Tie Rods:
Electrical System Layout and Parts
The arrangement of the electrical components is crucial for the efficient operation of any machinery. A well-organized system enhances functionality, simplifies troubleshooting, and improves overall performance. Understanding the various elements and their configurations can lead to better maintenance and optimal use.
Key Components of the Electrical Setup
At the heart of the electrical configuration are several vital elements. These include the battery, which serves as the primary power source, and the alternator, responsible for recharging the battery and supplying power to the electrical systems. Additionally, wiring harnesses connect these components, ensuring seamless communication and energy transfer throughout the machine.
Understanding the Wiring and Connections
Proper wiring is essential for a reliable electrical setup. Each wire must be correctly routed and secured to prevent damage and interference. Connectors play a significant role, as they facilitate easy disconnection and reconnection during maintenance. Regular inspections of these connections help to identify potential issues before they escalate into more significant problems.
Mowing Deck Assembly Explained
The assembly of a mowing deck is a crucial component in the overall functionality of lawn maintenance equipment. Understanding how these components fit together enhances the performance and efficiency of the machine. A well-assembled mowing deck ensures even cutting and longevity of the equipment.
Key Components of the Mowing Deck
The mowing deck typically consists of several essential elements, including the blade assembly, housing, and spindle. Each part plays a vital role in the cutting process. The blade assembly is responsible for the actual cutting action, while the housing encases the blades, providing protection and support. The spindle connects the blades to the power source, allowing them to rotate effectively.
Assembly Process Overview
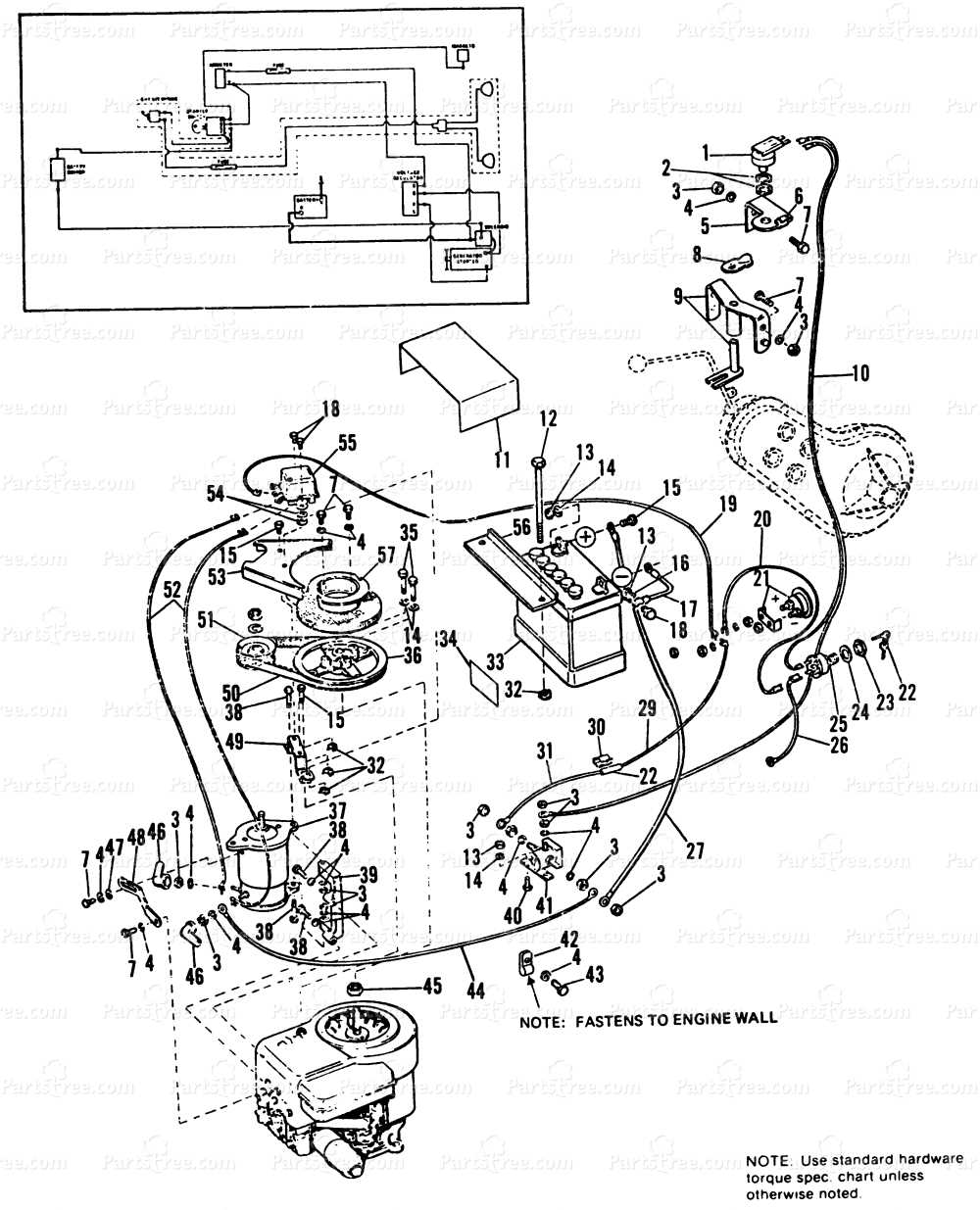
When assembling the mowing deck, it’s important to start with a clean workspace and gather all necessary tools. Begin by securing the housing to the frame of the equipment. Next, attach the blade assembly to the spindle, ensuring proper alignment for optimal performance. Finally, check all connections for stability and adjust the height settings as needed to achieve the desired cutting height.
Drive Belt and Pulley Systems
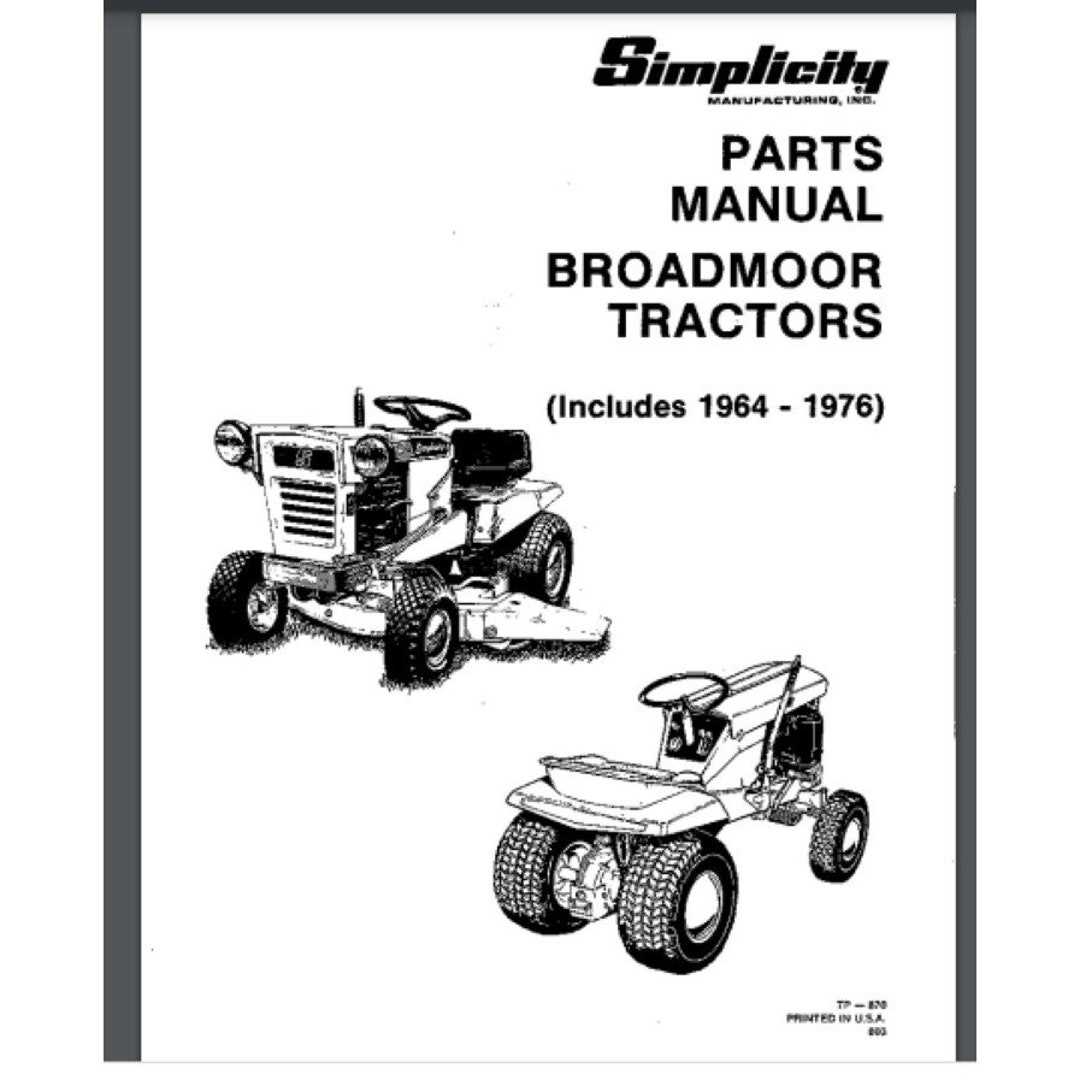
Drive belts and pulleys play a crucial role in the transfer of motion and power within various machinery. These components work together to efficiently transmit energy from one part of a machine to another, allowing for seamless operation. Understanding the mechanics behind these systems is essential for maintenance and performance optimization.
Components of Drive Belt and Pulley Systems
The primary elements of these systems include:
- Belt: A flexible loop made from durable materials that connects the pulleys.
- Pulleys: Wheels that guide the belt and transfer motion, often varying in size.
- Tensioner: A device that maintains the correct tension on the belt to prevent slippage.
- Idler Pulley: A pulley that helps redirect the belt and maintain proper alignment.
Benefits of Efficient Belt and Pulley Design
Well-designed drive belt and pulley systems offer several advantages:
- Energy Efficiency: Reduces power loss during transmission, enhancing overall performance.
- Noise Reduction: Provides quieter operation compared to direct drive systems.
- Flexibility: Allows for easy adjustments and replacements, simplifying maintenance tasks.
- Durability: High-quality materials ensure longevity and reliable operation under various conditions.
Blade Mounting and Replacement Tips
Proper attachment and replacement of cutting components are crucial for maintaining the efficiency and effectiveness of your equipment. Ensuring that these elements are securely fitted not only enhances performance but also promotes safety during operation. This section provides valuable insights into the best practices for mounting and replacing blades.
1. Inspect Before You Start: Always conduct a thorough examination of the cutting edge and its mounting area before initiating any changes. Look for signs of wear, damage, or corrosion that may affect performance. Addressing these issues beforehand can prevent further complications.
2. Use the Correct Tools: Having the right tools at your disposal is essential for effective blade installation. Utilize appropriate wrenches or sockets to ensure that fasteners are tightened to the manufacturer’s specifications. This helps avoid loosening during operation.
3. Follow a Step-by-Step Process: When mounting a new blade, adhere to a systematic approach. Start by aligning the blade with the mounting bracket accurately. Securely fasten all bolts or screws while ensuring even pressure distribution to prevent vibration during use.
4. Regular Maintenance: Implement a routine check-up schedule to assess the condition of the blades. Regular cleaning and maintenance can extend the lifespan of the components and improve cutting performance. Replace any blade that shows signs of significant wear or damage immediately.
5. Safety First: Always prioritize safety when handling sharp blades. Wear protective gloves and goggles to shield yourself from potential injuries. Ensure the equipment is powered off and disconnected from any power source during maintenance.
Maintenance of the Fuel System
Ensuring the proper functioning of the fuel delivery system is essential for optimal performance and longevity of your equipment. Regular upkeep can prevent issues such as clogging, leaks, and inefficiencies that can lead to costly repairs and downtime. This section outlines important practices to maintain this vital system.
Start by inspecting the fuel lines for any signs of wear or damage. Look for cracks, leaks, or kinks that may obstruct the flow of fuel. Replace any compromised sections promptly to maintain the integrity of the system.
Next, clean or replace the fuel filter according to the manufacturer’s recommendations. A clogged filter can restrict fuel flow and impact performance. Regular maintenance of this component is crucial for ensuring clean fuel reaches the engine.
Additionally, keep the fuel tank clean and free from contaminants. Periodically check for any debris or water accumulation, as these can lead to engine issues. If necessary, drain and clean the tank to ensure only quality fuel is being used.
Lastly, monitor the fuel quality and ensure you are using the appropriate type for your equipment. Stale or contaminated fuel can cause significant problems and reduce efficiency. Regularly refilling with fresh fuel will help maintain the performance of your equipment.
Troubleshooting Common Mechanical Issues
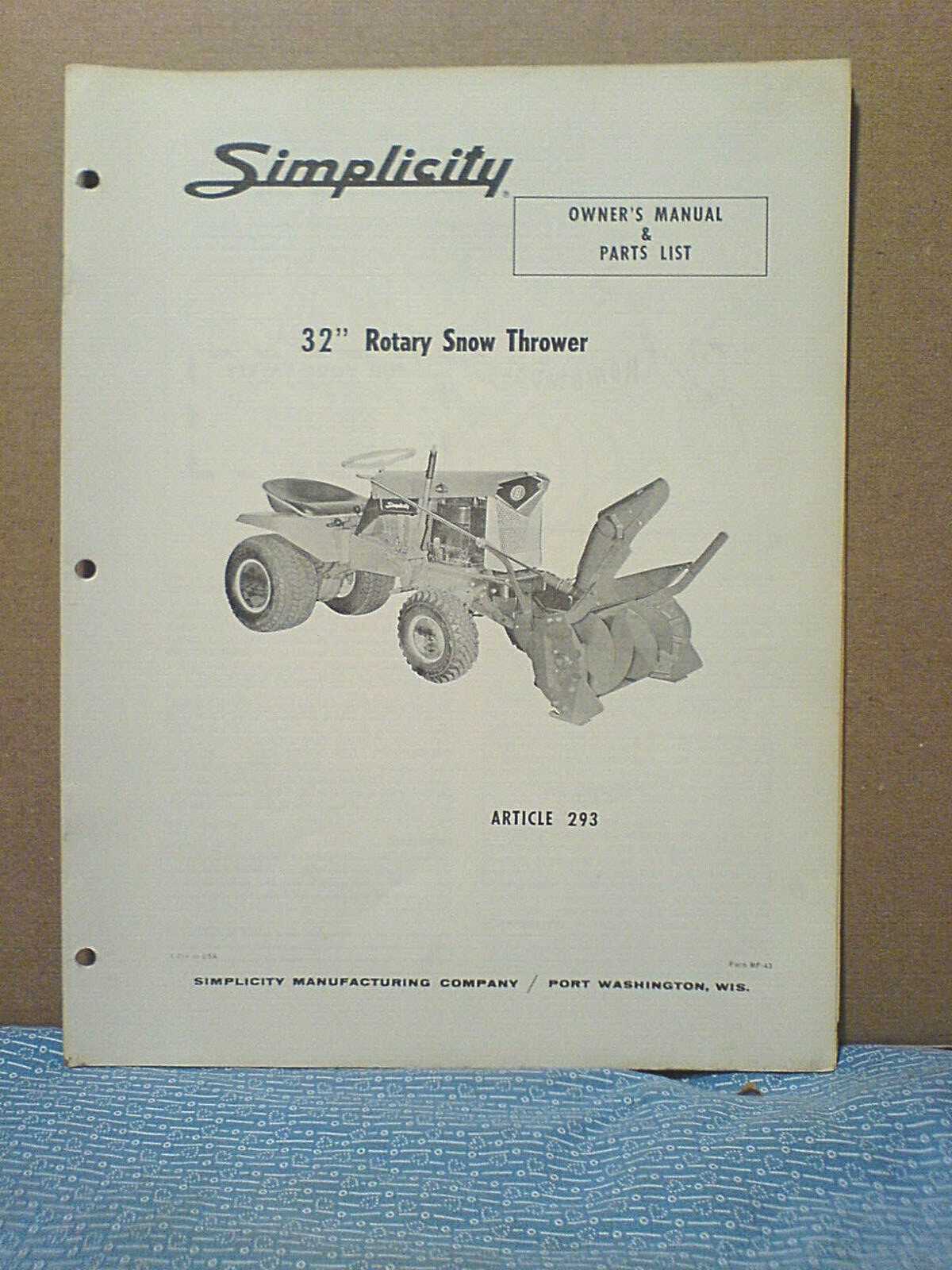
Mechanical systems can occasionally experience various complications that hinder their performance. Understanding these issues is crucial for efficient operation and maintenance. This section will guide you through identifying and addressing frequent mechanical problems, helping to ensure the reliability and longevity of your equipment.
Identifying Common Problems
Recognizing the symptoms of mechanical difficulties is the first step toward resolving them. Here are some typical indicators:
- Unusual noises during operation
- Inconsistent performance or power loss
- Visible wear or damage to components
- Vibrations or instability while in use
Steps for Resolution
Once you have identified potential issues, follow these steps to troubleshoot:
- Inspect Components: Check for any visible signs of wear or damage. Ensure all parts are securely fastened.
- Lubrication: Apply appropriate lubricants to moving parts to reduce friction and prevent wear.
- Adjust Settings: Review and adjust any settings to ensure they are within recommended ranges.
- Consult Manuals: Refer to technical documentation for specific guidance on your equipment.
- Seek Professional Help: If issues persist, consider consulting a qualified technician for in-depth analysis and repair.
Ordering and Replacing Essential Parts
Ensuring the functionality of your equipment requires timely acquisition and installation of key components. Understanding the process of sourcing and substituting these elements can significantly enhance performance and longevity. This guide outlines the necessary steps to efficiently obtain and replace vital components, ensuring your machinery operates smoothly.
Finding the Right Components
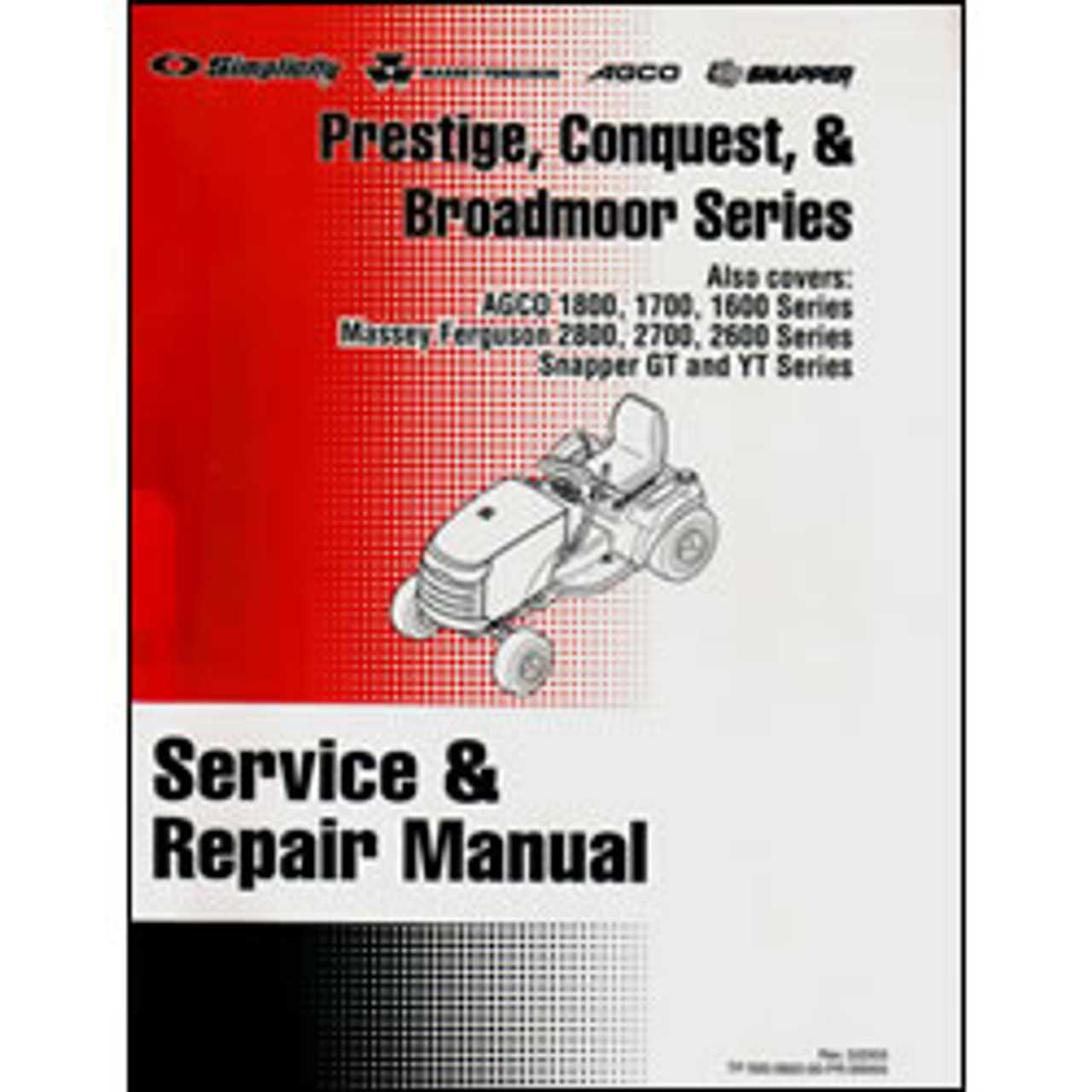
Start by identifying the specific components you need for replacement. Consult your user manual or product specifications to determine the exact model and compatibility. Utilizing online resources or contacting authorized dealers can help locate the appropriate items. Always ensure that you are choosing high-quality alternatives to maintain optimal performance.
Replacement Process
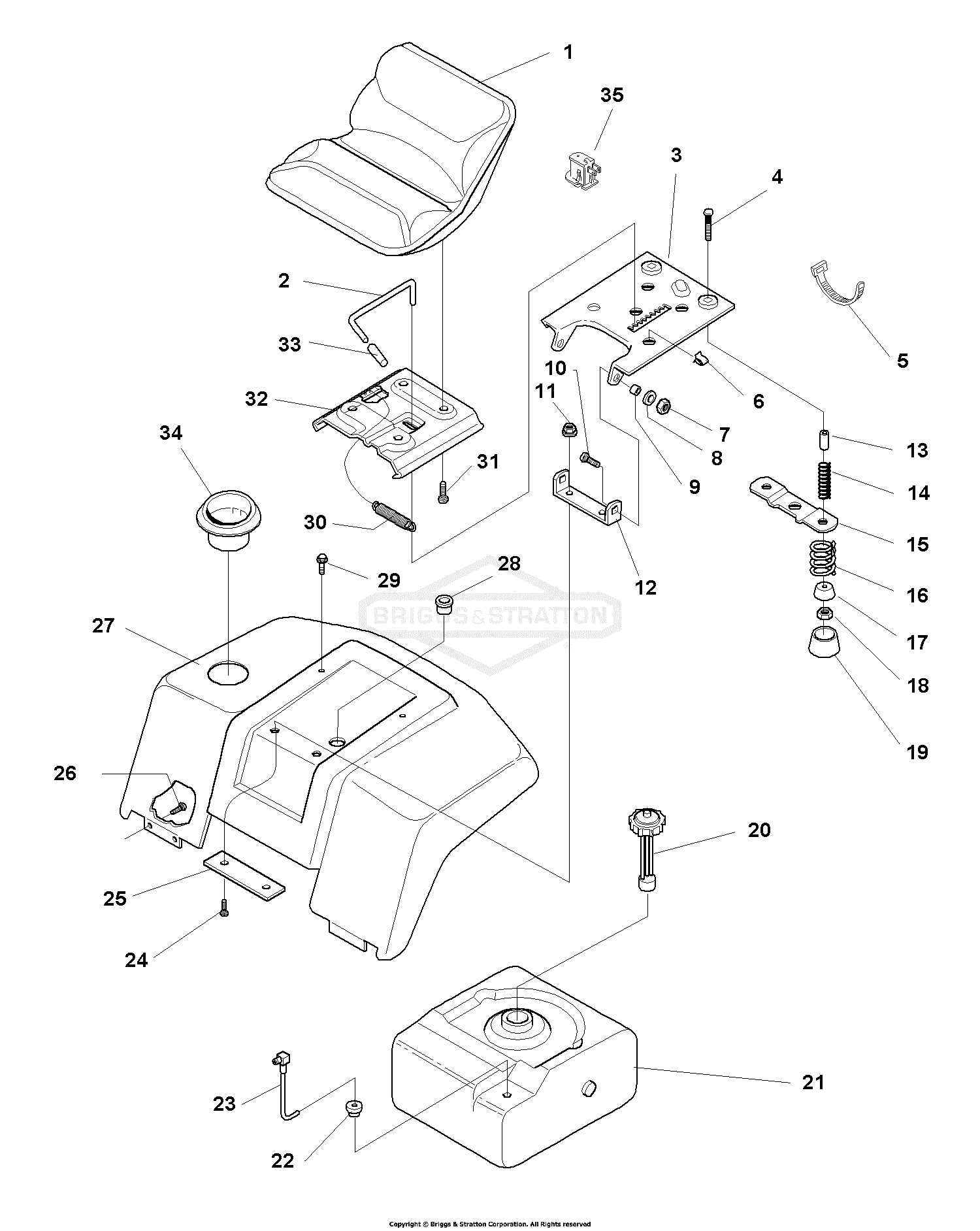
Once you have acquired the necessary components, follow the manufacturer’s guidelines for installation. It is advisable to gather the required tools before commencing. Carefully disconnect any power sources to ensure safety during the replacement process. Take your time to fit the new components precisely, as improper installation can lead to further complications. After replacing the items, conduct a thorough check to confirm that everything is functioning correctly.