Rotational Axis |
Base Plate and Support Foot Details
The foundation and stabilizing element play a crucial role in ensuring reliable performance. These components work together to provide a steady platform, supporting the structure during operation. Their design and functionality are essential for maintaining balance and ease of use.
- The foundation is typically designed for durability, crafted from materials that can withstand various conditions.
- The stabilizing element, often equipped with a broad surface, helps distribute weight evenly, reducing strain on the base.
- Both elements are adjustable to accommodate different surfaces and positions, enhancing overall flexibility.
- Maintenance involves regular checks for wear and proper alignment, ensuring longevity and efficiency.
Internal Gear and Screw Functionality
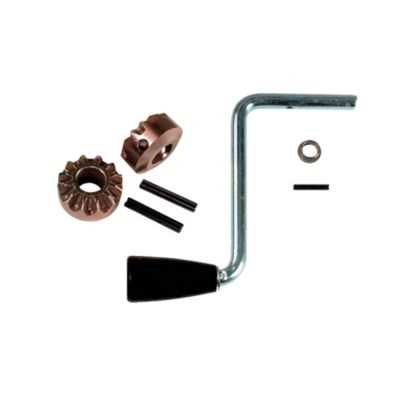
The internal mechanism consists of precisely aligned components that work together to convert rotational motion into linear movement. This transformation is essential for smooth and efficient operation, ensuring that the load can be moved with minimal effort.
Interaction Between the Gear and Screw
As the gear rotates, it engages the threaded screw, which moves up or down depending on the direction of the rotation. This interaction ensures controlled and gradual lifting or lowering, providing reliable and consistent movement.
Efficiency and Precision
The gear-to-screw system is designed for high accuracy and force distribution. Each rotation is calculated to offer maximum power with minimal friction, allowing for a balanced distribution of pressure, reducing wear on individual components and extending the overall lifespan of the system.
Wheel Attachment and Rotation System
The mechanism responsible for connecting and facilitating the rotation of the circular components plays a vital role in ensuring smooth mobility. Understanding this system is essential for optimizing performance and maintenance.
This system typically comprises several key elements that work together seamlessly:
- Mounting Bracket: This component secures the circular element, allowing for stability during operation.
- Spindle: A central axis that enables rotation, providing the necessary movement for maneuvering.
- Bearings: These reduce friction between moving parts, ensuring smooth rotation and extending the lifespan of the assembly.
- Fasteners: Essential for securing components together, preventing any accidental disconnection during use.
In addition, proper alignment of these components is crucial for efficient functioning. Misalignment can lead to increased wear and tear, impacting overall performance. Regular inspections and adjustments can help maintain optimal operation.
Bracket and Mounting Points Explanation
This section delves into the essential components responsible for securing and stabilizing equipment during operation. Understanding these elements is crucial for effective setup and maintenance, ensuring reliable performance and safety.
Functionality of Brackets
Brackets serve as critical supports that connect different components. They play a vital role in maintaining structural integrity. The following aspects highlight their significance:
- Provide stability to attached items.
- Facilitate ease of adjustment and alignment.
- Enhance overall durability of the assembly.
Mounting Points Overview
Mounting points are designated areas where components attach securely. Their design and location influence the effectiveness of the entire system. Key features include:
- Strategically placed for optimal weight distribution.
- Designed for compatibility with various support mechanisms.
- Ensure secure fastening to prevent movement during use.
Safety Pin and Locking Mechanism
The safety pin and its accompanying locking system play a crucial role in ensuring the stability and security of lifting devices. These components are designed to prevent accidental disengagement during use, thereby enhancing overall safety. Their reliable operation is essential for maintaining control and preventing mishaps when handling heavy loads.
Functionality and Importance
The primary function of the safety pin is to securely fasten the assembly, providing peace of mind while in operation. This mechanism typically engages automatically, ensuring that once the device is lowered, it remains firmly in place. Such a feature is vital, especially when the load is substantial, as it reduces the risk of sudden drops or unintended movement.
Maintenance and Inspection
Regular maintenance and inspection of the safety pin and locking mechanism are necessary to ensure their proper functioning. Users should frequently check for signs of wear or damage and replace any worn-out components promptly. Keeping these elements in optimal condition is essential for safe and effective usage.
Corrosion Protection and Coating Materials
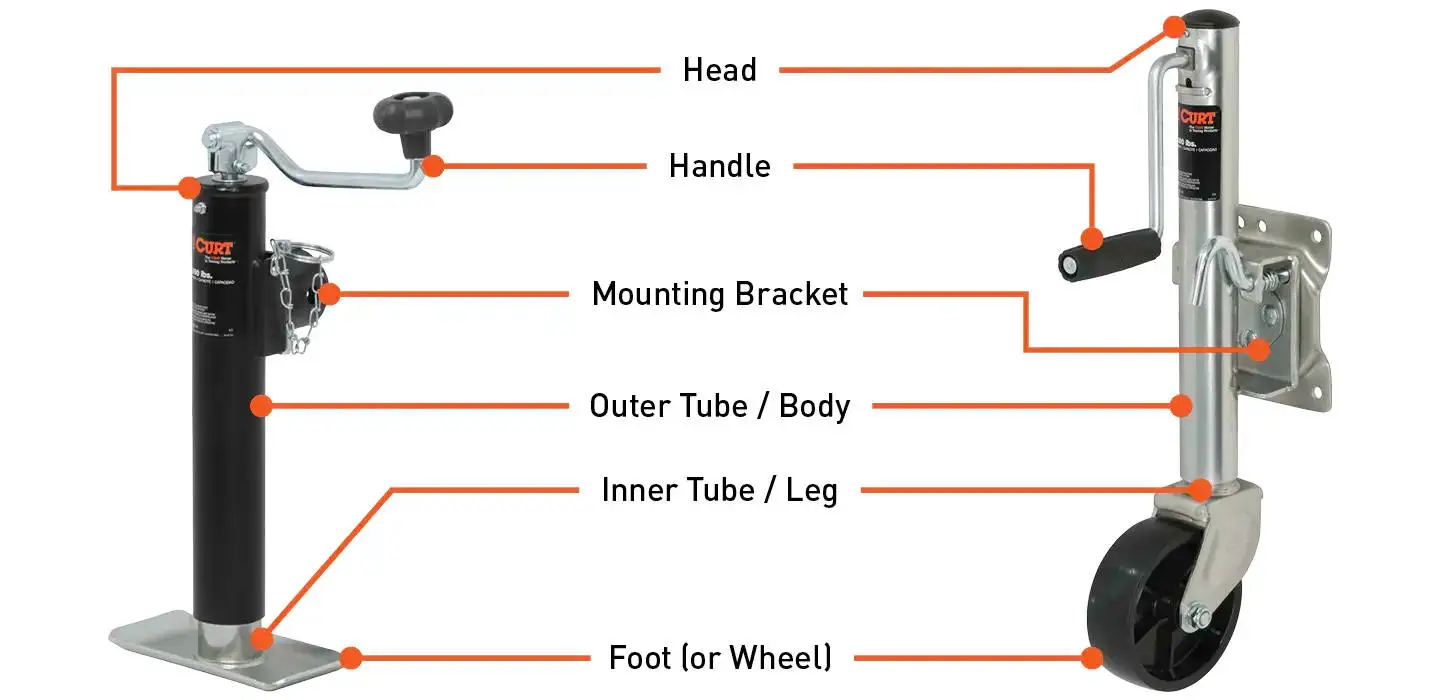
Ensuring the longevity of mechanical components requires effective measures against environmental degradation. Various materials and methods are employed to create a protective barrier, preventing rust and deterioration caused by moisture and other elements.
Understanding Corrosion Resistance is crucial when selecting the appropriate coating. Different environments pose unique challenges, thus necessitating the use of specific materials that can withstand exposure to harsh conditions. For instance, galvanization is a widely used technique that involves applying a zinc layer to ferrous metals, effectively inhibiting rust formation.
Additionally, polymer coatings offer excellent protection due to their flexible nature and resistance to moisture. These coatings can be tailored for various applications, providing not only a barrier against corrosion but also enhancing aesthetic appeal. It is important to evaluate the specific requirements of each application to choose the most suitable protective solution.
Maintenance and Lubrication Tips
Proper upkeep and adequate lubrication are essential for the longevity and efficiency of your lifting mechanism. Regular maintenance not only ensures smooth operation but also prevents wear and tear, ultimately saving you time and money in the long run.
Routine Inspection
- Check for signs of wear or damage on all components.
- Ensure that all bolts and fasteners are tightened securely.
- Inspect the lifting mechanism for any unusual sounds during operation.
Lubrication Practices
- Use a high-quality lubricant suitable for metal-on-metal contact.
- Apply lubricant to all moving parts regularly, especially those that experience friction.
- Wipe off excess lubricant to prevent dirt accumulation.
By following these guidelines, you can maintain the functionality and reliability of your lifting system for years to come.
Common Issues with Trailer Jacks
When utilizing support mechanisms for towing vehicles, several complications may arise, impacting their functionality and safety. Understanding these common problems can aid in effective troubleshooting and maintenance, ensuring optimal performance during use.
Frequent Complications
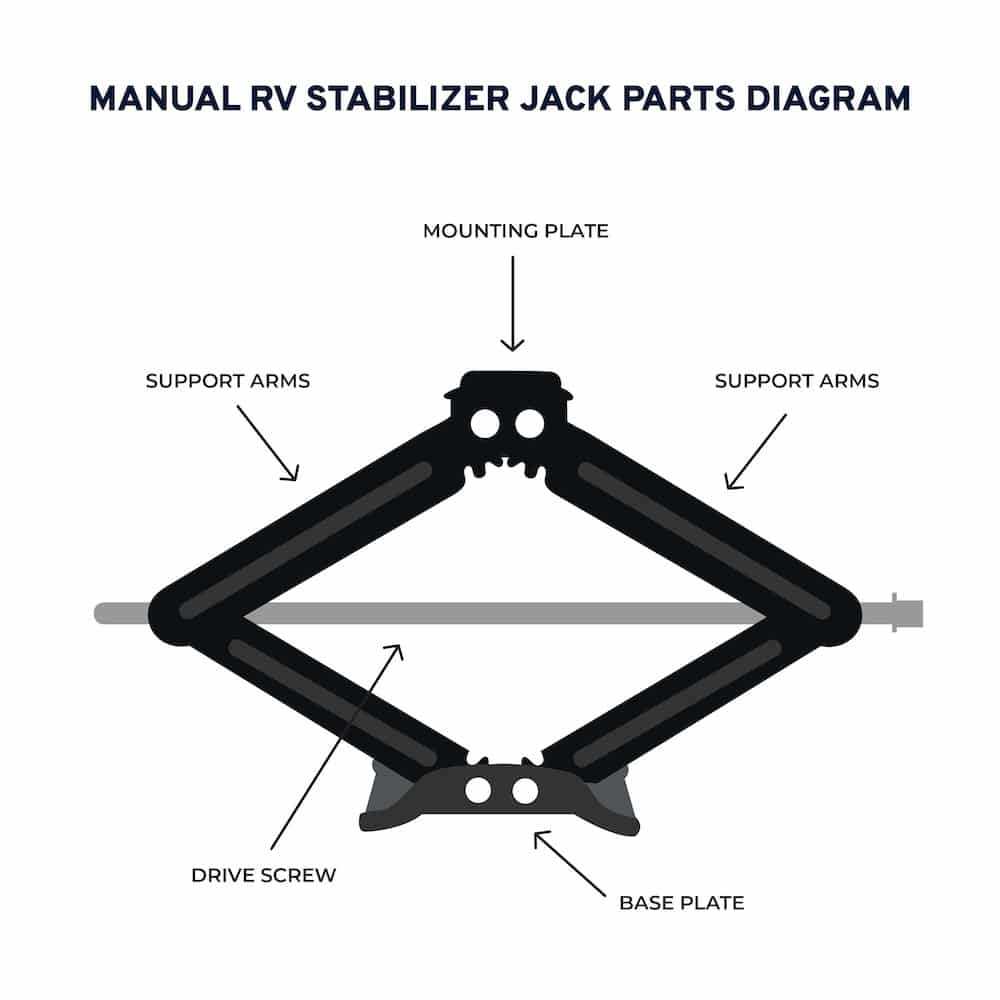
- Difficulty in Raising or Lowering: A common issue occurs when the mechanism becomes stiff or unresponsive, preventing easy adjustments.
- Worn Out Components: Over time, various elements can experience wear, leading to reduced efficiency and the need for replacements.
- Rust and Corrosion: Exposure to the elements can result in rust buildup, which compromises the integrity of the structure.
- Loose Connections: Fasteners and fittings can loosen over time, causing instability and requiring regular inspections.
Maintenance Tips
- Regularly inspect all components for signs of wear or damage.
- Lubricate moving parts to ensure smooth operation.
- Clean the structure to prevent rust and corrosion.
- Tighten any loose fasteners to maintain stability.
Replacing Damaged Trailer Jack Parts
Ensuring the proper functionality of a support mechanism is crucial for safe towing and handling. Over time, certain components may experience wear and tear, necessitating their replacement to maintain optimal performance. This section discusses the process of swapping out compromised elements for improved safety and reliability.
Identifying Worn Components
Before beginning the replacement process, it’s essential to identify which elements are damaged or ineffective. Look for signs of corrosion, cracks, or bending that may indicate a compromised structure. Regular inspections can help catch issues early, allowing for timely intervention.
Steps for Replacement
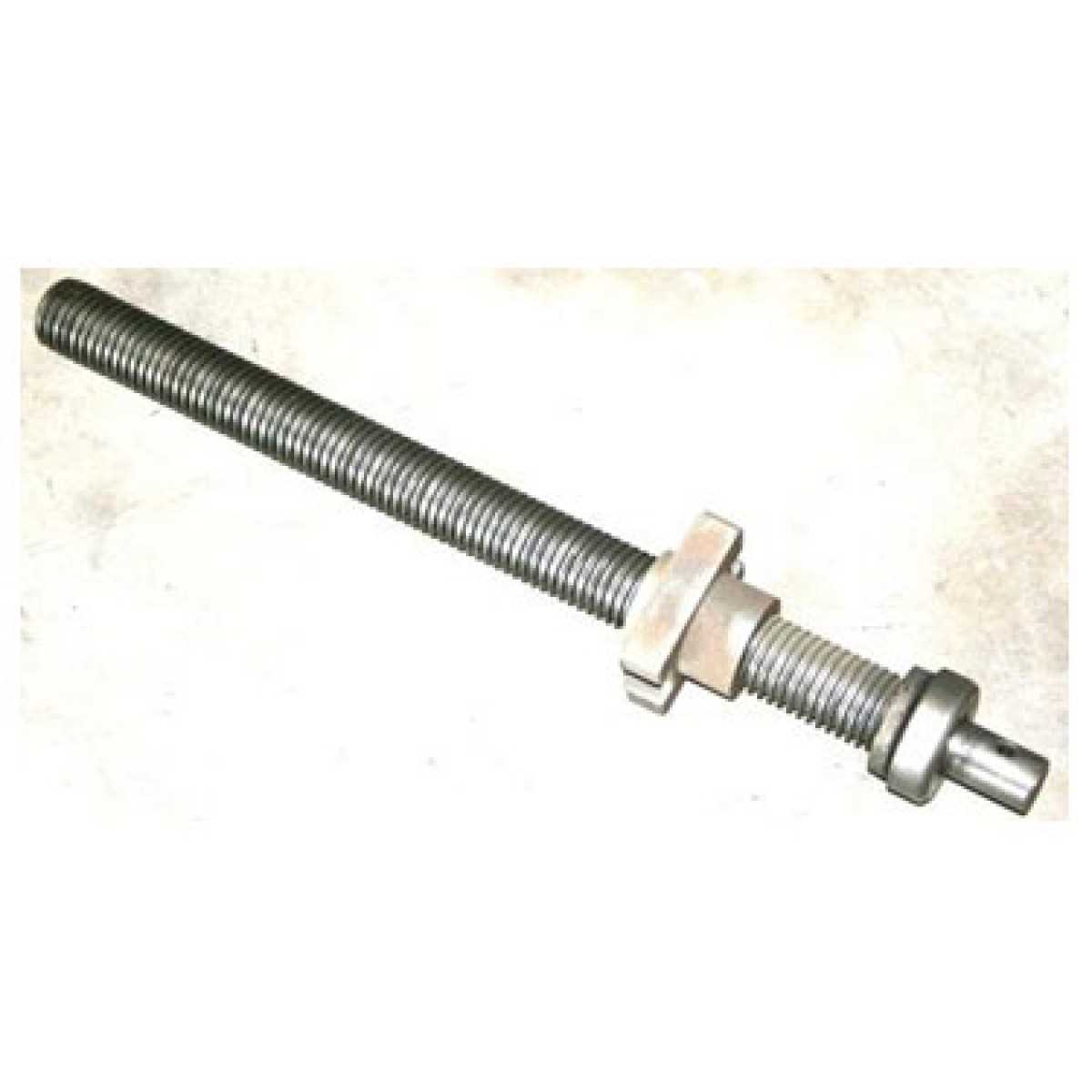
To initiate the replacement, gather the necessary tools and new components. Start by removing the faulty unit carefully, ensuring that all fasteners are adequately addressed. Once the damaged section is removed, install the new element according to the manufacturer’s instructions, securing it firmly in place. After installation, conduct a thorough check to confirm that everything is functioning correctly.