Connector Assembly |
Internal Structure of the RCK54P-127ZA
The device in question incorporates a complex assembly of interconnected components designed to ensure optimal performance. The overall design focuses on maximizing efficiency through precise alignment and integration of its internal elements. Each section within the unit is purposefully positioned to contribute to the seamless functioning of the entire system, making sure that the interactions between them are smooth and reliable.
Main Components and Layout
At the core of the internal structure lies a series of interconnected modules, each serving a distinct role in the operational process. These units are organized systematically, allowing for the transfer of energy and data between them without interference. The arrangement of these key parts is deliberate, ensuring that no excess heat is generated while maintaining stability across various operational conditions.
Material Composition and Durability
Durability is achieved through the use of high-grade materials that provide both structural support and resistance to wear over time. Each section is reinforced to handle pressure and stress, while also being lightweight enough to avoid
Understanding Electrical Connections in RCK54P-127ZA
When examining the intricate wiring systems in complex equipment, it is essential to grasp how the various electrical pathways interact to ensure proper functionality. These systems often rely on a network of connectors, cables, and terminals that transmit signals and power to the necessary components. By understanding how these connections work together, you can troubleshoot potential issues and improve the overall performance of the equipment.
Key Wiring Elements
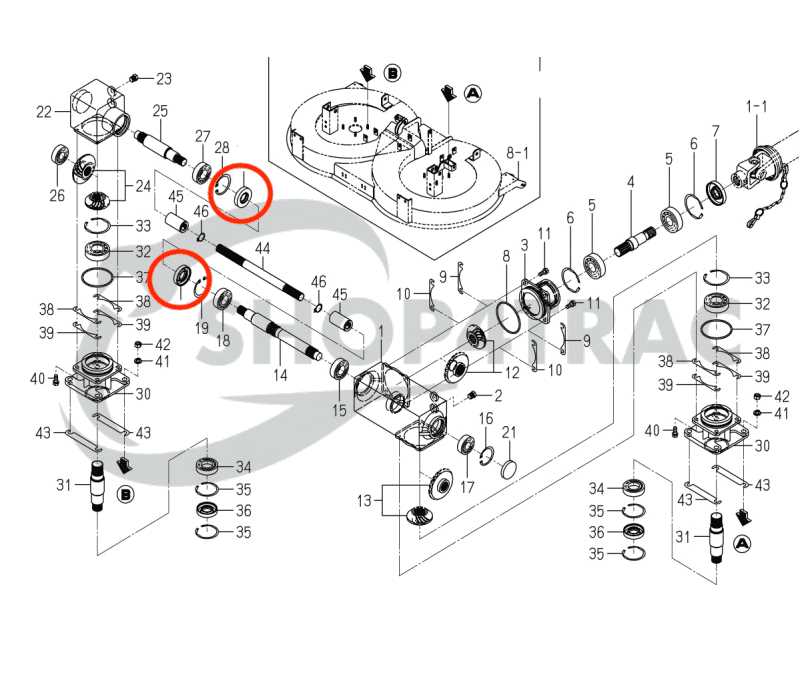
Each electrical network is composed of fundamental elements such as conductors, insulation, and connectors. Conductors facilitate the movement of electrical currents, while the insulation protects against short circuits and unwanted interference. Connectors, in turn, ensure secure and stable junctions between different components, preventing signal loss or power interruption. Mastery of these elements is crucial for ensuring that every part of the system operates seamlessly.
Maintaining Proper Conduct
Mechanical Elements of the RCK54P-127ZA
The device in question incorporates a variety of mechanical components that ensure its smooth operation. These elements work in harmony to provide stability, precision, and reliability during its use. Each component serves a specific role in the overall functionality, contributing to the durability and performance of the system.
One of the key aspects of its construction is the structural framework, which provides a solid foundation. This framework not only supports the internal mechanisms but also ensures resistance to wear and tear over time. The use of high-grade materials in its assembly helps maintain its integrity, even under heavy usage.
Another crucial element is the set of precision-engineered gears and levers. These moving parts are responsible for converting energy into motion, allowing the system to function efficiently. The design of these components is optimized for minimal friction, ensuring long-term reliability and reducing the need for frequent maintenance.
In addition, the presence of finely calibrated springs and tensioners plays a vital role in regulating the forces within the system. These components help absorb shock and maintain balance, protecting more delicate parts from sudden impacts or strain. Their contribution to
Common Issues and Their Causes
Understanding the frequent problems that can arise with mechanical systems is essential for ensuring optimal functionality. Identifying the root causes of these malfunctions can help in minimizing downtime and preventing long-term damage. Below, we will explore some of the most typical issues encountered and the possible reasons behind them.
Performance Fluctuations
Performance inconsistency is one of the more prevalent challenges that users may face. This often manifests as irregular operation or reduced efficiency. Several factors can contribute to these fluctuations:
- Poor maintenance practices, such as insufficient lubrication or cleaning, can lead to excessive wear.
- External environmental conditions like temperature or humidity may impact the operational stability.
- Component misalignment caused by improper installation or gradual shifting over time can result in inconsistent performance.
Unexpected Shutdowns
Maintenance Tips for Optimal Performance
Regular upkeep is essential to ensure the longevity and efficiency of your equipment. By following simple guidelines, you can prevent unnecessary wear and tear and maintain peak functionality over time. Proper care not only improves performance but also minimizes the risk of unexpected breakdowns.
Routine Inspection and Cleaning
Performing periodic inspections is key to identifying potential issues before they escalate. Regularly clean all moving parts to avoid debris build-up, which can lead to inefficiencies. A clean system operates more smoothly, reducing friction and extending the life of its components. Use appropriate cleaning tools and avoid harsh chemicals that could damage sensitive surfaces.
Lubrication and Adjustments
Ensure that all parts requiring lubrication are adequately serviced. This reduces friction and helps in maintaining optimal operation. Also, check for any necessary adjustments to ensure that the components are aligned correctly, which enhances both performance and safety. Over time, even small misalignments can cause significant strain on the system.
Identifying Major Subsystems
When analyzing complex machinery, it is essential to break down the system into its core components to better understand its functionality. These main sections, or subsystems, work together to achieve the overall purpose, each with its own specific role. Identifying these subsystems allows for easier diagnosis, maintenance, and optimization of the entire system. By categorizing each part, one can pinpoint specific areas for improvement or troubleshooting.
Core Functionality Units
The primary subsystems often consist of essential units that drive the overall operation. These units include:
- Power generation and distribution
- Control and monitoring systems
- Mechanical support and movement mechanisms
Supportive Subsystems
In addition to the core units, several supportive elements ensure smooth operation and reliability. These include:
- Cooling and thermal regulation
- Communication and data transfer systems
- Safety and emergency response mechanisms
Comparison of Similar Models
When exploring various models within the same category, it is essential to examine their features and specifications to determine their suitability for specific tasks. While each variant may offer unique strengths, comparing their core attributes helps in identifying the most appropriate option for users with different needs.
Key Features and Differences
- Design and build quality
- Functionality and versatility
- Durability and long-term performance
- Ease of maintenance and repairs
- Compatibility with other systems or accessories
Performance and Efficiency
- Power consumption and energy efficiency
- Speed and responsiveness in various conditions
- Output quality in relation to user requirements
- Durability in challenging environments
How to Replace Specific Parts
When it comes to maintaining and repairing equipment, knowing how to replace individual components is essential. Identifying the faulty elements and following the proper replacement procedure ensures the longevity and efficiency of the system. Below is a guide on how to effectively swap out key elements, minimizing downtime and ensuring smooth operation.
Follow these steps for replacing a specific component:
- Turn off the device: Always begin by powering down the equipment to prevent any electrical hazards or damage during the process.
- Access the faulty component: Depending on the device design, remove the outer cover or casing to expose the internal components. Make sure to keep screws and parts organized for reassembly.
- Disconnect the defective element: Carefully detach any wires, connectors, or fasteners that are linked to the part that needs to be replaced. Take note of the connections for easier reinstallation.
- Install the new component: Position the replacement part correctly, ensuring that it matches the original configuration. Reconnect all wiring and secure the part using the appropriate screws or fasteners.
- Test the system: After the new component is in place, power up the system and check for proper functionality. Run tests to verify that the issue has been resolved and the equipment operates as expected.
Regularly replacing worn-out components keeps equipment in optimal working condition, reducing the likelihood of major breakdowns and extending the overall lifespan of your device.
Safety Guidelines for Handling the Device
When working with complex equipment, ensuring proper safety measures is essential to prevent accidents and damage. Adhering to safety protocols not only protects the user but also extends the life of the device. It is crucial to follow specific precautions before, during, and after handling to avoid any potential hazards.
Precautionary Steps Before Use
Before operating the equipment, make sure it is placed on a stable surface and all connections are secure. Always check the power source and ensure that any electrical components are properly insulated. Disconnect the device from the main power supply when performing maintenance or inspections to avoid electric shocks or inadvertent activation.
Safe Operation and Handling Practices
While operating the equipment, avoid any unnecessary physical contact with exposed mechanical parts. Always use protective gloves if necessary to shield from sharp edges or hot surfaces. Proper posture and hand positioning are crucial to prevent strain or injury during extended use. Additionally, ensure that the surrounding area is free from clutter to maintain balance and reduce the risk of tripping or accidental impact.
After use, store the device in a designated safe location away from environmental factors such as moisture or extreme temperatures. Proper storage helps maintain the integrity of the equipment and ensures safety for future handling.
Material Composition and Durability
The construction quality of any mechanical system plays a crucial role in its long-term performance and reliability. The choice of materials significantly impacts the durability and overall functionality of each component. Understanding the composition of these materials is essential to predict their resistance to wear, stress, and environmental conditions over time.
Materials Used
- High-Strength Alloys: These materials are known for their ability to withstand high levels of mechanical stress and impact. Their resistance to corrosion and fatigue makes them ideal for components exposed to heavy usage.
- Reinforced Polymers: Polymers that have been enhanced with fibers or other materials offer flexibility and high resistance to abrasion, making them suitable for components that experience friction.
- Ceramic Coatings: Often used for protective layers, ceramic coatings provide a robust defense against high temperatures and abrasive forces, increasing the lifespan of the mechanical system.
Durability Factors
- Wear Resistance: Components made from materials with superior wear resistance ensure prolonged use without significant degradation, even under constant friction.
- Corrosion Resistance: The ability of materials to resist rust and chemical reactions extends the component’s lifetime, especially in challenging environments like high humidity or exposure to chemicals.
- Thermal Stability: Materials that can maintain their properties under extreme temperature variations are crucial in ensuring that components continue to function efficiently over time.