The Role of the Regulator in Airflow Control

The regulator plays a crucial part in managing the flow of pressurized gas within various systems. Its function is to ensure that the output pressure is consistent and adjustable according to specific needs, which is essential for maintaining efficiency and safety. By adjusting the regulator, the operator can fine-tune the pressure to match the requirements of different tasks, helping to avoid overpressure that could damage equipment or lead to malfunctions.
In operation, the regulator helps maintain steady performance by controlling the volume of gas that passes through the system. This makes it a vital component for achieving precision in various applications, from simple home tasks to more complex industrial processes. Its ability to regulate ensures smooth operation,
How the Safety Valve Protects the System
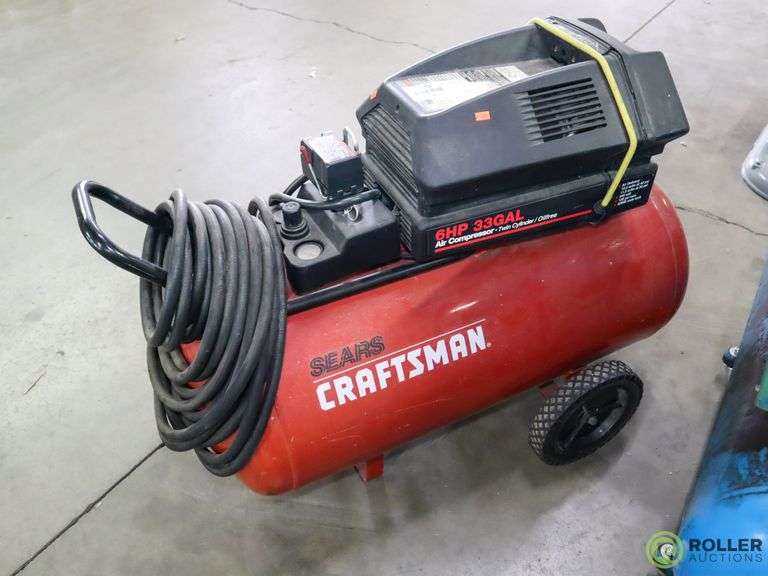
The safety valve plays a crucial role in maintaining the overall stability of the system by preventing excessive pressure buildup. It acts as a safeguard, releasing pressure when it reaches a critical threshold, ensuring that all components function within safe limits. This mechanism helps avoid potential damage or malfunctions that could occur due to an uncontrolled rise in pressure.
Pressure Regulation
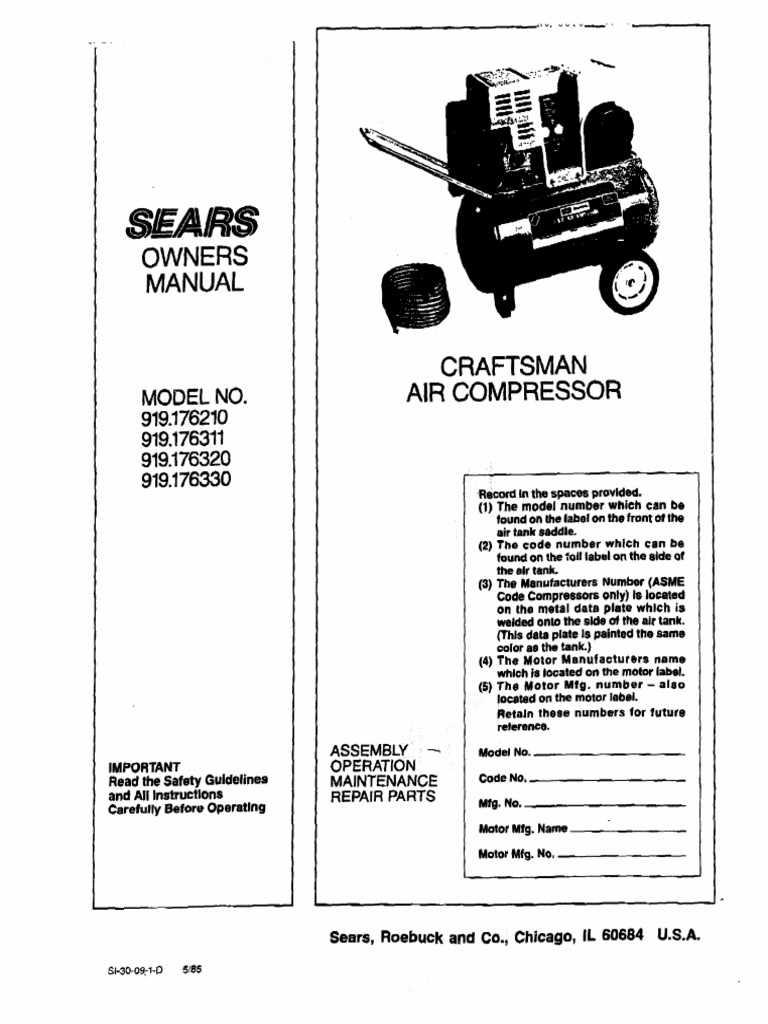
The valve constantly monitors the internal levels of force and is designed to respond swiftly when necessary. By automatically adjusting and releasing excess force, it keeps the system running smoothly and prevents wear or sudden failure of its parts.
Preventing System Overload
A properly functioning valve is essential for avoiding system overloads, which could lead to more severe issues if not controlled. Its timely intervention not only enhances the lifespan of
Maintaining the Compressor’s Oil Level
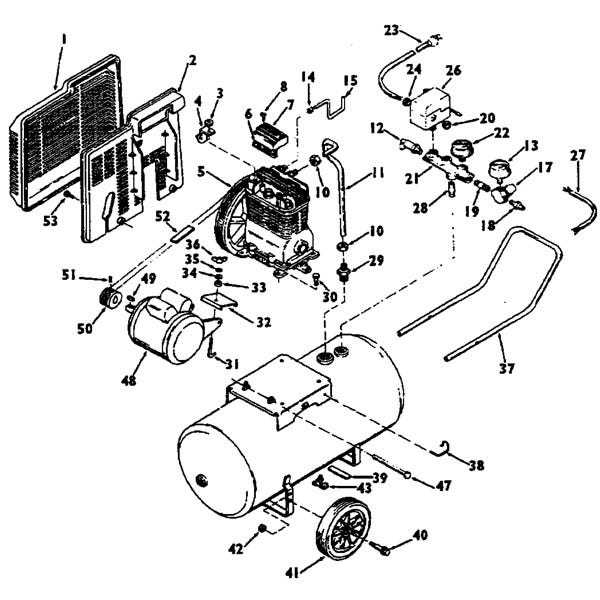
Regular monitoring of lubrication fluid is essential for optimal performance and longevity of your machinery. Proper maintenance of this fluid ensures that internal components operate smoothly, reducing wear and tear over time. Neglecting this aspect can lead to various operational issues, potentially resulting in costly repairs or replacements.
Checking the Fluid Level
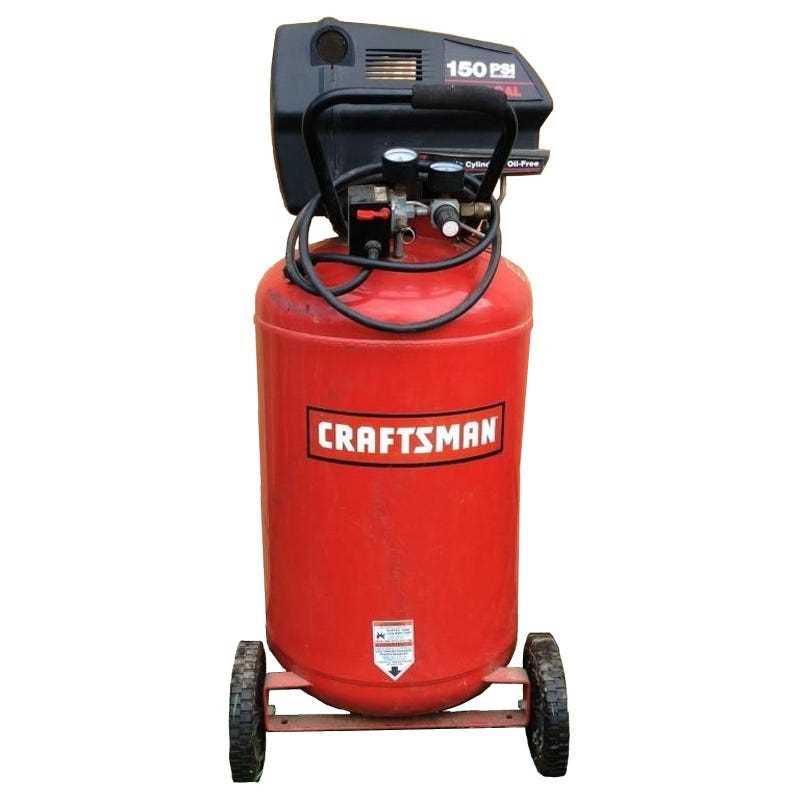
To begin, locate the designated viewing window or dipstick, which allows for easy assessment of the fluid level. It is advisable to check this level periodically, especially before using the equipment. If the level appears low, it is crucial to add the appropriate type of lubrication fluid to maintain optimal operation.
Adding Lubrication Fluid
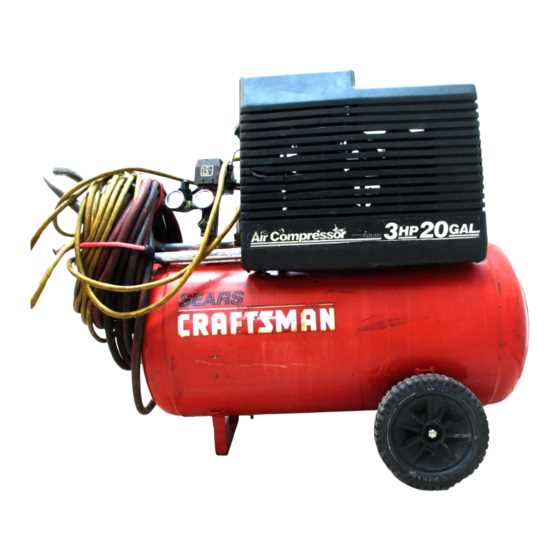
When replenishing the fluid, ensure that you use a product that meets the specifications outlined in the manufacturer’s guidelines. Pour the new fluid slowly to prevent overflow, and allow it to settle for a few moments before re-checking the level. Maintaining the correct fluid amount not only enhances performance but also promotes a more efficient and reliable operation.
Understanding the Function of the Drain Valve
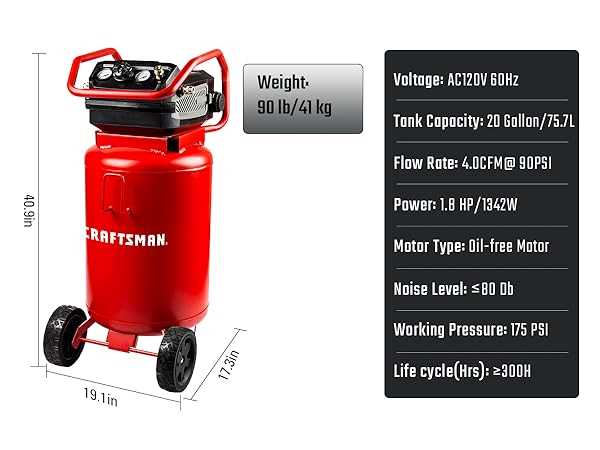
The drain valve serves a crucial role in the overall efficiency and maintenance of a pressure device. Its primary function is to allow for the expulsion of accumulated moisture and contaminants that can build up within the tank during operation. By effectively managing this residue, the drain valve helps to prolong the lifespan of the equipment and ensures optimal performance.
Importance of Regular Maintenance
Regularly checking and using the drain valve is essential for maintaining the integrity of the system. Neglecting this component can lead to rust and corrosion, which may compromise the unit’s functionality. Additionally, a properly functioning drain valve helps maintain safe operating conditions by preventing excess pressure buildup.
Operating the Drain Valve
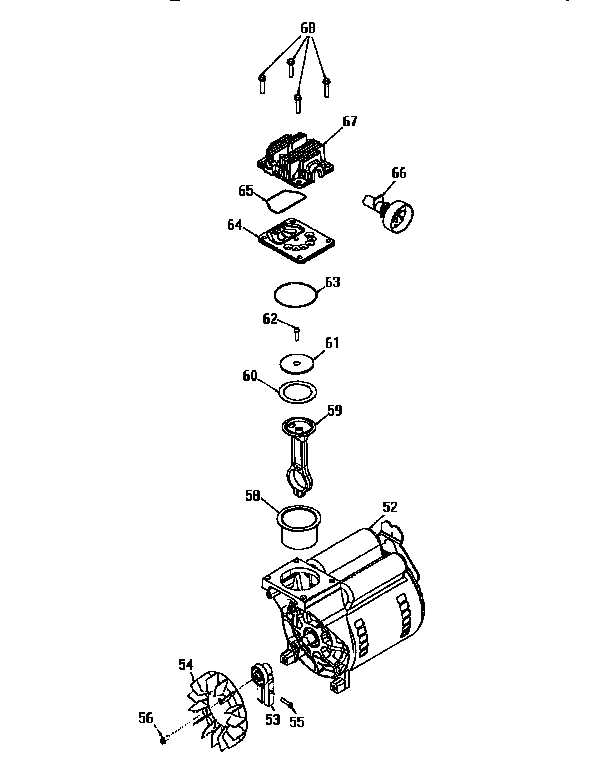
To operate the drain valve, users should ensure that the device is turned off and depressurized. Slowly opening the valve will release the trapped moisture and debris. It is advisable to perform this task periodically to maintain the system in peak condition. This simple practice can significantly enhance the durability and reliability of the equipment.
How the Tank Pressure Gauge Works
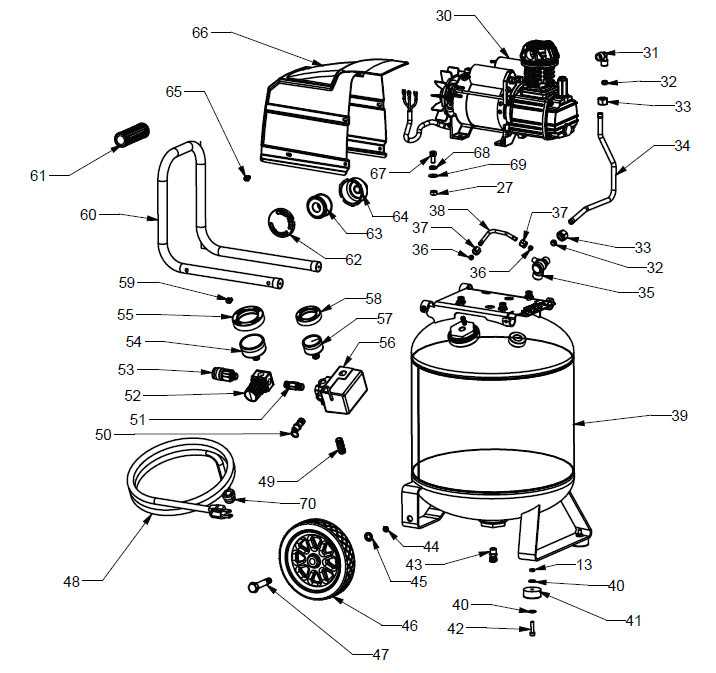
The pressure indicator serves a crucial role in monitoring the internal force within a storage vessel. This instrument allows users to assess the energy contained within the system, ensuring optimal performance and safety during operation.
Functionality Overview
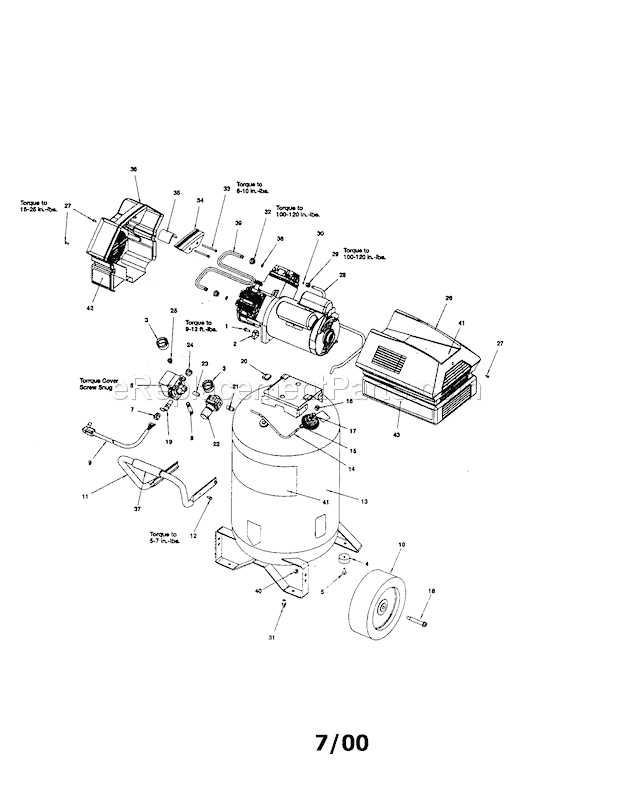
This gauge operates based on the principle of pressure measurement, using a mechanical or electronic mechanism to translate force into a readable value. As the pressure rises or falls, the gauge reflects these changes, providing vital information to the operator.
Importance of Accurate Readings
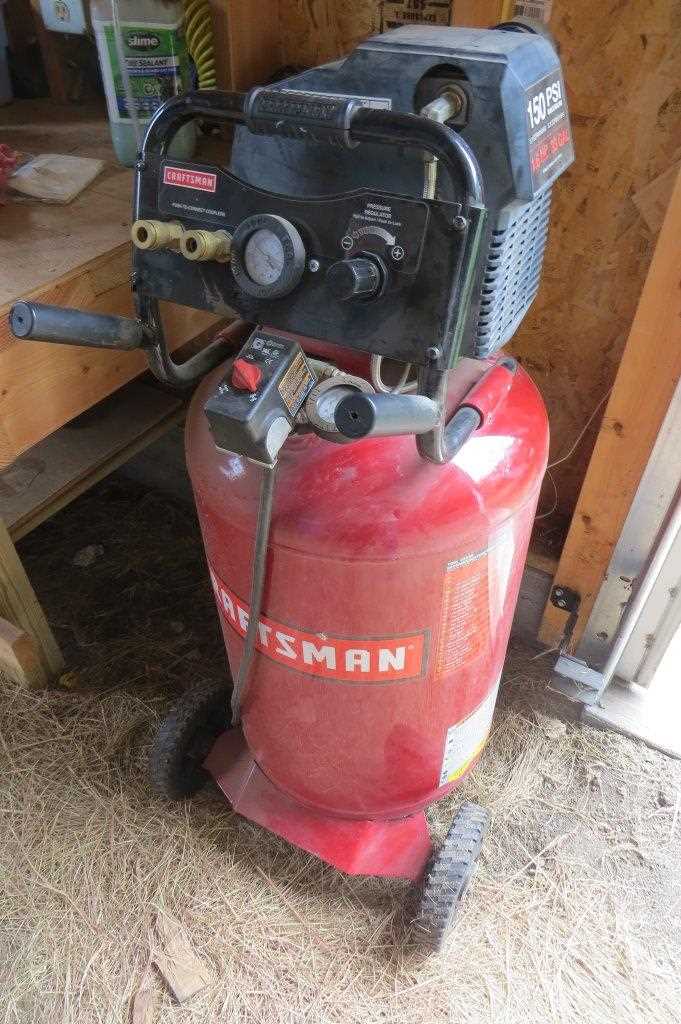
Accurate readings from this instrument are essential for maintaining efficiency and preventing potential hazards. By regularly checking the readings, users can make informed decisions regarding the operation and maintenance of the equipment.
Gauge Type |
Measurement Range |
Common Uses |
Analog |
0-150 psi |
Basic applications |
Digital |
0-200 psi |
Precision tasks |
Compound |
-30 inHg to 0-150 psi |
Vacuum and pressure applications |
Checking the Health of the Air Filter
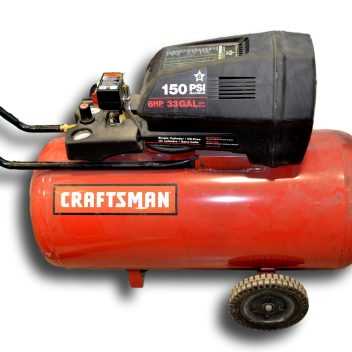
Maintaining the optimal performance of your equipment requires regular inspection of various components, including the filtration system. A well-functioning filter ensures that contaminants do not interfere with the machinery’s operation. This section outlines the steps to assess the condition of the filter and ensure it operates effectively.
Signs of a Clogged Filter
Identifying a blockage early can prevent further complications. Here are some common indicators:
- Reduced airflow during operation
- Increased noise levels
- Visible dust accumulation on the filter
- Unusual odors emanating from the equipment
Steps for Inspection
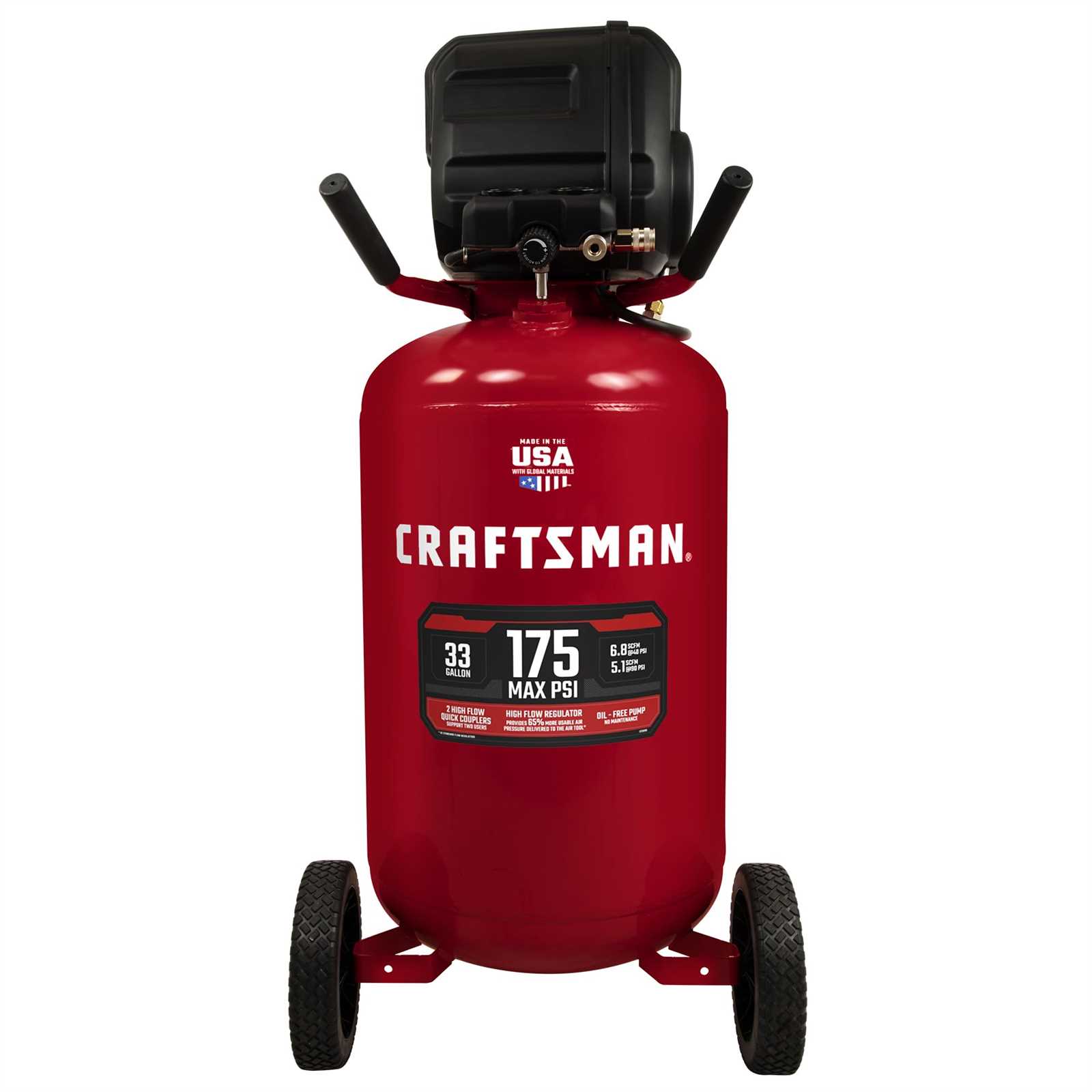
Follow these guidelines to evaluate the filter’s condition:
- Turn off the equipment and disconnect it from the power source.
- Carefully remove the filter from its housing.
- Examine the filter for dirt and debris.
- If heavily soiled, consider cleaning or replacing it.
- Reinstall the filter and ensure it is secured properly.
By keeping a close eye on the filtration system, you can enhance the longevity and efficiency of your machinery.
Replacing Worn Seals and Gaskets
Over time, the integrity of various components can diminish due to wear and tear. Addressing these issues promptly is crucial to maintain optimal functionality. Ensuring that all seals and gaskets are in good condition will prevent leaks and enhance performance.
Identifying Signs of Damage
Before proceeding with replacements, it’s essential to recognize the indicators that suggest seals and gaskets need attention:
- Visible cracks or tears
- Increased noise levels during operation
- Air leaks or reduced efficiency
- Unusual vibrations
Steps for Replacement
To successfully replace worn components, follow these steps:
- Turn off the unit and disconnect from power.
- Carefully remove the affected parts, taking care not to damage surrounding components.
- Clean the surfaces thoroughly to ensure a proper seal.
- Install new seals and gaskets, ensuring they fit securely in place.
- Reassemble the unit and conduct a test run to check for leaks.
Troubleshooting Common Air Compressor Issues
When dealing with equipment designed to provide pressurized gas, it is essential to recognize potential malfunctions that may arise during operation. Identifying and resolving these issues can ensure optimal performance and longevity of the machinery. This section outlines frequent problems encountered and offers practical solutions to restore functionality.
Identifying Performance Issues
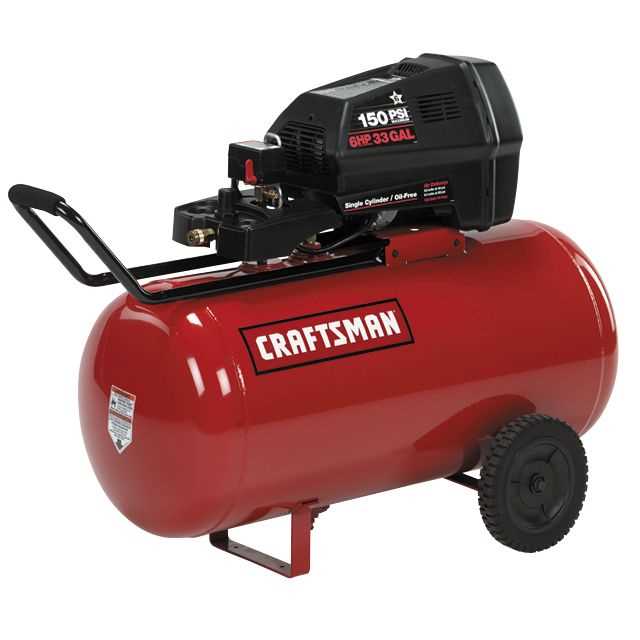
One of the most common challenges is the inability of the unit to build up adequate pressure. This may stem from various sources such as leaks in the system, a faulty pressure switch, or inadequate power supply. Checking for any visible cracks or connections that may be compromised is a good starting point. Additionally, ensure that the device is receiving sufficient electrical supply to operate correctly.
Addressing Noise and Vibration
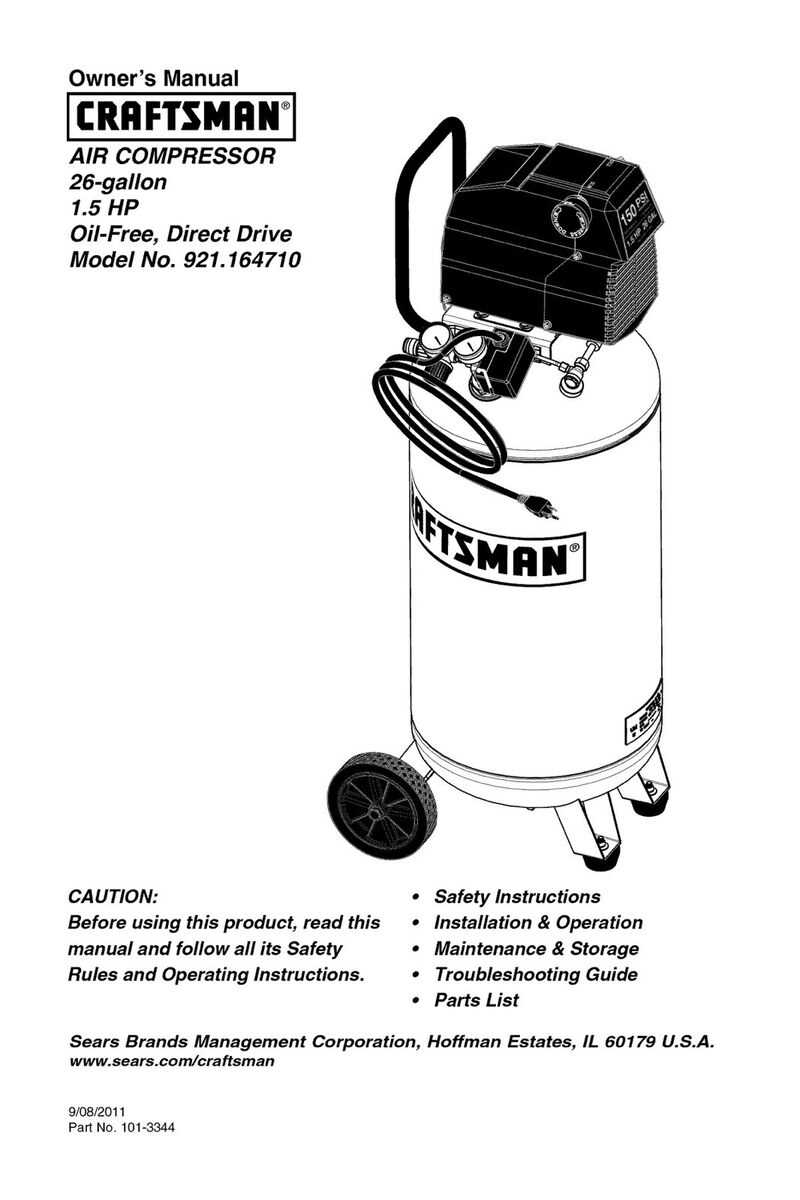
Unusual sounds or excessive vibrations can indicate underlying mechanical issues. These disturbances might be caused by loose components or imbalances within the motor or pump assembly. Tightening screws and examining moving parts for wear and tear can mitigate these problems. Regular maintenance and inspections can also help prevent such occurrences.
|