Cra
Breaking Down the Engine Mechanism
The inner workings of this model’s motor assembly are crucial to its overall performance. Understanding how the components collaborate helps in maintaining and repairing the system efficiently. By examining the key functional elements, you gain insights into the flow of power and the mechanical operations that drive the machine.
Main Moving Components
The core of the motor’s operation involves several critical moving parts, all designed to work in unison. Each element plays a specific role in converting energy into motion, whether it’s through combustion or mechanical force. Identifying and understanding these elements can prevent common issues and improve long-term functionality.
Operational Flow
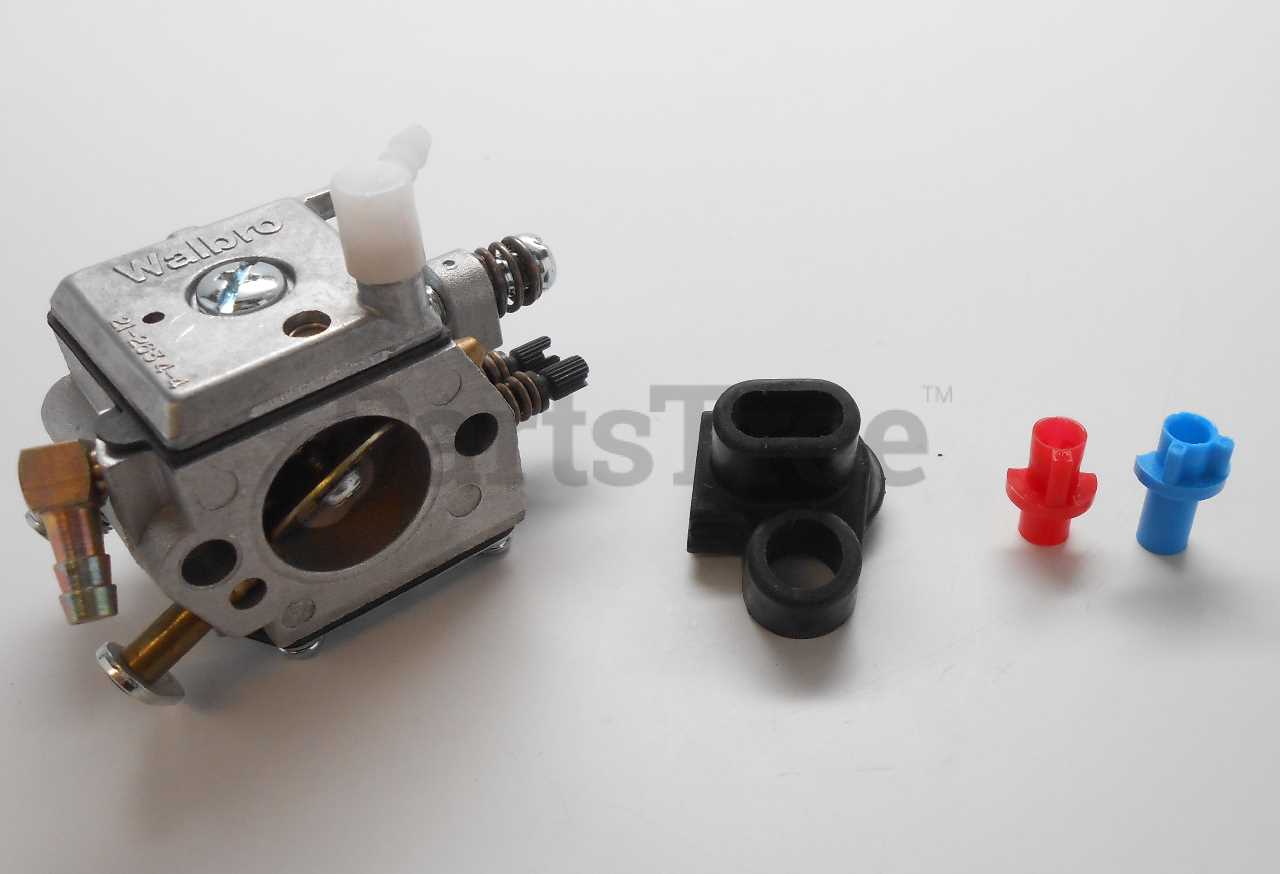
The process begins with ignition, setting off a sequence of actions that produce the energy required for movement. From air intake to the release of exhaust, each step is synchronized to ensure smooth and efficient operation. The more familiar you become with this flow, the easier it is to diagnose performance problems.
Guide to Fuel System Parts
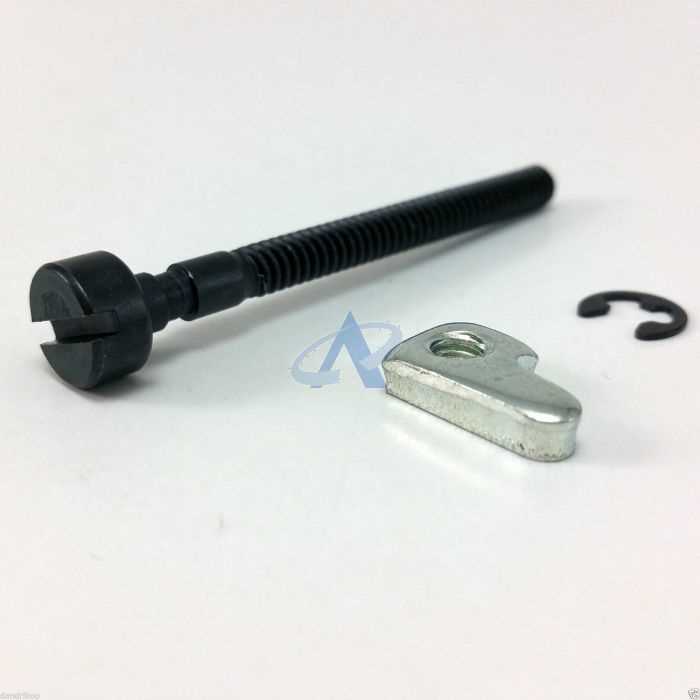
The fuel system is an essential component that ensures the smooth operation of any engine. Understanding the various elements that make up this system can help maintain efficient performance and prolong the lifespan of your equipment. Below is a breakdown of key components and their roles in delivering power effectively.
- Fuel Tank: A reservoir designed to store the liquid necessary for operation, keeping the supply consistent.
- Fuel Filter: A critical element that removes impurities from the liquid, ensuring that only clean fuel reaches the engine.
- Fuel Line: A conduit that transports the liquid from the storage area to the motor, playing a key role in the overall efficiency of the system.
- Carburetor: This part mixes air with the liquid in the correct ratio, ensuring optimal combustion and performance.
- Primer Bulb: A small pump that helps prime the system by drawing fuel into the lines before starting the engine.
Each of these elements contributes to a well-functioning system, ensuring that the engine runs smoothly and efficiently. Regular maintenance and inspection of these parts are crucial for optimal performance.
Exploring the Ignition and Starting Assembly
The ignition and starting mechanism is crucial for the effective operation of any outdoor power equipment. This assembly is responsible for initiating the combustion process, allowing the engine to run smoothly. Understanding the components involved in this system can enhance maintenance practices and ensure optimal performance.
At the heart of this assembly lies the spark plug, which ignites the fuel-air mixture within the engine’s cylinder. A reliable ignition coil is also essential, as it generates the high voltage needed to create a spark at the plug. Additionally, the starter mechanism, often consisting of a recoil starter, plays a vital role in enabling the engine to start with minimal effort from the operator.
Proper maintenance of the ignition and starting components is vital for longevity and performance. Regular inspections can help identify wear and tear, ensuring timely replacements and reducing the risk of breakdowns. Moreover, familiarizing oneself with the layout and function of these elements can empower users to troubleshoot common issues effectively.
By delving into the intricacies of the ignition and starting assembly, operators can gain valuable insights that contribute to enhanced reliability and efficiency in their equipment’s operation.
Maintaining the Cutting System
Regular upkeep of the cutting mechanism is essential for ensuring optimal performance and longevity. By focusing on key components and implementing a consistent maintenance routine, users can enhance efficiency and achieve precise results during operation.
Inspecting and Sharpening Blades
Routine examination of the blades is crucial. Look for any signs of wear or damage, such as nicks or dullness. Regularly sharpening the edges will not only improve cutting efficiency but also reduce strain on the engine. Utilize a suitable sharpening tool, ensuring a consistent angle for a clean edge.
Cleaning the Cutting Assembly
A clean cutting assembly contributes to better performance and reduced risk of mechanical issues. After each use, remove debris, such as grass clippings and dirt, to prevent buildup. Regularly check for loose screws or components, tightening them as needed to maintain structural integrity.
Handle and Control Features Overview
This section provides insights into the various functionalities and design elements associated with the gripping and operational components of the equipment. Understanding these features is essential for users to maximize efficiency and ensure safety during operation.
Grip Design and Ergonomics
The design of the handle plays a crucial role in user comfort and control. Ergonomically shaped grips are engineered to reduce fatigue, allowing for prolonged usage without discomfort. Additionally, materials that offer enhanced traction help maintain a secure hold, even in wet or slippery conditions.
Control Mechanisms
Control mechanisms are integral to the equipment’s functionality. Features such as throttle controls and safety switches are strategically placed to provide easy access while minimizing the risk of accidental activation. These controls are designed for intuitive use, enabling users to operate the equipment efficiently while maintaining a high level of safety.
Air Filter and Exhaust Assembly Breakdown
The air filtration and exhaust components are crucial for optimal engine performance. Understanding their structure and function helps ensure the machinery operates efficiently and minimizes emissions. This section delves into the specifics of these assemblies, highlighting their roles and how they interact within the system.
Key Components of the Air Filtration System
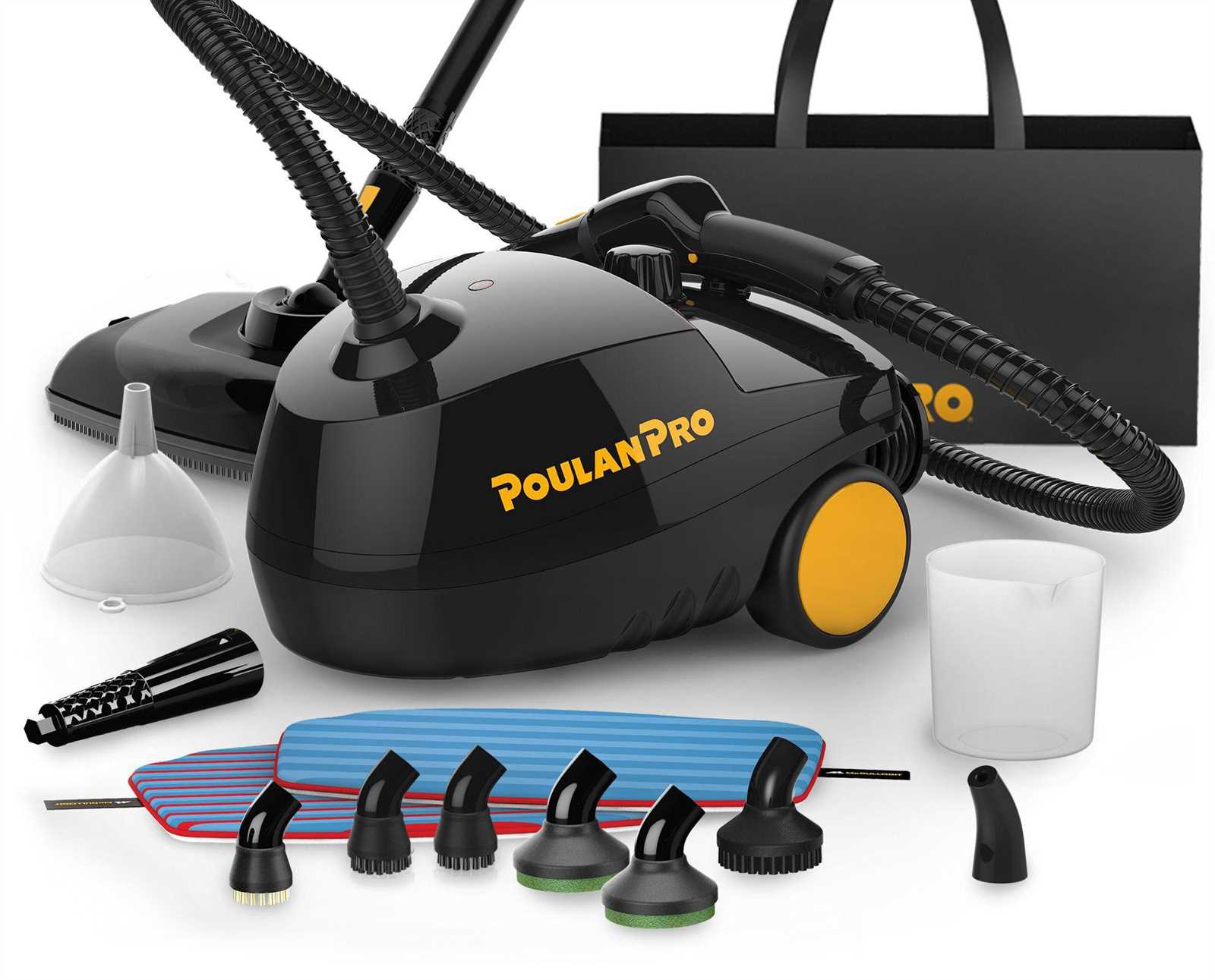
- Air Filter: Captures debris and particulates, preventing them from entering the engine.
- Pre-Filter: Provides an additional layer of protection, often designed for larger particles.
- Filter Housing: Encloses the filter, ensuring a secure fit and optimal airflow.
Understanding the Exhaust Assembly
- Exhaust Pipe: Channels exhaust gases away from the engine.
- Muffler: Reduces noise generated by the engine’s exhaust.
- Heat Shield: Protects surrounding components from excessive heat produced by exhaust gases.
By regularly inspecting and maintaining these components, users can enhance performance and extend the life of their equipment.
Replacing Essential Maintenance Parts
Regular upkeep is crucial for ensuring optimal performance and longevity of your equipment. By replacing key components periodically, you can prevent potential breakdowns and maintain efficiency. This section outlines the essential maintenance elements that should be monitored and replaced as necessary.
-
Air Filter:
This component plays a vital role in maintaining engine performance by ensuring clean airflow. Replace it regularly to enhance efficiency and prolong engine life.
-
Fuel Filter:
A clean fuel filter is essential for preventing contaminants from entering the engine. Check and replace it as part of routine maintenance to ensure smooth operation.
-
Spark Plug:
This component is critical for ignition. Replacing it at recommended intervals can significantly improve starting reliability and fuel efficiency.
-
Oil:
Regularly changing the oil is necessary to lubricate internal components and reduce wear. Follow the manufacturer’s guidelines for oil change intervals.
-
Battery:
Check the condition of the battery and replace it if it shows signs of wear or reduced performance. A reliable battery is essential for starting the engine effectively.
Implementing these replacements as part of a regular maintenance schedule will ensure your equipment operates smoothly and efficiently. Always refer to the manufacturer’s recommendations for specific maintenance guidelines and intervals.
Troubleshooting Based on Diagram Details
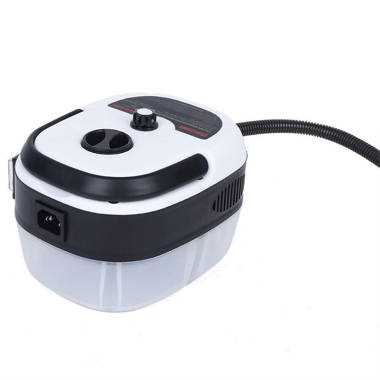
Understanding the intricacies of a schematic can significantly enhance the efficiency of maintenance and repair processes. When issues arise in equipment operation, a clear visual representation of components and their interconnections becomes invaluable. This section explores effective strategies for diagnosing problems by closely examining the schematic elements.
Identifying Common Issues
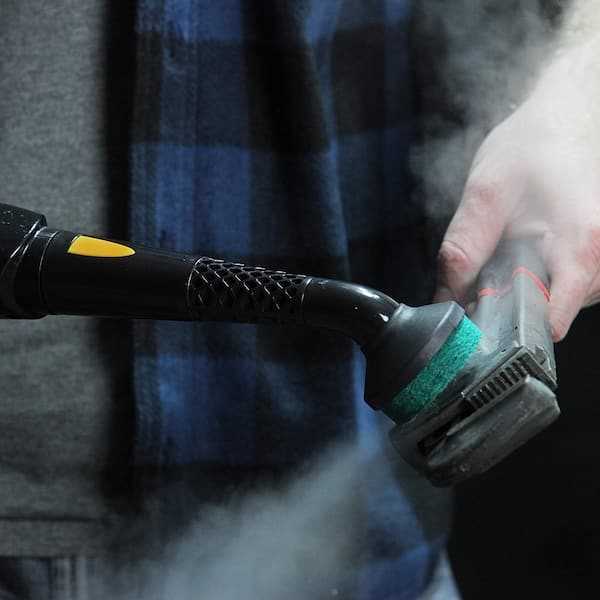
By analyzing the visual layout of components, one can pinpoint frequent malfunctions. For instance, a misplaced connection or a worn-out component can be easily detected. Regular inspections based on the schematic can help in recognizing wear and tear, allowing for timely interventions. Focus on areas where parts are frequently replaced, as these are often indicators of underlying issues.
Utilizing Visual References for Repairs
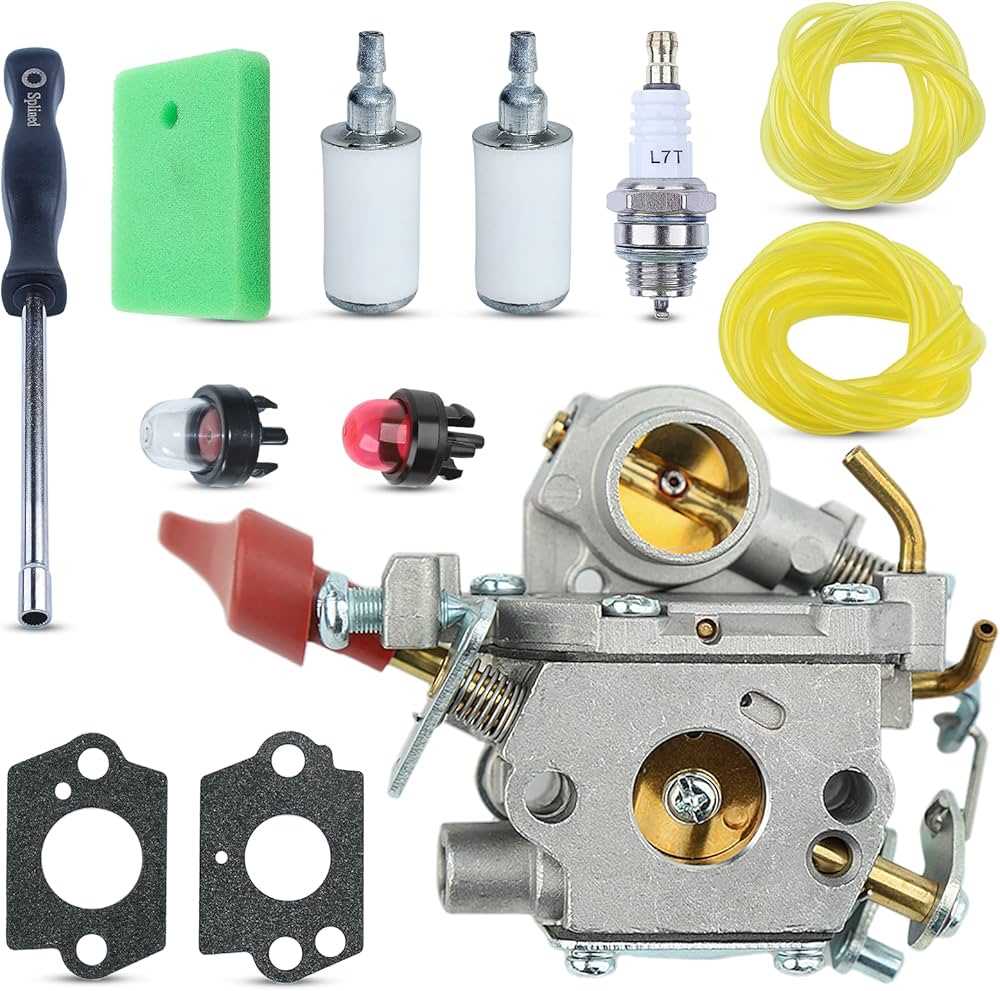
Employing visual references during repairs ensures that replacements and adjustments align with the original setup. It’s crucial to follow the arrangement depicted, as deviations might lead to further complications. Additionally, consulting the schematic allows for understanding the relationship between different elements, facilitating a more informed troubleshooting process. Always refer back to the visual guide when encountering unexpected behavior in the equipment.
|