Pul
Pulley Mechanisms for Smooth Performance
The efficient operation of mowing equipment relies heavily on the functionality of its pulley systems. These mechanisms ensure a consistent transfer of motion, allowing various components to work harmoniously. Proper maintenance and understanding of these elements are key to achieving optimal results.
Key Functions of the Pulley System
- Motion Transfer: The pulleys direct rotational movement from one part to another, ensuring synchronized action across the machine.
- Tension Management: Correct tension within the system prevents slippage and ensures consistent performance under varying conditions.
- Wear Prevention: Well-maintained pulleys reduce friction, prolonging the lifespan of belts and other linked components.
Maintenance Tips for
Deck Shell Construction and Durability
The design and robustness of the shell that encases the cutting components play a crucial role in the overall performance and longevity of lawn maintenance equipment. A well-constructed casing not only ensures efficient operation but also withstands the rigors of regular use, making it essential for homeowners and professionals alike.
Materials Used in Construction
The choice of materials for the outer shell significantly impacts durability. High-quality steel is commonly utilized due to its strength and resistance to wear and tear. Additionally, some models incorporate a powder-coated finish that provides extra protection against corrosion and environmental factors, extending the lifespan of the equipment.
Impact of Design on Performance
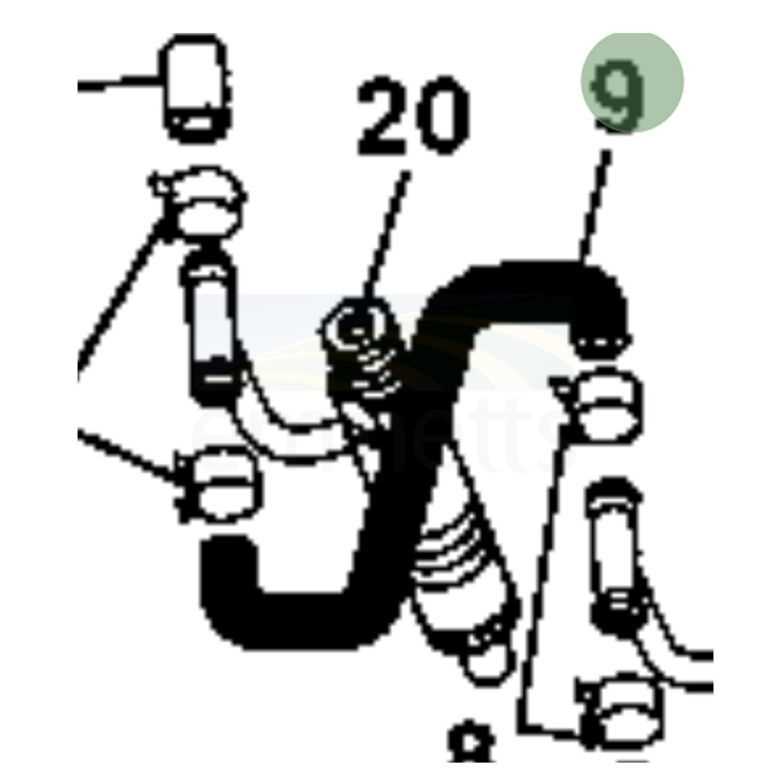
Engineered for optimal airflow and grass flow, the configuration of the casing influences cutting efficiency and overall functionality. An aerodynamic shape reduces drag, allowing for smoother operation, while strategic reinforcements ensure that the structure can endure impacts and stress during operation. Attention to detail in design translates to enhanced reliability and satisfaction in performance.
Adjusting the Mower Deck for Optimal Results
Properly calibrating the cutting apparatus is essential for achieving an immaculate lawn. Correct adjustments ensure that the blades function efficiently and deliver an even cut, promoting healthy grass growth and enhancing the overall aesthetic of your outdoor space.
Follow these steps to achieve the best results:
- Check the Leveling: Ensure that the cutting unit is level from side to side and front to back. This prevents uneven cutting and enhances the longevity of the blades.
- Adjust the Height: Set the desired height for cutting. Different grass types require different cutting heights for optimal health.
- Inspect the Blades: Regularly check the blades for sharpness and wear. Dull blades can tear grass rather than cut it cleanly, leading to brown tips.
- Maintain Proper Tire Pressure: Ensure that the tires are inflated to the recommended pressure. Uneven tire pressure can affect the level of the cutting apparatus.
By adhering to these guidelines, you can maintain an effective cutting tool that yields a beautifully manicured lawn throughout the mowing season.
Importance of the Idler Arm and Bracket
The idler arm and its associated bracket play a crucial role in the overall functionality of lawn maintenance equipment. These components are essential for ensuring that the cutting mechanism operates smoothly and efficiently. A well-designed idler arm helps maintain the proper tension in the belt system, which directly impacts the performance and longevity of the machinery.
These elements are responsible for guiding and supporting the drive belt, allowing for optimal power transfer from the engine to the cutting blades. Any wear or damage to the idler arm or bracket can lead to a range of operational issues, including reduced cutting efficiency and increased strain on other components.
Regular inspection and maintenance of these parts are vital for preventing potential breakdowns. When functioning correctly, the idler arm and bracket not only enhance performance but also contribute to a more consistent and reliable mowing experience.
Component |
Function |
Idler Arm |
Maintains tension on the drive belt, ensuring smooth operation. |
Bracket |
Supports the idler arm and secures it in place for proper alignment. |
Inspecting the Tension Spring for Proper Operation
Regular examination of the tension spring is essential to ensure optimal performance and longevity of the equipment. This component plays a critical role in maintaining the necessary force and stability during operation. A well-functioning spring contributes to the overall efficiency and effectiveness of the machinery.
Visual Inspection: Begin by conducting a thorough visual inspection of the tension spring. Look for signs of wear, corrosion, or deformation. Any noticeable damage could indicate a need for replacement. Ensure that the spring is securely attached and aligned properly within its housing.
Functionality Check: After the visual assessment, perform a functionality check. Engage the mechanism that the spring operates to observe its responsiveness. The spring should provide consistent tension without any noticeable slack or excessive resistance. If the spring fails to respond as expected, it may require adjustment or replacement.
Cleaning and Maintenance: Keeping the tension spring clean is crucial for its performance. Remove any dirt or debris that may have accumulated. Lubrication, if necessary, should be applied according to the manufacturer’s specifications to ensure smooth operation.
Conclusion: Regular inspection and maintenance of the tension spring will help prevent operational issues and extend the life of your equipment. By following these steps, you can ensure that the spring functions effectively and contributes to the machinery’s overall performance.
Common Wear Points on Deck Parts
Understanding the areas that experience significant wear in mowing equipment is essential for maintaining optimal performance and extending the lifespan of the machinery. These components often encounter a range of challenges, including friction, exposure to the elements, and constant movement, leading to potential degradation over time.
Key Areas of Concern
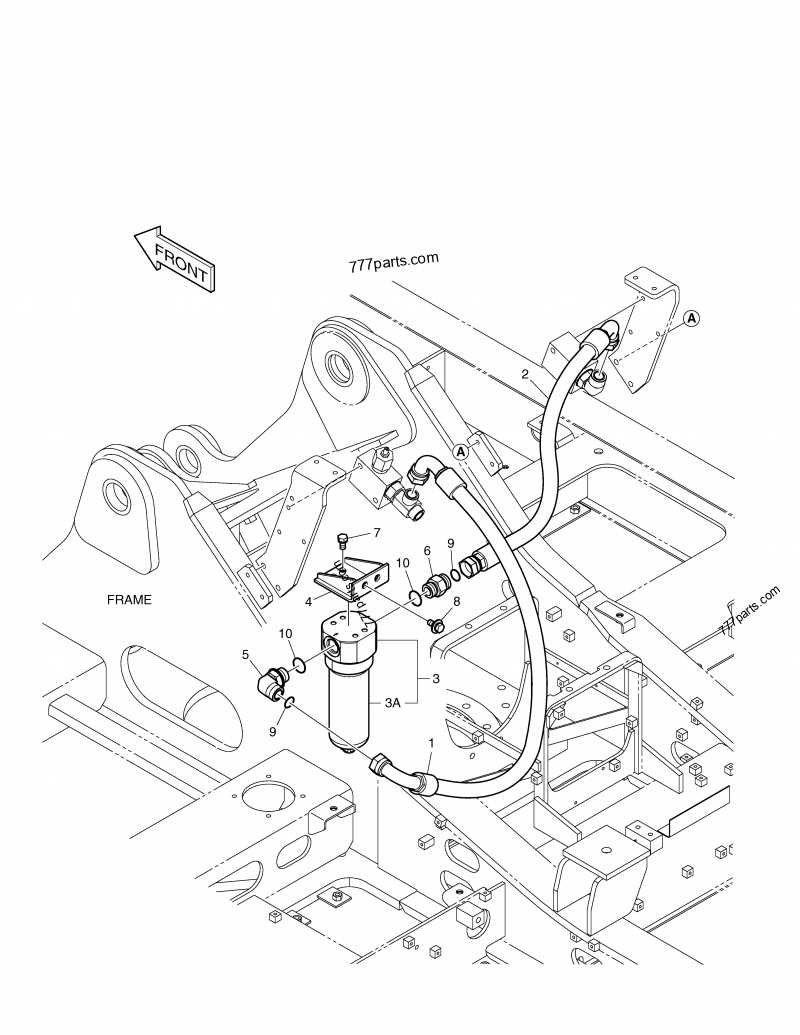
Several specific regions warrant close attention during routine inspections. Recognizing these wear points allows for timely maintenance, preventing more extensive damage and costly repairs.
Component |
Common Issues |
Recommended Maintenance |
Blades |
Chipping, dullness |
Regular sharpening, replacement as needed |
Spindles |
Worn bearings, misalignment |
Lubrication, alignment checks |
Wheels |
Flat spots, wear on tread |
Rotation, inflation checks |
Skirts |
Cracks, detachment |
Inspection, secure fastening |
Conclusion
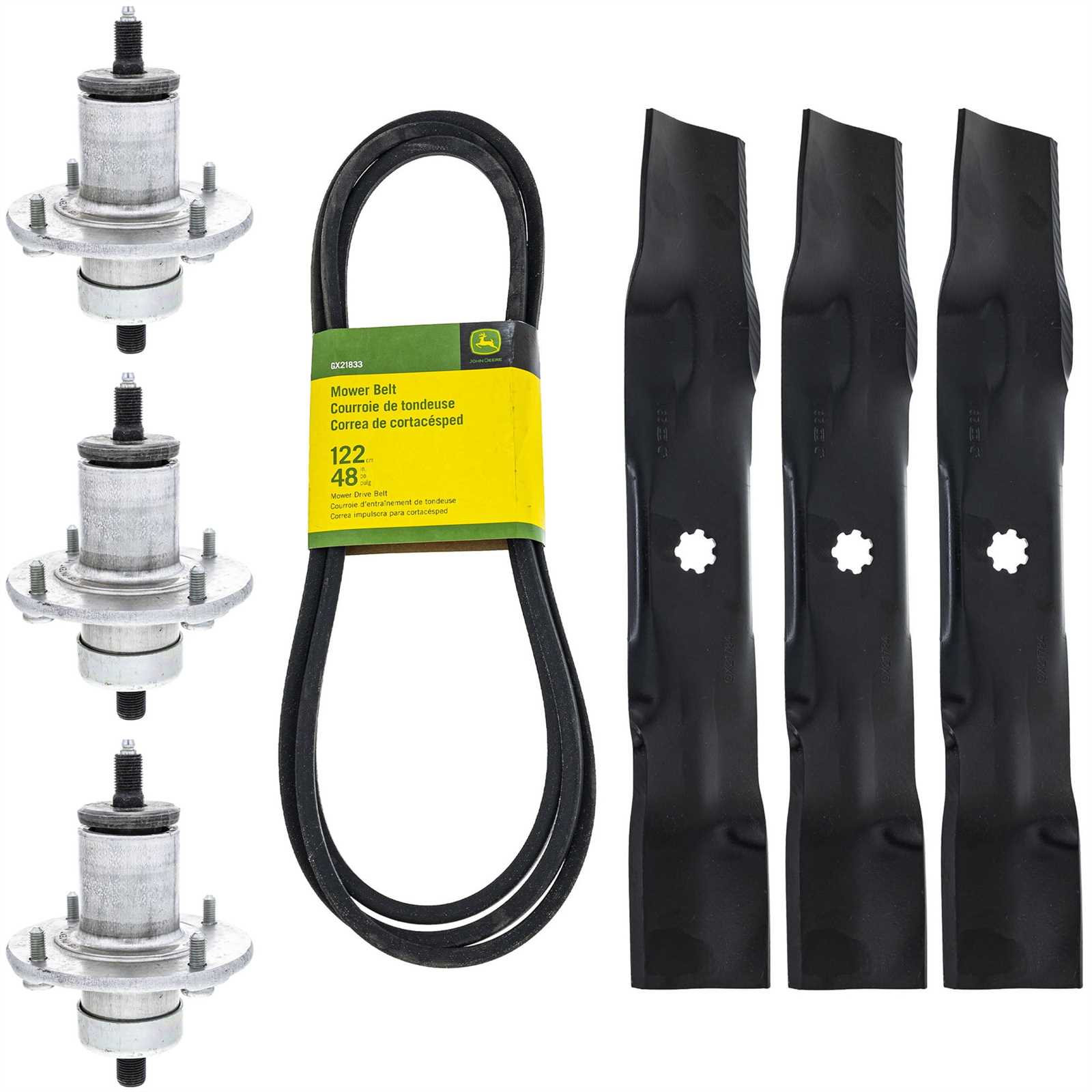
By identifying and addressing these common wear points, operators can enhance the efficiency of their equipment and reduce downtime. Regular maintenance is crucial for ensuring that all components function effectively and reliably.
Choosing the Right Replacement Parts
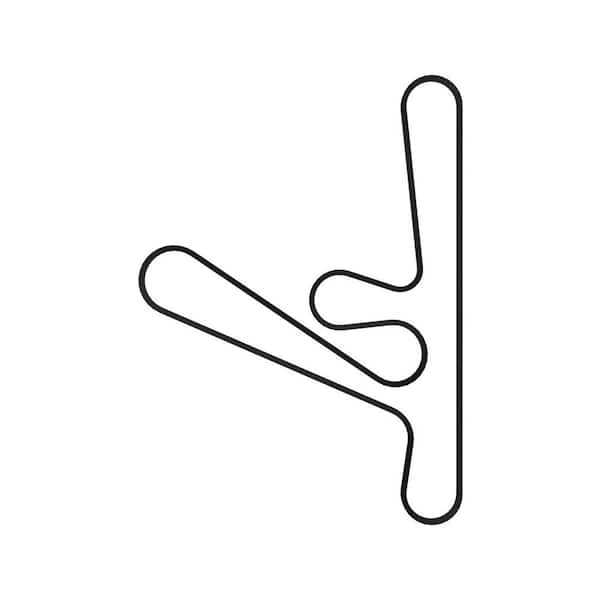
When it comes to maintaining equipment, selecting suitable components is crucial for optimal performance and longevity. The right replacements not only ensure efficiency but also prevent further damage, saving time and resources in the long run. Understanding the specific requirements of your machinery can significantly enhance its functionality.
Compatibility is a primary consideration when sourcing new components. Always verify that the replacements align with your machine’s specifications. This includes dimensions, material quality, and compatibility with existing systems. Using components designed for specific models can enhance overall performance.
In addition to compatibility, quality plays a vital role in your selection. Opt for reputable brands or manufacturers that offer durable and reliable components. Investing in high-quality replacements can prevent frequent breakdowns and enhance the lifespan of your equipment.
Lastly, consider availability. Choose suppliers that provide easy access to the parts you need, as well as a good return policy. This ensures you can quickly replace any faulty components without unnecessary delays, maintaining the efficiency of your machinery.
Lubrication Points for Long-Lasting Performance
Ensuring optimal functionality and longevity of your equipment requires regular attention to lubrication. Proper maintenance not only enhances performance but also reduces wear and tear on components, ultimately saving time and costs associated with repairs. Identifying and addressing key areas that require lubrication is essential for maintaining the efficiency of the machinery.
Key Areas to Lubricate
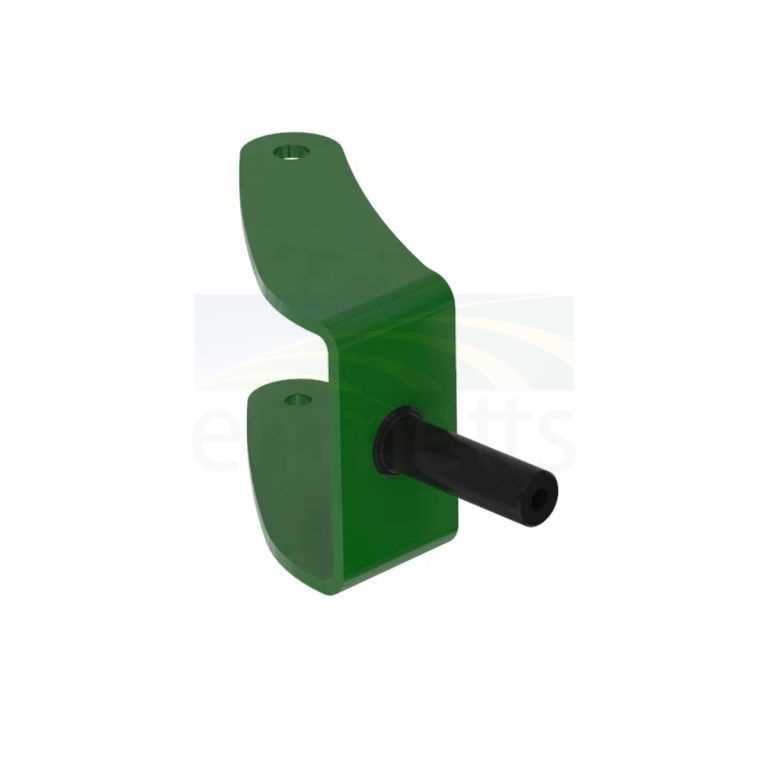
Several critical zones should be prioritized when applying lubricant. Focus on moving parts such as bearings, spindles, and pivot points, as these are susceptible to friction and wear. Regularly check and apply appropriate grease or oil to these areas to maintain smooth operation and prevent premature failure.
Recommended Lubrication Intervals
Adhering to a consistent lubrication schedule is crucial for optimal performance. It’s advisable to lubricate the identified points after every few hours of use or at least once per season. Consult the manufacturer’s guidelines for specific recommendations tailored to your equipment to ensure effective maintenance and extend its lifespan.