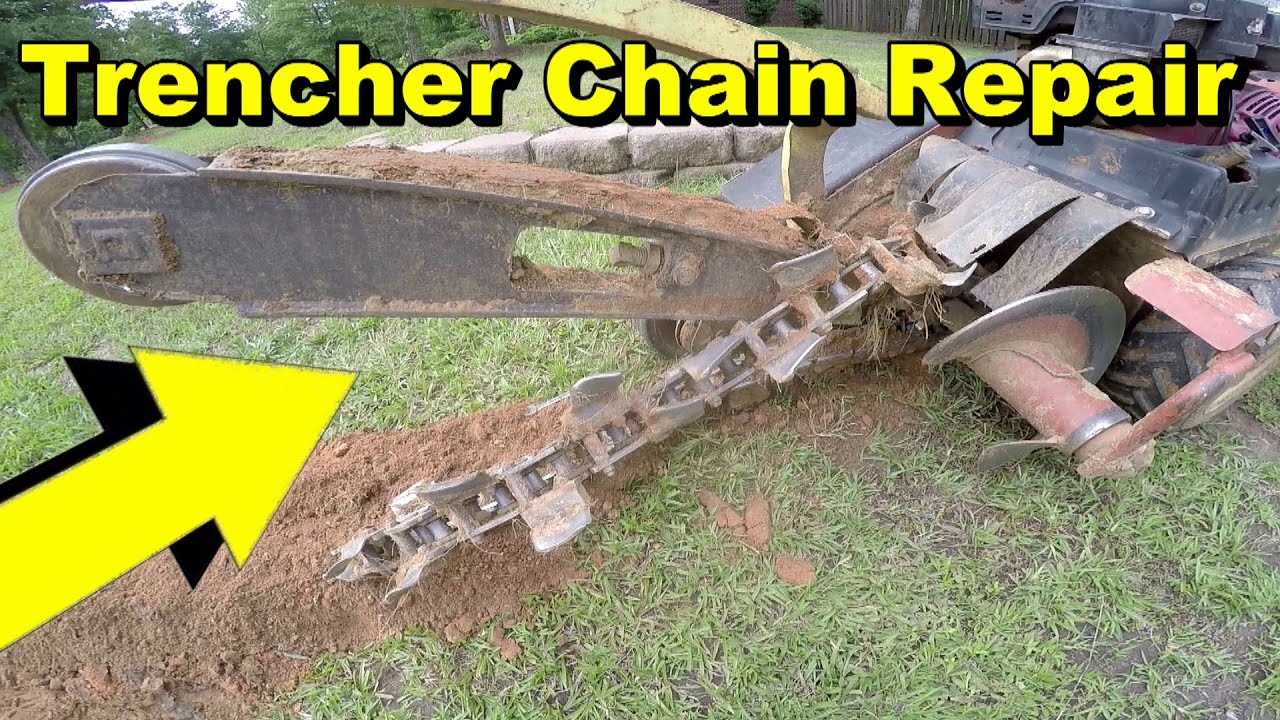
This section provides a comprehensive overview of the essential elements involved in a specific machinery model. By examining the layout and relationships between these various components, users can gain valuable insights into the functionality and maintenance of the equipment. This exploration serves as a guide for those looking to enhance their understanding of the intricate workings behind the machinery.
Through detailed examination, it becomes apparent how each element contributes to the overall performance and reliability of the system. Whether it’s identifying individual roles or recognizing the importance of each connection, this analysis aims to equip users with the knowledge necessary for effective troubleshooting and repairs. By familiarizing oneself with the configuration, operators can ensure optimal operation and longevity of their equipment.
As we delve into the specifics, readers will discover practical tips and recommendations for maintaining efficiency. This guide not only clarifies the interconnections but also highlights potential areas for improvement. Understanding these crucial components is key to achieving a high level of operational success.
Ditch Witch 1230 Parts Overview
Understanding the various components of this reliable trenching equipment is essential for both maintenance and performance optimization. Each element of the machine contributes to its overall efficiency, ensuring smooth operation across a variety of tasks. Familiarity with these key sections helps users troubleshoot issues and extend the lifespan of the equipment.
Key Structural Components
The equipment’s primary framework includes reinforced materials that provide durability and support during heavy-duty use. Its mechanical arm, known for precise movement, operates in tandem with a system of belts and chains, allowing for effective trenching actions. Vital hydraulic systems ensure that pressure is regulated, allowing for efficient power distribution to various parts of the machine.
Operational Mechanisms
Critical to its function is the motor, which delivers consistent energy to drive the mechanical processes. Gearboxes work alongside the motor to convert rotational power into trenching action, while controls allow the operator to adjust speed and direction seamlessly. The cutting blades and tracks, often exposed t
Understanding the Components
Every mechanical system is built from various elements that work together to perform specific functions. To ensure efficient operation, it is crucial to have a solid understanding of these elements, their roles, and how they interact within the system. By breaking down the structure into its core pieces, we can better comprehend how each contributes to the overall functionality and how to maintain or troubleshoot them effectively.
The essential units in this system include the power source, motion transmission mechanisms, control units, and functional attachments. Each of these plays a pivotal role, contributing to the system’s overall efficiency and usability. Proper maintenance and timely replacement of these elements can greatly extend the lifespan of the equipment and ensure safe operation.
Understanding how the motion is generated and transferred through the system is key. Whether through belts, chains, or hydraulic systems, the transmission of power must be smooth and reliable. The interaction between these components determines not only performance but also durability under stress.
Control units, including handles, levers, or electronic interfaces, provide the operato
Identifying Key Features
Understanding the main components and their specific functions is crucial for maintaining and operating mechanical equipment effectively. By identifying critical elements, users can troubleshoot issues, enhance performance, and extend the equipment’s lifespan. This section provides a detailed overview of the most significant structural and functional elements that require attention.
- Engine System: The power source that drives the entire machine, responsible for ensuring smooth operation. Monitoring this system helps prevent breakdowns and maintain efficiency.
- Hydraulic Mechanism: This system controls the movement and positioning of key operational parts. It is essential to maintain hydraulic pressure for optimal functionality.
- Control Console: The interface where the operator manages the machine’s functions. Clear, responsive controls are vital for safe and efficient usage.
- Transmission Components: These parts transfer power from the engine to the functional elements of the machine, ensuring the proper speed and torque distribution.
- Safety Features: Built-in systems that protect both the operator and the machine during use. Regular inspections of these elements can prevent accidents and equipment damage.
Each of these components plays a pivotal role in the overall fun
Maintenance Tips for Longevity
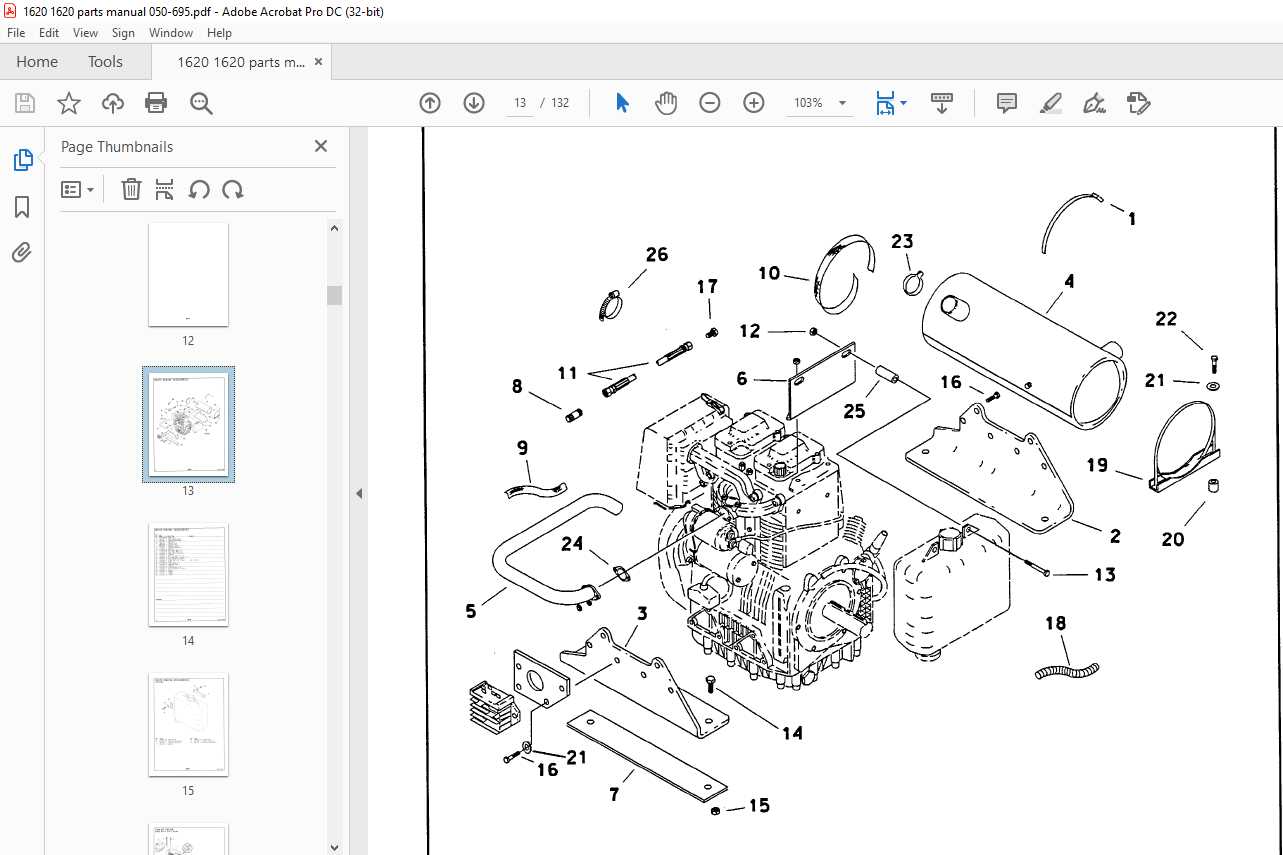
Proper upkeep of equipment is essential for ensuring its long-lasting and efficient performance. Regular maintenance not only prevents unexpected breakdowns but also extends the lifespan of machinery, allowing you to maximize its value and productivity. Below are some crucial tips to help maintain your equipment in optimal condition.
Regular Inspection
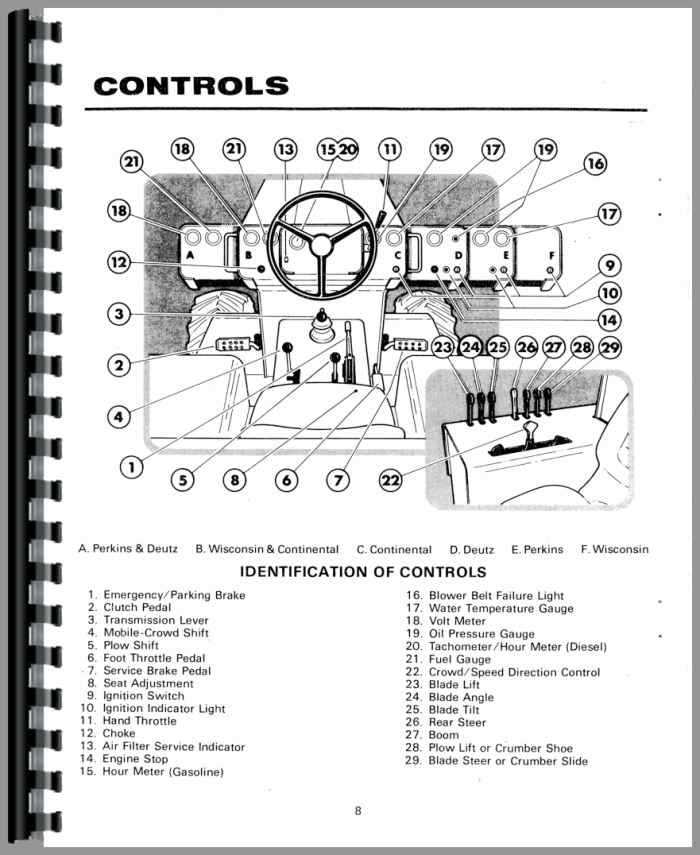
Conducting routine inspections is key to identifying potential issues before they escalate. Make it a habit to check for any signs of wear and tear, such as frayed belts, loose bolts, or fluid leaks. Early detection of these issues can save you from more costly repairs down the road.
- Check moving parts for signs of wear.
- Ensure bolts and fasteners are secure.
- Look for any leaks in fluid systems.
Lubrication and Cleaning
Keeping the equipment well-lubricated ensures smooth operation and reduces friction between moving components. Regular cleaning helps to avoid the buildup of dirt, debris, or grime
Common Issues and Solutions
Operating any heavy machinery can sometimes lead to a variety of challenges, particularly when it comes to mechanical wear and tear, unexpected malfunctions, or operational inefficiencies. In this section, we will explore several frequently encountered issues and provide practical solutions to keep equipment functioning smoothly and efficiently.
Engine Performance Problems
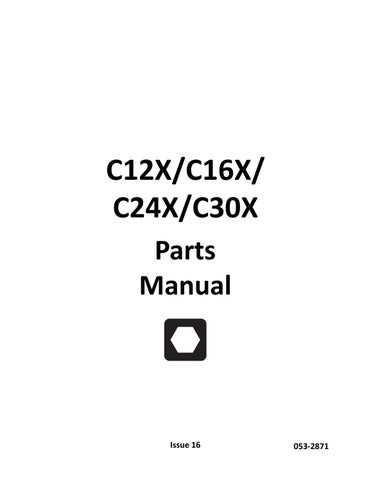
One of the most common challenges faced during operation is a drop in engine efficiency. This may manifest as reduced power output or difficulties starting the machine. Regular maintenance, including checking the fuel filter for blockages and inspecting the spark plug for corrosion, can often resolve these issues.
Issue |
Cause |
Solution |
Engine won’t start |
Faulty spark plug |
Clean or replace the spark plug |
Power loss during use |
Clogged fuel filter |
Replace
Parts Replacement Guide
Maintaining the efficiency and longevity of your equipment requires timely replacement of worn or damaged components. This guide provides step-by-step instructions to help ensure safe and proper maintenance of various elements. By following the outlined steps, users can minimize downtime and prevent further damage.
Preparation and Tools
Before starting the replacement process, ensure you have the necessary tools and safety equipment. Prepare a clean workspace and gather all required materials to avoid interruptions. Standard tools may include wrenches, screwdrivers, pliers, and any specialized instruments specific to the component being replaced.
Replacement Process
For each part, the process may differ slightly, but the general steps remain consistent. Follow these instructions:
Component |
Steps for Replacement |
Hydraulic Hose |
Disconnect power, relieve pressure, remove clamps, replace with new hose
Finding Genuine Parts Suppliers
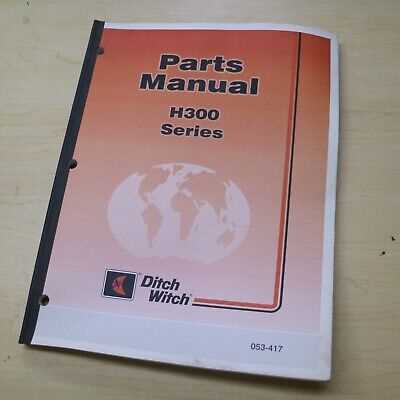
When it comes to maintaining or repairing essential machinery, sourcing authentic components is critical to ensure long-lasting performance and safety. Identifying reliable vendors who offer high-quality equipment can be challenging, especially with the vast number of options available both online and offline.
Research and Verification play a crucial role in this process. It’s essential to verify the legitimacy of a supplier by checking reviews, certifications, and customer feedback. Reputable suppliers often provide detailed information about the origin and quality of the components they sell, ensuring transparency and trust.
One of the most effective methods to find trustworthy vendors is through official distributor networks. These networks work closely with manufacturers and offer guaranteed compatibility. By purchasing from authorized sources, buyers reduce the risk of counterfeit or substandard items.
Another approach involves reaching out to industry-specific forums and professional communities, where experts often share insights on the best suppliers. Recommendations from seasoned professionals can guide buyers toward reputable sellers who have a history of providing genuine goods.
Finally, always look for clear return policies and warranty options, as these indicate that a supplier is confident in the quality of their products. Avoid deals that seem too good to be true, as they often lead to compromised reliability.
Exploring Compatibility with Other Models
When assessing the interchangeability of components across different equipment models, it is crucial to focus on the technical specifications, structural similarities, and mechanical features. Compatibility can offer significant advantages, from cost-efficiency to simplified maintenance, but requires careful evaluation of whether certain parts can function optimally when transferred between models.
Key Factors for Component Compatibility
The core elements to consider include dimensions, material strength, and the operating capacity of the item in question. For instance, similar engine systems or hydraulic mechanisms might share common parts, but variations in size or power output can affect overall performance. Additionally, manufacturer design changes across model lines can introduce subtle differences that may not be immediately visible but can impact long-term functionality.
Advantages and Challenges of Cross-Model Use
Utilizing compatible components across various models often leads to easier sourcing of replacements and reduced downtime. However, the challenge lies in ensuring that even seemingly interchangeable parts meet the performance demands of the specific machine in use. Minor deviations in engineering can result in premature wear or operational inefficiency, so it’s essential to verify full compatibility before making
Assembly Instructions and Best Practices
Proper assembly of complex machinery requires attention to detail and a systematic approach to ensure functionality and safety. In this guide, we will outline key steps and proven practices for effectively assembling equipment. Following these instructions will help avoid potential errors and ensure optimal performance over time.
Step-by-step assembly:
Begin by organizing all components, ensuring each part is clean and free of debris. Lay out the tools necessary for the process, such as wrenches, screwdrivers, and measuring devices. Assemble smaller subunits first, such as attaching brackets or mounting bolts, as this reduces complexity during later stages. Refer to the provided schematics to align parts correctly and ensure secure fitment.
Key considerations:
During assembly, ensure that all fasteners are tightened to the recommended torque levels. Over-tightening can cause stress on materials, while insufficient torque may lead to part failures. Use appropriate lubricants where required to reduce friction and prevent wear over time. Align all moving parts precisely to maintain smooth operation.
Best practices for longevity:
Reg
Visual Reference for Parts Diagram
Understanding the arrangement and function of individual components is crucial when performing repairs or maintenance. A clear visual guide allows users to quickly identify and locate specific elements, making the process more efficient. This section provides an overview of the layout and interactions between different elements, serving as a helpful reference point.
Component Breakdown
The illustration below organizes the key sections into easily recognizable groups. Each part plays a role within the broader system, and recognizing their positions will streamline troubleshooting or replacement tasks.
- Main Assembly: The core structure, typically consisting of foundational and connecting units.
- Drive Mechanism: Contains the power-transmitting elements responsible for movement and operation.
- Support Elements: Smaller components, such as brackets or mounts, that provide stability and alignment.
System Interaction
The interaction between various parts ensures smooth functionality. Observing the way these components fit together can reveal potential points of wear or areas needing attention.
- Power Transfer: From the engine, energy flows through the transmission and ge
Safety Precautions During Repairs
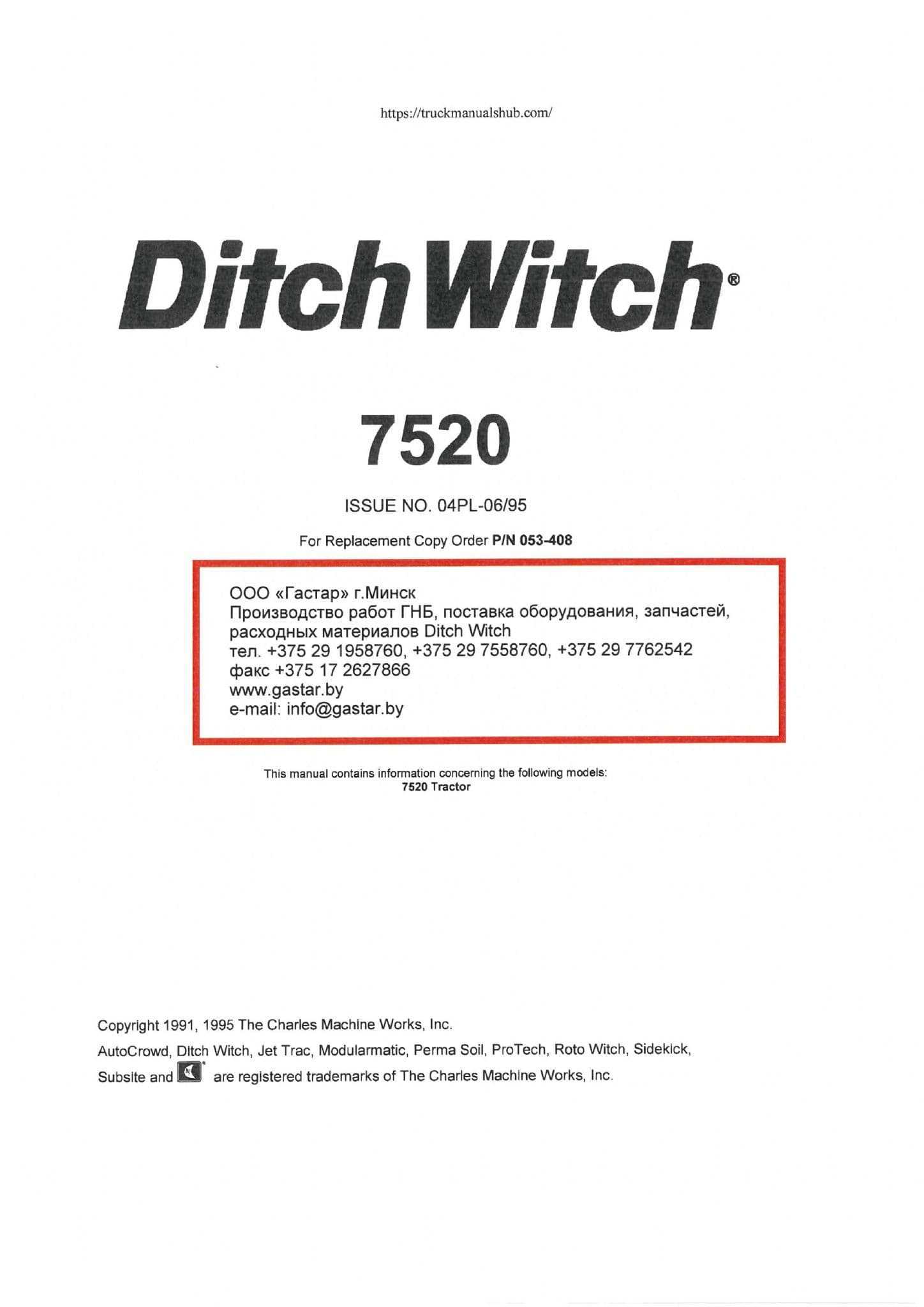
Ensuring safety during maintenance and repair tasks is crucial to prevent accidents and injuries. It is essential to adhere to specific guidelines that help minimize risks associated with operating heavy machinery. Proper preparation and awareness of potential hazards can significantly contribute to a safer working environment.
Personal Protective Equipment (PPE) should always be worn. This includes items such as gloves, safety goggles, and steel-toed boots, which provide a basic level of protection against various injuries. Additionally, ensuring that all clothing fits properly and is free from loose ends can prevent entanglement in moving parts.
Before beginning any work, conduct a thorough inspection of the equipment. Check for any signs of wear or damage that may pose a risk during repairs. This proactive approach not only safeguards the individual but also enhances the overall longevity and efficiency of the machinery.
Another vital aspect is to maintain a clean workspace. Cluttered environments can lead to slips, trips, and falls. Keeping tools organized and ensuring that the area is free of debris can greatly reduce these hazards. Moreover, using appropriate lighting ensures visibility, which is essential for identifying potential risks.
Lastly, always follow the manufacturer’s guidelines and instructions for repairs. Familiarizing oneself with the operational manuals can provide insights into safe practices and highlight any specific precautions that should be taken. Compliance with these recommendations helps ensure a smooth and secure maintenance process.
Resources for Further Learning
For those seeking to enhance their understanding and proficiency in the realm of machinery and equipment maintenance, a variety of resources are available. These materials cater to both novices and seasoned professionals, ensuring that users can deepen their knowledge and improve their skills effectively.
Online Courses and Tutorials
Numerous platforms offer comprehensive online courses and tutorials focused on machinery operation and repair. Websites such as Coursera and Udemy provide courses that cover everything from basic concepts to advanced techniques, enabling learners to study at their own pace. Additionally, many YouTube channels are dedicated to instructional videos that showcase hands-on repairs and maintenance practices.
Technical Manuals and Community Forums
Accessing technical manuals is essential for anyone looking to familiarize themselves with specific equipment. Manufacturers often provide detailed guides that include specifications and maintenance procedures. Furthermore, community forums and online discussion groups serve as valuable platforms for exchanging tips, troubleshooting advice, and sharing personal experiences. Engaging with these communities can significantly enhance one’s learning journey.
|
|