Gears |
Regulate speed and torque by altering the ratio between input and output. |
Front Loader Maintenance Tips and Tricks
Proper upkeep of your machine ensures optimal performance and extends its working life. Regular inspections and timely adjustments can prevent unnecessary breakdowns and keep your equipment running smoothly for years to come.
Below are key recommendations to maintain your front-end loader:
- Check fluid levels: Make sure hydraulic and engine fluids are at the appropriate levels to avoid malfunctions and ensure smooth operation.
- Inspect the tires: Consistently check for proper tire inflation and wear, which can affect stability and traction.
- Grease pivot points: Lubricate all moving parts regularly to minimize friction and prevent component damage.
- Examine hydraulic hoses: Look for any signs of leaks or wear on hoses and fittings to prevent loss of hydraulic pressure.
Following these essential practices will help keep your equipment in top condition, reducing downtime and prolonging its efficiency.
Inspecting and Replacing Brake Systems
Ensuring the proper functioning of the braking components is essential for the safe operation of heavy equipment. Over time, wear and tear can diminish their effectiveness, making it important to routinely check for signs of deterioration and address any issues promptly. Regular assessment and timely adjustments are key to maintaining reliable performance.
Identifying Wear and Tear
The first step in evaluating the condition of the brakes is a thorough visual inspection. Look for any noticeable signs of wear, such as thinning or cracking on critical components. Additionally, check for any unusual sounds or reduced responsiveness during operation, which could indicate underlying issues that require attention.
Replacement
Electrical Wiring Diagram Overview
An electrical schematic is essential for understanding the flow of current throughout a machine’s various systems. It offers insight into how power is distributed, ensuring that each component receives the necessary energy to function properly.
Understanding Connections and Pathways
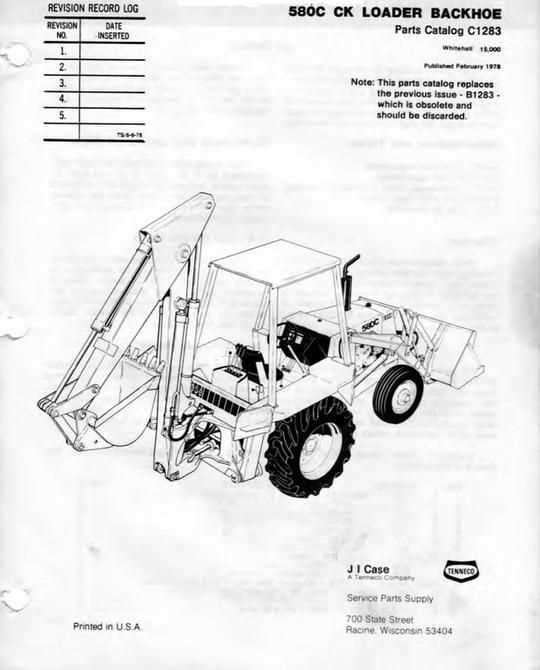
Each line in the diagram represents a conductive route, linking different elements such as switches, relays, and motors. By tracing these connections, it’s possible to identify how the circuits interact, which can help in pinpointing areas where electrical flow might be interrupted or compromised.
Key Symbols and Their Functions
The schematic uses standardized symbols to depict components like fuses, resistors, and capacitors. Recognizing these symbols and their respective functions is crucial for interpreting the system and ensuring that all connections are properly established and maintained.
Cabin Controls and Operator Features
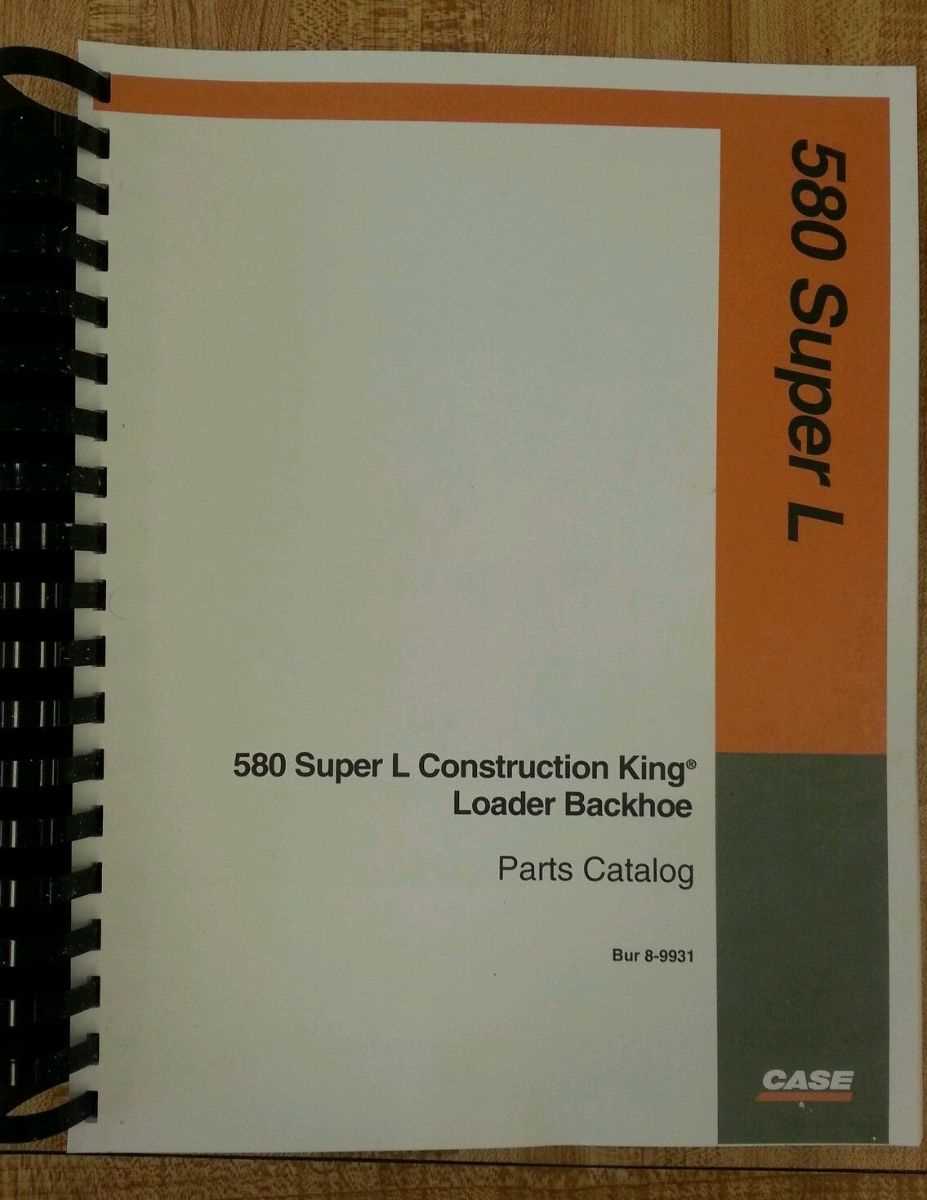
The interior control system of this machinery offers an intuitive setup designed to enhance productivity and ensure ease of use. With strategically placed levers and buttons, the operator is empowered to handle tasks efficiently, minimizing physical strain and optimizing workflow.
Control Layout
The control panel is structured for quick access, with each component clearly labeled to simplify operation. From steering mechanisms to hydraulic systems, everything is within arm’s reach, allowing the operator to maintain focus on the task at hand.
- Easy-to-use joystick for movement coordination
- Foot pedals aligned for precise control
- Ergonomic seating with adjustable positioning
Enhanced Operator Comfort
The cabin design prioritizes the comfort of the individual, ensuring long hours in the driver’s seat are manageable. With features like climate control and adjustable seating, the cabin environment can be tailored to personal preference.
Hydraulic Pump Assembly Breakdown
The core function of the hydraulic pump system revolves around efficiently converting mechanical power into hydraulic energy. This critical component channels fluid under high pressure, ensuring seamless operation of various interconnected systems. Understanding its design and structure helps in identifying potential inefficiencies or issues within the system.
Main Components:
- Housing: Protects internal elements and helps maintain fluid integrity.
- Pistons and Gears: These elements play a vital role in moving fluid through the system, creating pressure that powers other components.
- Valves: Control the direction and flow rate, regulating pressure within the system.
- Seals: Prevent leakage and ensure consistent pressure within the assembly.
Wheel Alignment and Tire Care
Proper wheel alignment and maintenance of tires are essential for ensuring optimal performance and longevity of your vehicle. Neglecting these aspects can lead to uneven wear, compromised handling, and decreased fuel efficiency. This section highlights the importance of maintaining correct alignment and caring for tires to enhance overall functionality.
Importance of Wheel Alignment
Correct alignment of the wheels is crucial for several reasons. Firstly, it improves steering accuracy, allowing for smoother navigation and enhanced safety. Additionally, properly aligned wheels help distribute weight evenly across tires, which promotes even tread wear. This not only prolongs the lifespan of the tires but also contributes to better fuel efficiency, as the vehicle requires less energy to move in a straight line.
Maintaining Tire Condition
Tire maintenance involves regular inspections, proper inflation, and timely rotation. Checking tire pressure regularly ensures they are inflated to the manufacturer’s specifications, which is vital for optimal grip and performance. Rotating tires every few thousand miles helps to promote even wear across all tires, extending their life and maintaining effective traction. Moreover, inspecting for signs of damage, such as cracks or bulges, can prevent unexpected failures on the road.
Fuel System Diagnostics and Solutions
The functionality of a machinery’s energy delivery system is crucial for optimal performance. Understanding how to identify issues within this system can greatly enhance operational efficiency and longevity. This section will delve into common problems encountered within the energy supply mechanism and provide effective remedies.
Identifying Symptoms: Observing signs of distress, such as irregular engine performance or starting difficulties, is the first step in troubleshooting. Pay attention to abnormal noises, stalling, or decreased power output, as these may indicate underlying complications.
Common Issues: Frequent challenges include fuel contamination, inadequate fuel flow, and air leaks. Contaminated fuel can lead to clogs, while insufficient flow hampers the engine’s ability to perform efficiently. Furthermore, air entering the system disrupts the proper fuel mixture, causing erratic engine behavior.
Diagnostic Techniques: Employing diagnostic tools can streamline the troubleshooting process. Use a fuel pressure gauge to assess the integrity of the system and check for consistent pressure levels. Visual inspections of fuel lines and filters can also reveal potential blockages or leaks.
Implementing Solutions: Addressing the identified issues involves several strategies. Cleaning or replacing filters, purging contaminants from the system, and ensuring all connections are secure can rectify many common problems. Additionally, maintaining a regular inspection schedule is vital to prevent future complications.
Conclusion: Proactively diagnosing and resolving issues within the energy delivery system not only ensures peak performance but also prolongs the life of the equipment. By being vigilant and addressing problems promptly, operators can maintain efficiency and reliability.