Cooling System
Understanding the Stator and Its Function
The stator plays a crucial role in generating the necessary magnetic field for the operation of rotating machines. Its design ensures that electrical energy can be efficiently converted into mechanical force. To fully grasp its significance, it is essential to explore its construction and how it supports overall performance.
- Core Structure: The stator consists of a laminated core, designed to minimize energy losses and improve efficiency.
- Windings: Coils of wire are wound around the core, which are responsible for creating the magnetic field when current flows through them.
- Housing: The entire stator assembly is enclosed within a protective casing, ensuring stability and heat dissipation during operation.
The careful design and arrangement of the stator components directly impact the system’s performance, making it a fundamental element in the operation of various machines.
The Role of the Rotor in Motor Operation
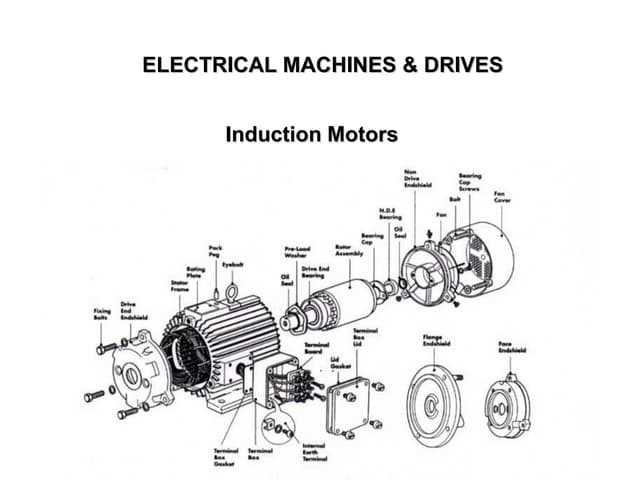
The rotor is a critical component in transforming electrical energy into mechanical motion. This part works in conjunction with other key elements to generate rotational force, which powers various systems and machinery. Its functionality relies on the movement of magnetic fields that interact with the rotor’s structure, causing it to turn.
As the rotor spins, it creates a mechanical output, which is essential for the functioning of the entire system. Its design, materials, and structure directly affect performance, efficiency, and durability. Proper operation ensures smooth and continuous rotation, minimizing wear and tear while maximizing output.
How Windings Affect Motor Performance
The arrangement and characteristics of the wire coils play a crucial role in determining the efficiency and effectiveness of the machinery. Variations in the design, such as the number of turns and the materials used, significantly influence how energy is converted into mechanical power.
Coils with a higher number of turns generally produce a stronger magnetic field, which can lead to improved torque and performance. However, this can also result in increased resistance, potentially reducing efficiency. Balancing these factors is essential for optimizing overall functionality.
Additionally, the type of winding configuration can affect how the system responds to changes in load. For example, certain layouts may enhance performance under specific conditions while compromising efficiency under others. Understanding these dynamics is vital for designing more effective systems that meet varying operational demands.
Moreover, the thermal characteristics of the winding materials influence the durability and longevity of the equipment. Materials that dissipate heat effectively can help maintain optimal operating temperatures, thereby enhancing performance and reducing the risk of failure. Choosing the right materials is therefore critical in ensuring reliable operation over time.
Exploring the Motor Housing Structure
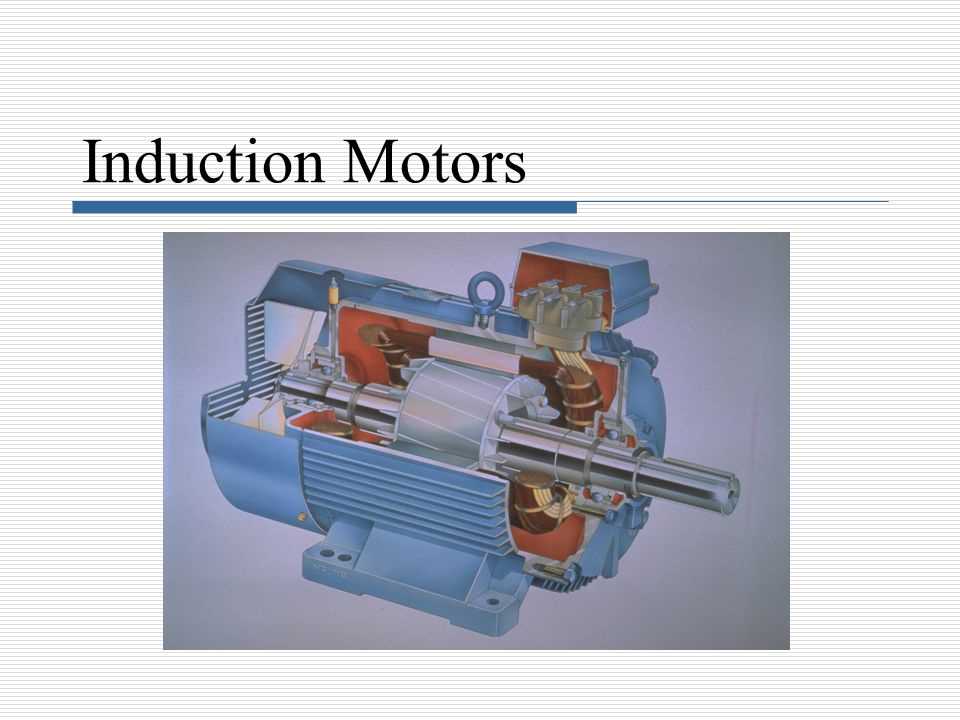
The outer casing of an electric machine plays a crucial role in its overall functionality and durability. This structure not only protects the internal components from external elements but also facilitates effective heat dissipation and vibration control. Understanding its design and materials is essential for ensuring optimal performance.
The housing typically consists of robust materials that withstand various environmental conditions. Its shape is engineered to maximize efficiency while minimizing energy loss. Various elements work in harmony within this framework to create a reliable system.
Component |
Description |
Shell |
The outermost layer that shields the internal parts from physical damage. |
End Bells |
Caps that secure the ends of the housing, providing support and stability. |
Cooling Fins |
Extended surfaces designed to enhance airflow and improve thermal management. |
Mounting Brackets |
Structures that facilitate secure attachment to other components or surfaces. |
Bearings and Their Importance in Motors
Bearings play a crucial role in the operation of rotating machinery, providing support and enabling smooth motion. Their primary function is to reduce friction between moving parts, which enhances efficiency and extends the lifespan of the equipment.
There are several key aspects to consider regarding bearings:
- Friction Reduction: By minimizing contact between surfaces, bearings significantly lower the energy loss that occurs due to friction.
- Alignment Maintenance: Bearings help maintain the proper alignment of shafts and other rotating components, which is vital for optimal performance.
- Load Distribution: They distribute loads evenly across surfaces, preventing wear and tear and ensuring longevity.
Choosing the right type of bearing is essential for achieving optimal performance. Common types include:
- Ball Bearings
- Cylindrical Roller Bearings
- Tapered Roller Bearings
- Spherical Bearings
Proper maintenance of these components is equally important. Regular inspections can prevent potential failures and maintain the efficiency of the machinery:
- Check for signs of wear or damage.
- Ensure proper lubrication to reduce friction.
- Monitor operating temperatures to avoid overheating.
In summary, bearings are fundamental to the reliability and efficiency of rotating machinery. Their proper selection and maintenance can lead to improved performance and longer operational life.
Cooling Systems for Electric Motors
Efficient temperature regulation is crucial for the longevity and performance of electric machines. Proper cooling mechanisms ensure that excessive heat generated during operation is effectively dissipated, maintaining optimal functioning conditions. Various systems can be employed to achieve this, each suited to specific applications and requirements.
Types of Cooling Systems
There are several methods to manage heat in electrical machinery. Air cooling is one of the most common techniques, utilizing ambient air to absorb heat from the equipment. This method is often used in smaller applications where heat generation is minimal. Liquid cooling, on the other hand, circulates a coolant through the system to absorb and transport heat away. This approach is typically found in larger, high-power applications where heat management is critical.
Benefits of Effective Cooling
Implementing robust cooling solutions not only enhances the performance of electric devices but also extends their operational lifespan. By reducing thermal stress, these systems prevent overheating and related failures, ensuring consistent reliability. Furthermore, efficient cooling can lead to energy savings, as devices can operate at optimal temperatures without the need for excessive power input.
Insulation Materials in Motor Construction
The choice of insulating substances plays a critical role in the efficiency and durability of electrical machines. These materials provide essential protection against electrical leakage and thermal stress, ensuring reliable operation under varying conditions. Selecting the appropriate insulation is vital for enhancing performance and extending the lifespan of the machinery.
Types of Insulating Materials
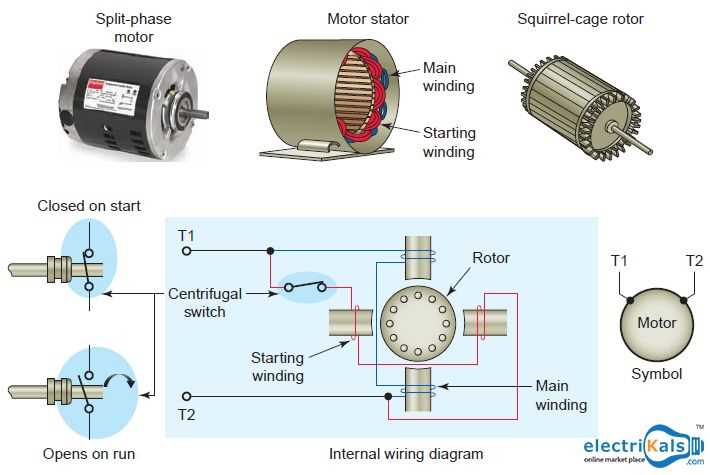
Various insulating materials are utilized in the construction of electrical devices, each offering unique properties suited for specific applications. The most common options include:
Material Type |
Properties |
Applications |
Polyimide |
High thermal stability, excellent chemical resistance |
Used in high-temperature applications |
Enameled Wire |
Good electrical insulation, flexibility |
Commonly used in winding |
Fiberglass |
Good thermal insulation, mechanical strength |
Used for structural reinforcement |
Epoxy Resin |
Excellent adhesion, moisture resistance |
Utilized for encapsulation and coating |
Importance of Quality Insulation
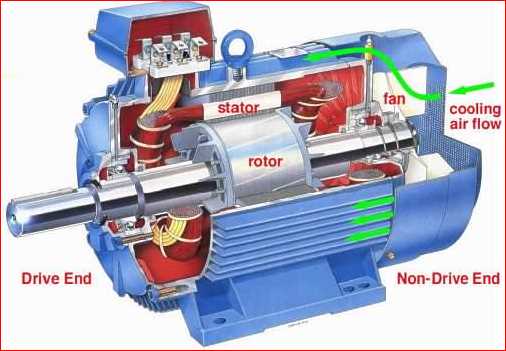
High-quality insulating materials are crucial for minimizing energy loss and enhancing overall efficiency. They help prevent breakdowns due to overheating or electrical failures, ultimately contributing to the machine’s performance and reliability. Investing in superior insulation not only ensures compliance with safety standards but also fosters a sustainable approach to energy consumption.
Electrical Connections and Motor Terminals
The proper configuration of electrical connections is essential for the efficient functioning of the machinery. These connections ensure that power is transmitted effectively, allowing for optimal performance. Understanding the layout and specifications of the terminals is crucial for anyone involved in installation or maintenance.
Typically, the terminals are labeled to indicate their respective functions, such as power supply, grounding, and control signals. Identifying these connections correctly can prevent potential hazards and enhance operational reliability. It is also important to adhere to the manufacturer’s guidelines when making these connections.
In addition to the physical layout, the quality of the electrical components used in the connections can significantly impact performance. Using high-quality wires and connectors minimizes the risk of failures and ensures a stable electrical flow. Regular inspections and maintenance of these connections are recommended to maintain efficiency and safety.
Common Faults in Motor Parts
Understanding the frequent issues that can arise within the various components of electrical machines is crucial for effective maintenance and troubleshooting. These faults can significantly affect the overall performance, efficiency, and lifespan of the equipment.
- Worn Bearings: Over time, bearings may degrade due to friction, leading to increased noise and vibration.
- Insulation Failure: Deterioration of insulation can result in short circuits, overheating, and ultimately equipment failure.
- Overheating: Excessive heat can be caused by overloading or poor ventilation, damaging internal components.
- Imbalanced Load: Uneven distribution of weight can lead to uneven wear and operational inefficiencies.
- Loose Connections: Corroded or improperly tightened connections can lead to electrical faults and reduced performance.
Regular inspection and timely intervention can help mitigate these issues, ensuring the longevity and reliability of the machinery.