After replacing or cleaning all necessary parts
Understanding the Pressure Gauge System
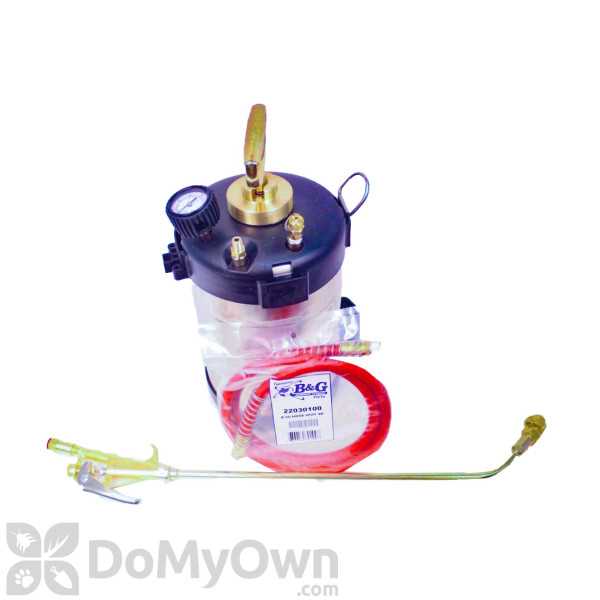
The pressure gauge system plays a critical role in ensuring the efficiency and accuracy of any fluid delivery system. It helps monitor the internal pressure, providing important information about the performance and safety of the device. A well-functioning pressure gauge ensures that the fluid is dispensed at the correct pressure, which is essential for achieving consistent results. Proper calibration and maintenance of the gauge system are key to prolonging the life of the equipment and avoiding potential issues during operation.
At its core, the pressure gauge provides real-time feedback on the internal pressure within the mechanism, allowing operators to make adjustments as needed to maintain optimal functionality. Understanding how to interpret these readings is essential for anyone using the equipment, as incorrect pressure settings can lead to inefficiency or even damage.
Component |
Function |
Pressure Gauge |
Monitors the internal pressure, allowing for adjustments to ensure correct operation. |
Release Valve |
Helps regulate pressure by releasing excess, preventing over-pressurization. |
Pressure Relief Valve |
Automatically releases pressure when it reaches dangerous levels, preventing equipment damage. |
By regularly checking and adjusting the pressure, operators can ensure that the system operates within safe and effective parameters. Over-pressurization can cause leaks or system failure, while under-pressurization might lead to inefficient performance. In either case, the pressure gauge system is an invaluable tool for maintaining the reliability and longevity of the equipment.
Replacing Seals and Gaskets
Maintaining proper sealing in equipment is essential for optimal performance. Over time, seals and gaskets can wear out, leading to leaks, reduced efficiency, or malfunction. Replacing these components is a straightforward yet crucial task to ensure that your equipment operates smoothly and effectively. The replacement process involves identifying the damaged or degraded seals, removing them carefully, and installing new ones in their place.
Step-by-step procedures typically start with disassembling the unit to access the faulty parts. Once removed, inspect the surfaces for any debris or buildup that might affect the new seals. Proper cleaning of these areas is necessary to ensure a tight fit for the new gaskets. Always use high-quality replacements that match the original specifications to prevent future issues.
After the new components are in place, reassemble the unit and test it thoroughly to verify that there are no leaks and that the system is functioning as expected. Regular maintenance of these seals will extend the life of your equipment and help avoid costly repairs down the road.
Maintenance Tips for Optimal Performance
To ensure your equipment operates efficiently and lasts longer, regular upkeep is essential. Proper care will prevent frequent malfunctions and reduce the need for costly repairs. Adopting simple maintenance routines can improve overall functionality, enhance precision, and extend the life of your tool.
Routine Cleaning
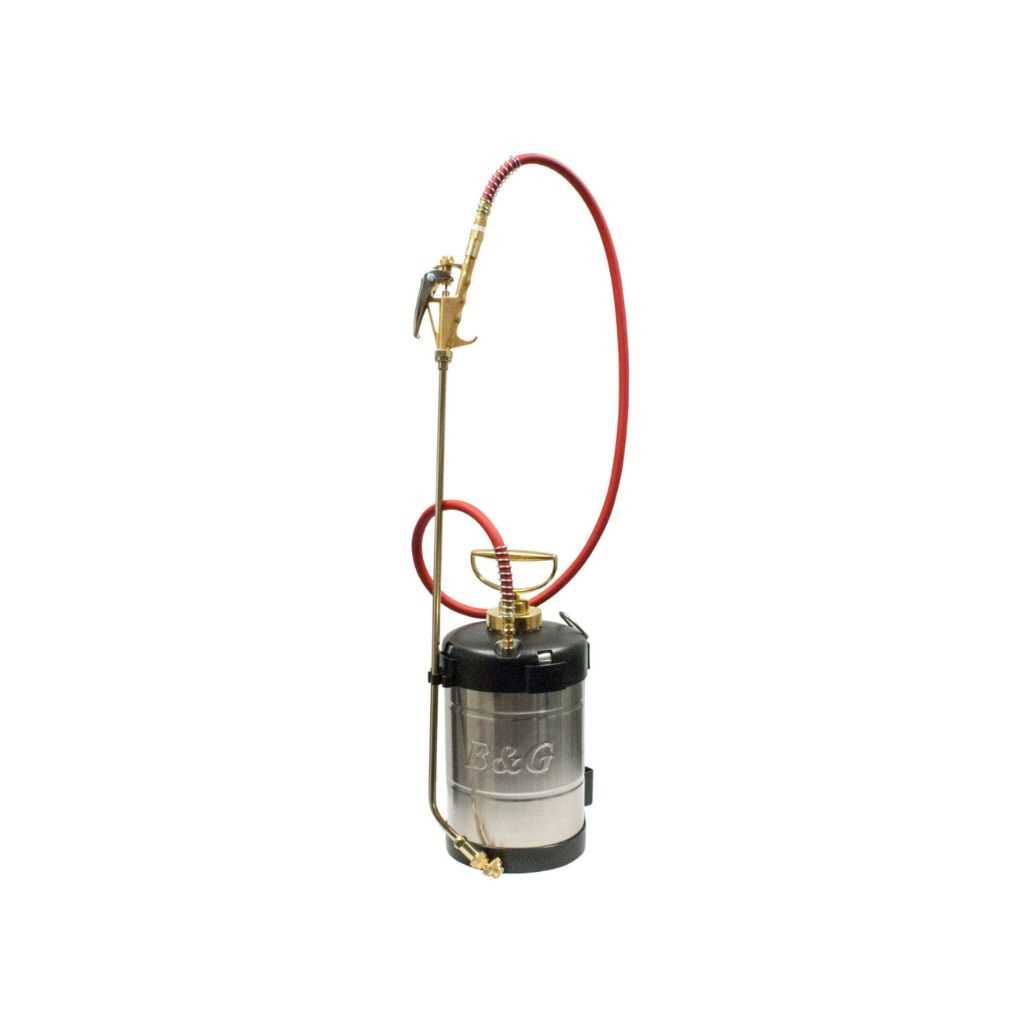
Maintaining cleanliness is vital for the smooth operation of any mechanical tool. After each use, thoroughly clean all components to remove any residue or buildup that may affect performance. Pay special attention to areas prone to clogging or wear, ensuring that all channels are free of obstructions. Use water and a mild detergent, then dry the parts completely to prevent rust or corrosion.
Lubrication and Sealing
Proper lubrication minimizes friction and ensures that all moving elements work seamlessly. Apply an appropriate lubricant to joints, valves, and seals to keep them functioning smoothly. Additionally, inspect all gaskets and seals regularly for signs of wear. Replace any damaged or worn seals to avoid leaks and maintain a tight system.
Regular Inspections should also be part of your routine. Check for cracks, loose fittings, or worn-out components that could compromise performance. Addressing small issues promptly prevents bigger problems from arising.
By implementing these basic maintenance tasks, you’ll keep your tool in top condition, saving time and money on repairs and ensuring peak efficiency for every task.
Common Issues and Their Solutions
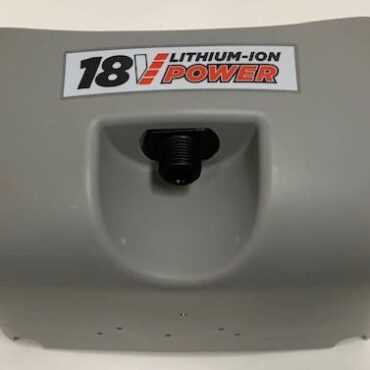
When working with equipment designed for liquid application, several common problems may arise that can hinder its performance. These issues can range from clogging to improper pressure, which can lead to inefficient operation. Addressing these concerns promptly can ensure the longevity of the equipment and maintain its effectiveness in use.
Below is a table listing typical problems, their causes, and suggested solutions to help you troubleshoot and resolve these issues efficiently.
Issue |
Possible Cause |
Solution |
Poor Liquid Flow |
Clogged nozzle or hose |
Clean or replace the nozzle and check the hose for blockages. |
Weak Pressure |
Faulty valve or air leak |
Inspect and tighten all connections. Replace damaged valves if necessary. |
Leaking |
Worn seals or loose connections |
Check seals for wear and replace them. Tighten all connections to prevent leaks. |
Unsteady Spray Pattern |
Debris in the nozzle |
Clean the nozzle thoroughly to remove any blockages that could affect the flow. |
Difficulty in Pumping |
Air trapped in the system |
Bleed the air out of the system according to the manufacturer’s instructions. |
By regularly maintaining and inspecting the equipment, you can prevent these issues from occurring and ensure that it operates smoothly when needed most.
Where to Find Replacement Parts
When it comes to maintaining or fixing your equipment, knowing where to source the necessary components is crucial. Whether you’re dealing with a malfunction or simply performing regular upkeep, identifying reliable suppliers will help ensure smooth operations. There are various avenues you can explore for obtaining high-quality items that meet the specifications of your device.
One of the most convenient options is to check with the original manufacturer. Many companies offer direct sales through their websites, providing the exact components that were designed for your machine. This ensures compatibility and quality assurance. Additionally, authorized dealers and service centers can be valuable resources, as they often stock genuine replacements and can provide expert advice.
For those seeking alternatives, online marketplaces and third-party retailers can offer a wide selection. Websites like Amazon, eBay, and specialized hardware platforms frequently carry aftermarket items that may fit your needs. However, it’s important to review seller ratings and product reviews to avoid counterfeit or substandard replacements.
If you’re looking for more hands-on options, local hardware stores or specialty equipment shops might also carry the parts you need. Visiting these stores allows you to physically inspect the items before purchasing, ensuring their quality. Additionally, many of these stores offer repair services, which can help with installation or troubleshooting.
Benefits of Regular Equipment Maintenance
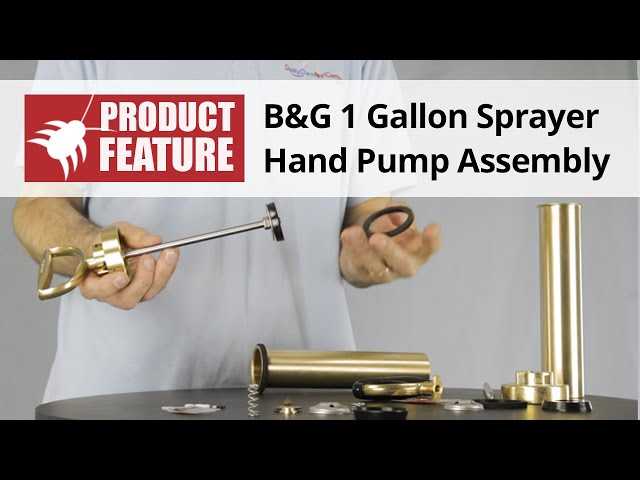
Maintaining your equipment on a regular basis is essential for ensuring its longevity and optimal performance. Regular checks and cleaning help prevent the buildup of dirt, residue, or blockages, which can hinder its effectiveness. Well-maintained devices operate more efficiently and are less likely to malfunction, allowing users to complete their tasks smoothly and without interruption.
Increased Efficiency
Routine upkeep ensures that all components are functioning correctly, reducing the risk of downtime and enhancing the overall efficiency of the device. This can result in faster job completion and improved productivity. A well-maintained system operates at peak capacity, reducing the need for frequent repairs or replacements.
Cost Savings
Investing time in proper upkeep can save you money in the long run. By addressing minor issues before they turn into major problems, you can avoid costly repairs or replacements. Regular maintenance also minimizes the need for professional services, which can add up over time.
Ultimately, keeping your equipment in top shape contributes to its reliable performance, ensuring that it serves its purpose effectively over an extended period.