Transfers motion and adjusts the speed of v
How the Blades Influence Juicing Efficiency
The design and sharpness of the cutting components play a crucial role in determining how effectively fruits and vegetables are processed during juicing. By breaking down produce into smaller pieces, the blades maximize the extraction of liquid, reducing waste and improving the overall yield. The speed and precision of these components can directly affect how much juice is obtained from each ingredient, making them vital for efficient performance.
- Material and Sharpness: High-quality, sharp edges ensure smooth cutting, reducing the time and effort needed to juice various fruits and vegetables.
- Cutting Motion: The way the components rotate or move influences how efficiently the produce is processed. Consistent and precise movements help in quicker extraction.
- Produce Compatibility: Well-designed blades handle a range of textures, from soft fruits to tougher vegetables, ensuring efficient juicing regardless of the ingredient.
- Maintenance Impact: Properly maintained components not only last longer but also continue to deliver high juicing efficiency over time.
Overall, the efficiency of juicing largely depends
Understanding the Role of the Motor Assembly
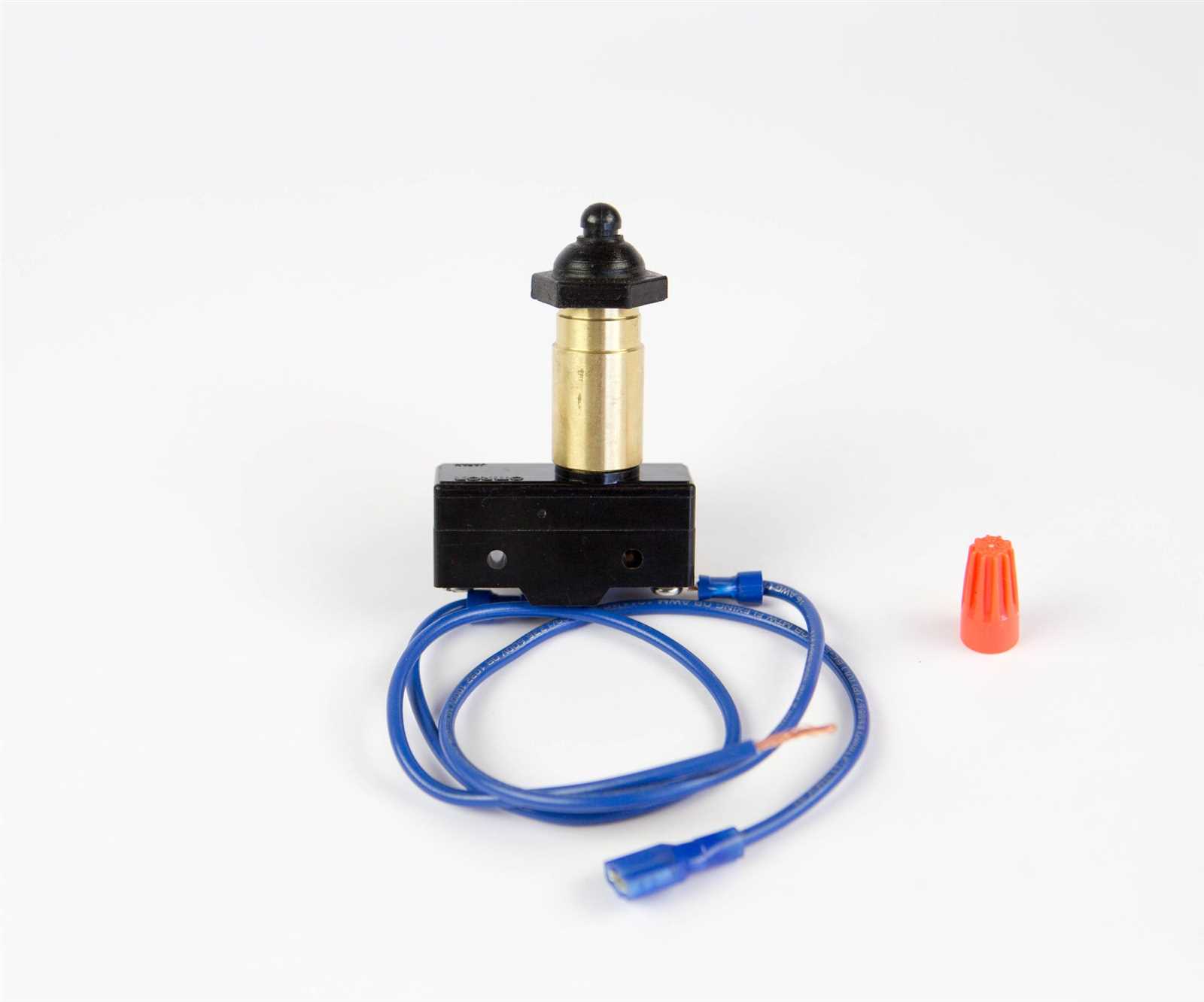
The motor assembly is the driving force behind many types of equipment, ensuring smooth and consistent operation. Its function is essential for powering the device and enabling it to perform its primary tasks. A well-maintained motor ensures efficiency and longevity, making it a critical component for overall functionality.
Key Components of the Motor Assembly
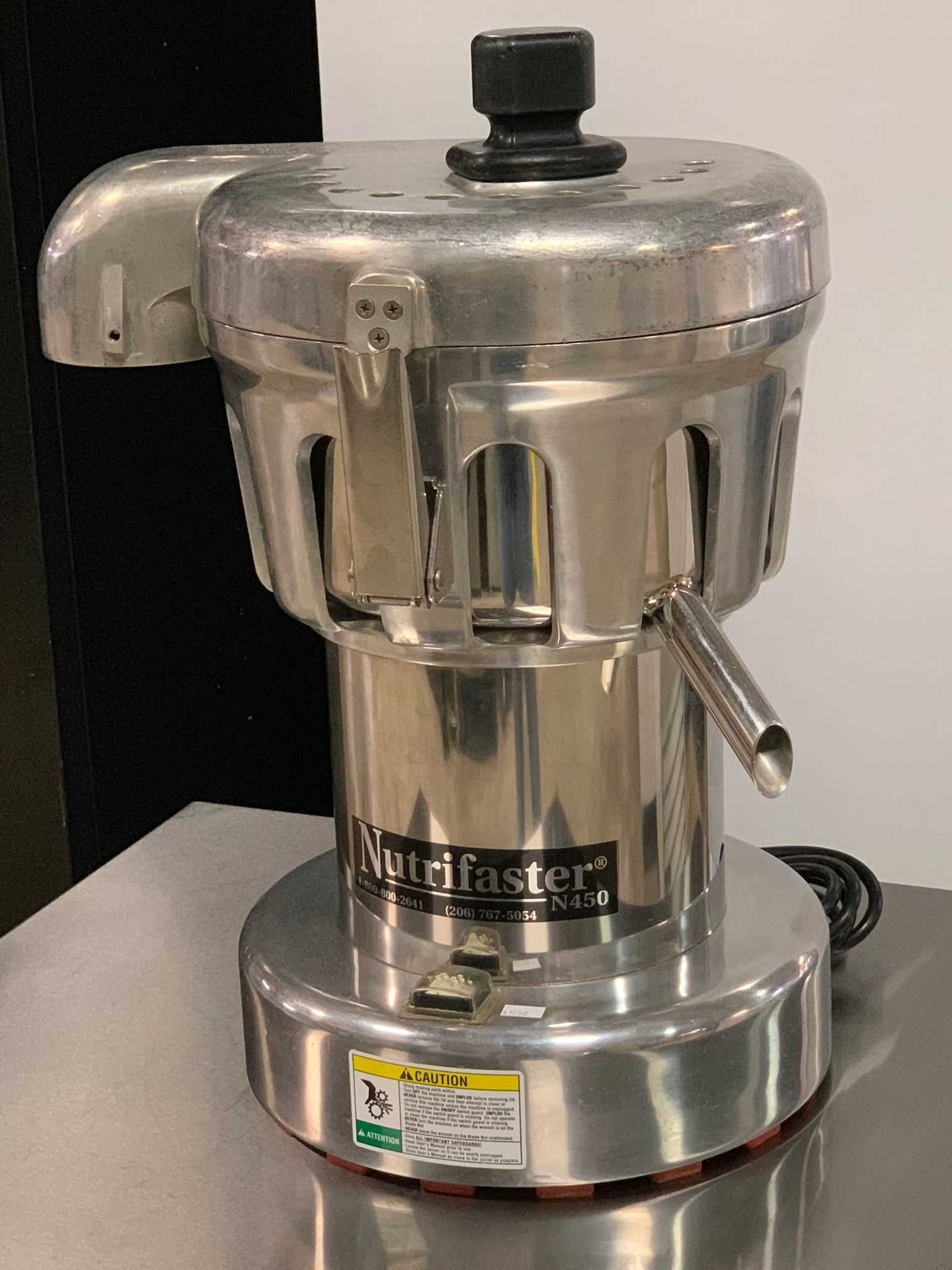
- Housing: The outer shell that protects internal parts from dust and damage.
- Rotor: The rotating element that converts electrical energy into mechanical movement.
- Bearings: Ensure smooth rotation and reduce friction between moving parts.
- Wiring: Conducts electricity to the motor, powering its operation.
Maintenance and Longevity
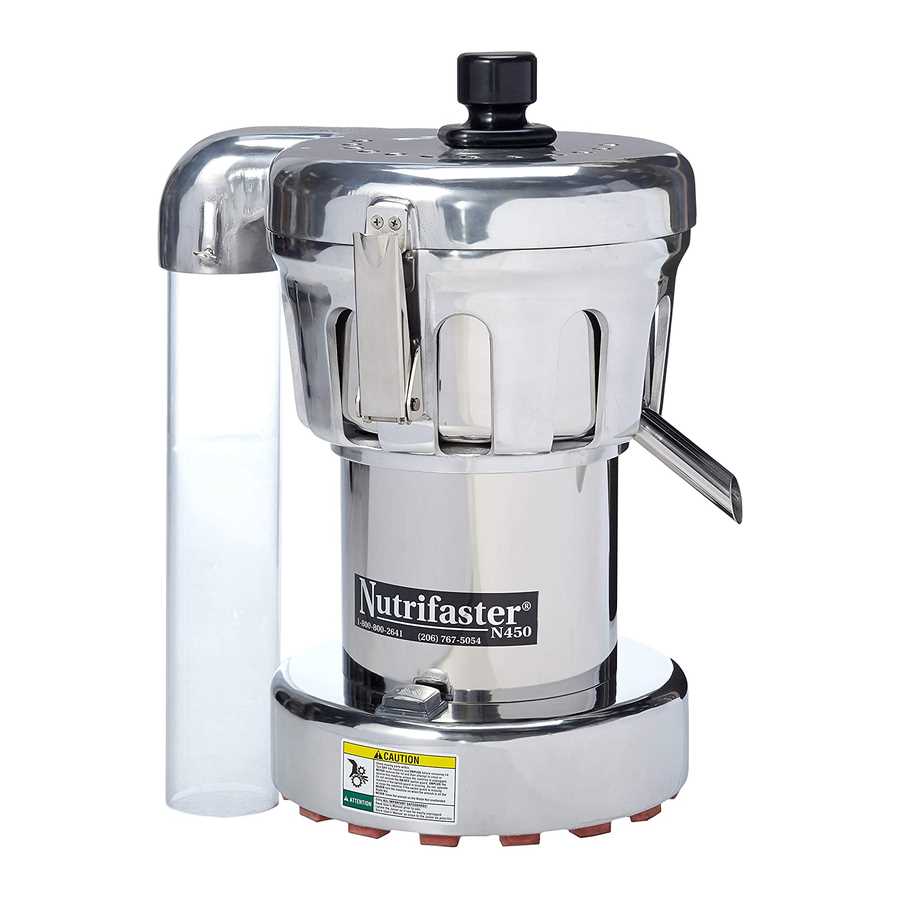
Regular care of the motor assembly is crucial for ensuring its long-term performance. Key maintenance steps include cleaning the housing, checking for wear on bearings, and inspecting the wiring for any signs of damage. By following these guidelines,
Material Durability in the Nutrifaster N450
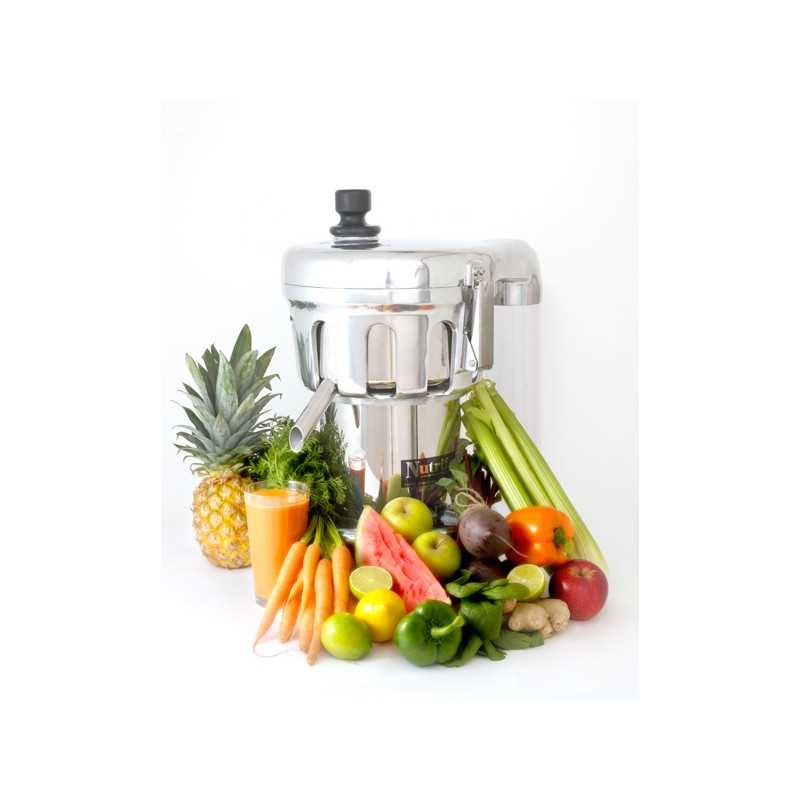
The longevity of any device largely depends on the quality of the materials used in its construction. Understanding how these components hold up under regular use, cleaning, and wear can provide insight into their overall reliability. Each element within this machine plays a role in determining how well it withstands constant operation, particularly in environments where it’s frequently utilized.
Here’s a breakdown of key factors affecting the durability of the device:
- Metal components: High-grade metals used in various sections ensure that the machine remains resistant to corrosion and mechanical stress. This contributes to the long-lasting performance of the system under heavy-duty usage.
- Plastic parts: Sturdy polymers provide lightweight yet strong support, crucial in reducing wear in moving parts. Their resistance to breakage helps maintain structural integrity over time.
- Seals and gaskets: Rubber and silicone elements prevent leaks and maintain airtight connections. The choice of flexible yet durable materials ensures that these components do not degrade quickly with repeated assembly and cleaning.
By utilizing robust materials, the overall construction remains resilient, enabling the device to function efficiently over an extended period.
Cleaning Tips for Removable Parts
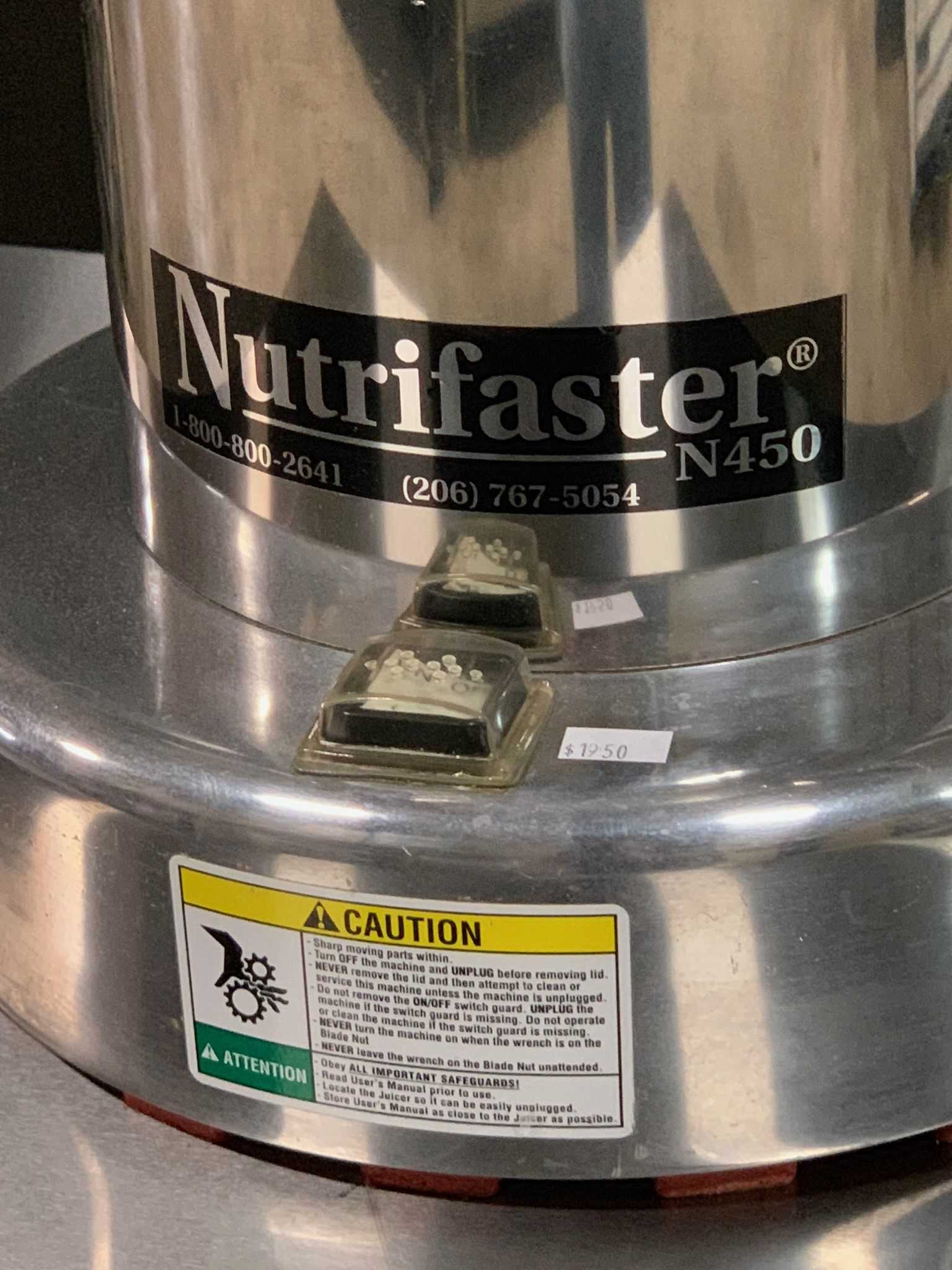
Keeping detachable components in excellent condition is essential for optimal performance and longevity. Regular maintenance not only ensures hygiene but also enhances the efficiency of the equipment. Below are some effective cleaning methods and tips to keep these elements clean and functional.
Recommended Cleaning Materials
When cleaning detachable components, it is crucial to use appropriate materials to avoid damage. Here is a list of recommended items:
Item |
Purpose |
Mild detergent |
Removes grease and residue |
Soft cloth |
Wipes surfaces without scratching |
Brush |
Cleans hard-to-reach areas |
Hot water |
Sanitizes and loosens stuck particles |
Step-by-Step Cleaning Process
Follow these simple steps for effective cleaning:
- Disassemble the components carefully according to the manufacturer’s guidelines.
- Soak the parts in warm soapy water for a few minutes.
- Use a soft cloth or brush to gently scrub away any stubborn residue.
- Rinse the components thoroughly with clean water to remove all soap.
- Dry completely before reassembling to prevent moisture buildup.
Chute Design and Its Impact on Performance
The configuration of the chute plays a vital role in the overall functionality and efficiency of the equipment. A well-designed chute facilitates the smooth flow of materials, reducing clogs and ensuring that the processing time is minimized. The shape, size, and angle of the chute can significantly affect how ingredients are delivered to the processing chamber, influencing the consistency and quality of the final product.
Moreover, the materials used in the chute’s construction can impact durability and ease of cleaning. Smooth surfaces help prevent residue build-up, while an appropriately sloped design aids in the quick and efficient discharge of contents. Inadequate design, on the other hand, can lead to delays, increased wear on components, and ultimately, lower output efficiency.
Understanding the nuances of chute design can help operators optimize performance and ensure consistent operation. Regular assessments and adjustments based on usage can further enhance the functionality of the equipment, leading to improved results in various applications.
Maintenance and Replacement of Internal Seals
Maintaining and replacing internal sealing components is crucial for ensuring the efficient operation of equipment. These elements play a vital role in preventing leaks and maintaining optimal performance. Regular inspection and timely replacement can significantly enhance the longevity and reliability of the machine.
Routine Maintenance is essential to identify wear and tear on seals. Inspect them periodically for any signs of deterioration, such as cracks or deformation. Keeping the area around the seals clean and free from debris will also help prevent premature failure.
When it comes to replacement, it’s important to choose high-quality materials that match the specifications of the original components. Follow the manufacturer’s guidelines for disassembly and reassembly to ensure proper installation. Additionally, using the correct tools can minimize the risk of damage during the replacement process.
In conclusion, understanding the maintenance and replacement of internal sealing components can lead to more efficient operation and extend the lifespan of your equipment. Regular care and prompt action in replacing worn seals will enhance overall performance and reduce the likelihood of costly repairs in the future.
Identifying Signs of Wear in the Centrifuge
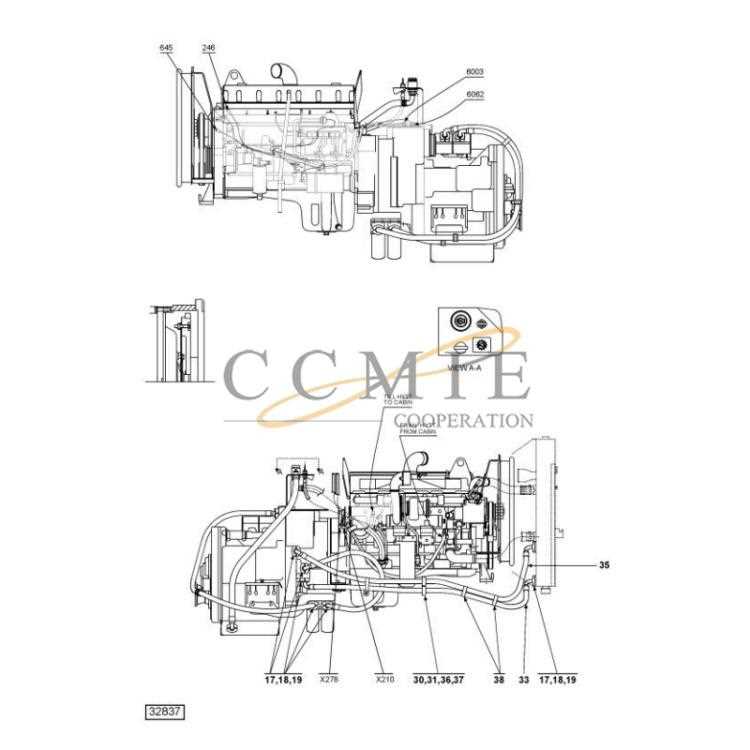
Recognizing the indications of deterioration in a spinning device is crucial for maintaining optimal performance and longevity. Various factors can contribute to wear, including the frequency of use, the quality of materials, and environmental conditions. Early detection of these signs can help prevent further damage and costly repairs.
Common Indicators of Wear
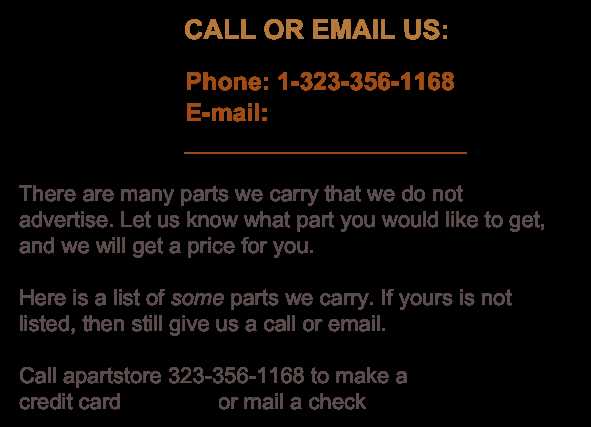
- Unusual Noises: Listen for grinding or squeaking sounds during operation, which may signal internal issues.
- Inconsistent Speed: If the unit fails to reach its designated speed, it may indicate wear on the motor or other components.
- Vibrations: Excessive shaking can result from misalignment or wear in the bearings, impacting performance.
Visual Inspections
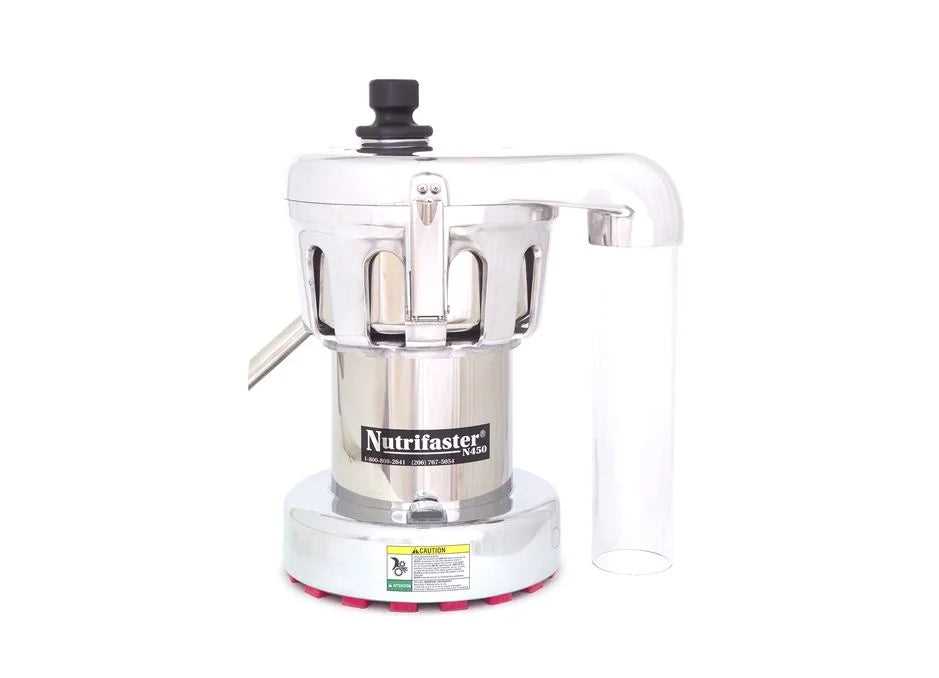
- Check for Cracks: Examine the housing and other visible parts for any signs of cracking or damage.
- Inspect Seals: Look for worn or damaged seals, which can lead to leaks and affect efficiency.
- Monitor for Rust: Corrosion can weaken components, so be vigilant for rust or discoloration.
The Importance of Proper Fit for Gaskets
Ensuring that sealing elements are correctly sized and shaped is crucial for the efficiency and longevity of any machinery. A well-fitted gasket can significantly enhance performance by preventing leaks and maintaining optimal pressure levels within the system.
Inadequate Fit can lead to numerous issues, including reduced efficiency, increased wear, and potential damage to components. When a sealing element does not match the designated space, it can result in gaps that allow substances to escape, which undermines the intended functionality.
Proper alignment of sealing elements not only optimizes performance but also contributes to safety by minimizing the risk of leaks that could lead to hazardous situations. Regular inspection and replacement of worn or improperly fitted gaskets are essential practices to ensure that equipment operates smoothly and effectively.
Safety Features Integrated into the Design
The design of this appliance incorporates a variety of safety features aimed at protecting users and ensuring reliable operation. These measures are essential for preventing accidents and enhancing the overall user experience.
One of the primary safety attributes is the inclusion of protective mechanisms that prevent overheating during operation. This feature not only safeguards the machine from potential damage but also enhances the safety of users by minimizing the risk of burns or fires. Additionally, the device is equipped with a secure locking system that ensures all components are properly assembled before it can function, reducing the likelihood of operational errors.
Moreover, the design incorporates easy-to-understand controls that are intuitive, allowing users to operate the machine safely without confusion. Emergency shutdown capabilities are also integrated, which enable quick power disengagement in unforeseen situations, providing an extra layer of safety.
Safety Feature |
Description |
Overheat Protection |
Automatically shuts off the appliance when it reaches a certain temperature to prevent damage and hazards. |
Secure Locking Mechanism |
Ensures all components are securely in place before the device can be activated, reducing the chance of misuse. |
Intuitive Controls |
User-friendly interface designed to minimize confusion and promote safe operation. |
Emergency Shutdown |
Allows for immediate power cut-off in emergency situations, enhancing user safety. |
Upgrading and Customizing Parts for Better Results
Enhancing the functionality of your equipment can lead to improved performance and efficiency. By carefully selecting and modifying specific components, you can tailor the device to better meet your needs, whether for personal use or in a commercial setting. Customization allows for a more precise operation, often resulting in higher quality outputs and a more satisfying experience.
When considering upgrades, it’s essential to assess the current capabilities of your equipment and identify areas for improvement. This may involve replacing standard elements with higher-quality alternatives or incorporating additional features that provide greater versatility. The choice of materials and design can significantly affect the overall effectiveness, making research and planning vital before proceeding with any modifications.
Another important aspect of customization is ensuring compatibility among the various components. This involves understanding how different parts interact and selecting those that work seamlessly together. Proper integration not only enhances performance but also minimizes the risk of damage or inefficiencies that could arise from incompatible elements.
Ultimately, investing time and effort into upgrading and customizing your equipment can yield substantial benefits. Enhanced functionality, improved efficiency, and the ability to tailor performance to specific tasks all contribute to a more rewarding experience, making these modifications a worthwhile consideration for any user.
Comparing Nutrifaster N450 to Similar Models
This section explores how a specific model compares to other similar appliances in terms of functionality, design, and user experience. By analyzing various alternatives, we can identify key differences and similarities that may influence a buyer’s decision.
Key Features Comparison
- Performance: Evaluate the efficiency of different machines regarding speed and output quality.
- Capacity: Consider the volume of ingredients each device can handle at once, impacting productivity.
- Durability: Compare the materials used in construction and their expected lifespan.
User Experience
- Ease of Use: Examine how intuitive the operation of each machine is, including setup and cleanup processes.
- Maintenance: Discuss the frequency and complexity of maintenance required for different models.
- Customer Feedback: Analyze reviews and ratings from users to understand real-world performance and satisfaction levels.
|