Magneto: Works by generating electrical pulses as the flywheel rotates, supplying current to the ignition coil
Air Intake and Exhaust System Parts
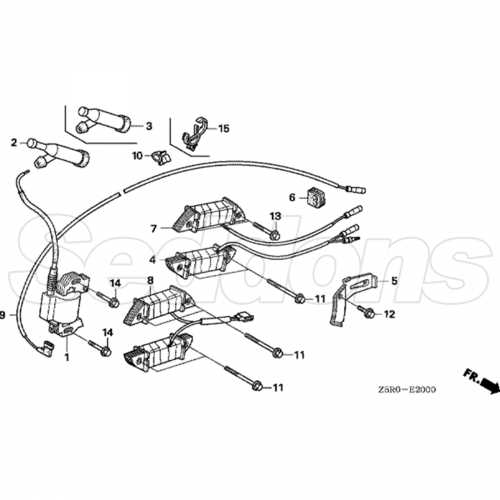
The air intake and exhaust system is crucial for optimizing engine performance and efficiency. This system is responsible for drawing in the necessary air for combustion and expelling exhaust gases produced during the process. Understanding the components involved in this system is essential for maintaining proper functionality and enhancing overall engine output.
Key Components of the Air Intake System
The air intake system includes several important elements designed to ensure a smooth flow of air into the engine. These components typically consist of the air filter, intake manifold, and throttle body. The air filter prevents dirt and debris from entering the engine, while the intake manifold distributes the incoming air to the cylinders. The throttle body controls the amount of air that flows into the engine, playing a significant role in regulating power output.
Exhaust System Components
The exhaust system is equally important, as it removes harmful gases produced during combustion. Key components include the exhaust manifold, catalytic converter, and muffler. The exhaust manifold collects gases from the engine and directs them to the catalytic converter, where harmful substances are neutralized. The muffler then reduces noise levels before the gases are expelled into the atmosphere, ensuring compliance with environmental regulations.
Crankshaft and Piston Assembly
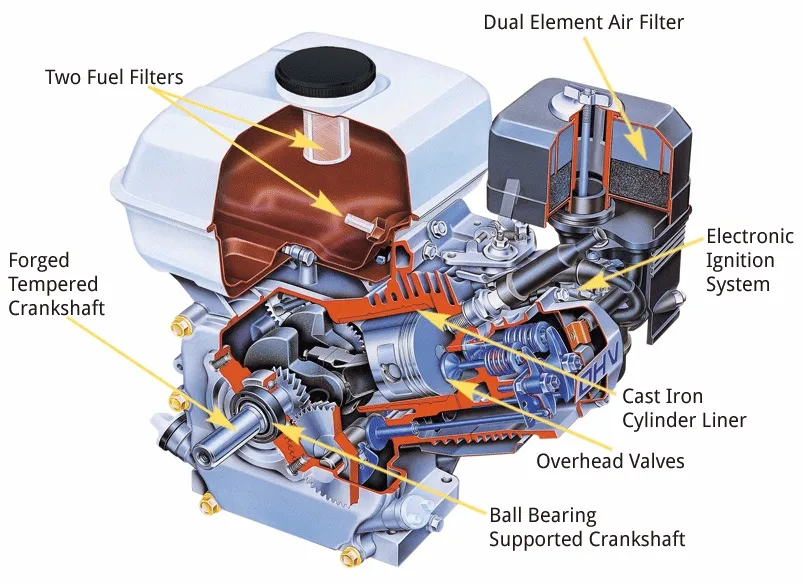
The crankshaft and piston assembly is a crucial component in an engine’s operation, playing a vital role in converting linear motion into rotational motion. This assembly ensures the effective transfer of energy produced during combustion, allowing the engine to generate power efficiently.
The crankshaft is designed to withstand significant forces and torque, transforming the vertical movement of the piston into the rotational energy needed to drive the machine. Made from high-strength materials, it features specific curves and weights to balance the engine’s performance and minimize vibrations.
The piston works in tandem with the crankshaft, moving up and down within the cylinder. Its primary function is to compress the fuel-air mixture and transmit the pressure generated from combustion to the crankshaft. Typically made from lightweight alloys, the piston is engineered to endure high temperatures and pressures while maintaining structural integrity.
Overall, the assembly’s design and materials are critical to the engine’s efficiency and longevity. Regular maintenance and timely replacements of worn components can help maintain optimal performance and prevent costly repairs.
Cylinder Head and Valve Diagram
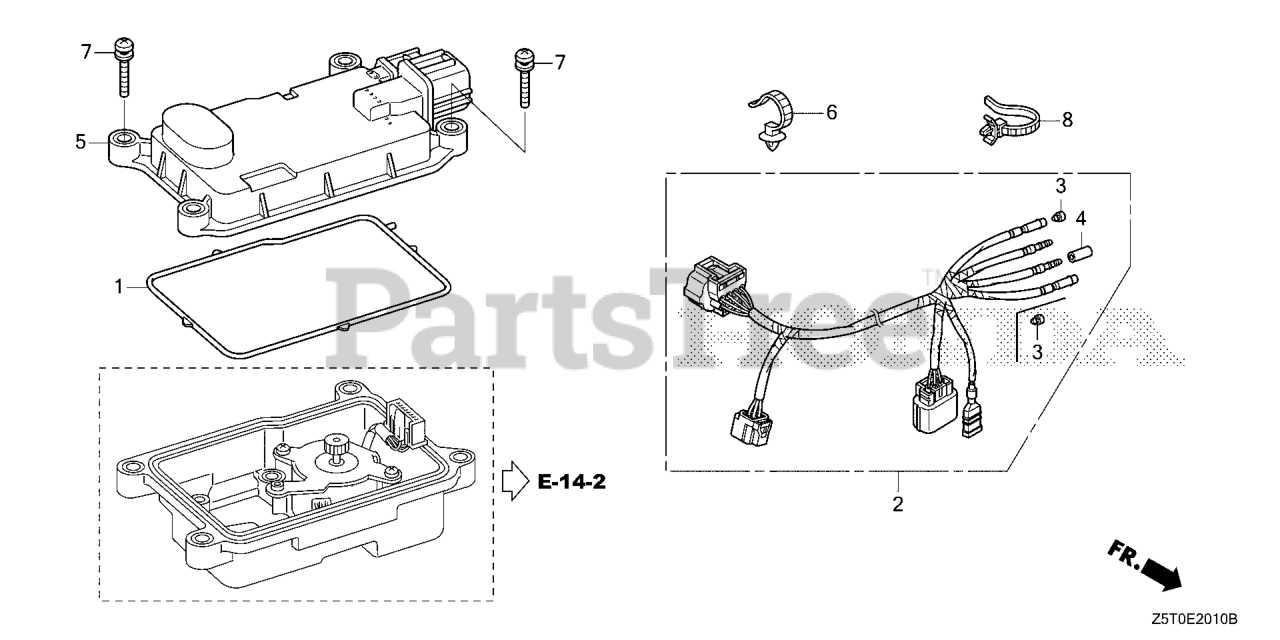
The cylinder head and valve assembly play a crucial role in the functionality of an internal combustion engine. This section delves into the essential components and their arrangements, providing insight into how these elements work together to facilitate efficient air and fuel intake, as well as exhaust expulsion.
Components of the Cylinder Head
The cylinder head is a vital component situated on top of the engine block. It houses the intake and exhaust valves, which control the flow of air and fuel into the combustion chamber. Additionally, it contains passages for coolant and oil, ensuring optimal operating temperatures and lubrication. Understanding the configuration of these elements is essential for diagnosing engine performance issues.
Valve Operation Mechanism
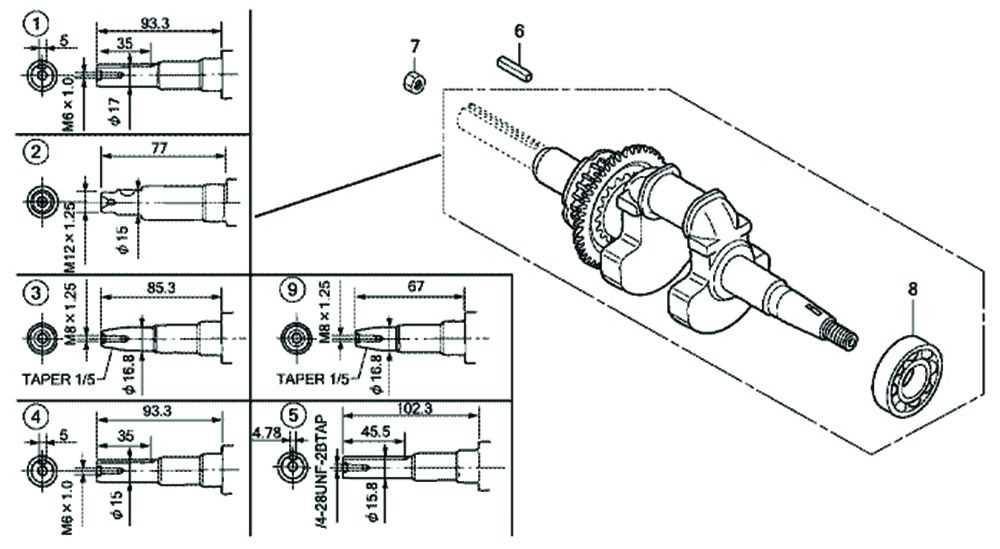
Valves are actuated by a series of components, including camshafts and rocker arms. The precise timing of valve opening and closing is critical for maximizing engine efficiency. When the engine is in operation, the camshaft rotates, pushing the rocker arms to open the intake valves and allowing air and fuel to enter the combustion chamber. Conversely, as the engine cycles, the exhaust valves open to release combustion gases. The synergy between these parts is fundamental to engine performance.
Cooling System Components Explained
The cooling system in an engine plays a crucial role in maintaining optimal operating temperatures, ensuring efficient performance and longevity. Various elements work together to dissipate heat generated during combustion, preventing overheating and potential damage to internal components.
Key components of the cooling system include:
- Radiator: This component transfers heat from the coolant to the air. It consists of a series of tubes and fins that maximize surface area for heat exchange.
- Water Pump: Responsible for circulating coolant throughout the engine and the radiator, ensuring a continuous flow that aids in heat dissipation.
- Thermostat: This device regulates coolant flow based on temperature, allowing the engine to reach its optimal operating temperature quickly.
- Coolant Reservoir: Stores excess coolant and helps maintain the system’s pressure, allowing for expansion and contraction as temperatures fluctuate.
- Hoses: Flexible tubes that transport coolant between the engine, radiator, and other components, facilitating effective circulation and heat management.
Understanding these components is essential for effective maintenance and troubleshooting, contributing to the overall health of the engine and its efficiency in performance.
Understanding the Governor Mechanism
The governor mechanism plays a crucial role in regulating the engine’s speed, ensuring stable performance under varying load conditions. By automatically adjusting the fuel supply or throttle position, it maintains a consistent operational range, enhancing efficiency and reliability. This system is vital for machinery where precise speed control is necessary, preventing fluctuations that could lead to potential damage or inefficiency.
How the Governor Operates

At its core, the governor employs a series of mechanical components that respond to engine speed. When the engine accelerates, the centrifugal force generated by the rotating parts causes adjustments that control fuel delivery. This response helps to balance the engine’s power output with the required workload, ensuring optimal performance without excessive strain.
Importance of Calibration

Proper calibration of the governor is essential for optimal operation. If misconfigured, it can lead to issues such as overspeed conditions or insufficient power during demanding tasks. Regular maintenance and adjustments help maintain the accuracy of the governor, contributing to the overall longevity and functionality of the engine.
Carburetor Parts Identification
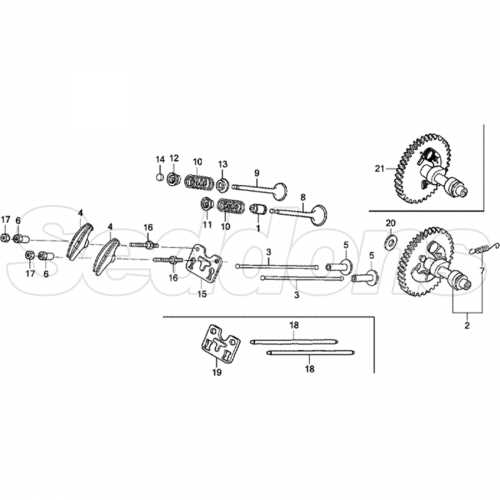
Understanding the components of a fuel delivery system is essential for efficient engine performance. Each element plays a significant role in regulating the air-fuel mixture, ensuring optimal combustion and power output. Recognizing these components allows for better maintenance and troubleshooting, leading to enhanced engine longevity.
Below is a table outlining the key elements of the fuel delivery mechanism, including their functions and descriptions:
Component |
Function |
Description |
Float |
Regulates fuel level |
A buoyant device that rises and falls with the fuel level, controlling the inlet valve. |
Jet |
Delivers fuel |
A precision opening that meters the amount of fuel flowing into the airstream. |
Throttle Valve |
Controls airflow |
A valve that adjusts the amount of air entering the carburetor, affecting engine power. |
Choke |
Enriches mixture |
A mechanism that restricts airflow during cold starts, increasing the fuel-to-air ratio. |
Fuel Bowl |
Holds fuel |
A reservoir that stores fuel before it is drawn into the engine. |
Gx390 Honda Electrical System Diagram

The electrical layout of a small engine is crucial for its efficient operation and reliability. This section provides an overview of the key components and their interconnections within the system. Understanding this network is essential for troubleshooting issues and ensuring that the engine functions properly.
The electrical assembly includes vital parts such as the ignition coil, spark plug, and battery, which work together to generate and manage power. The wiring harness connects these elements, allowing signals to flow seamlessly. A well-maintained electrical system ensures optimal performance and can prevent potential malfunctions.
In summary, familiarity with the electrical configuration enhances the ability to diagnose problems and maintain the engine’s performance. Regular checks and proper maintenance of each component contribute significantly to the longevity and efficiency of the overall system.