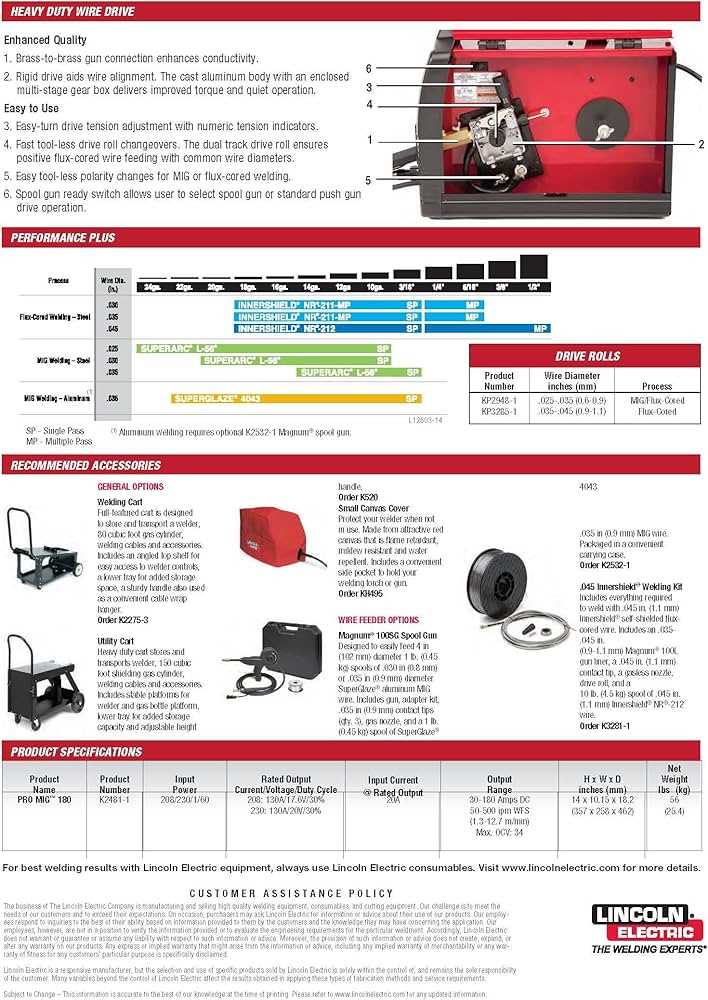
In any machinery, a clear comprehension of its individual elements is essential for effective maintenance and repair. This section delves into the intricate layout of a specific model, highlighting how each component interacts within the overall system. By grasping the relationships between the various pieces, users can better troubleshoot issues and enhance performance.
Familiarizing oneself with the configuration of the components can significantly simplify the process of identifying parts that may require replacement or adjustment. Each segment plays a vital role in the functionality of the machine, and recognizing their placements can lead to a more efficient workflow.
Moreover, an organized visual representation aids in developing a deeper understanding of how the assembly operates as a whole. By studying the arrangement, users are empowered to make informed decisions regarding upgrades and modifications, ensuring optimal performance for years to come.
Understanding the Lincoln 180C Parts Diagram
Gaining insight into the layout of components in a welding machine is essential for efficient operation and maintenance. This guide aims to provide clarity on the various elements involved, helping users comprehend how each piece interacts within the system. Understanding these components enhances troubleshooting abilities and ensures optimal performance.
Familiarizing yourself with the schematic allows for a deeper appreciation of the machine’s functionality. It highlights critical features and identifies potential wear points that require attention. By recognizing the role of each component, operators can better diagnose issues and perform necessary repairs.
Ultimately, a comprehensive grasp of the arrangement and function of the individual elements fosters confidence and competence in handling the equipment.
Overview of Lincoln 180C Welding Machine
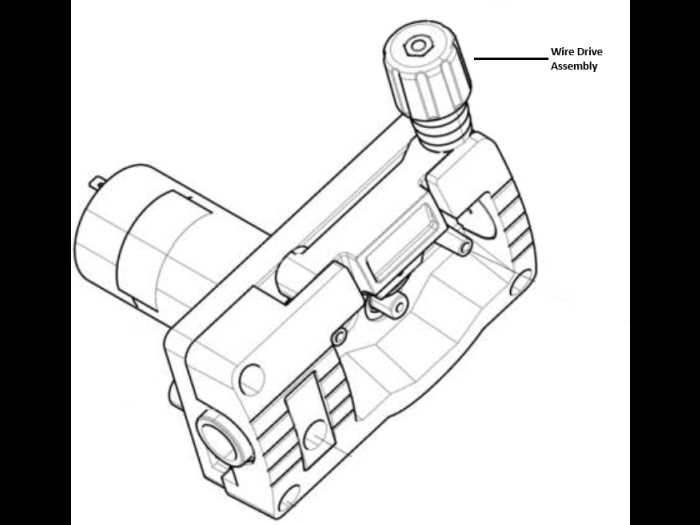
This section provides a comprehensive look at a versatile welding apparatus designed for various applications. Renowned for its reliability, this equipment is favored by both professionals and enthusiasts alike. Its robust features make it suitable for a range of tasks, ensuring optimal performance in diverse environments.
Key Features
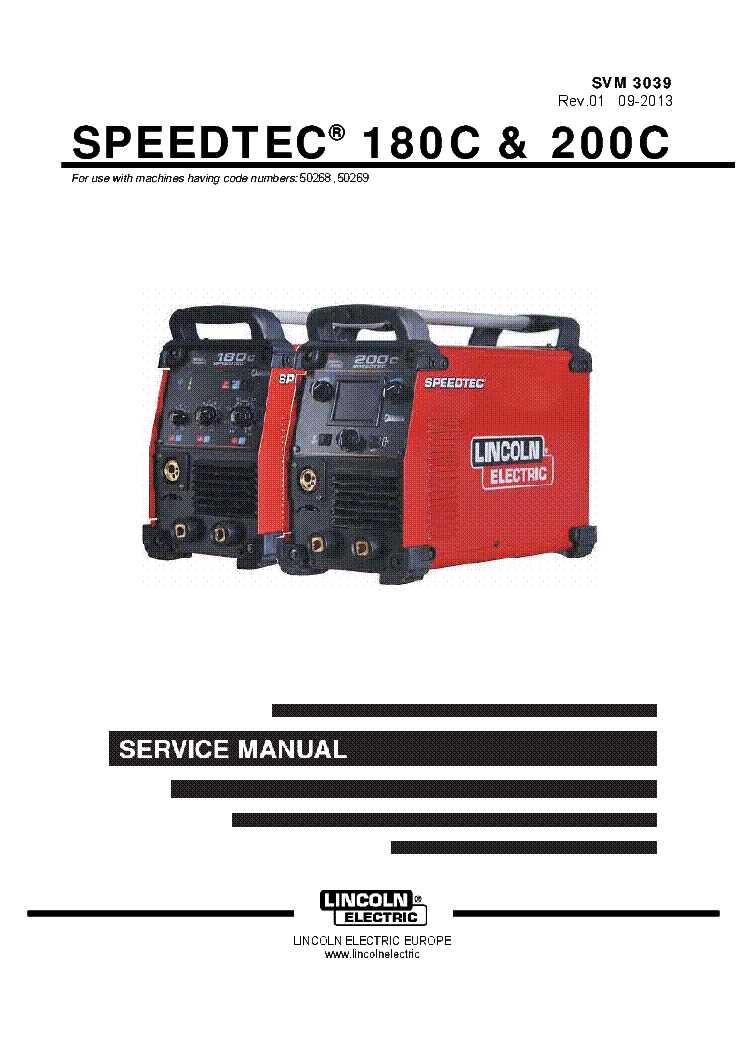
The welding machine boasts a user-friendly interface, allowing for easy adjustments to voltage and amperage settings. This flexibility caters to different welding techniques, whether for thin sheets or thicker materials. Additionally, the lightweight design enhances portability, making it ideal for job sites and workshops.
Applications
Commonly employed in construction and fabrication, this welding tool excels in tasks such as metal joining, repair work, and fabrication projects. Its adaptability makes it a valuable asset in various sectors, from automotive to industrial manufacturing.
Exploring the Main Components
This section delves into the essential elements that make up the equipment, providing insights into their functions and interrelations. Understanding these components is crucial for effective maintenance and optimal performance.
Component |
Description |
Engine Assembly |
The powerhouse of the machine, responsible for generating the necessary force for operation. |
Hydraulic System |
This system facilitates the movement of various parts through fluid power, enhancing operational efficiency. |
Control Panel |
The interface for the operator, providing essential controls and indicators for monitoring performance. |
Chassis |
The structural framework that supports all components, ensuring stability and durability during use. |
Cooling System |
This system regulates temperature to prevent overheating, thereby prolonging the life of the machinery. |
Identifying Electrical Connections
Understanding the various electrical connections is crucial for ensuring smooth operation and troubleshooting of welding equipment. Each wire and connector plays a specific role in transmitting power or signals, contributing to the overall performance. Familiarizing yourself with these elements will help in recognizing potential issues and maintaining optimal functionality.
Examining Power Supply Details
In any welding equipment, understanding the power source is essential for optimal performance and longevity. This section explores the vital components that make up the power system, ensuring a stable and reliable energy flow during operation. The following list highlights key areas to focus on when analyzing the power system of a welding unit.
- Input Voltage: The voltage required for the machine to function correctly, ensuring compatibility with available electrical outlets.
- Transformer: A core component responsible for adjusting the incoming voltage to the appropriate level needed for efficient welding processes.
- Rectifier: Converts alternating current (AC) to direct current (DC), which is often required for certain types of welding operations
Analyzing Control Panel Layout
The arrangement of the control interface plays a crucial role in ensuring efficient operation and user interaction. By understanding the layout, users can easily navigate the available functions and make precise adjustments during use. The positioning of the various controls allows for intuitive access, minimizing the need for unnecessary movements and enhancing workflow.
Key elements such as switches, dials, and indicators are typically organized in a manner that supports logical and ergonomic use. This structured design helps operators to quickly identify and engage the necessary controls, contributing to smoother operation and reduced downtime. Familiarity with this layout enhances both productivity and safety.
Detailing Wire Feeder Mechanism
The wire feeder mechanism plays a crucial role in ensuring smooth and consistent delivery of welding wire. This section focuses on the essential components involved in its operation, outlining how each part contributes to efficient performance. Understanding the intricacies of this system is important for maintaining high-quality results and avoiding potential issues during the welding process.
Core Elements of the Feeder
At the heart of the feeder mechanism are several key elements working in harmony. The drive rollers ensure consistent wire movement, gripping the wire securely and advancing it toward the welding torch. Proper tension and alignment are critical, as they prevent wire slipping or misfeeding, which could lead to interruptions or poor welds.
Adjustment and Maintenance
Inspecting Torch Assembly
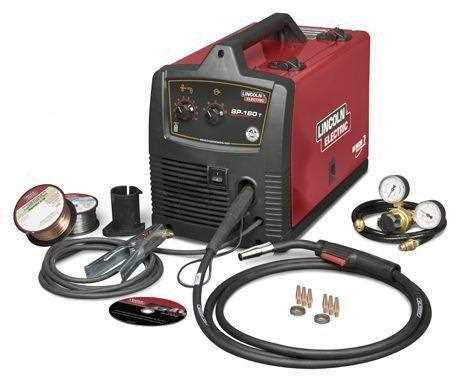
The torch assembly is a critical component that requires regular evaluation to ensure optimal performance and safety. By inspecting the various elements of the assembly, users can identify potential issues early, preventing more significant problems during operation.
Before inspection, it is essential to disconnect the power source to avoid any risk of injury. Begin by checking for wear and tear on the exterior components, such as the handle and cable. Look for any visible damage, cracks, or frayed sections that could lead to malfunction.
Next, examine the nozzle and tip for signs of overheating or buildup.
Understanding Gas Regulator Setup
Setting up a gas regulator properly is crucial for ensuring a smooth and efficient welding process. This component plays a key role in controlling the flow of gas, which is essential for maintaining a stable welding arc and achieving high-quality results. A well-adjusted regulator guarantees both safety and precision during operation.
First, ensure that all connections are secure to avoid leaks, which could compromise performance or even pose safety risks. It’s
Reviewing Cooling System Components
The cooling system is a crucial part of any machinery, helping to regulate temperature and prevent overheating during operation. Understanding its main components ensures efficient performance and longevity. Below, we’ll outline the key elements that contribute to maintaining an optimal thermal balance.
- Radiator: This component plays a significant role in dissip
Comparing Parts Variants and Options
When it comes to selecting components, there are often multiple variations available, each offering distinct features and performance levels. Understanding the differences between these options can help in making informed choices that align with specific needs and applications. By comparing the available alternatives, you can identify which version best suits your requirements, whether you’re prioritizing durability, efficiency, or cost-effectiveness.
Different versions of the same
Practical Maintenance Tips and FAQs
Regular upkeep is essential for ensuring that your equipment operates efficiently and has a long service life. This section provides practical advice on routine care, addressing common concerns and offering troubleshooting suggestions to help you maintain optimal performance.
Routine Maintenance Tips
- Inspect the machine frequently for any signs of wear or damage, especially in areas prone to high stress or frequent use.
- Clean the equipment thoroughly after each use to remove dirt, dust, or debris that may impact functionality.
- Lubricate moving parts according to the manufacturer’s guidelines t