The guide bar plays a crucial role in the overall effectiveness of the cutting tool. Its structure ensures smooth movement and alignment during operation, allowing the cutting mechanism to work with precision. The quality and type of the guide bar directly affect the stability, speed, and accuracy of the cut, making it a vital component in achieving optimal results.
Understanding the importance of the guide bar helps in choosing the right one for specific tasks, as well as maintaining the tool’s performance over time. Below is a basic overview of key guide bar characteristics and how they influence cutting efficiency:
Feature |
Impact on Performance |
Length |
Longer bars increase reach, while shorter ones provide better control. |
Understanding the Tensioning System
The tensioning system plays a crucial role in maintaining the optimal performance of your equipment. Ensuring the correct balance and adjustment is key to both safety and functionality. A well-tuned mechanism helps to reduce wear and improve efficiency during operation.
Proper Adjustment: Regularly checking and adjusting the tension is necessary to prevent excessive strain. Over-tightening can lead to premature wear, while insufficient tension may result in slippage or instability. The balance between flexibility and firmness is essential for smooth and effective usage.
Maintenance and Inspection: Routine inspection of the tensioning components ensures that they remain in good working order. Any signs of loosening or wear should be
Clutch Assembly Breakdown
This section provides an overview of the components and functions of the clutch assembly within a power tool. Understanding the elements involved is essential for maintenance and troubleshooting, ensuring optimal performance during operation.
Key Components
The clutch assembly consists of several crucial parts that work together to engage and disengage the power transmission. Each component plays a specific role in the overall functionality, allowing for smooth operation and effective torque transfer.
Component |
Description |
Clutch Drum |
Houses the friction components and engages with the drive mechanism. |
Friction Discs |
Provide the necessary grip to transmit power when engaged. |
Spring Mechanism |
Controls the engagement force, allowing for smooth transitions. |
Drive Shaft |
Connects the clutch assembly to the engine, transmitting power. |
Functionality and Maintenance
Regular inspection of the clutch assembly is vital for maintaining performance and prolonging the life of the tool. Ensuring all components are free from wear and damage will help avoid potential issues during operation.
Fuel System Overview and Maintenance
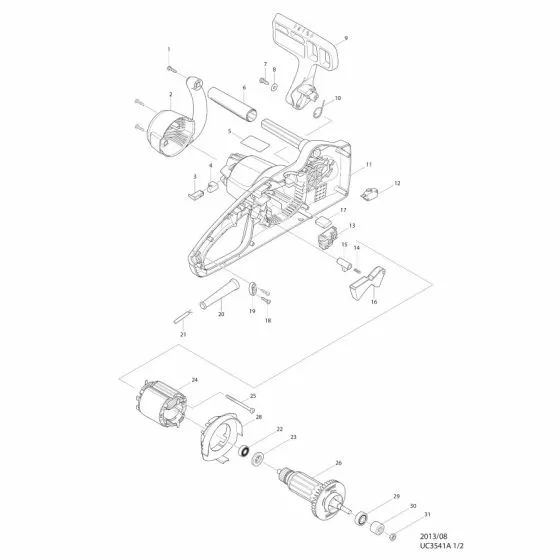
The fuel system is a critical component of any cutting device, ensuring that the engine receives the proper mixture of fuel and air for optimal performance. Understanding its function and how to maintain it is essential for longevity and efficiency. Regular maintenance can prevent issues such as poor performance, starting difficulties, and increased emissions.
Proper upkeep of the fuel system involves inspecting various elements to ensure they are functioning effectively. Here are the key components to consider:
Component |
Description |
Maintenance Tips |
Fuel Tank |
Holds the fuel necessary for operation. |
Regularly check for leaks and clean to prevent sediment build-up. |
Fuel Filter |
Traps impurities from the fuel before reaching the engine. |
Replace periodically as per the manufacturer’s guidelines. |
Fuel Lines |
Transport fuel from the tank to the engine. |
Inspect for cracks or wear and replace if necessary. |
Carburetor |
Mixes fuel and air in the correct proportions. |
Clean and adjust settings to maintain efficient operation. |
By regularly checking these components and performing maintenance tasks, users can enhance performance and extend the lifespan of the device.
Carburetor Functionality and Troubleshooting
The carburetor plays a crucial role in the operation of various small engines by mixing air and fuel in the appropriate ratio for combustion. This essential component ensures that the engine runs smoothly and efficiently, impacting overall performance. Understanding its functionality can aid in identifying common issues that may arise during use.
Common Issues: When the mixture is not correctly calibrated, it can lead to poor engine performance, including difficulty starting, stalling, or uneven operation. Signs of malfunction may include excessive smoke, reduced power, or unusual noises. Regular maintenance and inspection can help prevent these issues.
Troubleshooting Steps: Start by examining the air filter to ensure it is clean and unobstructed. A clogged filter can restrict airflow, affecting the mixture quality. Next, check the fuel supply; stale or contaminated fuel can hinder performance. If problems persist, it may be necessary to adjust the carburetor settings or clean its internal components to restore optimal functionality.
Preventative Maintenance: Regularly inspect and service the carburetor as part of routine maintenance to enhance longevity and performance. Keeping it clean and properly adjusted will contribute to efficient engine operation and reduce the likelihood of unexpected issues.
Air Filter and Its Importance
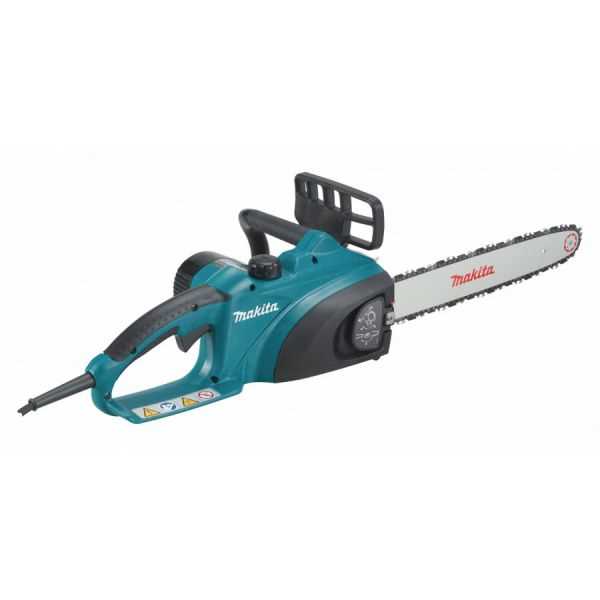
The air filter plays a crucial role in ensuring optimal performance of outdoor power equipment. Its primary function is to prevent dirt and debris from entering the engine, thereby protecting it from potential damage. A clean and efficient air filter is vital for maintaining the longevity and reliability of the equipment.
Functionality of the Air Filter
An effective air filter allows the engine to breathe properly, providing the necessary airflow for combustion. When the filter is clogged, the engine struggles to receive sufficient air, leading to reduced power output and increased fuel consumption. Regular maintenance and replacement of the air filter can significantly enhance the overall efficiency of the machine.
Signs of a Worn-Out Filter
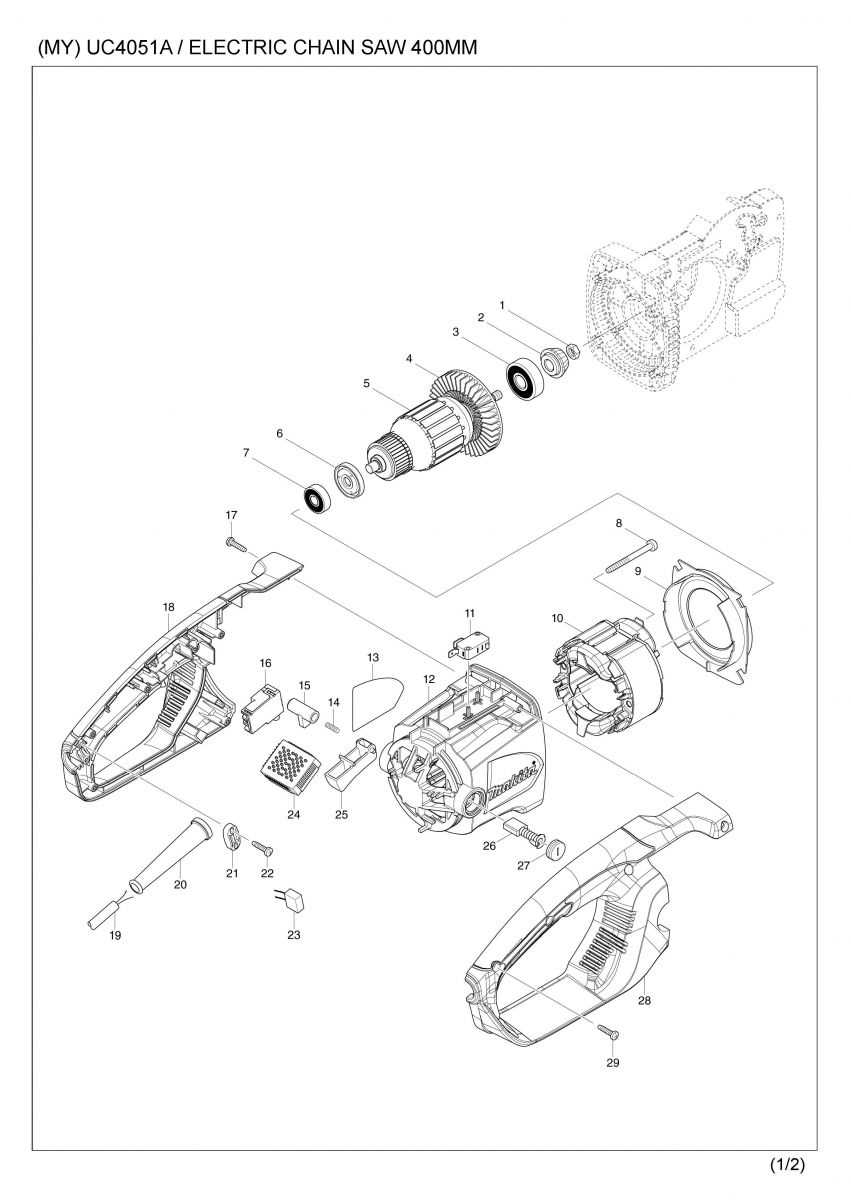
Indicators that the air filter may need attention include decreased performance, unusual engine noises, or visible dirt accumulation. Ignoring these signs can result in more severe engine issues and costly repairs. Ensuring the air filter is clean and functioning correctly is essential for optimal operation.
Ignition System Parts and Operation
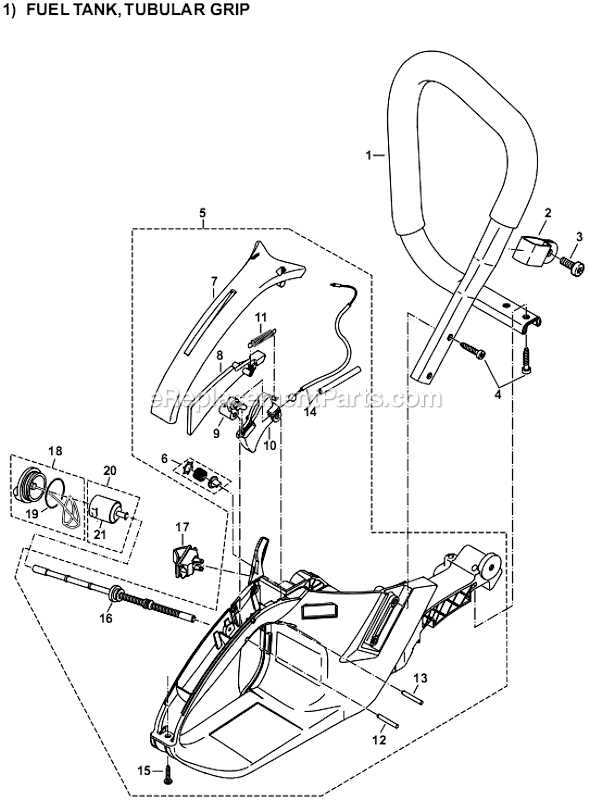
The ignition system plays a crucial role in the functionality of various motorized tools. It is responsible for initiating combustion within the engine, ensuring that the device operates efficiently and reliably. Understanding the components and their interactions within this system is essential for maintaining optimal performance and troubleshooting any issues that may arise.
Key Components of the Ignition System
The ignition mechanism consists of several integral components. These include the spark plug, which generates the spark needed for ignition, and the ignition coil, which transforms the battery voltage into a higher voltage. Additionally, the flywheel plays a pivotal role by creating a magnetic field that aids in the ignition process. Each of these elements works in unison to ensure that the combustion process occurs at the right moment.
Operational Process
During operation, the ignition system begins by sending a current to the ignition coil, which amplifies the voltage. This high voltage is then directed to the spark plug, producing a spark that ignites the fuel-air mixture in the engine’s combustion chamber. The timing of this spark is critical; it must occur at precisely the right moment to maximize power and efficiency. Any malfunction within the ignition system can lead to starting difficulties or reduced engine performance.
Oil Pump Mechanism for Chain Lubrication
The oil pump is a crucial component in ensuring the smooth operation of cutting equipment. Its primary function is to deliver lubricant to the chain, minimizing friction and wear during use. By maintaining an appropriate oil flow, the mechanism contributes to the longevity and efficiency of the tool.
Functionality of the Oil Pump
This mechanism works by drawing oil from a reservoir and distributing it along the chain. The design typically incorporates a gear or diaphragm system, which regulates the flow rate based on the operational speed. As the tool is activated, the pump adjusts to deliver the necessary amount of lubricant, ensuring that the chain remains adequately saturated.
Maintenance and Care
Regular maintenance of the oil pump is essential for optimal performance. Users should frequently check the oil level and inspect for any blockages or leaks in the delivery system. Cleaning the pump and its components will help maintain a steady flow of lubricant, preventing potential damage to the cutting elements.
Handle Components and Vibration Control
The grip assembly of power tools plays a crucial role in user comfort and control during operation. Properly designed handle components ensure that the tool is easy to maneuver while minimizing user fatigue. Additionally, vibration dampening systems are essential for enhancing overall handling experience and reducing potential strain on the operator.
Importance of Ergonomic Design
Ergonomic design in handle components is vital for promoting a natural grip and reducing discomfort during prolonged use. Features such as contoured shapes and soft materials can enhance the user experience by allowing for a secure hold and less hand fatigue. This is especially important when performing repetitive tasks, as it enables better control and precision.
Vibration Dampening Techniques
Effective vibration control mechanisms are integral to enhancing safety and comfort. Various technologies, including rubber isolators and composite materials, are utilized to absorb and dissipate vibrations generated during operation. These features not only improve user comfort but also prolong the lifespan of the tool by reducing wear on internal components.
Safety Features and Their Functions
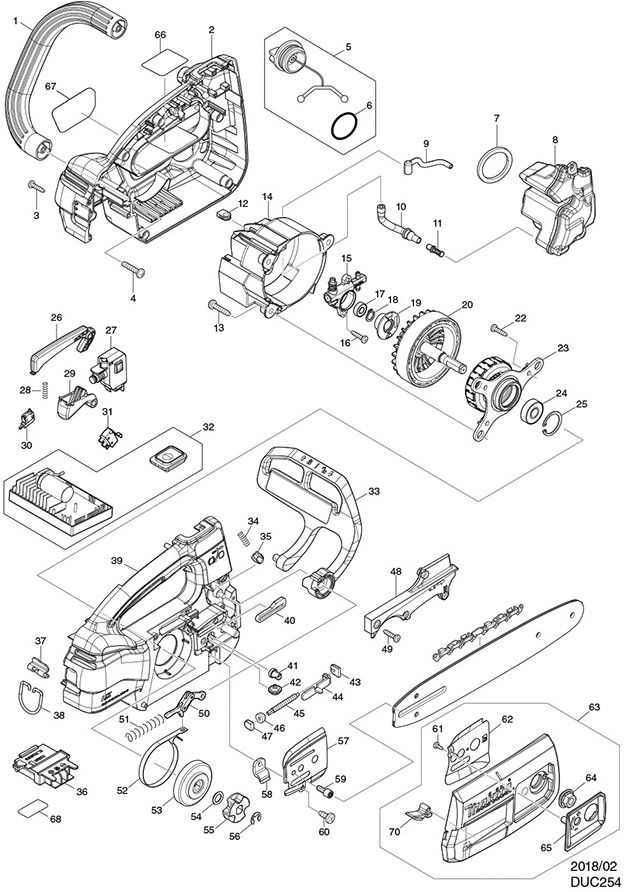
Understanding the safety mechanisms in power tools is crucial for ensuring the well-being of users and those around them. These features are designed to minimize the risk of accidents and enhance user control during operation. By familiarizing oneself with these elements, operators can utilize their tools more effectively while prioritizing safety.
Key Safety Mechanisms
- Chain Brake: This feature halts the movement of the chain in the event of kickback, preventing potential injury.
- Throttle Lock: The throttle lock prevents accidental acceleration, ensuring that the tool only operates when intended.
- Hand Guard: Positioned in front of the handle, this guard shields the user’s hands from debris and unintended contact with the cutting edge.
- Low Kickback Chain: Designed to reduce the risk of kickback, this type of chain helps maintain better control during cutting.
Importance of Safety Features
Each safety feature serves a specific function that contributes to the overall security of the user. By integrating these mechanisms, manufacturers aim to reduce the likelihood of accidents, fostering a safer working environment. Regular maintenance and adherence to safety guidelines are essential to ensure these features function effectively.