The mechanism designed for stretch film applications plays a crucial role in enhancing packaging efficiency and product protection. By utilizing advanced engineering techniques, this system allows for the seamless application of film around various loads, ensuring stability during storage and transport. Understanding the intricacies of this mechanism can greatly benefit those involved in the packaging industry.
This mechanism comprises several essential elements that work together harmoniously. The primary components include a film dispenser, tension control system, and an adjustable film roll holder. Each part contributes to the overall effectiveness of the packaging process, allowing for consistent film application tailored to specific load requirements. The tension control system, in particular, ensures optimal stretch levels, preventing film breakage and enhancing load security.
Regular maintenance of this system is vital to ensure its longevity and performance. Key practices include inspecting the film rolls, checking tension settings, and cleaning the dispensing unit to prevent material build-up. By implementing these maintenance strategies, operators can maximize efficiency and reduce downtime, ultimately leading to a more streamlined packaging process.
The rotating platform serves as a crucial component in various industrial applications, enhancing efficiency and precision in the handling of materials. This system is designed to facilitate the smooth movement of goods, ensuring optimal performance during operations. Understanding its primary elements is essential for anyone looking to maximize the benefits of this equipment.
The assembly consists of several vital elements that work in harmony. The base provides stability and support, while the rotating surface allows for seamless access from multiple angles. Integrated controls enable operators to adjust speed and direction, promoting versatility in different operational contexts.
This platform’s design emphasizes user-friendliness and reliability. By reducing the need for manual handling, it minimizes labor costs and enhances safety in the workplace. Its ability to accommodate various load types makes it an invaluable asset in warehouses and production lines, streamlining processes and improving overall productivity.
Understanding the Role of Sensors in Q300
Sensors are critical components that significantly enhance the functionality and efficiency of automated systems. These devices gather data from the surrounding environment, enabling equipment to make informed decisions and adjustments in real-time. By accurately detecting various parameters, sensors contribute to seamless operation and improved performance.
Types of Sensors and Their Functions
In sophisticated machinery, different types of sensors are employed, each serving a unique purpose. For example, proximity sensors detect the presence of objects without direct contact, ensuring safe operation and preventing collisions. Temperature sensors monitor thermal conditions, allowing the system to adjust operations to prevent overheating or damage. By integrating these devices, the overall reliability and efficiency of the equipment are greatly enhanced.
Impact on System Performance
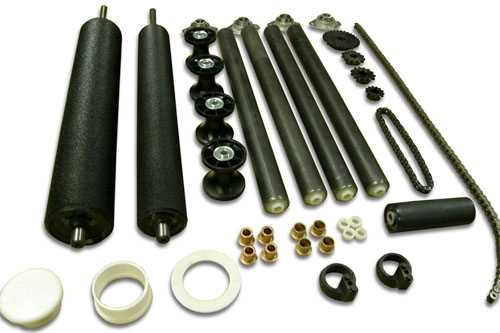
The integration of sensors into automated systems leads to significant improvements in operational performance. With real-time monitoring capabilities, these devices facilitate quick responses to changing conditions, ensuring optimal functionality. Additionally, they contribute to predictive maintenance by providing valuable insights into wear and tear, thus reducing downtime and extending the lifespan of the machinery. Embracing the use of advanced sensing technology ultimately fosters a more efficient and reliable operational environment.
Detailed View of the Q300 Hydraulic System
The hydraulic system plays a crucial role in the operation of advanced machinery, ensuring efficient movement and control of various components. This intricate network utilizes fluid mechanics to transmit power, enabling precise handling of heavy loads and facilitating smooth functionality throughout the system. Understanding the various elements and their interactions is essential for optimizing performance and maintaining reliability.
At the heart of this hydraulic mechanism lies a sophisticated pump that generates the necessary pressure for fluid circulation. This pressure drives the system’s actuators, which convert hydraulic energy into mechanical movement. Hydraulic cylinders are a key component, responsible for creating linear motion, while valves control the flow and direction of the fluid, allowing for versatile operations.
Another integral aspect includes the reservoir, which stores hydraulic fluid and ensures a steady supply to the pump. Additionally, filters within the system help maintain fluid cleanliness, preventing contaminants from causing wear or damage. Regular maintenance and monitoring of these components are vital for ensuring the hydraulic system operates at peak efficiency, thus enhancing overall equipment performance.
Identifying Commonly Replaced Q300 Parts
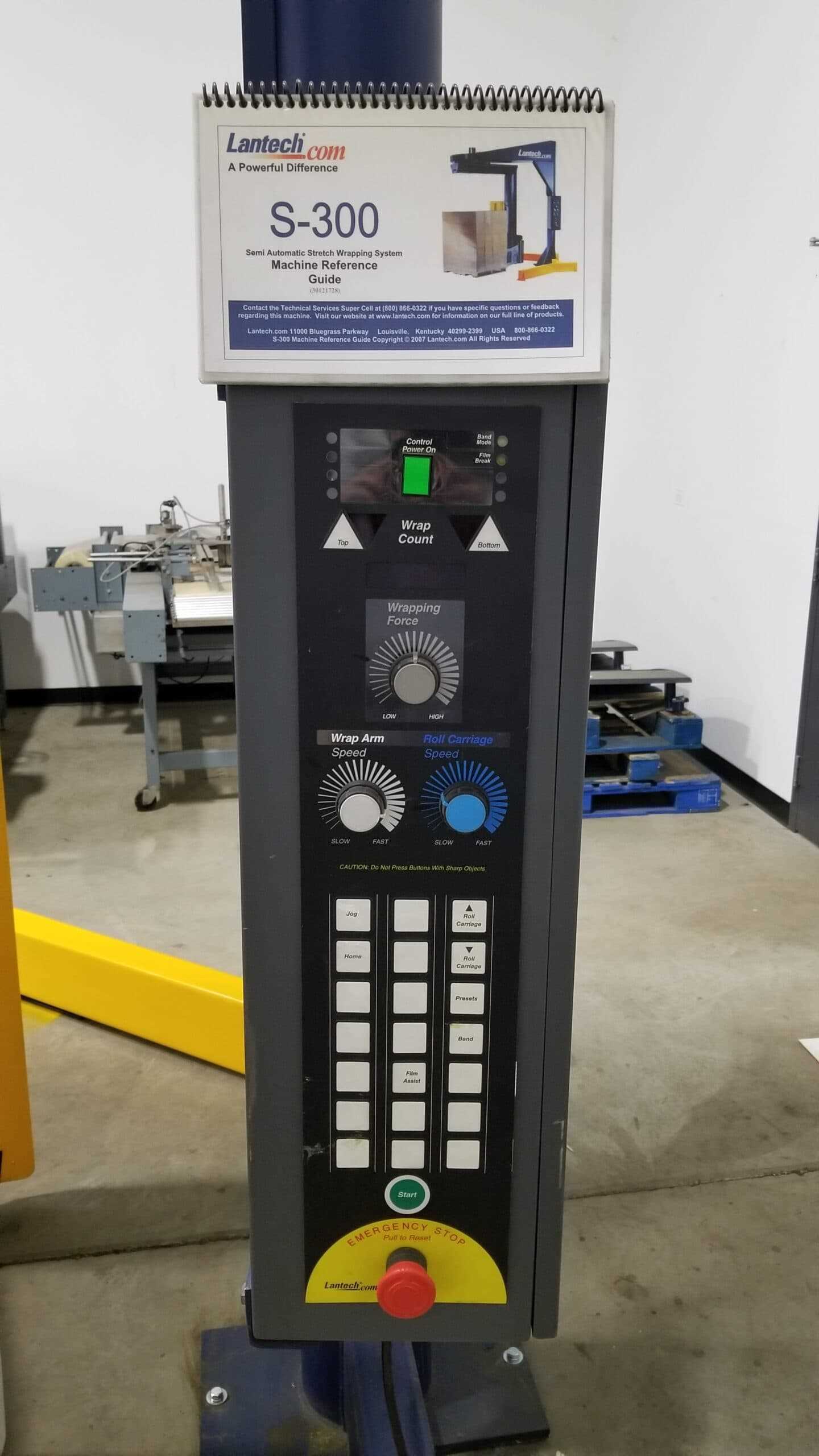
Understanding the components that require frequent replacement is crucial for maintaining optimal performance and prolonging the lifespan of machinery. Various elements of the system may experience wear and tear over time, necessitating timely intervention to ensure uninterrupted operation. This section focuses on the commonly swapped components that users may encounter.
Component |
Symptoms of Failure |
Recommended Action |
Drive Belt |
Slipping, unusual noises |
Replace immediately to avoid further damage |
Motor |
Overheating, reduced performance |
Inspect and replace if necessary |
Controller Board |
Erratic behavior, failure to start |
Test functionality and consider replacement |
Rollers |
Decreased efficiency, jams |
Replace worn or damaged rollers |
Power Supply |
No power, flickering lights |
Check connections and replace if faulty |
How to Source Original Lantech Q300 Parts
Finding authentic components for your machinery can significantly enhance its performance and longevity. Ensuring that you obtain high-quality replacements is crucial for maintaining optimal operation and preventing future issues. This section outlines effective strategies for acquiring genuine elements essential for your equipment.
Start by reaching out to authorized distributors or manufacturers. These sources typically offer original items, ensuring compatibility and reliability. It’s advisable to verify the credentials of any supplier to confirm their legitimacy. Consider checking their website for customer reviews and certifications, as this can provide insight into their reputation in the industry.
Another viable option is to consult with industry professionals or forums dedicated to machinery. Engaging with knowledgeable individuals can lead you to reputable sources that others have successfully used. Additionally, online marketplaces may have listings for genuine components, but exercise caution and ensure that the seller has a proven track record.
Finally, keeping track of your equipment’s model and specifications is essential when searching for replacements. Having detailed information readily available can streamline the process and ensure that you procure the correct items. By following these steps, you can secure the necessary elements to keep your machinery functioning at its best.
Maintenance Tips for Lantech Q300 Components
Regular upkeep of machinery components is crucial for ensuring optimal performance and longevity. By adhering to specific maintenance practices, operators can significantly reduce downtime and enhance the efficiency of their equipment. This section provides essential guidelines for maintaining the various elements of your machinery, promoting seamless operation and minimizing wear and tear.
Routine Inspections
Conducting regular inspections helps identify potential issues before they escalate. It is advisable to check critical components such as belts, rollers, and electrical connections. Implement a schedule for these inspections to ensure all parts are functioning correctly and address any signs of wear promptly.
Lubrication Practices
Proper lubrication is essential for reducing friction and preventing damage to moving parts. Utilize the recommended lubricants and follow the guidelines for application. Ensure that bearings, gears, and other mechanical parts receive adequate lubrication to maintain optimal performance.
Component |
Recommended Maintenance |
Belts |
Inspect for wear; replace if frayed or cracked. |
Rollers |
Check alignment; lubricate bearings regularly. |
Electrical Connections |
Inspect for corrosion; ensure tight connections. |
Gears |
Clean and lubricate to avoid excessive wear. |
Filters |
Replace regularly to ensure optimal performance. |