Guide Bar Alignment: Ensuring that the guide bar remains straight and properly aligned is crucial for accurate cuts. A bent
Sprocket Mechanism: How It Works
The sprocket mechanism is a crucial component in various machinery that facilitates the transfer of motion and power. It operates by engaging with a chain or belt, creating a system of interconnected movement that enhances efficiency and performance. Understanding its functionality can provide insights into its importance in mechanical designs.
This mechanism consists of a toothed wheel, known as a sprocket, that meshes with a corresponding chain. When the sprocket rotates, it pulls the chain along, translating rotary motion into linear motion. This interaction allows for smooth operation and is essential for driving other parts of the equipment effectively.
One key aspect of the sprocket mechanism is its ability to change the direction of force. By adjusting the size and arrangement of the sprockets, designers can optimize the torque and speed of the system. This versatility makes it a vital element in many applications, ranging from simple tools to complex machinery.
Regular maintenance of the sprocket and chain is essential to ensure longevity and optimal performance. Wear and tear can lead to inefficiencies, making it necessary to inspect and replace components as needed. By understanding how the sprocket mechanism works, users can appreciate its role in enhancing operational effectiveness.
Chain Tensioning System Explained
The tensioning mechanism is a crucial element in maintaining the functionality of cutting equipment. It ensures that the cutting loop remains taut, providing optimal performance and safety during operation. Proper tensioning prevents the chain from slipping or derailing, which can lead to ineffective cuts and potential hazards.
Importance of Proper Tension
Maintaining the correct tension is essential for achieving the desired cutting efficiency. A too-loose chain can result in poor cutting performance and increased wear on the components. Conversely, an excessively tight chain can cause excessive strain on the motor and lead to premature wear of both the chain and the bar.
Adjusting the Tension
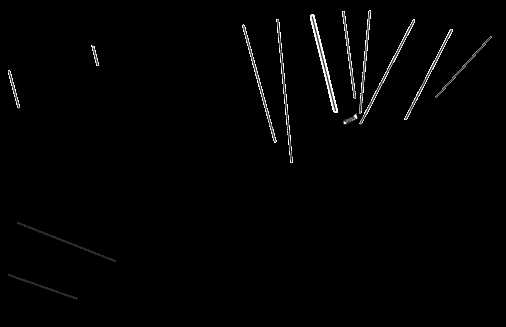
Most tensioning systems allow for easy adjustment, typically utilizing a simple mechanism that can be operated with basic tools. Regular checks and adjustments are recommended, especially before starting a new task. Familiarizing oneself with the tensioning procedure can enhance the lifespan of the equipment and improve overall performance.
Oil Pump and Lubrication System
The lubrication mechanism is essential for maintaining optimal performance and longevity of cutting equipment. This system ensures that moving parts operate smoothly by providing a consistent flow of lubricant, reducing friction and wear during operation.
Functionality of the Lubrication System
The lubrication system functions by delivering oil to critical components, particularly the guide bar and chain. This process minimizes overheating and promotes efficient cutting. It typically relies on a pump mechanism that can be either automatic or manual, allowing for precise control over the amount of oil dispensed.
Maintenance Tips
Regular maintenance of the lubrication system is crucial for ensuring effective operation. Inspecting the oil levels and cleaning the pump regularly can prevent clogs and ensure a steady oil supply. Additionally, using the appropriate type of lubricant is essential for optimal performance and to extend the life of the equipment.
Switches and Safety Features
The functionality of a cutting tool relies significantly on its control mechanisms and safety systems. These components play a vital role in ensuring both ease of use and user protection during operation. Understanding how these elements work together is crucial for safe and efficient handling.
Control switches are designed to provide immediate access to the device’s power, enabling users to start or stop the operation as needed. Many models include a dual-switch system, requiring the simultaneous engagement of two switches for activation, which enhances safety by preventing accidental starts. This design feature minimizes the risk of injury during use.
In addition to control mechanisms, various safety features are incorporated to protect users from potential hazards. Safety guards are strategically placed to shield users from debris and the cutting chain, while automatic braking systems can halt the chain’s movement almost instantly if the device is released. These enhancements are critical in maintaining a secure environment for operators.
Furthermore, ergonomic designs and safety grips improve handling and stability, allowing for better control during cutting tasks. By prioritizing user comfort and safety, these tools aim to reduce fatigue and the likelihood of accidents, making them a reliable choice for both professionals and DIY enthusiasts.
Understanding the Drive Links
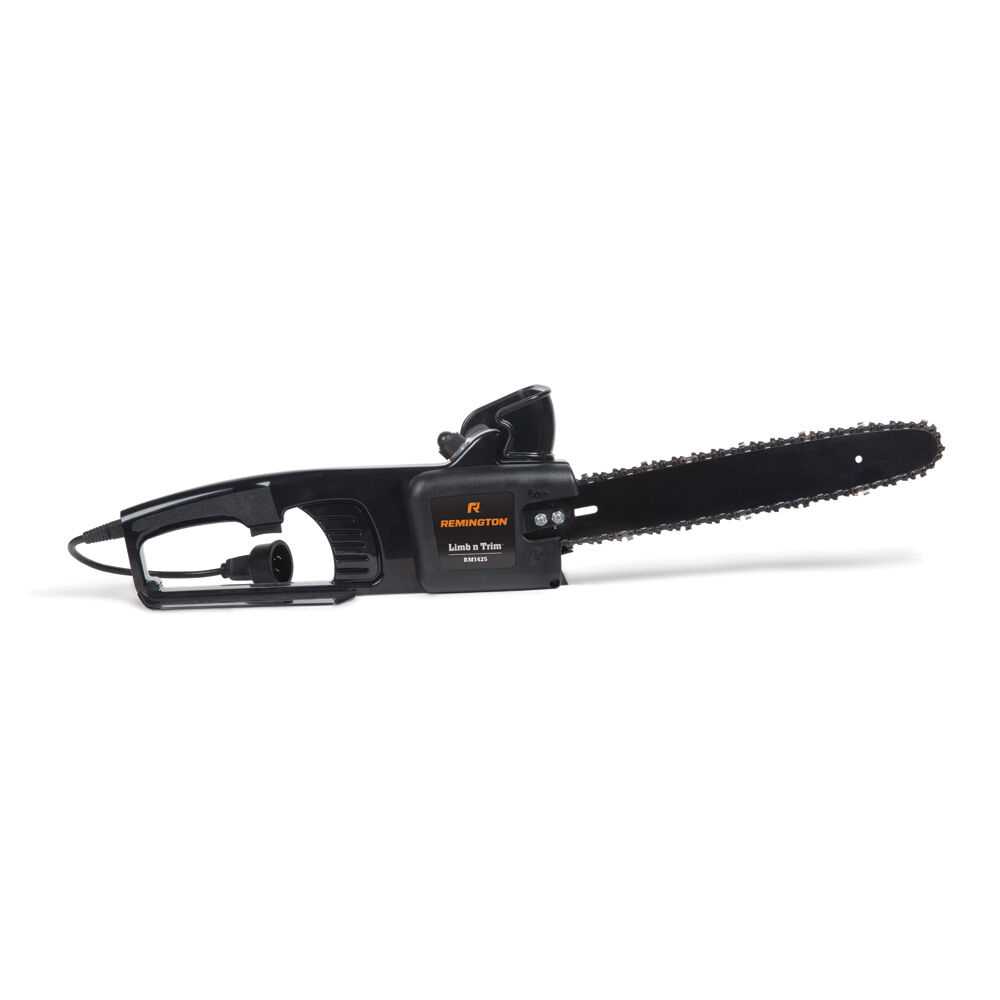
The drive links play a crucial role in the overall functionality of cutting tools. These components are responsible for transferring power from the motor to the cutting mechanism, ensuring efficient operation. A clear understanding of how these links work can enhance performance and extend the lifespan of the equipment.
Drive links are designed to fit securely within the guide bar and engage with the sprocket, allowing for smooth movement. Proper maintenance and selection of these components are essential for optimal performance.
Feature |
Description |
Material |
Drive links are commonly made from durable metals to withstand friction and wear. |
Length |
The length of drive links affects the overall cutting length and efficiency of the tool. |
Compatibility |
It’s important to select drive links that are compatible with the specific model for effective operation. |
Maintenance |
Regular inspection and cleaning help maintain optimal performance and prevent damage. |
Replacing the Chain Brake
Maintaining optimal safety features is essential when working with cutting tools. One critical component in ensuring protection is the brake mechanism. If the brake is not functioning correctly, it is necessary to replace it to prevent accidents and ensure smooth operation.
To begin the replacement process, gather the necessary tools, including a screwdriver and a replacement brake. Carefully remove any covers or guards obstructing access to the brake assembly. Pay close attention to how the original brake is positioned, as this will guide the installation of the new component.
Once the old brake is removed, take the time to inspect the surrounding area for any debris or wear that may have affected performance. After ensuring everything is clean, install the new brake in the same orientation as the original. Secure it properly, making sure it is tightly fastened to avoid any movement during use.
Finally, reassemble any removed parts and conduct a thorough check to ensure that the brake engages and releases smoothly. Regular maintenance of this safety feature is crucial for effective operation.
Common Issues with Chain Sprockets
Chain sprockets play a crucial role in the functionality of various machinery that relies on a chain drive system. Understanding the common problems associated with these components is essential for ensuring efficient operation and longevity of the equipment. This section will explore frequent issues that may arise, their symptoms, and potential solutions.
Worn or Damaged Teeth
One of the most common issues is the wear and damage of the sprocket teeth. This can lead to inefficient power transfer and increased strain on the chain. Key indicators include:
- Visible wear or deformation on the sprocket teeth.
- Difficulty in engaging with the chain.
- Increased noise during operation.
To address this issue, regular inspection and timely replacement of worn sprockets are recommended.
Misalignment
Misalignment of the chain and sprocket can cause uneven wear and reduced performance. Signs of misalignment include:
- Uneven chain wear.
- Excessive vibration during operation.
- Increased wear on other drivetrain components.
To correct misalignment, it’s important to check the alignment regularly and adjust as necessary, ensuring that all components are properly seated and tensioned.
Maintenance Tips for Optimal Performance
Regular upkeep is essential to ensure that your tool operates efficiently and reliably. Proper care not only extends the lifespan of the equipment but also enhances its effectiveness in various tasks. Following a few straightforward guidelines can significantly improve performance and prevent potential issues.
First, always keep the cutting mechanism clean and free of debris. After each use, wipe down the surfaces and remove any residue that may hinder operation. Additionally, regularly inspect the mechanism for signs of wear or damage, replacing components as needed to maintain optimal functionality.
Lubrication is another critical aspect of maintenance. Ensure that moving parts are adequately lubricated to reduce friction and wear. This practice not only enhances performance but also minimizes the risk of overheating during extended use.
Furthermore, pay attention to the power source. Regularly check connections and ensure they are secure. If you notice any fluctuations in power delivery, address them promptly to avoid interruptions during operation. Keeping the equipment charged and ready for use is also essential for seamless performance.
Lastly, store the equipment in a dry, cool place away from direct sunlight. Proper storage prevents rust and other forms of corrosion, ensuring that the tool remains in peak condition for your next project.