Drive belt: Transfers power to the spindle assembly, allowing the blades to rotate effectively
Drive Belt and Tension Adjustment
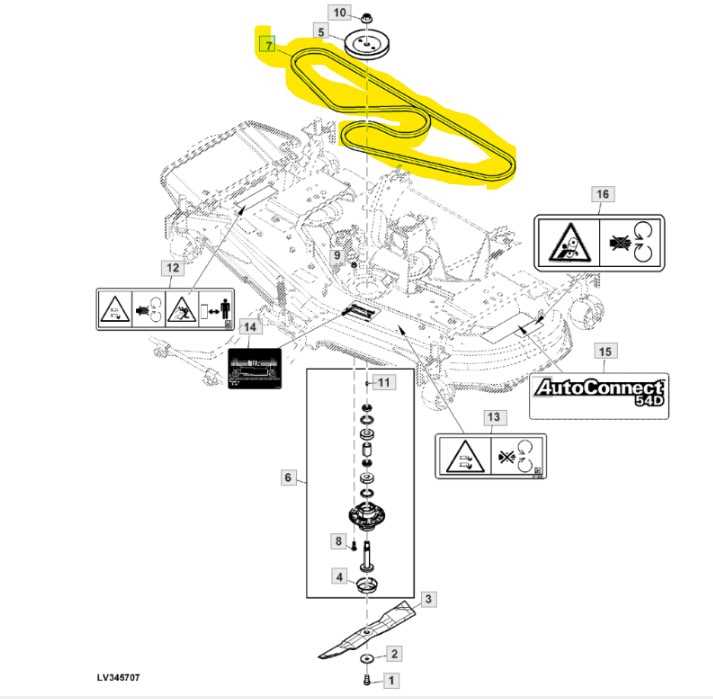
Ensuring proper belt tension is essential for efficient operation and prolonging the lifespan of the equipment. An adequately adjusted belt guarantees optimal performance, reducing wear and preventing slipping during use. Regular checks and timely adjustments help avoid unnecessary strain on mechanical components.
Inspecting the Belt
Before making any adjustments, it’s important to inspect the condition of the belt. Look for signs of wear, such as cracks or fraying, and ensure the belt is properly aligned. If the belt shows significant damage, replacement may be necessary to maintain smooth operation.
Adjusting the Tension
Once the belt is inspected, focus on adjusting its tension. Loosen the adjustment bolts to relieve tension, then gradually retighten while checking the belt’s firmness. The tension should be firm enough to avoid slipping, but not too tight as to cause excessive strain. A proper balance ensures longevity and reliability.
Identifying the Spindle Assembly Parts
The spindle assembly plays a crucial role in ensuring the smooth operation of equipment. By understanding the various components that make up this section, you can maintain and repair your machine efficiently. Recognizing the different elements of this mechanism will help ensure longevity and optimal performance.
Main Components of the Spindle Assembly
At the core of this assembly are several key elements. These typically include a rotating shaft, bearings, and supporting hardware that allow for smooth rotation. These parts work in unison to provide stable and efficient movement, minimizing friction and wear.
Importance of Regular Maintenance
Frequent inspection of this section is essential to avoid damage or failure. Worn-out parts should be replaced promptly to prevent further issues. Regular lubrication and cleaning also help in extending the life of the components, ensuring
Role of the Cutting Height Adjustment Mechanism
The cutting height adjustment mechanism plays a crucial role in ensuring optimal performance and adaptability to various terrain conditions. By controlling the height at which the cutting components operate, users can achieve the desired precision for different grass lengths and types, promoting healthier and more uniform growth.
Key Benefits of Height Adjustment
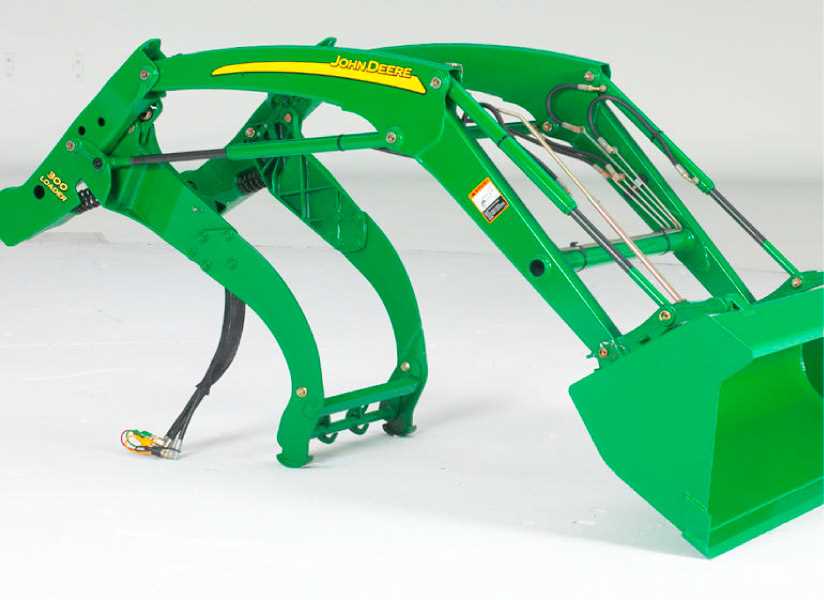
- Enhanced control over cutting precision for various grass types.
- Adaptability to different terrain surfaces, ensuring consistent results.
- Minimized wear and tear on components by avoiding excessive strain during operation.
Operational Adjustments
Adjusting the cutting height is a straightforward process that typically involves a series of calibrated settings. Users can manually fine-tune these settings based on the required grass height, ensuring optimal performance. Regular adjustments allow for flexibility, especially when transitioning between different
Exploring the Anti-Scalp Wheels Function
Understanding the role of anti-scalp wheels is essential for maintaining optimal performance and health of mowing equipment. These components are designed to prevent damage to the turf and ensure a clean cut, promoting a lush, healthy lawn. By examining their function, we can appreciate how they contribute to effective grass management.
Anti-scalp wheels serve several key purposes:
- They help maintain consistent cutting height, preventing the mower from scalping the grass.
- These wheels provide stability, especially when navigating uneven terrain.
- They reduce the likelihood of blade contact with the ground, minimizing wear and tear on the blades.
- Properly functioning wheels can enhance maneuverability, allowing for precise turns and movement.
To ensure these components operate effectively, it is important to consider the following:
- Regularly inspect the wheels for signs of wear or damage.
- Adjust the height of the wheels according to the desired cutting height.
- Ensure the wheels are clean and free from debris that may hinder their function.
- Lubricate moving parts as recommended to maintain smooth operation.
By focusing on the functionality and maintenance of anti-scalp wheels, users can ensure a superior mowing experience and prolong the lifespan of their equipment.
Connection and Disconnection Process of the Deck
Understanding the procedures for attaching and detaching the mowing apparatus is essential for effective operation and maintenance. Properly connecting the implement ensures optimal performance during use, while the correct disconnection process aids in safe storage and transportation.
To attach the mowing apparatus, begin by positioning the vehicle on level ground. Align the implement with the mounting points on the vehicle, ensuring all connection points are accessible. Engage any locking mechanisms to secure the attachment firmly, allowing for a seamless operation.
For disconnection, reverse the attachment steps carefully. Release any locking mechanisms and gently lower the implement to the ground. Once fully disengaged, move the vehicle away, taking care to avoid damage to the implement or vehicle. Regularly inspect the connection points for wear or damage to maintain safe and efficient operation.
Maintenance Tips for Deck Longevity
To ensure the durability and efficiency of your mowing apparatus, regular upkeep is essential. By following a few straightforward practices, you can prolong the lifespan of your equipment and maintain optimal performance. Consistent attention to maintenance not only enhances the functionality but also minimizes the likelihood of unexpected issues.
Regular Cleaning
Keeping your equipment clean is crucial for its longevity. Here are some tips:
- Remove debris, such as grass clippings and dirt, after each use.
- Use a brush or a hose to clean hard-to-reach areas.
- Inspect for any signs of rust or corrosion and address them promptly.
Lubrication and Inspections
Regular lubrication and inspections are vital components of effective maintenance:
- Apply lubricant to moving parts according to the manufacturer’s guidelines.
- Check belts and cables for wear and tear, replacing them as necessary.
- Examine the cutting elements for damage and ensure they are sharpened regularly.
Common Replacement Parts for 72D Deck
Maintaining the efficiency and performance of your lawn equipment often requires the timely replacement of certain components. Identifying the most frequently needed items can help ensure smooth operation and longevity of your machine. Below is a list of essential components commonly replaced during routine maintenance.
One vital component is the cutting blade, which directly influences the quality of the cut. Regular inspection and replacement are crucial to achieving optimal results. Another important item is the spindle assembly, which supports the blade and facilitates its movement. A worn or damaged spindle can lead to performance issues and should be replaced as necessary.
Additionally, belts play a significant role in transferring power from the engine to the cutting mechanism. Over time, these can wear out and may need to be changed to maintain proper function. Furthermore, ensuring that all fasteners and hardware are secure is essential, as loose or damaged bolts can compromise safety and performance.
Lastly, air filters are often overlooked but are essential for maintaining engine efficiency. Regularly replacing these filters can improve airflow and prolong the life of the engine. By keeping these components in check, you can enhance the performance and durability of your lawn equipment.