Main Drive Elements of the Baler
The drive system plays a crucial role in ensuring the proper functionality of the machine. It transfers power from the engine to key components, facilitating the efficient operation of the equipment. Understanding how these elements work together is essential for maintaining smooth performance and reducing downtime.
Transmission Gears
The transmission gears are responsible for converting rotational energy into usable power for the equipment’s mechanical functions. By adjusting speed and torque, these gears ensure the seamless operation of the various mechanisms, allowing the system to perform at optimal levels.
Power Shaft and Chains
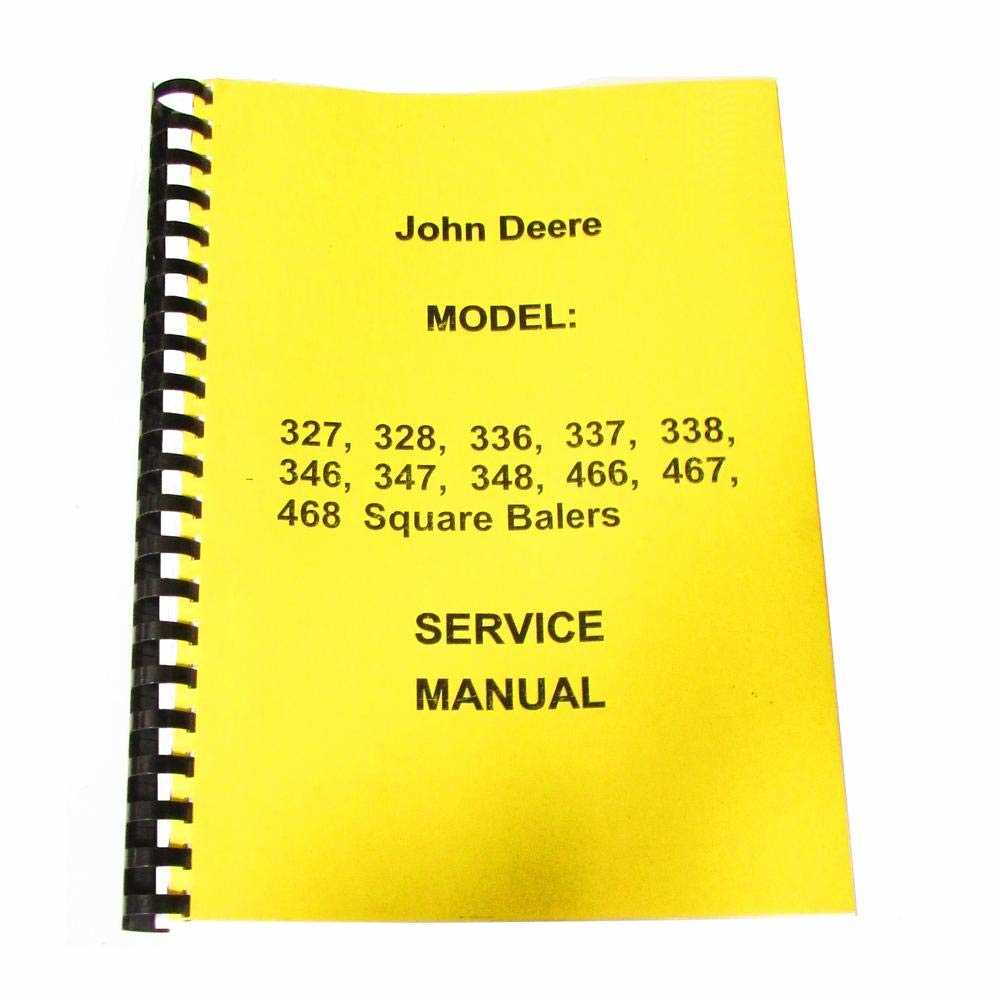
The power shaft acts as the central conduit for distributing energy throughout the machine. It connects with heavy-duty chains that transfer motion to the critical working parts. Proper maintenance of these chains is essential for avoiding mechanical failures and ensuring long-term durability.
Hydraulic System Parts Breakdown
The hydraulic mechanism is an essential component that powers the machine’s lifting and compression functions. It operates through a series of interconnected elements designed to regulate fluid pressure, enabling smooth and consistent movement of various mechanical parts. Understanding how these elements work together ensures optimal system performance and longevity.
Main Components of the Hydraulic Mechanism
The key elements include the pump, which generates fluid pressure, and the valve assembly, responsible for directing the flow of hydraulic fluid. Additionally, hoses and cylinders are crucial in transferring force and enabling the system to perform its tasks. These components work in harmony to maintain fluid dynamics and efficient operation.
Maintenance and Troubleshooting
Regular inspections of the hydraulic system are vital to avoid leaks or pressure loss. Checking seals, hoses, and
Function of Hydraulic Cylinders in Baling
Hydraulic cylinders play a crucial role in the operation of machinery designed for compressing and binding materials. These components are responsible for transforming hydraulic pressure into mechanical force, allowing the system to perform key tasks with precision. In the context of agricultural machinery, they enable the pressing and securing of crop materials, ensuring a consistent and efficient workflow during the collection process.
How Hydraulic Cylinders Operate
At the heart of the hydraulic system, these cylinders control the movement of critical elements within the machine. The pressurized fluid within the system pushes the piston, which is connected to various moving parts, allowing for the compression of hay, straw, or other similar materials. The force generated by this movement is essential for creating uniform bales, which are then securely tied for transport or storage.
Benefits of Efficient Hydraulic Systems
When hydraulic cylinders are well-maintained, they contribute to smoother, faster, and more reliable operations. The power they deliver ensures that the compression process occurs evenly and rapidly, reducing downtime and improving overall efficiency. This is particularly important in large-scale farming operations where productivity and speed are vital for success. Proper functioning of these systems leads to higher-quality output and a smoother workflow in the field.
Pickup Assembly Parts and Maintenance
The pickup assembly is a crucial component for efficient collection and transportation of materials. Regular attention to its components ensures smooth operation and extends the lifespan of the equipment. This section covers the essential elements involved in maintaining the pickup system and their role in the overall functionality of the machine.
Maintenance of the pickup assembly requires periodic checks on various individual components that work in harmony to achieve optimal performance. Ensuring that each element is well-maintained minimizes downtime and helps avoid costly repairs in the future.
Component |
Description |
Maintenance Tips |
Pickup Reel |
The rotating mechanism that gathers material and moves it toward the intake. |
Regularly inspect for wear and tear. Lubricate moving parts to prevent rust and ensure smooth operation. |
Feed Rake |
Helps in directing collected material towards the gathering mechanism. |
Check for bent tines and replace if necessary. Ensure proper alignment to avoid uneven feeding. |
Gears and Drive System |
The system that powers the pickup reel and other moving parts. |
Ensure gears are properly lubricated and inspect for any signs of damage or misalignment. |
Bearings |
Support rotating components, reducing friction and wear. |
Check for play or noise during operation. Replace bearings that show signs of wear. |
Belts |
Transmit power from the engine to various moving parts. |
Inspect for cracks or fraying. Adjust tension regularly and replace if signs of wear are visible. |
By staying proactive with the upkeep of these key components, the efficiency and longevity of the pickup system are significantly enhanced. Regular maintenance routines will help keep the equipment running smoothly and prevent costly interruptions in operations.
Detailed Look at the Tine Bars
The tine bars play a crucial role in the efficient operation of agricultural machinery, especially in systems designed to handle hay or straw. These components are responsible for gathering and moving material through the system, ensuring that everything is properly processed. Understanding the design and functionality of these parts is essential for maintaining optimal performance and extending the lifespan of the equipment.
Constructed from durable materials, the tine bars are engineered to withstand the wear and tear that comes with daily use. The unique shape and alignment of each tine are crucial for creating the right flow of material. They are positioned in such a way that they can handle large volumes of organic matter while minimizing clogging or jamming, ensuring smooth operation even in challenging conditions.
Regular inspection of the tine bars is necessary to ensure that they remain in good working condition. Over time, they can become worn or bent, which affects their ability to perform optimally. Proper maintenance, including lubrication and alignment, will help in avoiding premature damage and will ensure the system runs efficiently during the harvesting season.
Twine and Net Wrap System Overview
The twine and net wrap system plays a crucial role in the baling process, ensuring that harvested material is securely bound for storage or transportation. This system consists of various components that work together to wrap the material tightly, preventing spillage and preserving the quality of the crop. The primary purpose is to keep the material compact and protected during handling and storage.
Twine System
The twine system utilizes strings to wrap the compacted material, ensuring that the bale holds its shape. The twine is automatically fed into the machine during the process, wrapping it around the bale several times before it is secured with a knot. Key features of this system include:
- Automatic twine feeding mechanism
- Twine storage compartments for easy access
- Efficient knotting system to secure the bale
Net Wrap System
Alternatively, the net wrap system uses large sheets of netting material to wrap the bale. This system offers the advantage of faster wrapping and provides additional protection from weather elements. The net wrap is applied evenly around the bale to provide a strong, secure outer layer. Features include:
- High-strength netting material for enhanced durability
- Quick and uniform coverage of the bale
- Automatic net tension adjustment for optimal wrapping pressure
Components Ensuring Proper Bale Wrapping
Efficient wrapping of hay or straw bales is essential for maintaining quality and preventing spoilage. Proper wrapping ensures the integrity of the bale during storage and transport, reducing waste and preserving nutrients. Several key elements work together to guarantee that the wrapping process is smooth and effective. These components contribute to the consistent application of material, secure tension, and uniform coverage.
Key Elements for Proper Bale Coverage
- Roller Mechanisms: These components help maintain constant pressure as the bale rotates, ensuring even application of the wrapping material.
- Film Dispensing System: This system is responsible for evenly dispensing the wrapping material around the bale, creating a consistent layer.
- Tension Control: Proper tension prevents loose wrapping, which can lead to damaged bales. A tension control system ensures that the wrapping material is securely held in place.
- Feed Mechanism: The feed mechanism ensures that the bale is positioned correctly as it moves through the wrapping process, preventing misalignment and uneven wrapping.
Additional Factors to Consider
- Adjustable Settings: Being able to adjust the wrapping settings according to the size and type of the bale helps achieve optimal results.
- Sensor Technology: Some systems utilize sensors to monitor the bale’s size and position, automatically adjusting the wrapping process to maintain uniformity.
- Maintenance and Lubrication: Regular maintenance of all components, including lubrication of moving parts, ensures the wrapping system remains functional and efficient over time.
Examining the Bale Chamber and Gates
The bale chamber is an essential component in the process of forming and compacting the hay or straw into a tightly bound roll. The structure of this chamber, along with the gates that control its size and function, plays a pivotal role in the overall efficiency and output of the machinery. In this section, we will explore the key elements of this part of the system, focusing on its design and the mechanism behind the gates.
Functionality of the Bale Chamber
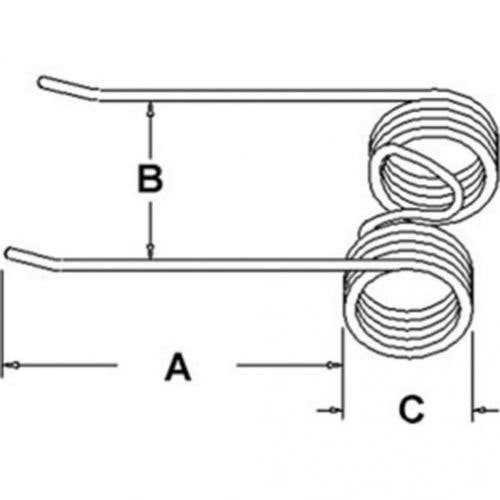
The primary function of the bale chamber is to apply pressure to the material, transforming it into a dense, uniform cylinder. This chamber is carefully engineered to provide consistent compression, ensuring that the bale is tightly packed and easy to handle. The shape and size of the chamber directly affect the quality of the final product, influencing factors such as density, size, and shape.
- Compression mechanisms in the chamber
- Influence of chamber dimensions on bale quality
- Material flow and the role of chamber pressure
Role of the Gates
The gates surrounding the chamber are integral to its function. These gates regulate the size of the bale being formed, ensuring that the chamber remains compacted to the appropriate level. Gates may be adjustable, offering flexibility in the size of the bale, or fixed for standard operations. The precision of the gate mechanisms impacts both the efficiency of the machine and the quality of the end product.
- Types of gate mechanisms
- Adjustable vs. fixed gate systems
- Maintenance considerations for gate operation
Parts Responsible for Bale Formation
The process of creating compact bundles of material requires a variety of components that work together seamlessly to ensure efficiency and consistency. Each element plays a crucial role in compressing, shaping, and tying the materials into a cohesive form. Understanding the specific responsibilities of these components is essential for the optimal operation of the equipment.
Compression and Shaping Mechanisms
- The core mechanism for compressing the material into the desired shape is the chamber, where the materials are gathered and compacted.
- Stiff, rotating cylinders or rollers ensure that the gathered material is tightly compressed into the proper shape.
- A series of belts or chains continuously move the material through the system, ensuring uniform density and placement.
Binding and Tying Components
- Twine or wire feeding systems deliver the necessary binding material that wraps around the compacted bundle.
- A tying device automatically wraps and secures the binding material, completing the bale formation.
- The tension control system adjusts the tightness of the binding to ensure the bale remains intact and secure during handling.
Clutch and Driveline Components Explained
The clutch and driveline system in agricultural machinery plays a crucial role in ensuring the proper transfer of power between various mechanical parts. This system enables the machine to operate smoothly by regulating the connection and disconnection of the power source to different functional components. Each part of the system works in harmony to ensure efficient and consistent operation under varying conditions.
At the heart of this system is the clutch, which controls the engagement and disengagement of the drive mechanism. The driveline, on the other hand, includes several interconnected parts that transmit mechanical power from the engine to various components, such as the rotating drum or other accessories. These parts must be durable, as they undergo significant stress during heavy-duty operation.
Component |
Description |
Clutch |
A device that controls the connection between the engine and the driveline, allowing the machine to start or stop smoothly. |
Driveline Shaft |
The central shaft that transmits power from the engine to the various components of the machine. |
U-Joints |
Universal joints that allow the transmission shaft to flex, enabling the driveline to handle various angles and maintain smooth power transfer. |
Bearings |
Support structures that reduce friction and facilitate smooth rotation of the driveline components. |
Pulleys and Belts |
Systems that adjust the speed and torque transmitted through the driveline, crucial for maintaining the machine’s operational efficiency. |
Regular maintenance and understanding of these key elements are essential for keeping the machinery running at peak performance. Over time, wear and tear can affect the efficiency of these components, and timely replacement or repair is necessary to avoid costly breakdowns.