atmospheric air and compresses it to the desired pressure.
Control Valves: These components regulate the flow of air within the system, directing it to the necessary areas to perform specific tasks. They ensure that air pressure is maintained at optimal levels.
Cylinders: Cylinders convert the energy from compressed air into linear motion. They are used to push, pull, or lift objects in various operations, providing mechanical force where needed.
Air Filters: These ensure that the compressed air used in the system is free from contaminants, such as dust or moisture, which could cause damage or inefficiency.
Electrical Connections Overview
Understanding the layout and structure of electrical connections is crucial for efficient operation. This section provides a comprehensive look at how different components are interconnected, ensuring proper functionality and safety in the system.
Key Components in Electrical Systems
- Main power supply units
- Control modules and circuits
- Sensors and relays
Common Connection Types
- Wire harnesses for secure connections
- Terminal blocks for organized wiring
- Plug-and-play connectors for easy maintenance
Common Replacement Parts for Vactor 2100
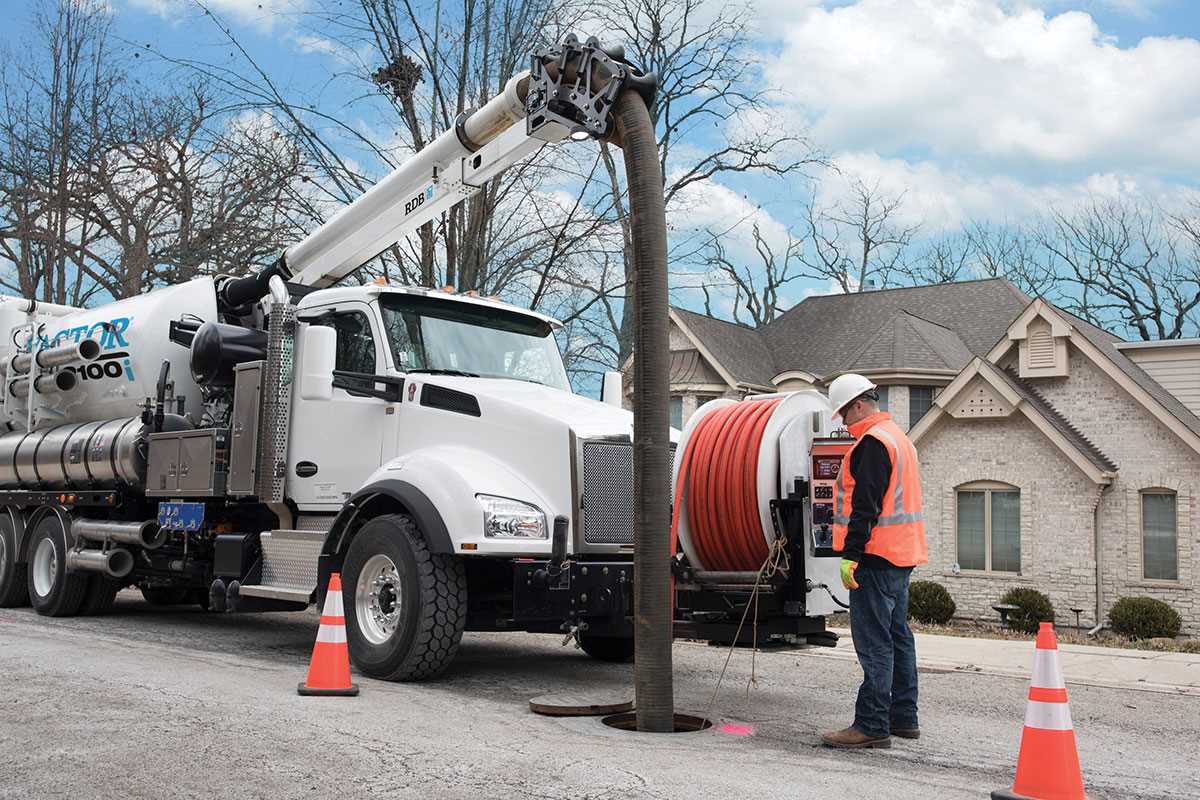
When maintaining heavy-duty equipment, understanding the essential components that may require replacement is crucial. Regular use can lead to wear and tear on various elements, impacting performance and efficiency. Knowing which components are commonly replaced can help in timely maintenance and reduce downtime.
Among the frequently replaced items are filters that ensure optimal operation by trapping contaminants. Seals and gaskets are also vital, as they prevent leaks and maintain the integrity of the system. Additionally, hoses and fittings should be inspected regularly for signs of damage, as they play a key role in fluid transfer.
Another critical component includes pumps, which may need replacement due to prolonged use or wear. It is essential to have a reliable source for these items to ensure compatibility and quality. Lastly, keeping spare parts on hand can facilitate quick repairs, ensuring that the equipment remains functional and efficient.
Maintaining the Water Pump Assembly
The upkeep of the water pump unit is essential for ensuring efficient operation and longevity of the equipment. Regular maintenance helps to prevent malfunctions and extends the lifespan of the components involved. This section outlines key practices for keeping the assembly in optimal condition.
To effectively maintain the water pump assembly, consider the following steps:
- Inspect the assembly regularly for any signs of wear or damage.
- Check the seals and gaskets for leaks and replace them as necessary.
- Ensure that the connections are secure and free from corrosion.
- Clean the pump inlet and outlet to prevent blockages.
- Monitor the operational temperature and pressure to identify potential issues early.
In addition to these practices, it is crucial to follow the manufacturer’s guidelines for maintenance schedules and procedures. Keeping a log of maintenance activities can help track the condition of the assembly over time, allowing for timely interventions when needed.
By adhering to these maintenance tips, you can ensure that the water pump assembly functions effectively, contributing to the overall performance of the system.
Essential Filters and Their Placement
Proper filtration is crucial for maintaining the efficiency and longevity of any vacuum system. Understanding the types of filters involved and their specific locations can significantly enhance the performance of the equipment. This section outlines the essential filters that play a vital role in ensuring optimal operation.
Primary Filter: This filter is designed to capture large particles and debris, preventing them from entering the system. It is typically positioned at the inlet, where air and contaminants first enter. Regular inspection and cleaning are necessary to maintain airflow and system efficiency.
Secondary Filter: Located downstream from the primary filter, the secondary filter provides additional protection by trapping finer particles that may pass through the first stage. Ensuring that this filter is replaced as per the manufacturer’s recommendations can prevent damage to sensitive components.
HEPA Filter: High-Efficiency Particulate Air filters are essential for environments requiring high cleanliness standards. Positioned at the exhaust, they ensure that no harmful particles are released back into the atmosphere. Regular maintenance of this filter is vital to sustain air quality.
By understanding the functions and placements of these essential filters, operators can ensure their equipment runs smoothly and efficiently, minimizing downtime and repair costs.
The Role of Valves in the Vactor 2100
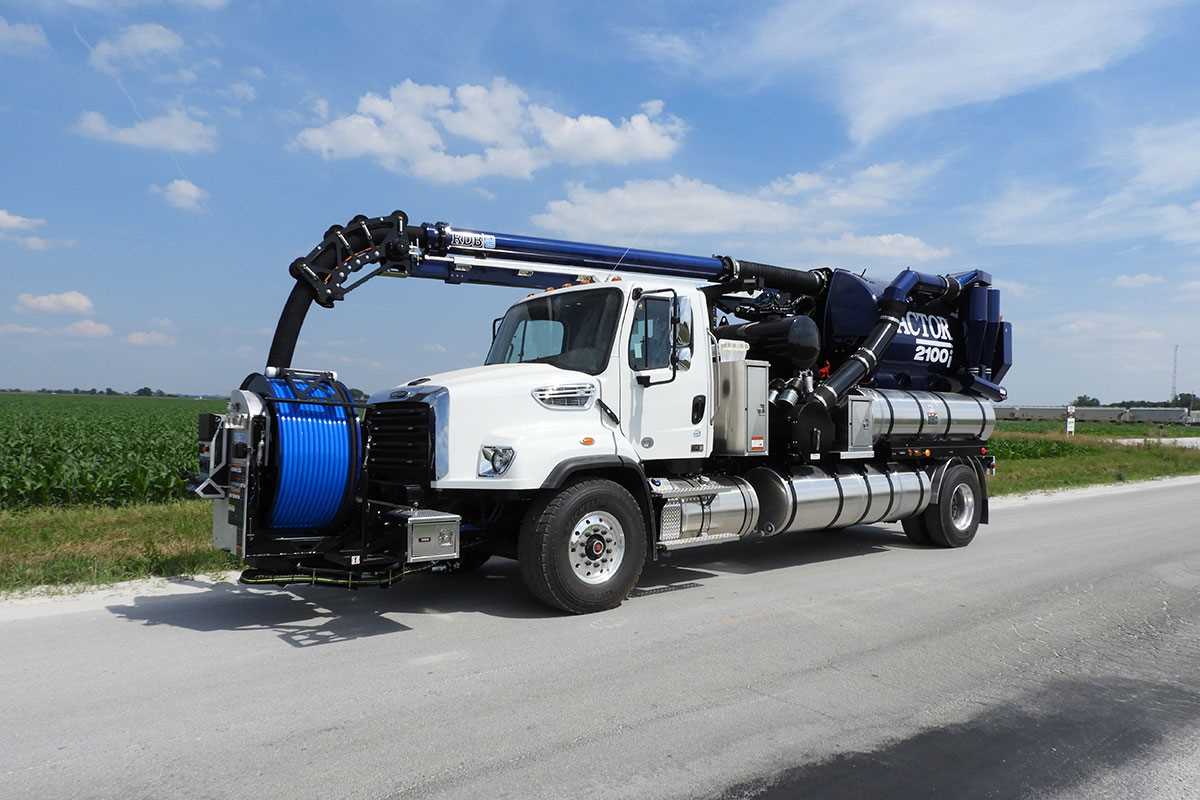
In complex machinery, the functionality of components is crucial for efficient operation. One such element that significantly influences performance is the valve system. These mechanisms regulate the flow of fluids, ensuring that operations proceed smoothly and effectively. Understanding their role is essential for maintaining optimal functionality and performance of the entire system.
Functionality of Valves
Valves are integral to controlling the direction and flow rate of liquids or gases within the system. By opening or closing, they allow or restrict passage, thus influencing the overall efficiency. Proper valve operation can enhance responsiveness and prevent issues related to pressure and flow disruptions.
Maintenance Considerations
Regular maintenance of the valve system is essential for long-term reliability. This includes inspecting for wear, ensuring seals are intact, and verifying that operational mechanisms function correctly. Timely maintenance can prevent failures and extend the lifespan of the machinery.
Understanding Hose and Reel Mechanisms
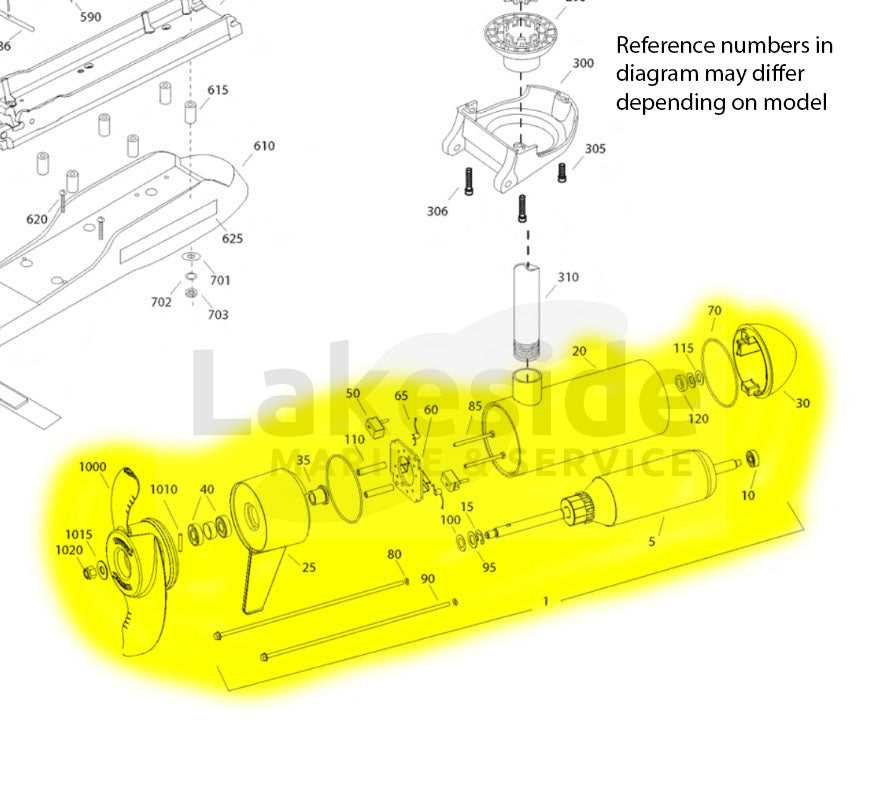
The functioning of flexible conduits and their storage systems is essential for efficient operation in various applications. These components work together to ensure smooth deployment and retraction, enhancing usability and performance.
In this section, we will explore the fundamental aspects of these systems:
- Hose Types:
- Flexible materials that cater to different pressures and environments.
- Variety in lengths and diameters to accommodate diverse tasks.
- Reel Designs:
- Manual and automatic options for ease of use.
- Durable constructions that ensure longevity and reliability.
- Mechanisms of Operation:
- Methods for deploying and retracting hoses with minimal effort.
- Importance of maintaining tension to prevent kinks and tangles.
Understanding these elements is crucial for optimal performance and maintenance of the systems in which they are integrated.
Inspecting the Debris Body Components
Regular examination of the debris collection components is essential for ensuring optimal performance and longevity of the equipment. This process involves assessing various parts that play a critical role in the efficient operation of the system.
To begin, it is important to check for any signs of wear and tear on the surfaces and connections of the debris body. Visual inspections should focus on identifying cracks, corrosion, or loose fittings that may impact functionality. Additionally, any accumulated debris or residue should be cleared to maintain proper flow and efficiency.
Furthermore, examining the seals and gaskets is crucial, as these components prevent leaks and ensure that materials are contained within the body. Regular maintenance of these elements will help in preventing unexpected breakdowns and enhancing overall operational reliability.
How the Vacuum System Operates
The efficiency of a vacuum system relies on its ability to create a significant pressure difference, which allows for the effective removal of debris and liquids. This system is designed to maintain a consistent airflow, enabling it to draw in materials through a series of strategically placed inlets and hoses.
Key Components of the System
Essential elements of the vacuum mechanism include a powerful motor, a fan for airflow management, and filtration systems that ensure clean operation. Each component plays a critical role in maintaining optimal performance and extending the longevity of the equipment.
Operational Process
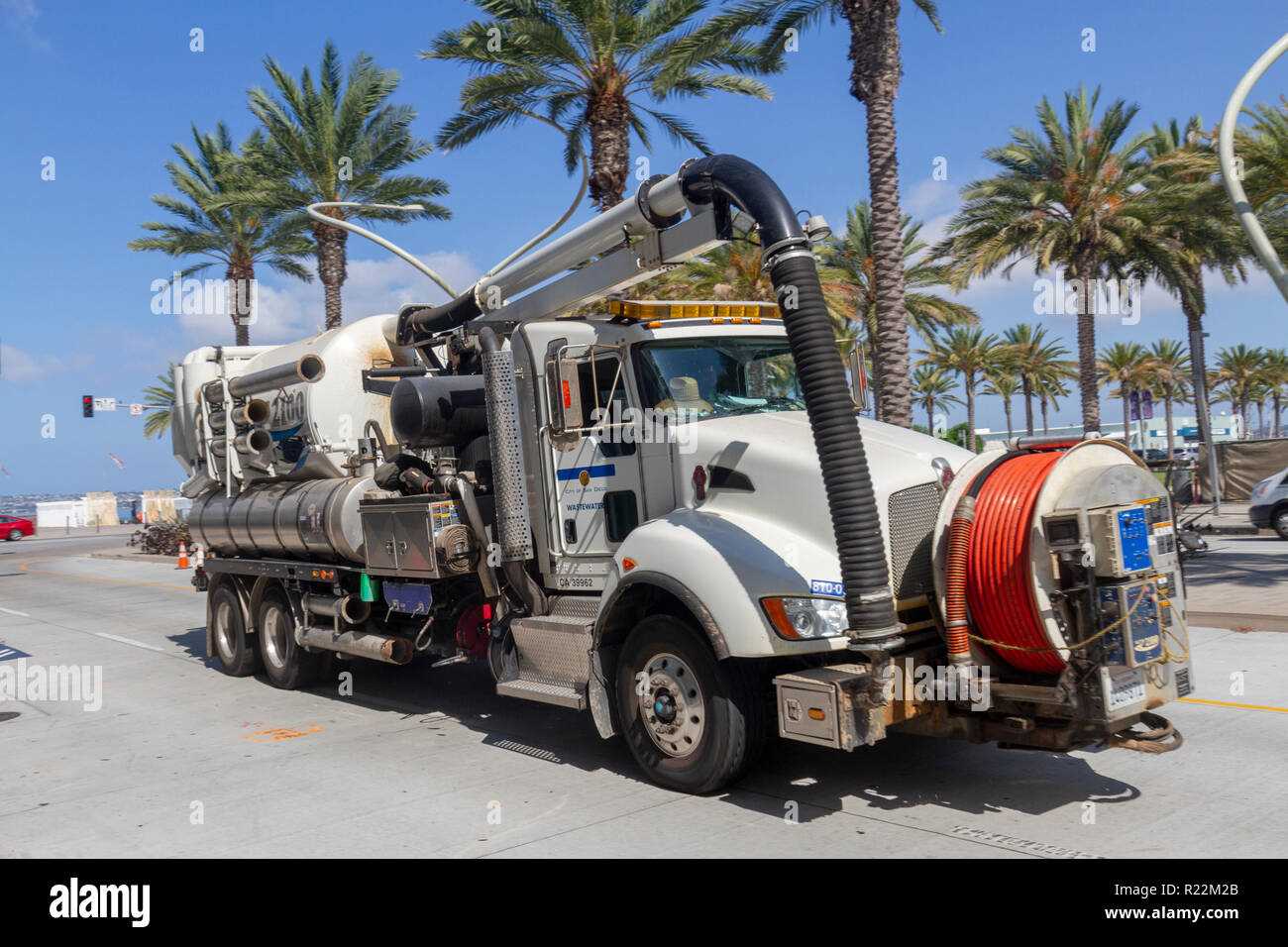
During operation, the motor generates suction, creating a low-pressure area that draws material into the intake. As the air and debris flow through the system, filters trap particulates, preventing them from re-entering the environment. This continuous cycle of suction and filtration is vital for achieving effective cleaning results.