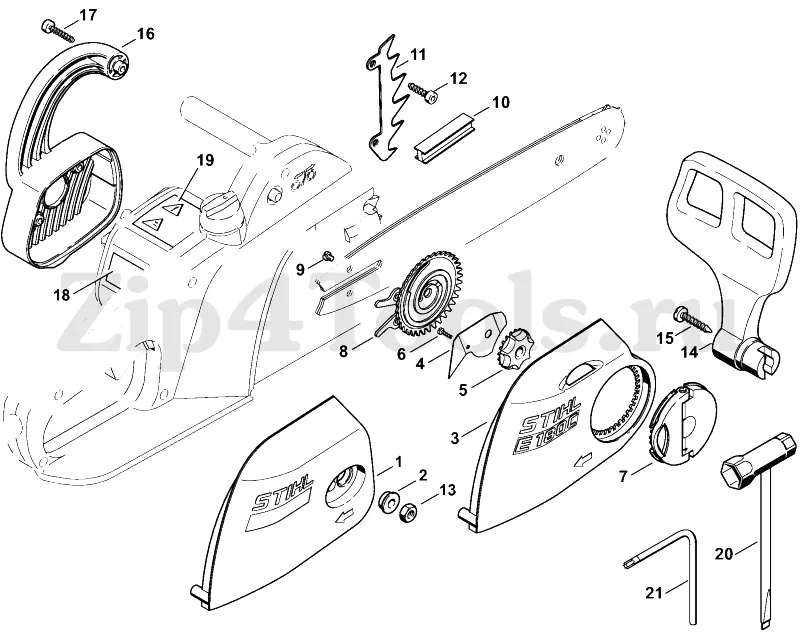
When working with various mechanical tools, it becomes essential to have a clear understanding of their internal structures. This knowledge aids in both maintenance and troubleshooting, ensuring that every part functions smoothly and efficiently. By familiarizing yourself with the key elements and how they interact, you can significantly extend the lifespan of your equipment while also optimizing performance.
In this guide, we will explore the fundamental components that form the backbone of these machines. Each element plays a critical role, contributing to the overall effectiveness of the device. Whether you are looking to repair, replace, or simply understand the structure, identifying and recognizing these individual elements is crucial for successful upkeep.
We’ll break down the major assemblies, examine how they work together, and provide an overview that helps demystify the internal workings of these tools. With the right knowledge, tackling any issues or performing regular maintenance becomes a much more straightforward task.
Understanding the Components of an Electric Chainsaw
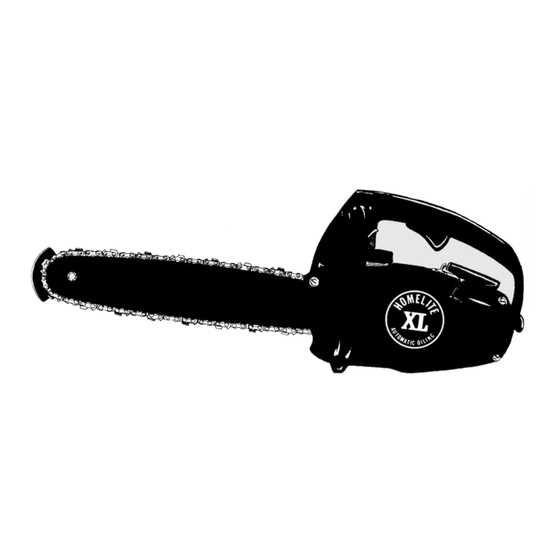
Proper comprehension of the internal mechanisms and external features of this powerful tool is crucial for its effective use and maintenance. Each element plays a specific role, contributing to the functionality and performance during operation. Let’s explore the essential sections that make up the device.
- Power Source: This unit drives the motor and provides the energy required for the device to operate.
- Motor: The motor converts the supplied energy into mechanical motion, powering the cutting mechanism.
- Cutting Blade: A sharp, rotating or moving element that slices through wood and other materials with precision.
- Safety Features: Components designed to protect the user, such as automatic shut-off mechanisms and guards.
- Control System: A set of levers and buttons that allow the operator to manage speed, start, and stop functions.
- Chain Tensioner: This mechanism ensures the cutting chain remains properly aligned and tensioned for smooth operation.
Motor Assembly Overview
The core of the cutting tool lies within its engine system, which is responsible for powering the mechanism. This section provides a thorough understanding of how the internal components function together to drive the device. Key elements within this unit ensure the proper transfer of energy, ensuring smooth and effective operation during use.
Main Components of the Motor
The motor consists of several crucial parts that work in harmony to generate the necessary force. These include the rotor, stator, and brushes, each playing a pivotal role in the movement. The interaction between these components allows for efficient energy conversion, driving the chain to perform its task efficiently.
How Energy is Transmitted
Once initiated, the system converts electrical power into mechanical motion, with the rotating elements facilitating this transition. The rotor spins at high speed, interacting with the magnetic field produced by the stator, allowing for the smooth delivery of force. The brushes ensure continuous contact, maintaining steady performance throughout the process.
Chain and Bar System Explained
The essential cutting mechanism revolves around the interaction between two main components. These elements work in unison to deliver precise and efficient slicing, forming the core functionality of any cutting tool.
The chain consists of sharp links designed to move along a guiding path. Each link is meticulously engineered to cut through material with minimal resistance. Its movement is powered by an internal drive system, ensuring consistent speed and power throughout the process.
The bar acts as a stabilizer and guide for the chain. This sturdy component ensures the cutting line remains accurate, providing balance and reducing the risk of deviation during operation. The surface is designed to reduce friction, allowing the chain to glide smoothly while maintaining optimal alignment.
Understanding the relationship between these components is vital for maintaining peak performance. Proper tensioning, lubrication, and alignment all contribute to the overall efficiency, making this system a critical aspect of the tool’s operation.
Guide to the Chain Tensioner
Maintaining the correct tension is crucial for efficient operation and prolonged durability of the cutting system. This guide will help you understand how the tensioner works and how to adjust it for optimal performance. Consistent attention to this component ensures smoother cutting and minimizes wear.
Step |
Action |
Result |
1 |
Locate the adjustment mechanism near the guide bar area. |
Properly positioned for easy access and control. |
2 |
Turn the tensioning screw clockwise to tighten the chain. |
Increased tension for a secure and stable operation. |
Understanding the Oil Reservoir Function
The lubrication system plays a crucial role in maintaining optimal performance and extending the lifespan of any cutting equipment. One of its key components is the oil container, which ensures that the chain remains well-lubricated during operation, preventing excessive wear and friction.
The Role of Lubrication
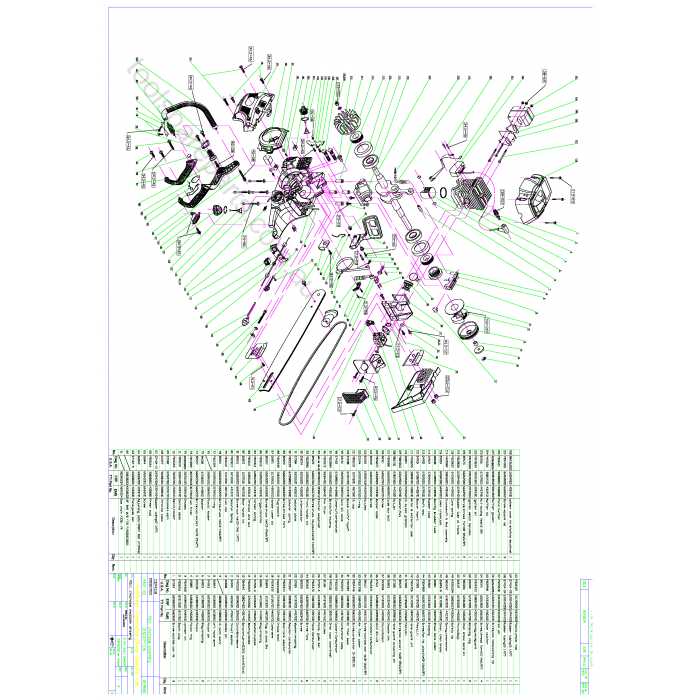
Without a consistent supply of oil, friction between the moving components can lead to significant damage. The reservoir stores the necessary lubricant, releasing it gradually to ensure smooth operation throughout use.
Key Features of the Oil Container
- Automatic release mechanism to distribute lubricant efficiently.
- Easy-to-access filler cap for convenient refilling.
- Transparent design for quick oil level inspection.
Maintaining a sufficient level of lubricant is essential for long-term reliability and effective cutting performance.
Handle Design and Safety Features
When working with power tools, the design of the handle plays a crucial role in providing both comfort and control. The structure of the grip ensures a stable and secure hold, reducing the risk of accidents during operation. Thoughtful design elements, such as ergonomic contours and textured surfaces, enhance user experience and prevent fatigue during prolonged use.
Safety is paramount in the design of the handle, and manufacturers incorporate various features to minimize risks. For instance, the inclusion of a safety switch or trigger lock helps prevent unintended activation, offering an extra layer of protection. Additionally, protective guards around the handle can shield users from debris or accidental contact with moving parts, ensuring safe handling at all times.
Beyond comfort and safety, the materials used in constructing the handle are equally important. Lightweight yet durable components are selected to provide strength while maintaining ease of maneuverability. These factors work together to make the tool both practical and secure in various work environments.
Trigger and Lock Mechanism
The trigger and locking system is an essential component of any cutting tool, ensuring safety and control during operation. This mechanism is designed to provide the user with the ability to engage the tool with precision while preventing accidental activation. It typically involves two main parts: the trigger that initiates the action and the lock that prevents the tool from starting unintentionally when not in use.
The trigger mechanism is the point of interaction between the user and the tool. It responds to pressure applied by the operator, engaging the internal components and activating the cutting functions. This system must be sensitive yet responsive enough to allow for easy activation without being too prone to accidental engagement.
On the other hand, the locking system serves as a safety feature, often requiring a deliberate action to release it before the tool can be activated. This feature is crucial in preventing unintentional startups, especially when the tool is being handled or transported. A well-designed locking mechanism enhances the overall safety of the tool by ensuring that the user must intentionally engage the cutting function.
In conclusion, the integration of these two elements–trigger and lock–forms a critical part of the tool’s design, balancing ease of use with necessary safety features to reduce risks during operation.
Inspecting the Sprocket for Wear
When maintaining your cutting tool, it’s crucial to examine key components that affect overall performance. One of the most important parts to inspect regularly is the rotating mechanism that engages with the chain. Over time, this element may show signs of wear, which could lead to inefficient operation or damage to other parts. Ensuring this component is in optimal condition helps prolong the life of the equipment and prevents unnecessary repairs.
Signs of Wear
Examine the surface for any noticeable grooves, cracks, or deformation. A well-maintained rotating element should have a smooth and even surface, allowing for proper chain movement. Any irregularities, such as chipped teeth or uneven wear, can affect the function and cause the chain to slip or become misaligned.
Steps to Inspect
To inspect this component, first remove any safety covers or barriers. Then, visually inspect the sprocket for signs of damage. Gently rotate the mechanism to ensure it moves freely and does not experience resistance. If the sprocket seems worn or damaged, consider replacing it to avoid further complications. Always replace any parts with suitable replacements to maintain the tool’s effectiveness.
Examining the Chain Brake System
The brake mechanism is a critical safety feature in cutting tools, designed to reduce the risk of injury during operation. This system is responsible for stopping the chain when certain conditions are met, ensuring the user maintains full control. Understanding its components and how they work together is essential for maintaining safety and performance.
Key Components
- Brake band
- Brake lever
- Activation mechanism
The brake band wraps around the sprocket, slowing down or halting the movement of the chain when engaged. The brake lever, typically located near the handle, is activated either manually or automatically in response to certain actions, such as a sudden kickback.
How It Works
- Manual activation: The user engages the brake by pressing a lever, quickly stopping the chain.
- Automatic activation: In the event of kickback or unusual movement, the system automatically triggers to stop the chain.
This dual-function design helps prevent accidents and enhances operational control, ensuring the device remains safe even in high-risk situations.
Power Cord and Switch Layout
This section focuses on the configuration and organization of the electrical components that deliver power to the tool, specifically the flexible cable and the control mechanism used to initiate and stop the device. Proper understanding of the setup is crucial for maintenance and troubleshooting to ensure smooth operation and safety during use.
Understanding the Power Cord Arrangement
The power cord is a key component, designed to transfer electrical current from the outlet to the machine. It is typically structured to withstand wear and tear, offering durability in various working conditions. The cord is often equipped with a sturdy insulation layer to protect against abrasions, moisture, and electrical hazards. The length and thickness are carefully chosen to meet the demands of the tool while maintaining flexibility and ease of movement during operation.
Control Mechanism and Switch Functionality
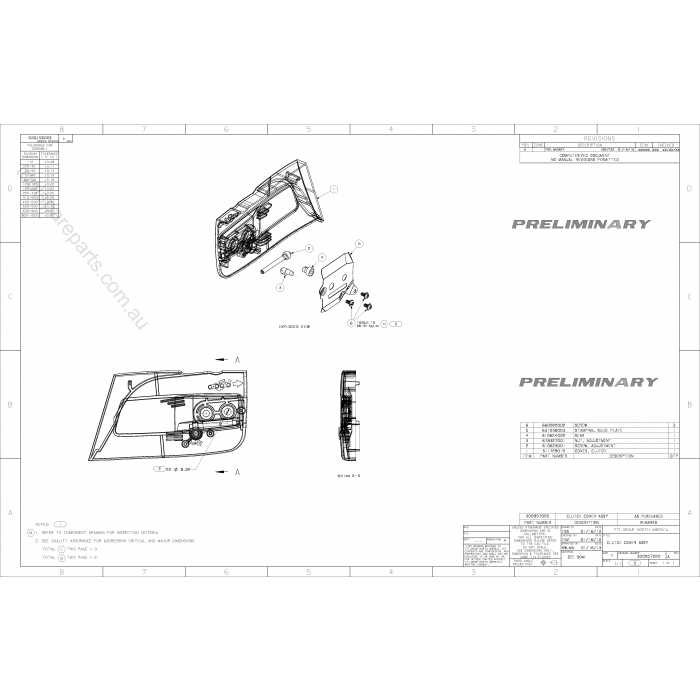
The control switch is the central interface for turning the tool on and off. It is usually designed for easy accessibility, ensuring the user can quickly activate or deactivate the device without unnecessary effort. In many cases, the switch is integrated into the housing of the device for convenience, offering both safety and reliability. A well-designed switch system contributes significantly to the overall performance and user experience.
Bar Cover and Chain Protection
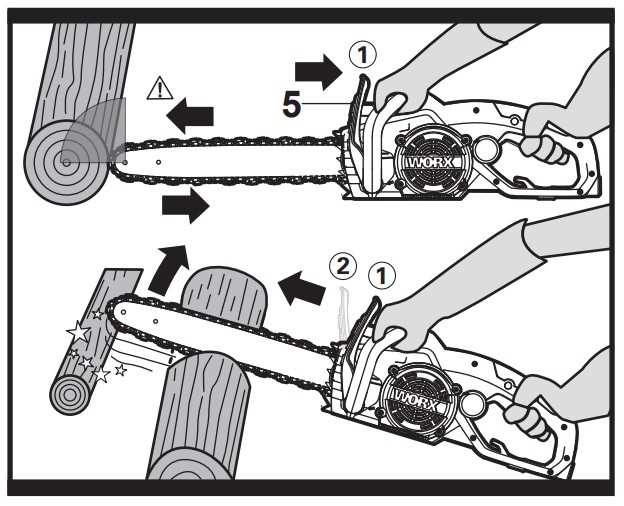
Ensuring the safety and longevity of a cutting tool requires careful attention to the protective components that surround its working elements. The cover designed for the bar and the mechanisms in place to guard the chain play crucial roles in preventing damage and reducing wear. These features are vital in safeguarding both the user and the tool during operation and storage.
The cover serves as a shield for the bar and chain, offering protection against dirt, moisture, and physical damage. It also helps maintain optimal performance by preventing corrosion and other forms of deterioration. When not in use, this protective component is essential for keeping the cutting edge safe from accidental contact and environmental factors.
Chain protection mechanisms are equally important. They ensure that the chain remains secure and properly tensioned, reducing the risk of operational failures. These safeguards contribute to the overall safety by reducing the chances of unexpected malfunctions that could lead to accidents or damage to the tool.
Cleaning and Maintaining Key Parts
Regular upkeep of essential components is vital for extending the life of your equipment and ensuring its optimal performance. Keeping all elements in top condition can prevent unnecessary breakdowns and maintain efficiency during use. A few simple steps can go a long way in improving both functionality and safety.
The following areas require consistent attention to avoid wear and tear:
- Motor Housing: Keep free from dirt and debris. Use a damp cloth to wipe surfaces, ensuring ventilation areas remain unobstructed.
- Cutting Mechanism: Ensure the cutting area is well-lubricated and free of any accumulated sap or debris. Regularly check the alignment and tension of the chain.
- Cooling Vents: Clear any dust or dirt from the vents to maintain proper airflow and prevent overheating.
- Handles: Clean regularly to remove any grime that may build up during use, ensuring a comfortable grip for safe operation.
By following these maintenance tasks, your equipment will perform at its best, ensuring smoother operations and fewer disruptions during work.