Provides the space for fuel
Cutting Blade Structure
The cutting blade is a vital component that enables efficient trimming and shaping of various materials. Its design is optimized for precise and smooth performance, ensuring effective cutting with minimal effort. The blade’s overall structure allows for balanced operation and durability during extensive use.
Blade Material and Durability
One of the key features of the cutting blade is the material it is crafted from. Designed to withstand heavy-duty work, it maintains sharpness and strength over time, even in challenging conditions. This ensures long-lasting reliability and reduced need for frequent replacements.
Efficiency and Maintenance
To maximize efficiency, the blade’s structure is designed to reduce resistance while cutting, allowing for clean and swift action. Regular maintenance, such as sharpening and cleaning, is essential to preserve its cutting precision and extend the life of the blade.
Fuel System Configuration
The fuel system is a vital component that ensures the efficient operation of a power tool. It is designed to deliver the necessary energy to the engine while maintaining optimal performance. Proper configuration of this system is essential for achieving reliability and longevity.
Key elements of the fuel system include:
- Fuel Tank: This is where the fuel is stored before it is supplied to the engine. A clean and properly sealed tank prevents contamination.
- Fuel Lines: These flexible tubes transport fuel from the tank to the engine. Ensuring they are free of leaks and blockages is crucial.
- Filter: A fuel filter is installed to remove impurities from the fuel, safeguarding the engine from potential damage.
- Pump: The pump helps in drawing fuel from the tank and supplying it to the carburetor or fuel injection system, depending on the design.
- Carburetor or Fuel Injector: This component mixes fuel with air in the correct ratio for combustion, playing a key role in performance.
Regular maintenance and inspection of the fuel system components are recommended to prevent issues. Always use the recommended fuel type for optimal performance.
Oil Pump and Lubrication Mechanism
The oil delivery system plays a crucial role in ensuring the smooth operation of equipment, allowing for optimal performance and longevity. This mechanism is designed to maintain proper lubrication of essential components, preventing wear and tear during use. The efficient circulation of lubricant minimizes friction, which is vital for the effective functioning of the machinery.
Within this system, the pump is responsible for transferring oil from the reservoir to various moving parts. By utilizing a combination of pressure and flow, it ensures that all critical areas receive adequate lubrication. Regular maintenance of this assembly is essential to prevent clogs or failures that could lead to significant operational issues.
Understanding the layout and functioning of the lubrication mechanism is key for users seeking to optimize their equipment’s efficiency. Proper servicing and timely oil changes contribute significantly to maintaining peak performance and extending the lifespan of the machinery.
Throttle Control and Trigger Layout
The configuration of the throttle mechanism and trigger system plays a crucial role in the operation of power tools. Understanding how these components interact allows for improved handling and optimal performance. This section explores the essential features and functions of the throttle control and trigger layout.
Components Overview
Several key components comprise the throttle control and trigger layout:
- Throttle Trigger: This part is responsible for regulating the engine’s speed. It allows the operator to adjust power output based on the task requirements.
- Return Spring: A vital element that ensures the trigger returns to its original position when released, promoting safety and control.
- Throttle Cable: This cable connects the throttle trigger to the engine, facilitating smooth operation and response.
- Control Housing: The housing protects internal components and provides a comfortable grip for the user.
Functionality and Usage
The throttle trigger enables users to easily manage engine performance. Proper usage ensures efficient operation while minimizing the risk of accidents. Key points to consider include:
- Always ensure the trigger is fully functional before use.
- Adjust the throttle gradually to maintain control during operation.
- Regularly inspect the throttle cable and return spring for wear and tear.
Chain Drive System Details
The chain drive system is a crucial component that facilitates the transfer of power between the engine and the cutting mechanism. This system ensures efficient operation and reliable performance in various tasks, contributing to the overall functionality of the equipment.
Key Components
- Chain: A robust link structure that transmits motion and force.
- Sprockets: Gear-like wheels that engage with the chain, enabling rotation.
- Tensioner: A device that maintains appropriate chain tension for optimal performance.
- Guide Bar: A support structure that directs the movement of the chain.
Operational Principles
In this system, the engine generates power, which is conveyed through the sprockets and chain. The continuous loop of the chain allows for smooth rotation, facilitating cutting or trimming tasks. Regular maintenance, such as lubrication and tension adjustment, is essential to ensure longevity and efficient operation.
Protective Guard Placement
The proper positioning of protective barriers is essential for ensuring safety during the operation of gardening equipment. These safeguards serve to shield the user from potential hazards, minimizing the risk of injury while enhancing the overall efficiency of the tool.
Correct Installation: It is crucial to follow manufacturer guidelines when installing protective shields. These instructions provide detailed steps for effective placement, ensuring that the guards effectively cover vulnerable areas.
Regular Inspection: Frequent checks should be conducted to confirm that the guards remain securely in place and are not damaged. Any signs of wear or malfunction should be addressed immediately to maintain optimal safety standards.
- Ensure that the guard does not obstruct any moving parts.
- Position the guard to provide maximum coverage without hindering visibility.
- Consult the manual for specific alignment instructions.
Exhaust System Components
The exhaust system plays a crucial role in the performance and efficiency of small engines. It is responsible for directing harmful gases away from the engine while minimizing noise and ensuring optimal operation. Understanding the various elements within this system can help in maintaining and troubleshooting engine performance.
Main Components
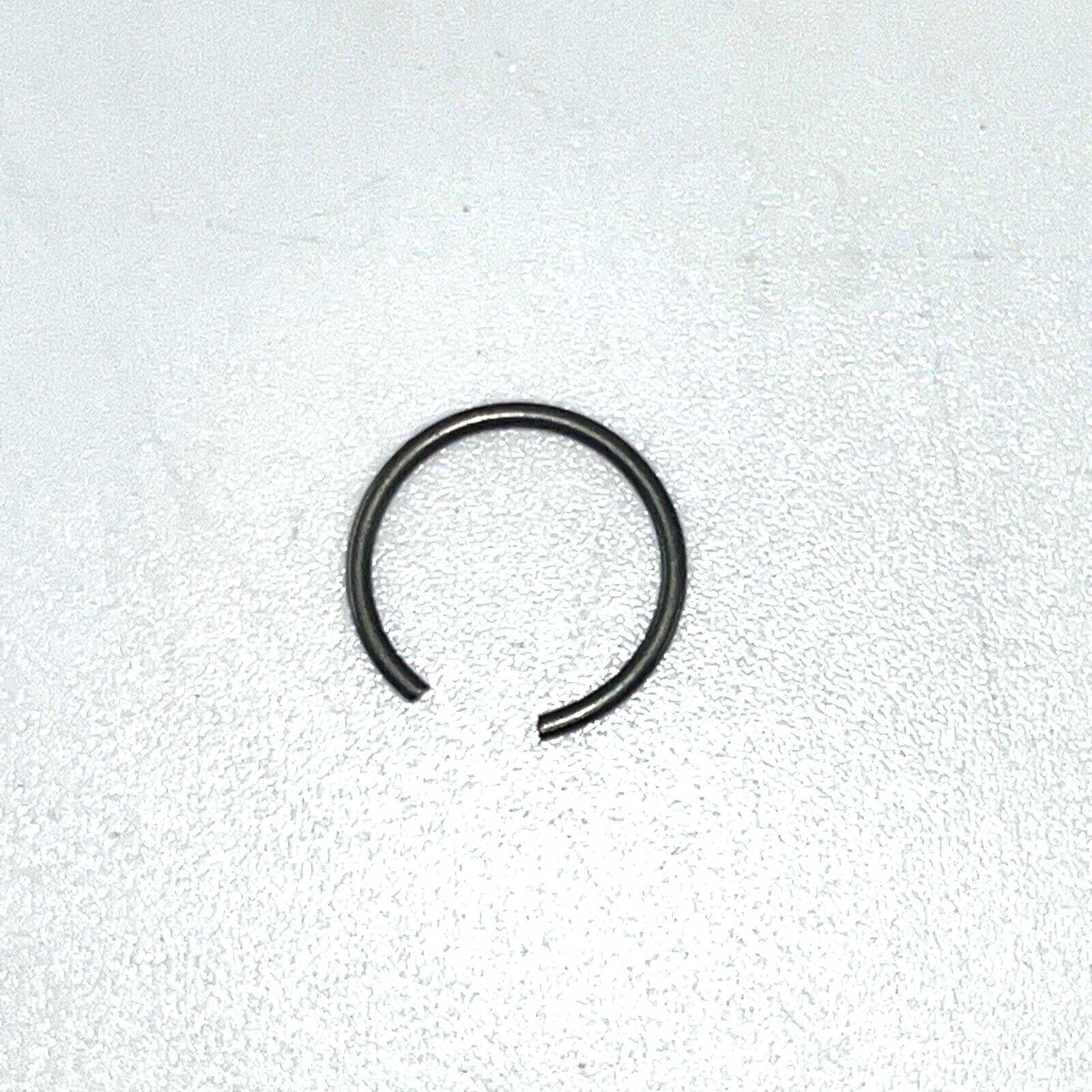
- Exhaust Manifold: This part collects gases from the engine cylinders and channels them into the exhaust pipe.
- Silencer: Also known as a muffler, it reduces the noise produced by the escaping gases, providing a quieter operation.
- Exhaust Pipe: The pipe connects the manifold to the exit point, allowing gases to exit the engine safely.
- Gaskets: These seals are essential for preventing leaks at joints, ensuring efficient gas flow.
- Heat Shield: This component protects surrounding parts from excessive heat produced by the exhaust system.
Importance of Maintenance
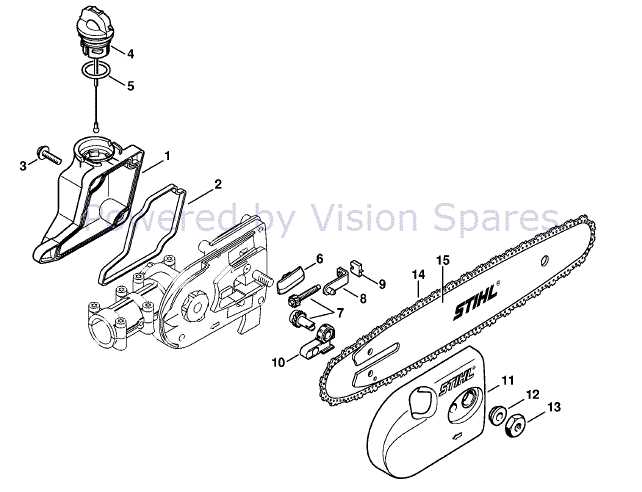
Regular inspection and maintenance of the exhaust system components are vital for ensuring engine longevity and performance. Neglecting these parts can lead to increased emissions, reduced efficiency, and potential engine damage.
Signs of Malfunction
- Unusual noise from the exhaust area.
- Decreased engine performance or power.
- Visible damage or corrosion on exhaust components.
- Strong odors from exhaust fumes.
Maintenance Tips for Longevity
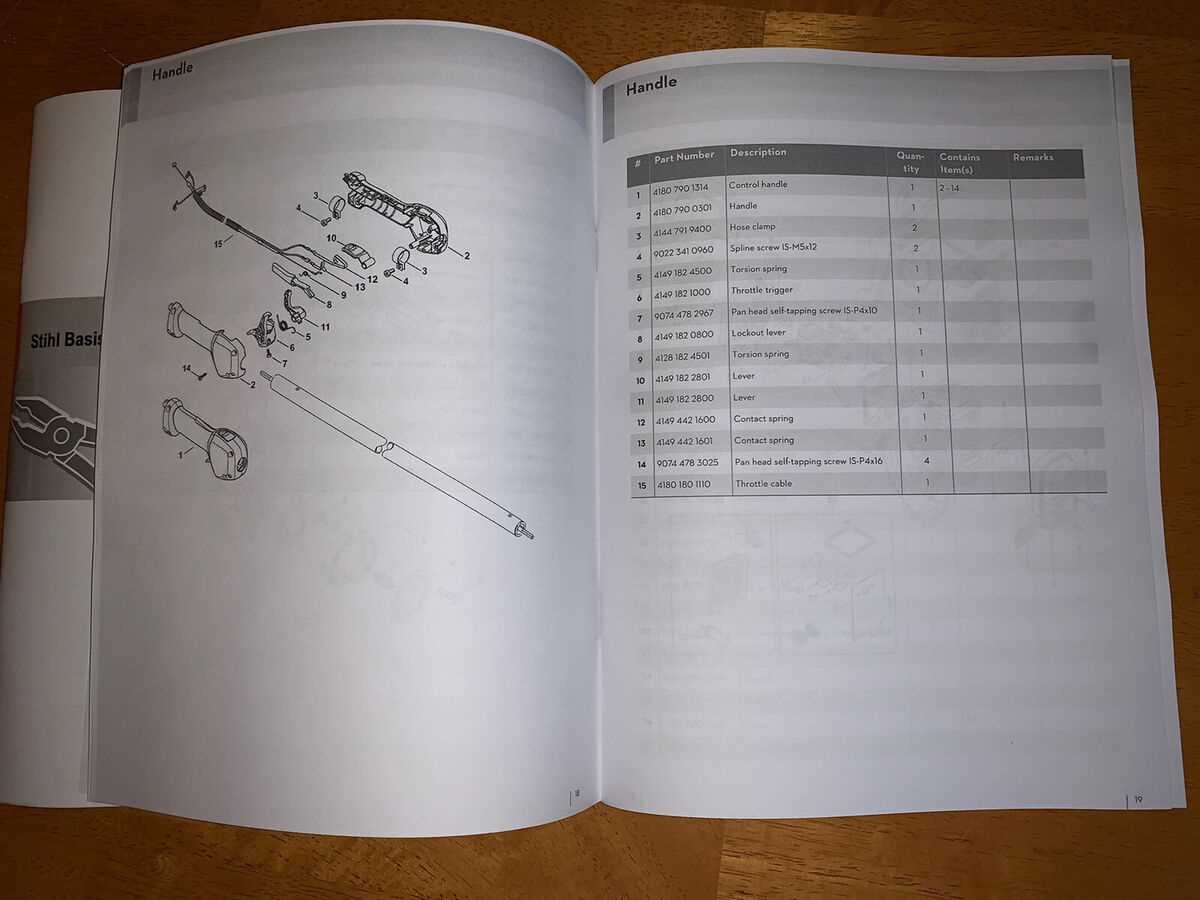
To ensure the extended life of your equipment, regular upkeep is essential. Adopting a consistent maintenance routine can significantly enhance performance and durability, preventing unexpected breakdowns and costly repairs.
1. Regular Cleaning: After each use, remove any debris and dirt. Keeping the device clean helps prevent damage and maintains optimal functionality.
2. Inspect Components: Frequently check key components for wear and tear. This includes examining blades, filters, and other crucial parts for any signs of damage that could hinder performance.
3. Lubrication: Proper lubrication of moving parts reduces friction and wear. Ensure to apply the appropriate lubricant to extend the life of your machine.
4. Storage Conditions: Store the equipment in a dry and sheltered area to protect it from moisture and extreme temperatures, which can lead to corrosion and other damage.
5. Follow the Manual: Always refer to the user manual for specific maintenance instructions and recommended service intervals, ensuring your equipment receives the proper care it requires.
|