Power Unit and Drive System Layout
The design of the power source and the mechanical drive arrangement is essential for achieving smooth and consistent operation. It includes various elements that work together to transfer energy efficiently, ensuring precise movement and control during operation.
The energy system typically consists of a motor or other power-generating unit that supplies the necessary force to operate. This force is transmitted through a series of components, which may include belts, chains, or gears, each playing a role in maintaining proper functionality and performance.
The drive arrangement helps in translating this energy into linear or rotational motion, depending on the requirements. The setup allows for adjustable speeds and torque, providing flexibility for different tasks and operational conditions.
Hydraulic Features and Functionality
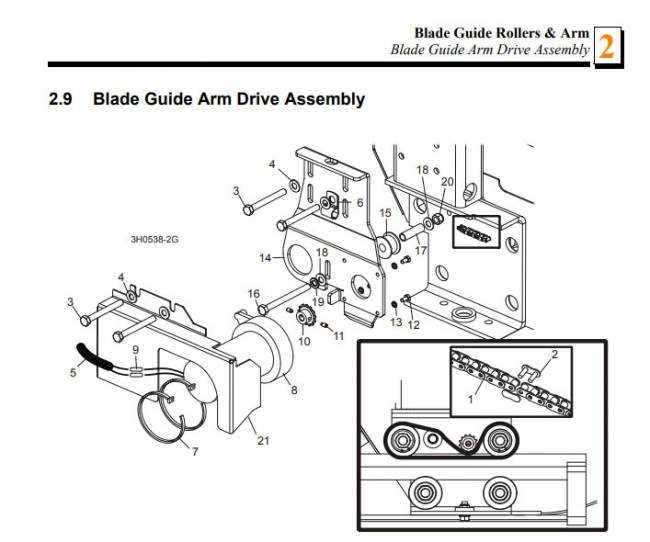
Understanding how hydraulic mechanisms contribute to operational efficiency is essential in maintaining smooth performance. These systems offer controlled power to various components, allowing for precise adjustments and automated processes that would otherwise require manual effort. Hydraulics provide the force necessary to handle heavy-duty tasks with minimal input from the operator.
The fluid-driven technology enhances the overall handling and maneuverability, ensuring seamless transitions between functions. This not only improves productivity but also ensures consistency in performance by delivering reliable energy transfer across key operations. The flexibility of this system also supports various customization options, tailored to the specific needs of the user.
Tracking System for Accurate Operation
Ensuring precision during operation is critical in any machinery. A reliable tracking mechanism enhances efficiency, allowing for consistent performance and minimizing errors. This section delves into the essential components and functionalities that contribute to an effective monitoring system.
The following elements play a vital role in maintaining an accurate tracking process:
- Sensors: Devices that detect and measure various parameters to provide real-time feedback.
- Control Units: Central systems that process sensor data and adjust machine operations accordingly.
- Calibration Tools: Instruments used to fine-tune the tracking system, ensuring it operates within desired specifications.
Each of these components works together to facilitate a seamless operational flow. Regular maintenance and updates are essential for optimizing the system’s performance.
- Perform routine inspections of sensors to ensure accurate readings.
- Regularly update control unit software for enhanced functionality.
- Utilize calibration tools to adjust settings and maintain precision.
By prioritizing these practices, operators can achieve greater accuracy and efficiency, resulting in improved outcomes and reduced downtime.
Control Panel and Interface Elements
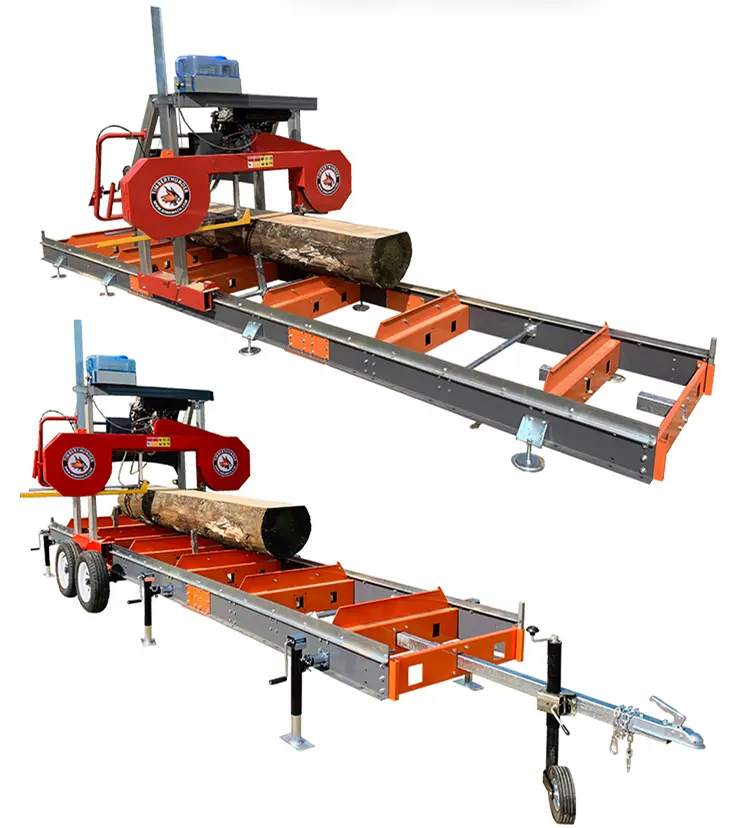
The control interface serves as the central hub for operators, providing essential tools and features for efficient management. Understanding the layout and functions of these components is crucial for optimal machine performance.
This section explores the various elements found within the control setup, detailing their purposes and interactions. Key components typically include:
- Power Switch: Activates the entire system, ensuring safe startup and shutdown procedures.
- Speed Control: Allows users to adjust the operational pace, tailoring it to specific tasks.
- Indicator Lights: Provides visual feedback on machine status, such as power availability or operational readiness.
- Emergency Stop Button: A critical safety feature that instantly halts operations in case of emergencies.
- Display Screen: Shows real-time information and settings, aiding in monitoring and adjustments.
Familiarity with these interface elements enhances user confidence and promotes safer, more efficient operation.
Sawing Bed and Material Handling
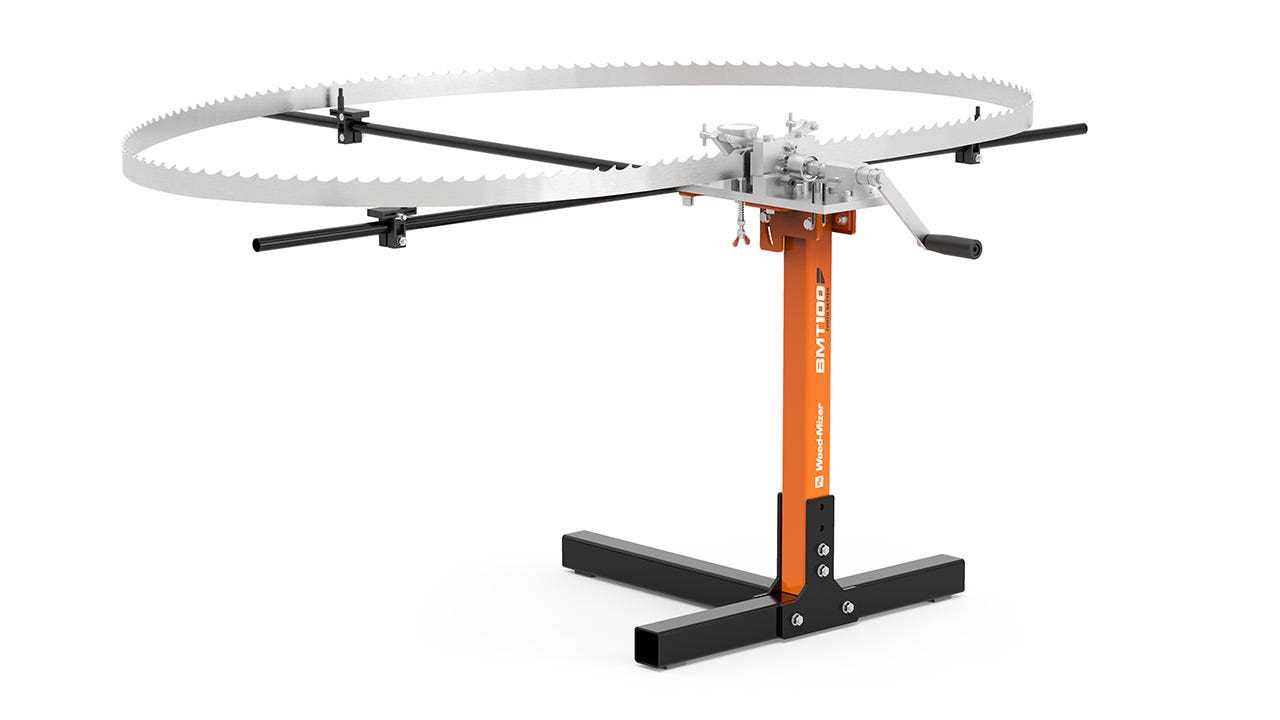
The foundation of any effective cutting operation lies in the arrangement that supports the materials being processed. An optimal setup ensures precision and stability, facilitating smooth workflow and efficiency during the cutting process. Understanding the components involved in material support and movement is crucial for achieving high-quality results.
Support Structure
The support system consists of a robust framework designed to hold the material securely in place while it is being cut. This structure typically features adjustable supports, allowing for various lengths and sizes of materials. An efficient support design minimizes movement and vibrations, contributing to more accurate cuts.
Material Movement
Effective handling of materials is essential for maximizing productivity. Incorporating rollers or conveyor systems can streamline the process of loading and unloading materials. These mechanisms not only enhance the speed of operation but also reduce physical strain on operators, allowing for safer and more efficient workflow.
Lubrication System for Optimal Performance
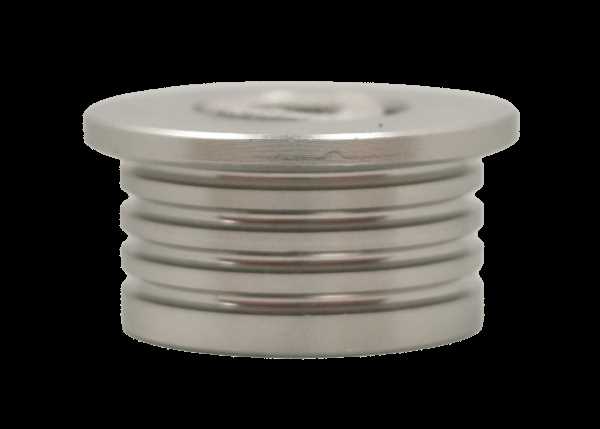
Ensuring smooth operation of machinery hinges on a well-designed lubrication mechanism. This essential system minimizes friction between moving components, promoting longevity and enhancing efficiency. Regular maintenance of this system is crucial for maintaining the reliability and performance of equipment.
Effective lubrication plays a vital role in preventing wear and tear, reducing heat generation, and protecting against corrosion. By creating a protective barrier, lubricants facilitate the seamless movement of parts, which in turn minimizes downtime and increases productivity.
Understanding the various components of the lubrication system is key to its upkeep. Regular checks on oil levels, the condition of filters, and the integrity of hoses can prevent costly repairs. Implementing a consistent schedule for lubrication tasks not only extends the lifespan of machinery but also optimizes overall operational effectiveness.
Safety Mechanisms and Protective Gear
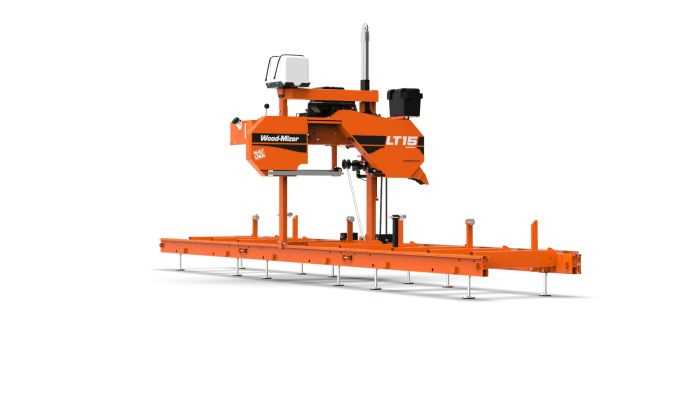
Ensuring a safe working environment is paramount when operating heavy machinery. Effective safety features and appropriate protective equipment play a crucial role in minimizing risks associated with the use of cutting tools. These elements work together to safeguard the operator and those nearby from potential hazards.
Modern machinery incorporates various safety mechanisms, such as emergency stop buttons, safety guards, and automatic shut-off systems. These features are designed to prevent accidents by allowing quick responses in case of unexpected situations. Regular maintenance and inspection of these safety devices are essential to ensure their functionality and reliability during operation.
In addition to built-in safety features, wearing suitable protective gear is vital. Items such as helmets, eye protection, hearing protection, and sturdy footwear are indispensable for minimizing injury risks. Choosing the right equipment and adhering to safety protocols enhances overall workplace safety and contributes to a more efficient operational process.
Maintenance and Spare Parts Guide
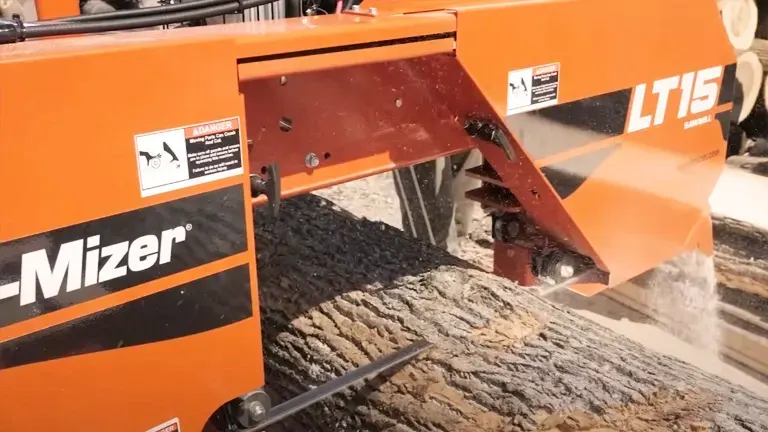
Proper upkeep and timely replacements are crucial for ensuring optimal performance and longevity of machinery. This section outlines essential practices and components necessary for maintaining equipment effectively. Understanding the various elements involved in care and repairs will help operators minimize downtime and enhance efficiency.
Routine Maintenance Practices
- Regularly inspect moving parts for wear and tear.
- Keep all surfaces clean to prevent buildup that could impede operation.
- Lubricate components as specified in the manufacturer’s guidelines.
- Monitor fluid levels and replace filters as needed.
- Test safety features to ensure proper functioning.
Key Components to Keep in Stock
- Belts: Essential for the transfer of motion between parts.
- Blades: Critical for cutting efficiency; maintain sharpness or replace as necessary.
- Bearings: Key to smooth operation; check for signs of wear regularly.
- Seals and Gaskets: Prevent leaks and maintain pressure in systems.
- Electrical Components: Ensure wiring and connectors are intact to avoid electrical failures.