Filters: Water filters
Proper Maintenance for Longevity
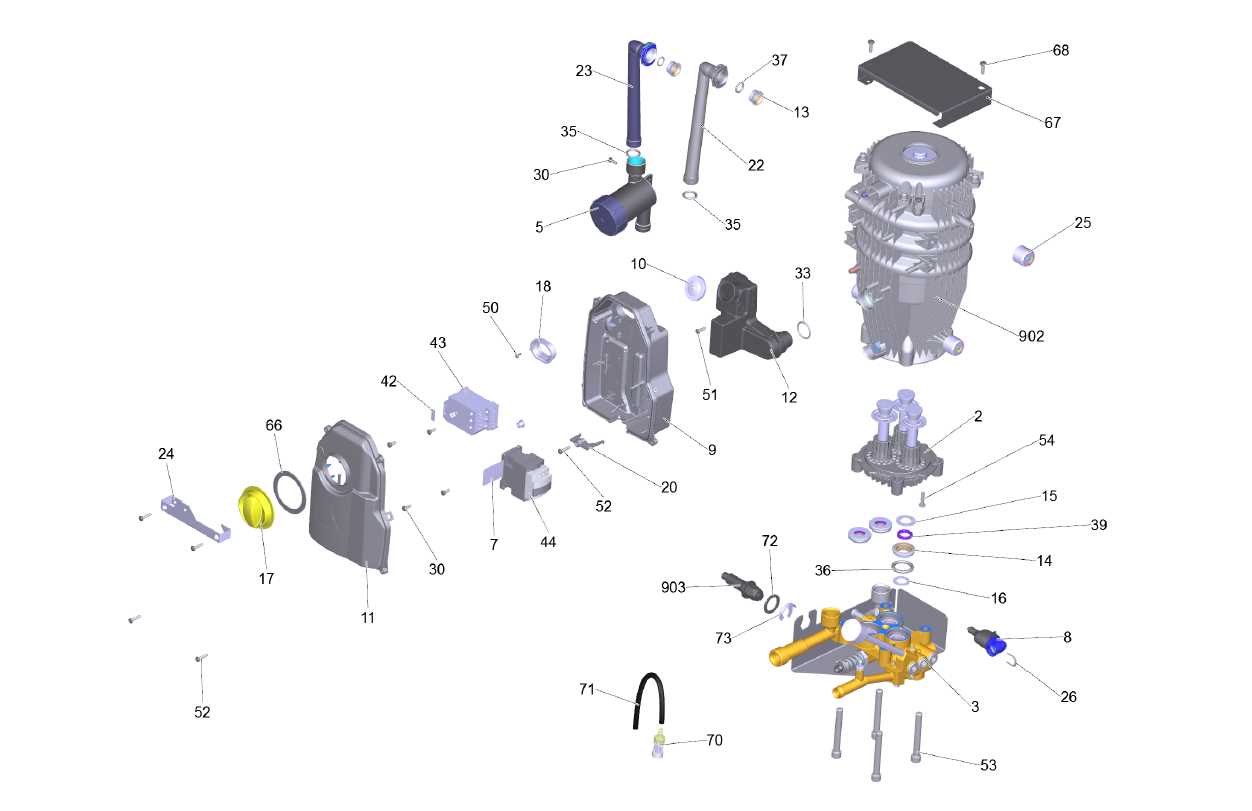
To ensure the prolonged functionality and reliability of your cleaning device, regular upkeep is essential. Adhering to a few straightforward practices can significantly extend the lifespan of your equipment and maintain optimal performance. Below are key strategies for effective maintenance.
Regular Cleaning
Keeping the exterior and components of the unit clean is vital. This helps prevent buildup that can impair functionality. Consider the following steps:
- Wipe down the surface with a damp cloth after each use.
- Check and clean filters to avoid clogging.
- Inspect hoses for leaks and ensure connections are tight.
Routine Checks
Conducting periodic inspections will help identify potential issues before they escalate. Focus on these areas:
- Examine seals and gaskets for wear and tear.
- Test the motor for any unusual sounds or vibrations.
- Ensure that all attachments are functioning correctly.
Implementing these maintenance practices can greatly enhance the efficiency and durability of your equipment, ensuring that it serves you well for years to come.
Hose and Nozzle Connection Overview
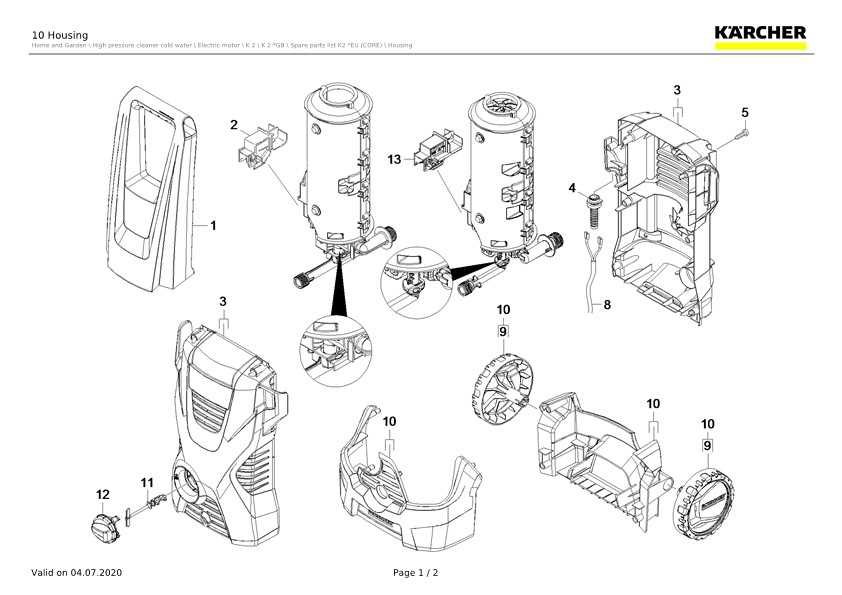
This section provides an understanding of the connections between flexible tubes and spray attachments used in various cleaning systems. Proper assembly and maintenance of these components are crucial for optimal functionality and performance. Users can benefit from comprehending how these elements interact to ensure efficient operation during cleaning tasks.
Types of Hoses
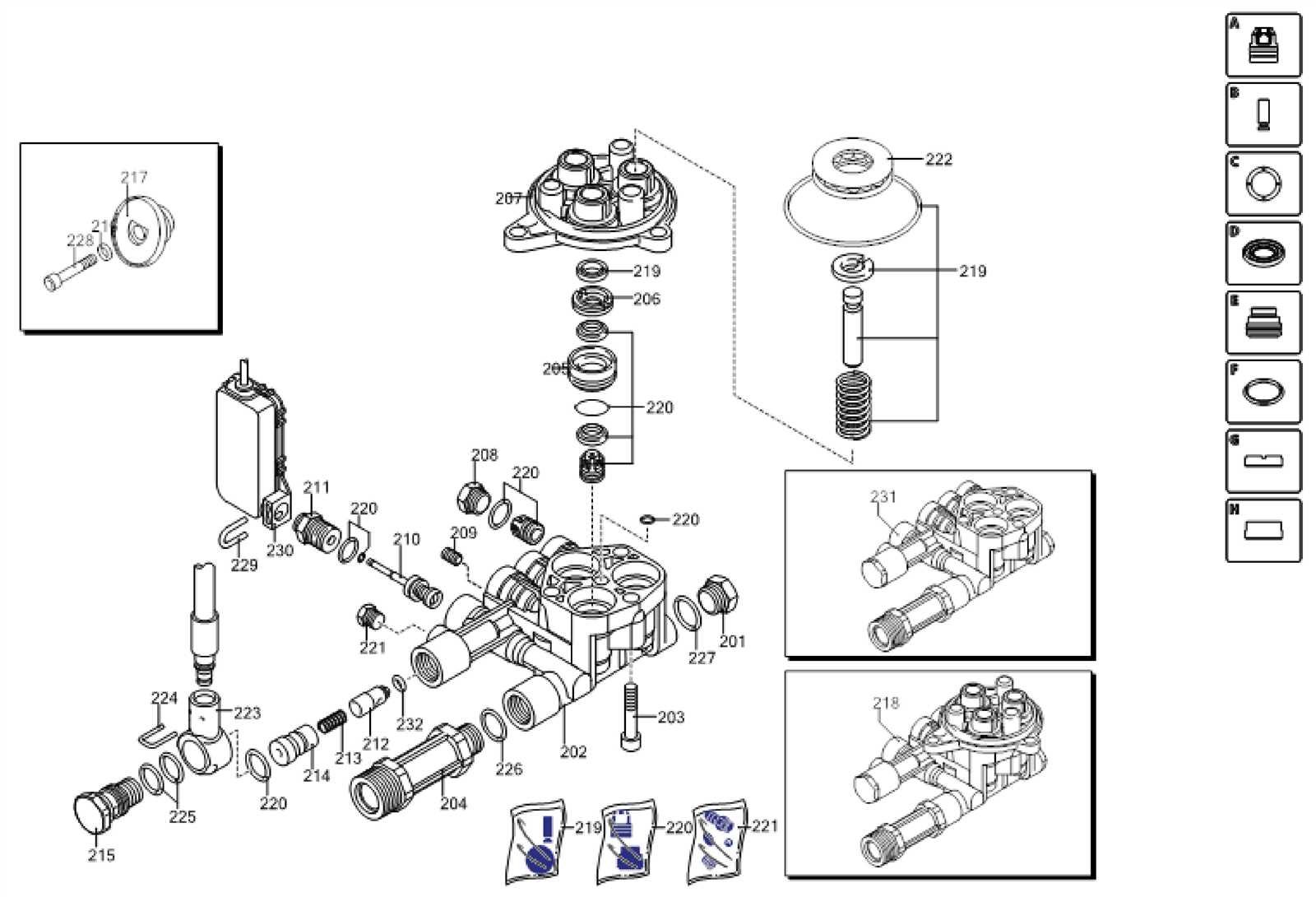
Flexible tubes come in various lengths and diameters, designed to accommodate different cleaning applications. Selecting the appropriate hose is essential for achieving desired water flow and pressure levels. Users should also consider the material of the hose, which can affect durability and resistance to wear.
Nozzle Variations
Spray attachments offer multiple spray patterns to suit various cleaning needs, from gentle misting to focused jets. Understanding the features of each nozzle type helps users to select the right one for specific tasks. Properly connecting nozzles to hoses enhances the overall cleaning efficiency and effectiveness.
Inspecting the Inlet and Outlet Valves
The functionality of any cleaning device relies heavily on the efficient operation of its internal components. Among these, the entry and exit mechanisms play a crucial role in ensuring optimal performance. Regular examination of these elements can help maintain efficiency and prolong the lifespan of the equipment.
Understanding Their Importance
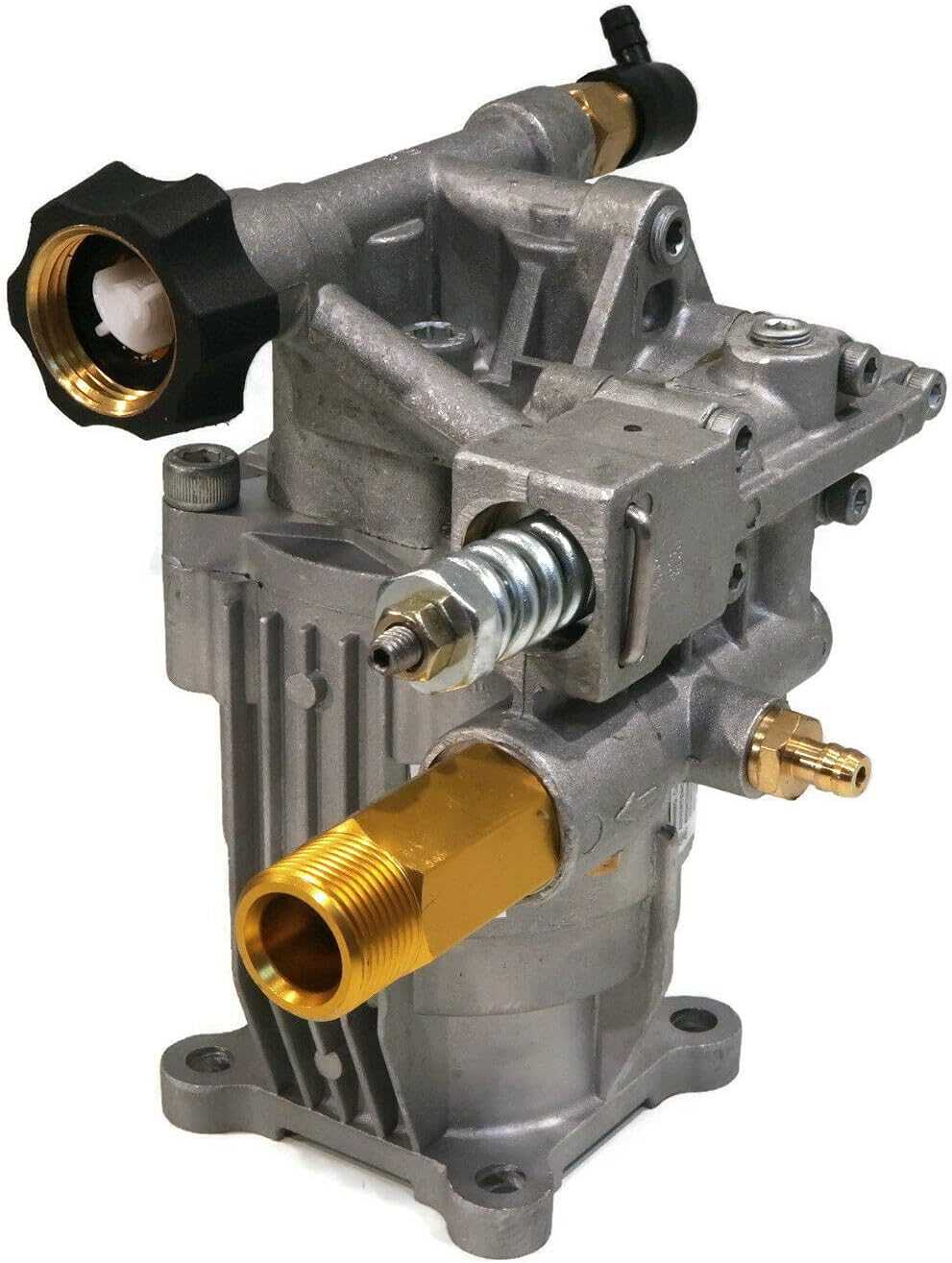
The entry and exit mechanisms facilitate the flow of fluid, making them essential for effective cleaning. If these components become damaged or clogged, it can lead to reduced performance and possible mechanical failures. Thus, recognizing their significance in the overall operation is vital.
Steps for Inspection
To carry out a thorough examination, begin by disconnecting the device from its power source. Inspect both mechanisms for signs of wear or damage, such as cracks or blockages. Cleaning the surfaces and ensuring proper seating can often resolve minor issues. If significant damage is detected, replacement may be necessary to restore full functionality.
Role of the Unloader Valve in Performance
The unloader valve serves a crucial function in enhancing the efficiency and overall operation of cleaning equipment. This component is responsible for regulating the flow of fluid within the system, ensuring optimal pressure levels are maintained during operation. By managing the release of excess pressure, the unloader valve prevents potential damage to the machine and contributes to its longevity.
Impact on Pressure Management
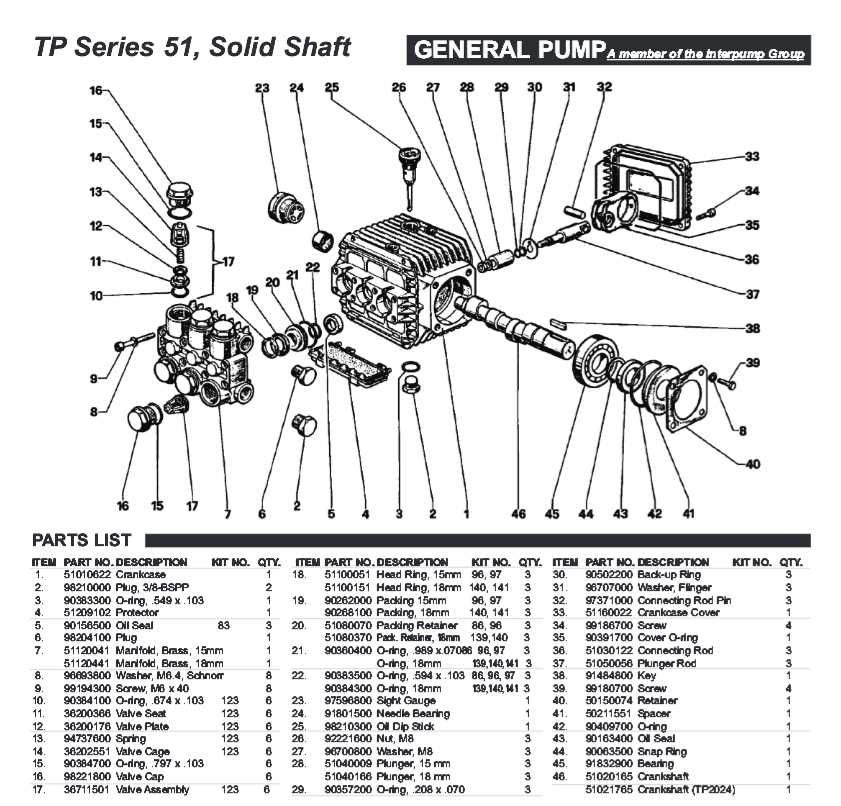
One of the primary roles of the unloader valve is to manage the pressure within the system effectively. When the equipment is not in use, the unloader valve redirects the flow of fluid, preventing unnecessary strain on the motor and other components. This not only helps in conserving energy but also extends the lifespan of the machinery by minimizing wear and tear.
Contribution to Efficiency
In addition to pressure regulation, the unloader valve plays a significant role in enhancing the efficiency of the equipment. By ensuring that the right amount of fluid is circulated, it enables the machine to perform optimally while consuming less energy. This efficiency translates into better cleaning results, allowing users to achieve their desired outcomes with less effort and time.
Seals and O-Rings: Importance and Care
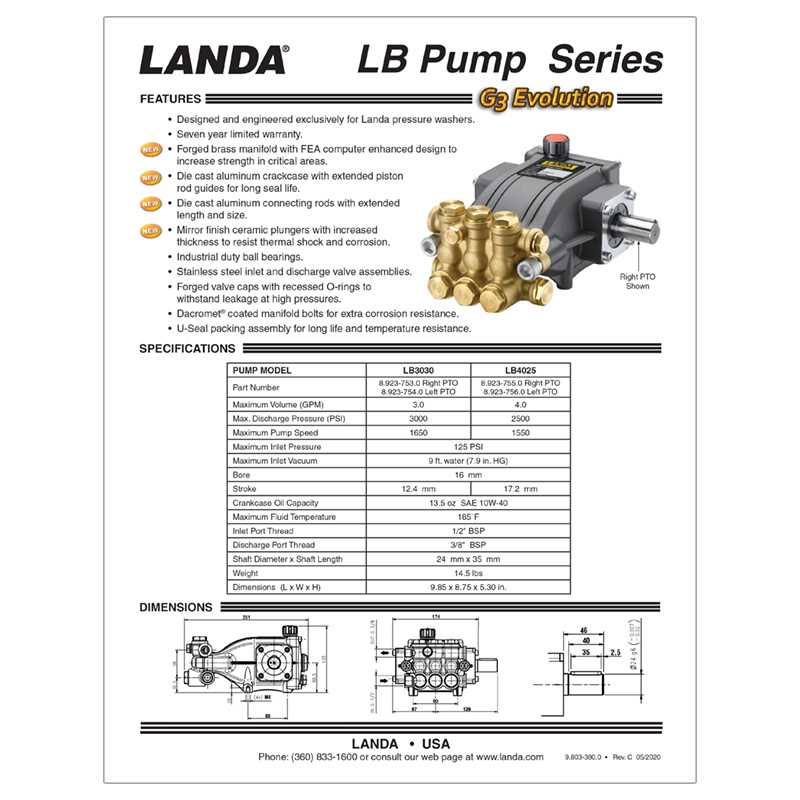
In any mechanical system, the functionality and longevity of components heavily rely on the effectiveness of seals and O-rings. These essential elements serve to prevent the escape of fluids and protect internal mechanisms from contamination. Ensuring their proper maintenance is crucial for optimal performance and reliability.
Significance of Seals and O-Rings
Seals and O-rings play a vital role in maintaining pressure integrity within a system. They act as barriers that minimize leakage, thereby enhancing efficiency. Additionally, these components help to safeguard sensitive parts from dirt and moisture, which can lead to wear and tear over time.
Maintenance Tips
Regular inspection and maintenance of seals and O-rings are essential to ensure their effectiveness. Check for signs of wear, such as cracks or deformation, and replace any damaged components promptly. Furthermore, keeping these elements clean and lubricated will extend their lifespan and maintain system efficiency.
Guidelines for Replacing Damaged Parts
When it comes to maintaining your cleaning equipment, addressing any faulty components promptly is crucial for ensuring optimal performance. This section outlines essential recommendations for effectively replacing any compromised elements in your device.
Follow these guidelines to ensure a smooth replacement process:
- Identify the Issue: Before starting the replacement, accurately diagnose the problem. Check for any visible signs of wear or malfunction.
- Gather Necessary Tools: Ensure you have all required tools at hand, including screwdrivers, wrenches, and any specific equipment needed for your model.
- Select Quality Replacements: Always choose high-quality components that are compatible with your model to guarantee longevity and efficiency.
- Follow Manufacturer Instructions: Refer to the user manual for specific replacement instructions and diagrams to avoid any potential errors.
- Test After Replacement: Once the new component is installed, run a test to ensure everything operates correctly and efficiently.
By adhering to these guidelines, you can effectively manage replacements and maintain the efficiency of your cleaning device for years to come.
Common Issues and Troubleshooting Tips
When operating cleaning equipment, users may encounter various challenges that can affect performance. Identifying these issues early can save time and effort, ensuring that the device operates efficiently. Understanding the common problems and their potential solutions is crucial for maintaining the longevity and effectiveness of the equipment.
Frequent Performance Problems
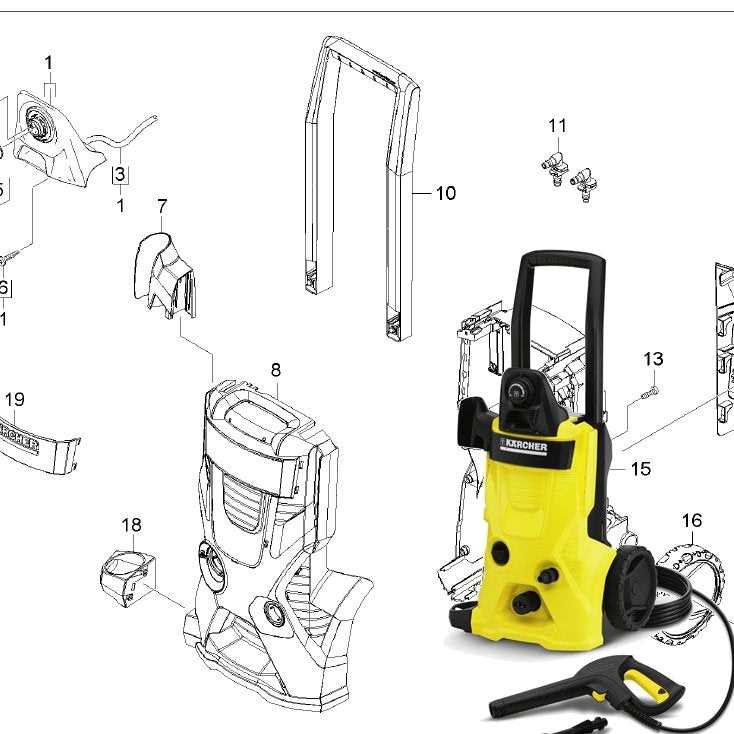
One of the most common issues faced is a lack of pressure during use. This can stem from several factors, including clogged filters or hoses. Regular maintenance, such as cleaning or replacing these components, can often resolve the problem. Additionally, ensuring that the water supply is adequate and that connections are secure can help restore optimal function.
Noise and Vibration Concerns
Unusual noises or excessive vibration may indicate internal problems. Such symptoms can arise from loose components or worn-out bearings. Inspecting the device for any loose screws or signs of wear can assist in diagnosing these issues. Tightening any loose parts and replacing worn components promptly will contribute to smoother operation and enhance overall performance.
Optimizing Performance Through Regular Checks
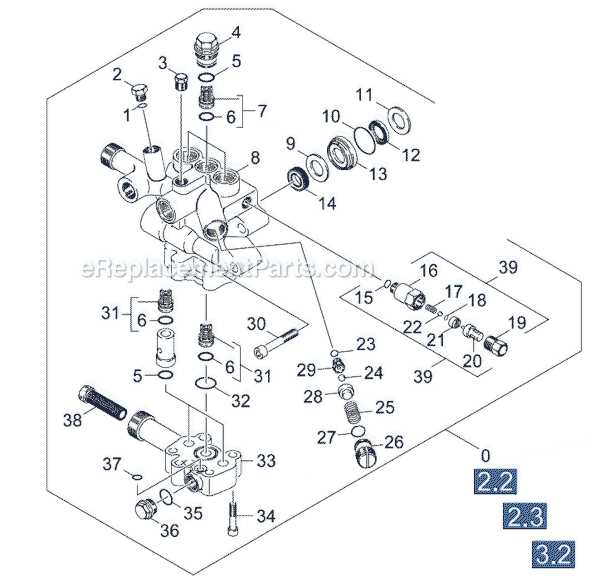
Maintaining optimal functionality of any cleaning equipment involves consistent inspections and timely interventions. Regular evaluations can help identify issues before they escalate, ensuring that the device operates efficiently and extends its lifespan. This section focuses on essential checks that enhance overall effectiveness.
Key Areas for Inspection
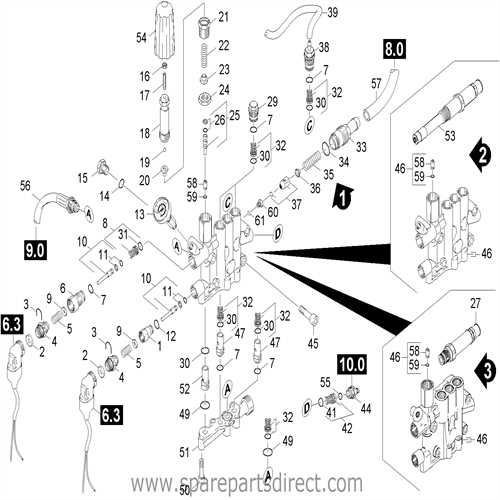
Regular assessments should encompass several critical components. Each element plays a vital role in ensuring the device functions as intended. The following table outlines the primary areas to focus on during routine checks:
Component |
Recommended Action |
Frequency |
Hoses |
Inspect for leaks or wear |
Monthly |
Filters |
Clean or replace as needed |
Every 3 months |
Nozzles |
Check for clogs and cleanliness |
Before each use |
Connections |
Ensure tightness and integrity |
Every 6 months |
Benefits of Routine Maintenance
Implementing a structured maintenance routine yields numerous advantages. Not only does it enhance the reliability of the equipment, but it also improves the efficiency of operations, reducing energy consumption and ensuring better results. Ultimately, dedicating time to regular checks pays off through enhanced performance and reduced repair costs.